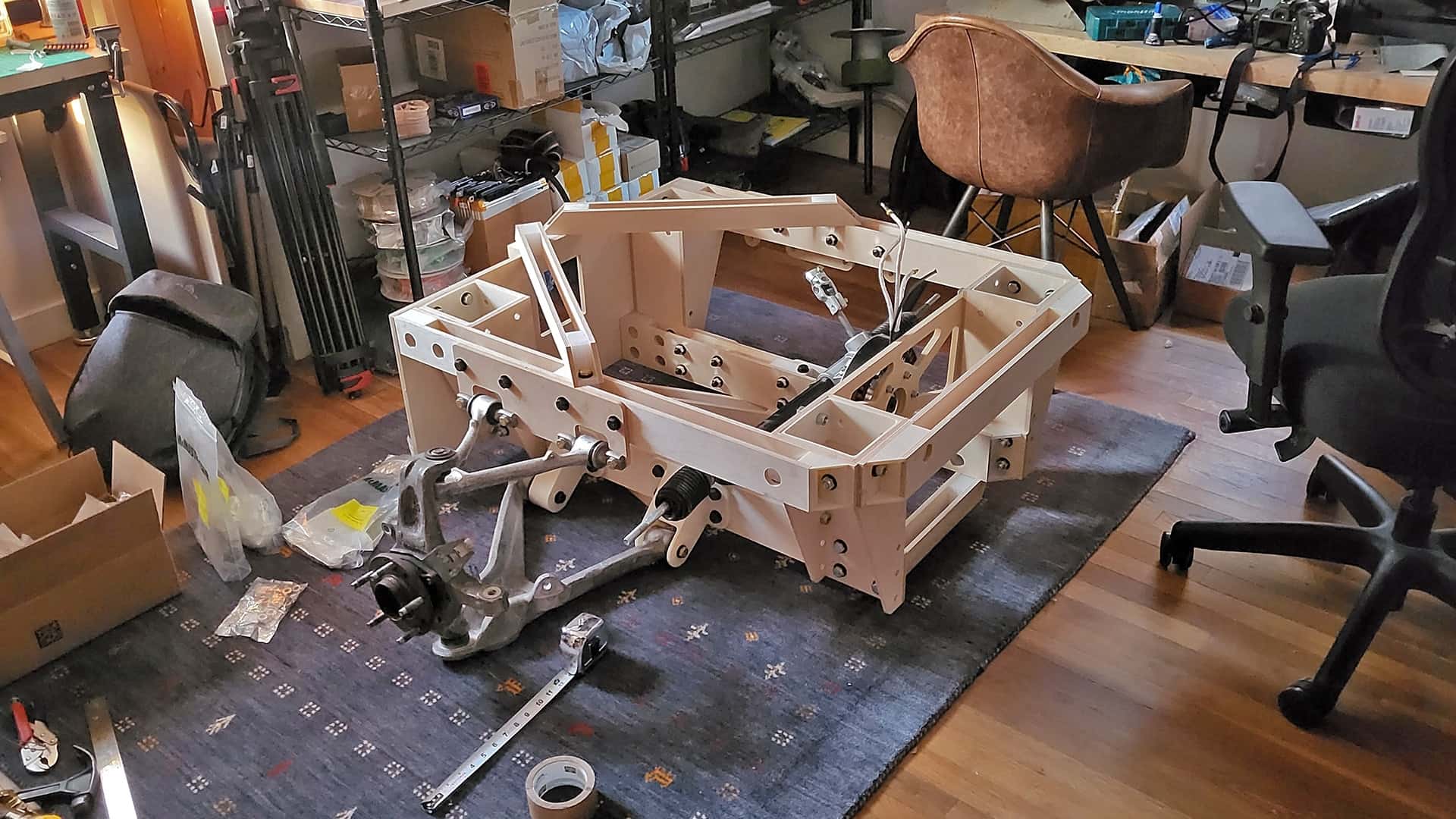
Determining the correct order of operations for any project can be difficult, but especially this one. There’s just so much to do, and first steps are the hardest to take. The last time we spoke, this project hadn’t really left the computer. But now I finally have a mockup to work with.
For those who don’t know, I’m building my own hybrid sports car. It’s an all-wheel-drive machine powered by a rear-mounted 160-horsepower BMW K1600 motorcycle engine and a front-mounted 50-horsepower electric motor. Think of it as a lightweight, compact, straight-six-powered Corvette E-Ray.
A lot of the things that I’m less comfortable with have to do with the front axle. For that reason, I decided to do a full-size mockup of this area, which is now assembled and sitting in my home office. Finally.

