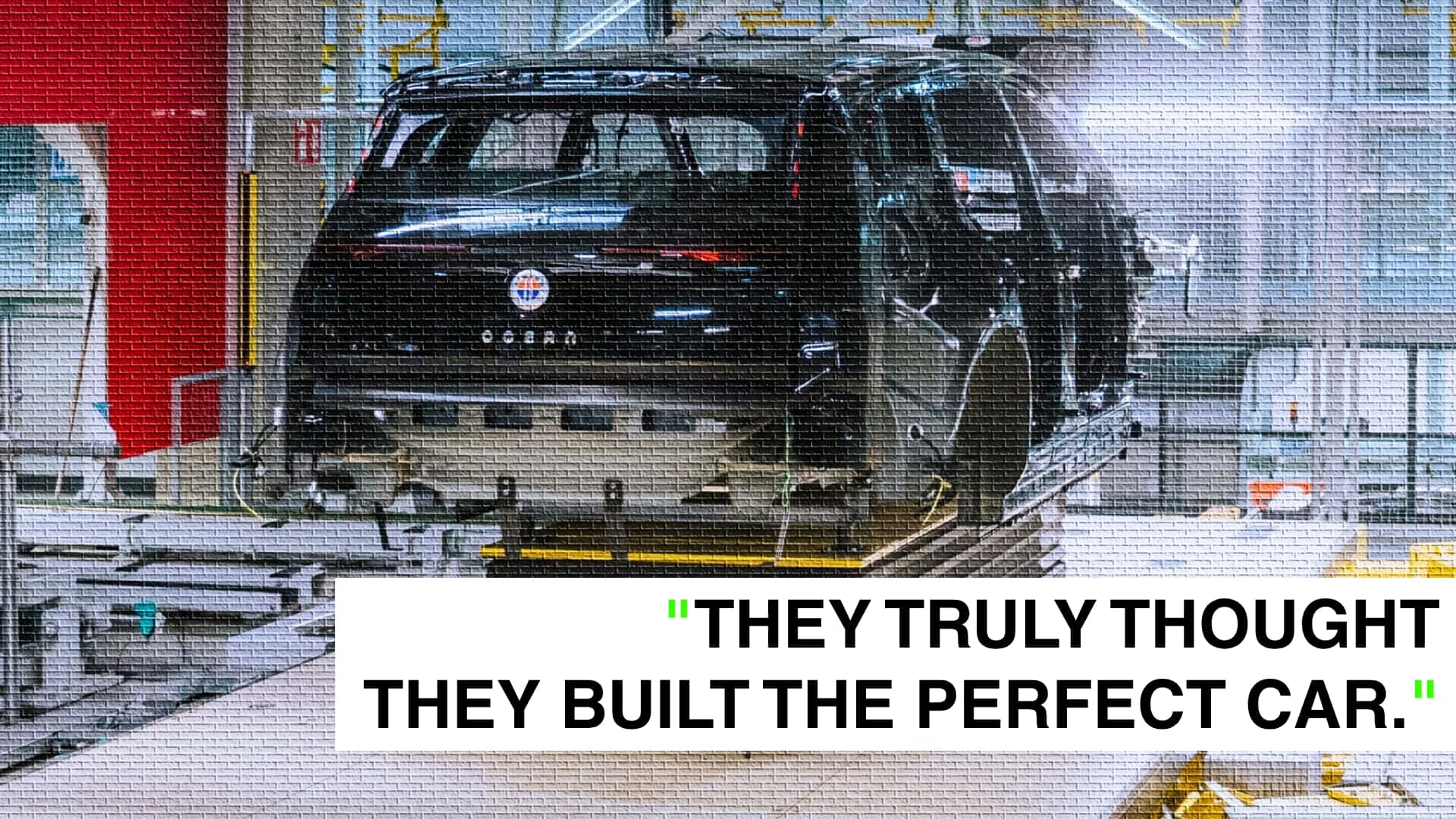
Fisker had grand plans to become the next Tesla. The electric vehicle startup touted an Apple-like business model that would allow it to outsource manufacturing while focusing on technology and design. And Fisker actually got its debut vehicle—the sleek, Range Rover-esque Ocean SUV—out to thousands of paying customers, something many EV upstarts die trying to do.
