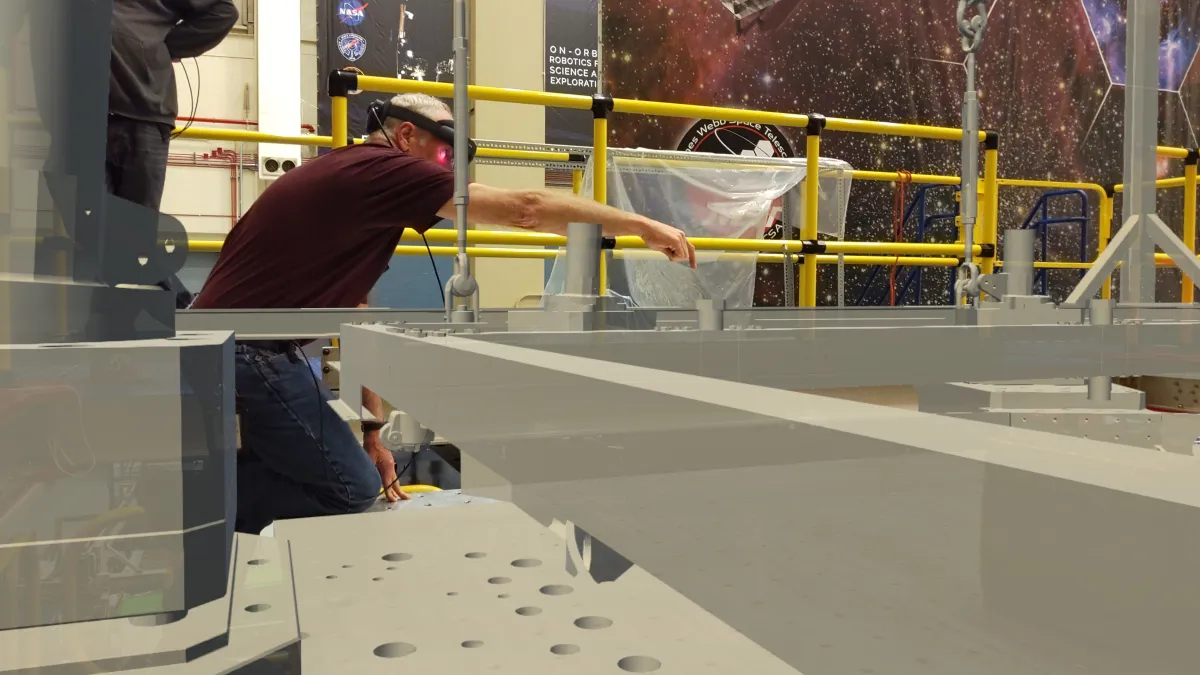
Engineers at NASA are turning to augmented reality (AR) to build spacecraft more efficiently and with greater accuracy.
The Roman Space Telescope team has already started applying the technology while working on the next-gen observatory — its next major eye on the sky after the James Webb Space Telescope's massive success. Roman is currently being assembled at NASA's Goddard Space Flight Center in Greenbelt, Maryland, and the agency said AR has already saved days' worth of work. Tasks that would typically require multiple engineers and technicians were also able to be completed with way less effort.
With augmented reality headsets and advanced measuring techniques, the NASA team has been able to project digital models of the telescope’s components into the real world. This allows them to align parts with an accuracy down to thousandths of an inch and identify potential interference before any manual assembly takes place.
"We've been able to place sensors, mounting interfaces, and other spacecraft hardware in 3D space faster and more accurately than previous techniques," said Ron Glenn, a NASA Goddard engineer, in a press release. “That could be a huge benefit to any program’s cost and schedule."
This could be a game changer as constructing a spacecraft is no easy feat. These structures must be lightweight, yet capable of withstanding extreme conditions; they must contain numerous complex systems, yet have components that snap together seamlessly. Procuring this type of machine requires extensive theorizing, rigorous testing, and, often, quite a bit of money. It even introduces significant complexity during manufacturing — consider how a slight aberration on one of the Hubble Space Telescope's mirrors before it launched in 1990 led NASA to create an entire mission that required astronauts to fix it in Earth orbit.
Furthermore, the virtual nature of augmented reality also means information is readily available to anyone linked into the AR. For instance, an engineer can quickly reference important information on the spot, from big-picture structural guidelines all the way down to torque specifications for individual bolts — all accessible via different hand gestures.
There is also the added benefit that remote engineers can provide input virtually from wherever they are. "Partners at other locations can collaborate directly through the technicians' point of view,” explained Aaron Sanford, another engineer working on the project. "Using QR codes for metadata storage and document transfer adds another layer of efficiency, enabling quick access to relevant information right at your fingertips. Developing AR techniques for reverse engineering and advanced structures opens many possibilities such as training and documentation."
But the benefits go beyond just time saving, with Glenn emphasizing that AR has allowed the team to achieve more than they initially expected. "The original project goal was to develop enhanced assembly solutions utilizing AR and find out if we could eliminate costly fabrication time," he said. "We found the team could do so much more."