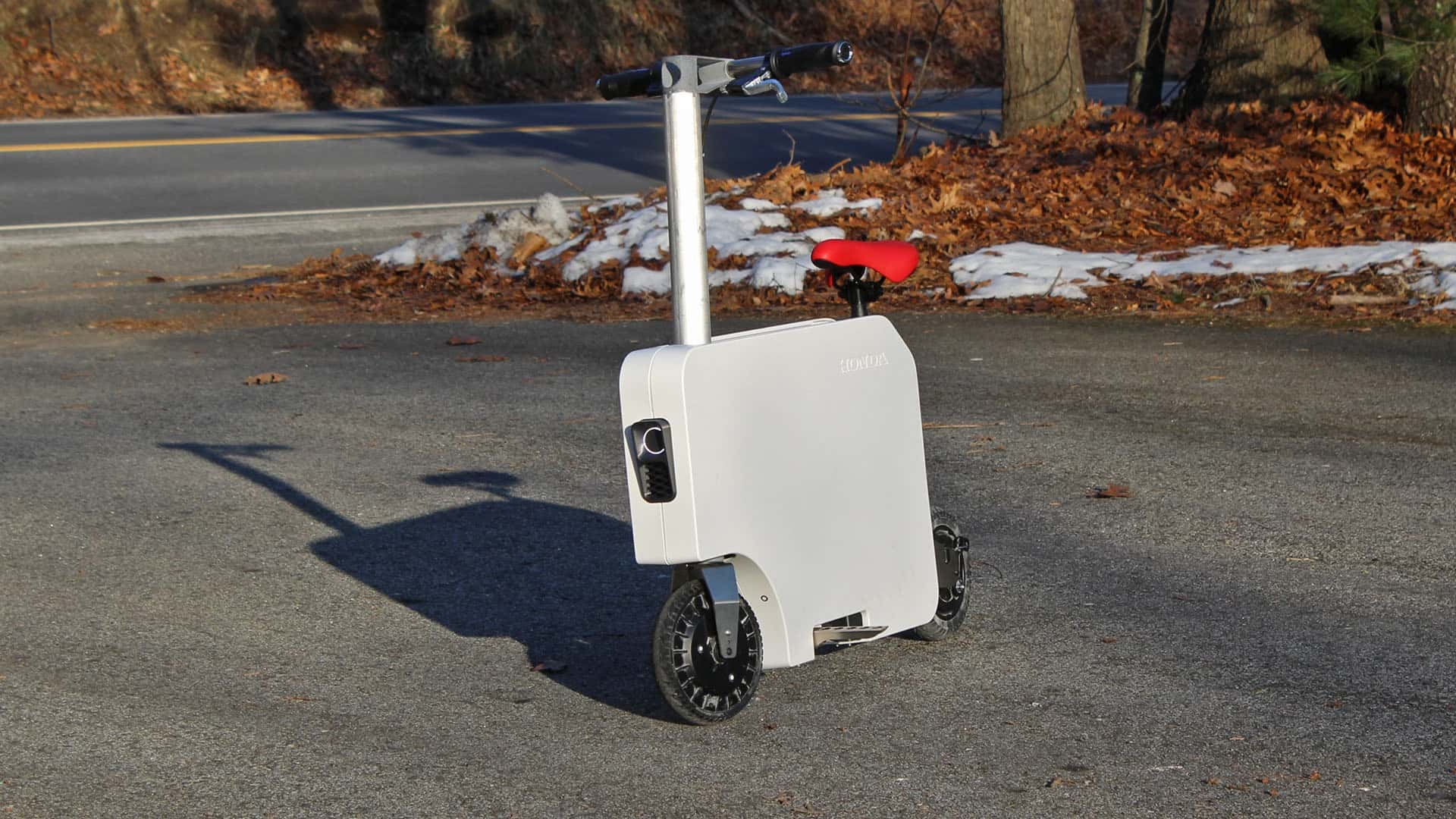
Honda's Motocompacto is a cool gadget. A tiny foldable scooter built to speed through busy urban environments, it has just one big problem: It doesn’t really speed anywhere; Its rated output is less than a single horsepower. Sure, it will go 15 miles per hour, but that takes seven seconds. Too slow. Those are rookie numbers.
For that reason, we decided to make a Motocompacto Type R. Honda only puts the Type R badge on its most engaging and capable machines. To be worthy of the name, we’ll have to make our Motocompacto faster, lighter, and a lot more fun. How will that work? Well, there are a few ways you can do something like this. The course I took is probably not the easiest one, but perhaps the best.
Decisions, Decisions
One of the first things I realized is that buying and modifying an existing Motocompacto didn’t make a ton of sense. It’s easier just to build your own.
The Motocompacto is a Honda product like any other. Therefore most of its components have part numbers like a Civic would. This means you can just order stuff like the Motocompacto’s front wheel, which is the electric motor (08Z15-PR8-100R11), the rear wheel which is the brake (08Z15-PR8-100R14), and both sides of the body (08Z15-PR8-100R5), (08Z15-PR8-100R6). That’s most of what you need to make something that at the very least looks like a Motocompacto.
There’s more. The Motocompacto costs $995, but Honda doesn’t seem keen on people modifying them. The battery pack, for instance, is fused to limit the current that can flow out of it. The motor controller—called an inverter on larger EVs—is also something of a “black box” that would likely be difficult to crack into. The battery may also have a management system with its own performance-limiting features. At the very least, I would have to replace the inverter, bypass the main fuse, and modify or replace the stock battery to unlock more performance.