But according to several former Fisker employees who spoke with InsideEVs on the condition of anonymity, the startup was never really ready to sell cars in the first place. Fisker did not plan for a proper stockpile of replacement parts in the U.S. for repairs, for example. The resulting scarcity of parts has sometimes left Ocean owners high and dry when they’ve needed basic fixes. And it’s forced Fisker to source components in unconventional ways, like from disassembled cars, former employees said.
Get Fully Charged
Fisker's woes
The California-based EV startup made a splash when it launched deliveries of the Ocean SUV last summer. Fisker's big debut has since been marred by problematic cars and financial struggles. It's warned that bankruptcy may be near and has laid off a significant portion of its staff.
“It became very clear to anybody looking that this was a company not ready for prime time—to sell a product, to have any kind of customer service,” said one ex-employee.
New details surrounding the reported parts shortage were also reported by TechCrunch on Friday. However, Fisker denied former employees’ basic claims in both stories.
“This is false. Our service department did plan for and establish a parts inventory. The inventory forecast was made by the service team and the purchasing department supported those requests. Our suppliers are obligated to provide 10 years’ worth of parts,” a Fisker spokesperson said.

Less than a year after the Ocean hit the market, Fisker finds itself on the ropes. The California-based carmaker has all but run out of money. It’s slashed the price of the Ocean, which has been plagued by quality issues and government safety probes. Production has screeched to a halt, and management has implemented deep staff cuts. Fisker has warned it’s close to bankruptcy.
In the meantime, if Ocean owners do not need spare parts now, they will someday, just like they would for any car. And former employees say the automaker never planned adequately for that.
The first batch of Oceans was delivered to U.S. customers in June 2023, and shipments picked up throughout the summer. As Fisker owners got into inevitable fender benders and components failed, it didn’t take long for the lack of replacement parts on hand to become an issue.
“No plan was ever made for service parts, no matter how much we asked,” one source said. “By September, things were breaking and we had nothing to fix [them] with.”
Fisker only purchased the parts it needed for production and didn’t set aside extras for repairs, so replacement parts regularly had to be plucked from the Ocean’s factory in Austria and shipped to the U.S., three sources said. (Fisker denies this.) As a result, Fisker would sometimes have some parts stocked in the U.S., but the supply was thin and unpredictable, two former employees said.
Fisker enlisted the veteran contract manufacturer Magna Steyr to build the Ocean at a facility where it also assembles cars for Mercedes-Benz and Jaguar, among others. Fisker founder and CEO Henrik Fisker touted the benefits of an arrangement similar to Apple’s relationship with Taiwan’s Foxconn, which makes iPhones. (When reached for comment, a Magna spokesperson said the company does not share information about any of its customer programs.)
The rationale from Fisker leadership, including from COO and CFO Geeta Gupta-Fisker (who is also Henrik Fisker’s wife), for not setting up a more robust parts infrastructure was that the Ocean would be so “perfect” and so well-built that it would rarely need replacement parts, three former employees said. “They truly thought they built the perfect car,” one said.
“We are not aware of anyone at Fisker making these statements,” the Fisker spokesperson said. “In fact, our approach to inventory levels is inconsistent with anyone taking the position that there was not a need for replacement parts.”
Carmakers typically order the parts they need for production, plus some additional stock for servicing cars. They crunch the numbers to figure out what supply of each component they’ll need for repairs based on failure rates and the likelihood that some crashes will happen, said Dan Hearsch, Americas co-leader of the automotive and industrial practice at AlixPartners, a consulting firm.
“A normal part of the vehicle launch process is figuring out: What parts do you need in the market even on day one,” he told InsideEVs. That’s what former Fisker employees say the company failed to do.

Speaking generally, Hearsch said it’s not unheard of for a carmaker to keep its production and service parts together at its factory. However, he said companies with a global footprint need to consider that they’ll likely need a stock of parts across multiple regions where vehicles are sold.