Certainties and Uncertainties
Physical mockups are extremely helpful, but they require certainties in the design you’re constructing. In other words, you don’t want to spend the money building something that isn’t final, and you need to do a lot of work to finalize the respective design.
That was my biggest hurdle. I hadn’t designed many pieces that would determine what the front subframe would look like. The suspension’s control arms are the best example. How should they mount? What should they look like? How should I make them? I’m not an engineer, and with that uncertainty lingering over the entire front end, I felt uncomfortable creating a mockup.
Then, just by happenstance, a very smart engineer named Derek Young reached out to me. If you don’t know Young, he’s the guy who stuffed a Kawasaki Ninja engine into the back of a Nissan Leaf. His project is similar to mine, and he had a lot of valuable advice to offer. The big thing was that if I was unsure about the engineering or manufacturing of a certain piece, I should try to use parts from an existing car. He also noted that I should work on multiple pieces of this project in parallel, because—speaking from his own experience—as soon as I lost interest in one piece of the puzzle, I could move to another.
That advice led me to develop more of the car’s interior and build a mockup of the front end to clear up all of those uncertainties. I would need to adapt the suspension from another car to do this, which is more difficult than it sounds.
Donor Vehicle
The problem is that there are relatively few mass-produced all-wheel drive sports cars, which means the parts are expensive. The Audi R8 and Porsche 911 4S seem like potential choices to snatch pieces from, but the cost of the parts is too high. Other cars you might expect to be eligible, like all-wheel drive sedans, have front struts or very tall control arms. That means my hood height would be unacceptably high. Basically, I needed a cheap, common, double-wishbone all-wheel drive car with coilovers mounted to one of the control arms, not the knuckle itself.
The answer is… the fifth-generation Chevy Corvette.
The C5 isn’t all-wheel drive, right? Right. But to save money, the C5 only has two distinct spindles, whereas most cars have four distinct spindles. The front-left and back-right spindles are the same castings with the same features. Different stuff bolts onto them—the rear uprights have shoes for a drum-style parking brake, for instance—but vitally, you can bolt the splined rear wheel bearings directly to C5 front spindles. Voila. All-wheel-drive. At least on paper.

And the parts are cheap. You can get an entire corner of a C5 suspension for less than $200. Both control arms, the knuckle, the wheel bearing, everything. I ordered and 3D-scanned these parts, and soon enough, I mounted them in my chassis, at least virtually. The rear end needed a considerable rework to get everything to fit, but the front was a pretty seamless integration.
The big problem to solve is CV axle clearance for the front end, and perhaps the rear, too. The Corvette had transverse composite leaf springs until the C8, but the front shocks are in a conventional location which blocks the path for a CV axle.
To solve this problem, I decided to ditch the transverse leaf and move to conventional coilovers. Transverse composite leaf springs are great for a lot of reasons, but it’s very hard to find custom ones. It’s comparatively easy to find adjustable coilovers with various spring rates.
Once I decided on coilovers, I needed to figure out where to mount them to avoid the axle shafts. The rears should be fine as-is, although my axles are at an angle that could compromise clearance. I talked about my axle angles in the previous post. I think it will be alright, but I plan to make a rear subframe mockup to ensure the fit.
The front end is not so straightforward. The Corvette E-Ray solves the axle clearance problem by forking the bottom of the coilover around the axle shaft. The other two options are to use pushrod suspension, which is pretty appealing for its packaging flexibility, or to modify the upper or lower control arm to accept the shock in a different location which avoids the axle. The best options are likely the first two.
The Mockup
This is where the mockup and this post’s sponsor, SendCutSend, enter the picture. I wanted to ensure all of this stuff would work before I started bolting and bonding the expensive aluminum chassis together, so I approached SCS to help me build a mockup of the front subframe. The company will also hopefully support other parts of the vehicle.
SCS offers a ton of different materials like metals, plastics, carbon fiber, and more, all with instant quoting. Just upload a file, select a material, and it will instantly tell you how much it costs. Free shipping, too. With all of this in mind, I devised a plan to make a full-sized wood mockup. SCS would cut the plywood and a few other materials, and I would do a lot of 3D printing to complete the picture. The end result has all of the correct external dimensions of every aluminum tube down to a fraction of a millimeter, and it’s flexible enough to add features as I go.





This mockup is valuable for so many reasons. It allows me to test-fit not only all of the vital parts of the car as well as their respective mounting solutions, but also gives me an idea of the correct order of assembly and what sorts of fasteners to use. I can also develop the front wheel alignment, articulate the suspension to ensure I have adequate steering angle and clearance, and even test-fit full-sized wheels. The body will bolt onto this mockup, too, so I can tune its fitment and get the car’s stance just right. Basically, anything I need to figure out for the real deal, I can solve using this model.
So far, I have the passenger-side suspension mostly mounted and a preliminary fit on the steering rack. The electric motor is also in position. The lower control arm ended up in a funny place and an extra bracket is necessary to ensure both body-side mounts are in double-shear. I’ll add it, but it’s not present in the mockup because I ran out of 3D printer filament as of writing.
The next step is to get the front differential mounted. Then I can make CV axle mockups and sort out the coilover mounting. After that’s done, I can immediately mount the front fascia and perhaps even some of the body panels. I also need to figure out the steering column location, but I need to mock up more of the middle of the chassis to do that.
Other Developments
I won’t go deep into other areas of development on the vehicle because they’re still preliminary, and this post is already pretty long. Most of them have to do with the interior design.
The car’s systems will mostly interact with an Android-powered touchscreen, although key physical controls will be present. Stuff like the battery management system, motor controls, and less-vital things like music and GPS are best handled by a touchscreen.
I’m currently testing an unusual 1920x480 display for this purpose. It’s powered by a Khadas Edge2 single-board computer, which is very powerful and has most of the features I need, like Bluetooth and WiFi. It defaults to vertical, which wasn’t my intent, but I kind of like how unusual it is, and so far all the apps I plan to use on it work fine in this orientation. I have also been looking at a lot of material swatches for the carpet and other interior surfaces. I think it’s important that this vehicle has a complete interior to sell the idea of a hybrid sports car to normal people.
The next update will cover more developments, once I start to get the suspension system together in earnest. Once I have the differential mated to the motor, I can fire up the electric axle in my office.
It’s all getting very real, very suddenly, and I appreciate the readers who are following along with this project. Likewise, none of this would be possible without key sponsors like SendCutSend. SCS is transforming how things are made for the better, and I wouldn’t be saying that if I didn’t genuinely believe it. Ten years ago, a lot of what I’m doing now just wasn’t possible, and it’s exhilarating now that it finally is.
Stay tuned for the next update, which is coming soon.