It seemed a better idea to start from scratch. I knew the wheelbase of Honda’s scooter and knew I could get most of the OEM parts needed. Because the Motocompacto isn’t very complex—it has no suspension, for example—I could piece the rest together with known quantities in the light EV tinkering space. With a plethora of images and information available about the Motocompacto itself, building something that would look and ride a lot like the factory scooter didn’t seem impossible.
Ordering The Parts
The most important pieces of the puzzle are the motor and controller. I ordered the motor from Honda first. I got the controller from a company called Flipsky, which builds inverters based on the VESC framework. I wanted to get this Motocompacto drivetrain working on the bench before putting it on a scooter, and a few days later, everything showed up at my door. The first thing I did was crack open the motor to see what I was working with.
The motor appears to be a generic scooter hub motor that’s likely built specifically for Honda by a different manufacturer. Internally it looks very similar to other hub motors I’ve disassembled. The only thing that really sets it apart is the temperature lead on the sensor harness, which Honda probably wanted in order to protect the motor from overheating.
I don’t think any overheating is likely, though. As previously mentioned, the Motocompacto puts out just ⅔ horsepower or 490 watts. Honda doesn’t state the scooter's operating voltage publicly for some reason, but the model number on the side of the hub motor indicates it's a 36V (nominal) system.
Heat in any electrical circuit is mostly a function of current, (assuming a fixed resistance) and since wattage is just volts multiplied by amps, we can surmise that the Motocompacto only operates at around 14A. That’s a pretty weak figure that’s not gonna cause much heating. The whole system is also fused for just 20A. In other words, its maximum power before you hear a loud pop is only 720W, or 25 watts shy of a single horsepower.
To get past the one horsepower mark—practically the sound barrier for this thing—I bought the aforementioned controller that supports up to 50A at a maximum of 60V. Using this inverter, I can turn the power up or down to my liking, adjust the throttle curve and regenerative braking, pretty much everything you want in a vehicle like this. It can also be programmed on the fly using a computer or a smartphone.
After some soldering to get all the connectors to agree with each other, I plugged everything in and… It actually worked the first time, which I considered a very good omen, perhaps even an excellent omen.
The three thick cables from the controller are the phase wires that send the battery current to the stator. They make the motor move. One of the smaller plugs is for the sensing harness. It uses magnetic sensors to tell the motor which way to spin from a dead stop. The motor will work without plugging that stuff in, it just has to be spun in a certain direction to tell it which way to go first. If you don’t do that and apply throttle it just kind of vibrates and gets warm. Happens to the best of us.
The Frame
With the drivetrain mostly sorted, I designed the frame. I ordered the rear wheel from the stock scooter as well as the front motor, so I just needed to get everything in between them right. To do this I pasted the known Motocompacto wheelbase of 29.2 inches into CAD and scaled a side-view photo of the scooter to the measurement. After that, I just matched up all of the ergonomic hardpoints like the seating position, foot pegs, handlebar height, front fork angle, etc.
The scooter’s frame is a three-inch square aluminum tube, a few round aluminum tubes for the seat tube and fork, and some bent steel for everything else. It came together pretty easily with only minor adjustments required.
This is where the project’s sponsor, Oshcut, enters the picture. It offers instant-quoted laser-cut metal parts with no minimum order quantities. All of the metal on the scooter is from them, with few exceptions.
I can’t say enough nice things about Oshcut’s service. You can design a part, upload it to their website, select a material, and it tells you how much the project costs and when your part will arrive. It does flat metal parts as well as pieces bent over a brake and even tubes. Honestly, even if we didn’t work out a sponsorship deal for this project, I would’ve ended up using the company’s services.
The one part that isn’t 100% from Oshcut is the fork. To make it, I used a few 3D-printed parts combined with their metal components. I’m not sure how long these plastic parts will really hold up, but they’re made using an industrial process called Multi Jet Fusion, a 3D printing process that I am very familiar with. I tapped the parts to accept fasteners and glued the handlebar bracket on with some 3M structural bonding adhesive. I wanted to avoid welding for the sake of simplicity. Also, I don’t have a welder, which would’ve made welding difficult.
Final Steps
Mounting the body was the last step, and it took a little tuning. The scooter’s body is held on with just four screws and some velcro (from the factory). I 3D scanned most of it to get the dimensions into CAD. Scanning was also helpful on the front and rear wheels to come up with a mounting solution. Eventually, I got the fit just right with some 3D-printed spacers, and it wrapped around my frame. The only modification was removing a protrusion for the Motocompacto’s folding handle. My design does not fold for the sake of simplicity and the alternative was cutting a big hole in the frame. So I removed that bit.
With all of that sorted, though, you can see the final result.



I 3D-printed a new headlight for the scooter, which is illuminated by a white LED filament. It’s on its own power supply separate from the traction battery. I think it looks pretty sharp.
The next story in this series will cover actually riding the scooter, as well as talking more about the power electronics, which are related directly to the driving experience. Until then, tell me more of what you want to see. I get really wrapped up in this kind of stuff and sometimes forget what people want to know. This has been a really fun project so far and, rest assured, more stuff like this is on the way.
Image credit: Honda