Given the scarcity of parts, scavenging components from donor cars was commonplace, several sources said. Fisker denies that this has ever happened.
Two former Fisker technicians who helped prepare vehicles for delivery said they would regularly take parts off of donor Oceans for use in customer cars. One, who helped prep Oceans when they came off cargo ships, said his group would set aside one SUV of each color to use for parts like glass roofs, door handles, body panels and window regulators. The supply of parts in the U.S. was extremely low, the technicians said. Ordering replacement parts was “a nightmare,” one said, because they had to come from Magna.
Body panels like fenders and bumpers were especially tough to come by, making collision repairs difficult, two former workers said. So those were swiped off of existing vehicles.
Business Insider has also previously reported that Fisker had swapped parts onto customer cars.
Multiple sources also said that parts were occasionally transported from the Magna facility in Austria to the U.S. in employees’ personal luggage to expedite shipping. One recalled seeing “a suitcase full of A/C vents arrive that way.” A Fisker spokesperson said it can’t comment on the travel policies of other companies.

Fisker’s service strategy has been a moving target since the Ocean launched. Initially, Henrik Fisker announced a partnership with Bridgestone that would see Fisker leverage the tire chain’s vast retail footprint to maintain Oceans.
In January, the automaker announced a shift from a Tesla-like direct-to-consumer sales model to a more conventional dealer model. According to the plan, dealerships would assume the burden of sales and service as they were rolled out. The company also hired its own team of mobile technicians to diagnose and repair vehicles at customers’ homes.
Meanwhile, Ocean owners have complained about long waits for repairs or answers to questions, InsideEVs has reported previously. Fisker itself has acknowledged that its service infrastructure needed work. “We realize, based on customer feedback, that we need to make improvements, so we are ramping up our service operations globally,” Henrik Fisker said in a December press release.

It would be one thing if the Ocean was some problem-free marvel of engineering. But according to multiple owners who have spoken to InsideEVs and posted about their experiences online, it isn’t. The first generation of any car model is prone to issues. And even experienced car companies have run into snags rolling out new electric models lately. Oceans, especially early builds, wound up with all sorts of problems related to both software and hardware, InsideEVs has reported. Air conditioning vents, for example, broke frequently and needed to be replaced on many cars, the former technicians told InsideEVs. Key fobs struggled to lock and unlock Oceans from the jump.
But some Fisker customers have suffered through long waits for parts, former employees said. Indeed, on social media and in conversations with InsideEVs, owners have complained about the lack of available parts for simple repairs.
Nicole Ellis told InsideEVs that her Ocean’s passenger-side footwell gets soaking wet anytime it rains heavily because of an issue with her passenger door. Fisker has not been able to source the necessary part for her car for months, she said.
“Luckily I live in Los Angeles, where it doesn’t usually rain as much as it has,” Ellis said.
Another owner, who asked not to be identified to avoid online harassment from Fisker fans, said his insurance company totaled his Ocean One after a minor crash in part because of challenges sourcing a new bumper, hood and fender.
Digital infrastructure for service has been lacking as well, former employees said. A Salesforce-based software system intended for technicians to document repairs did not function properly and was not widely used even long after Ocean deliveries began, multiple sources said. In part, this was because technicians had so much on their plates, they said. As a result, work done to customers’ cars either before delivery or later on frequently was not recorded, they said. A Fisker spokesperson said the system is “fully functional.”
“In many cases, records just simply don’t exist because the information was never gathered,” said one source.
That may pose a problem for Fisker customers trying to force the company to buy back their Oceans. Without service records detailing issues and the steps taken to remedy them, it may be tough to prove that an Ocean was defective. Indeed, an untold number of owners are seeking Lemon Law buybacks.
The availability of replacement parts will likely become even more dire if Fisker declares bankruptcy or closes down. If parts were already hard to come by when Fisker was still in business, what’s in store for Ocean owners over the next several years? That’s surely on the minds of Fisker’s customers as the company struggles to stay afloat.
Got a tip? Contact the author: tim.levin@insideevs.com