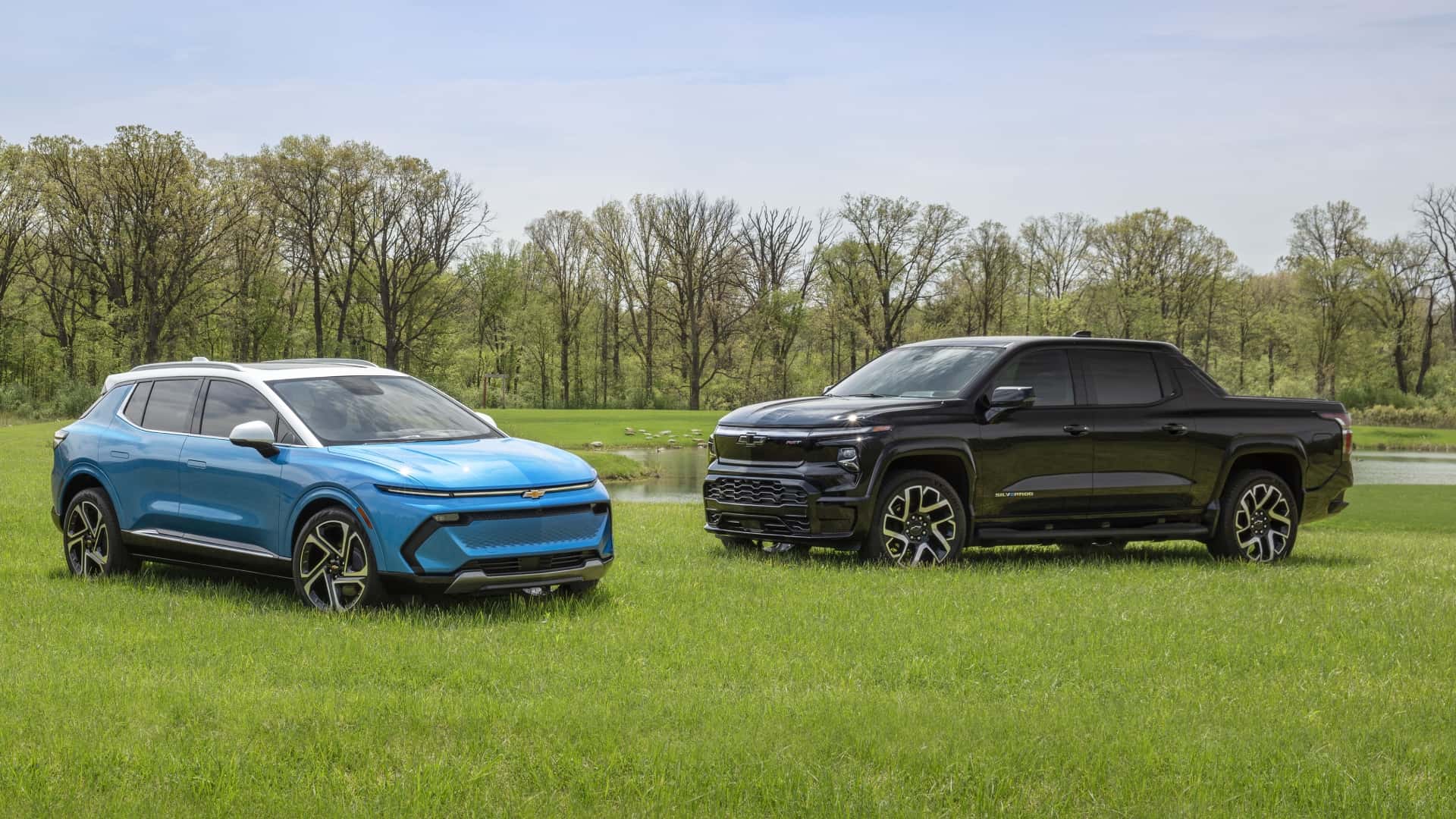
After witnessing Tesla’s scale and production capabilities, thanks to simplified architectures and fewer components, most automakers are mimicking the approach.
The industry has realized that lean manufacturing can help them reduce losses in their EV businesses and put them on the path to profitability. General Motors CEO Mary Barra explained that in detail in yesterday’s second-quarter earnings call. She revealed that the 2025 Cadillac Lyriq featured 24% fewer parts than the 2024 model year. It turns out that the Lyriq isn’t the only GM model on a diet.
Get Fully Charged
The race to make EVs profitable.
EVs are simpler than gas cars, packing fewer components, requiring less maintenance and saving plenty of cash during the ownership period. It's almost counter-intuitive that reaching this simplicity involves painfully complex engineering and redesign to reduce costs on the production line and pass on those cost-benefits to customers.
GM told InsideEVs today that all new Ultium-based Chevrolet and Cadillac models would feature fewer components than before to reduce costs and improve production efficiency.
“During yesterday’s call, the Lyriq was used as an example of what the team was able to achieve through Winning with Simplicity, a company-wide initiative that impacts all vehicles that will launch this year,” a GM spokesperson said. “Cadillac as well as Chevrolet customers will notice fewer trim combinations and more standard content on certain models.”

On the earnings call, Barra said this was crucial to improve the company’s margins. With what she called “smarter contenting and optimizing selectable options,” GM was able to eliminate more than 2,400 unique parts on ten vehicles it plans to launch through the first quarter of 2025. It’s unclear if all these are EVs, but now we know they include models like the Chevy Equinox EV, Blazer EV, Silverado EV, and Cadillac Optiq, among others.
“The list of parts that we no longer need to design, engineer, source, install … is extensive,” Barra said. According to her, this includes seat assemblies, consoles, and door trims, which require complex engineering and are relatively costly. “A crucial element is reducing the number of buildable electrical combinations, which is delivering hardware and software quality improvements as well as savings.”

Rivian took a similar approach with its second generation R1S and R1T. It includes eliminating 1.6 miles of internal wiring and reducing the number of electronic control units (ECUs)—devices responsible for controlling specific functions in a car—from 17 to just seven.
GM says this approach would help it save $2 billion dollars in what it calls a "fixed cost reduction program." The savings are expected to be even greater in the years to come. It’s too early to decipher the implications of these lean manufacturing goals. However, it seems to have worked for Tesla, albeit after undergoing a “manufacturing hell” phase. We’ll keep an eye on how it works out for GM.