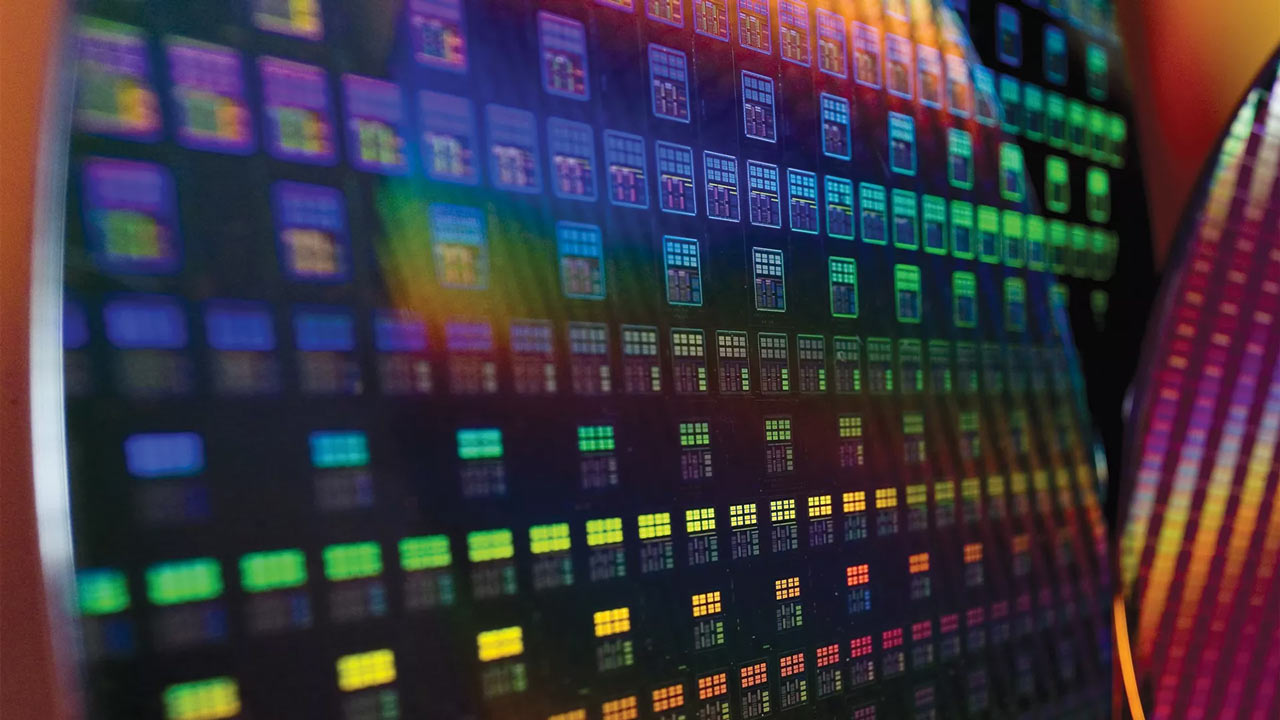
TSMC revealed additional details about its N2 (2nm-class) fabrication process at the IEEE International Electron Device Meeting (IEDM) earlier this month. The new production node promises a 24 to 35% power reduction or 15% performance improvement at the same voltage, and 1.15X higher transistor density than the prior-gen 3nm process. The vast majority of these advantages are enabled by TSMC's new gate-all-around (GAA) nanosheet transistors along with N2 NanoFlex design-technology co-optimization capability and some other enhancements detailed at IEDM.
Gate-all-around nanosheet transistors allow designers to adjust their channel width to balance performance and power efficiency. On top of that, TSMC's N2 adds N2 NanoFlex DTCO, enabling designers to develop short cells with minimum area and enhanced power efficiency, or tall cells optimized for maximum performance. The technology also includes six voltage threshold levels (6-Vt) spanning a 200mV range, achieved using TSMC's third-generation dipole-based integration with both n-type and p-type dipoles.
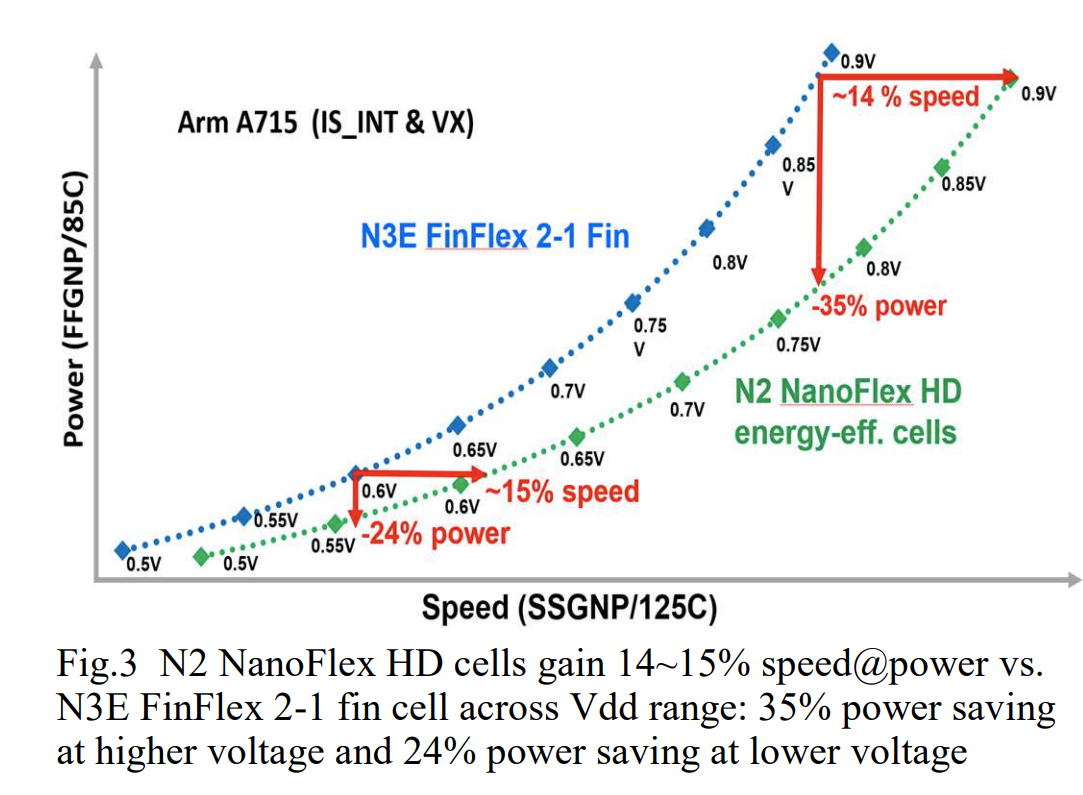
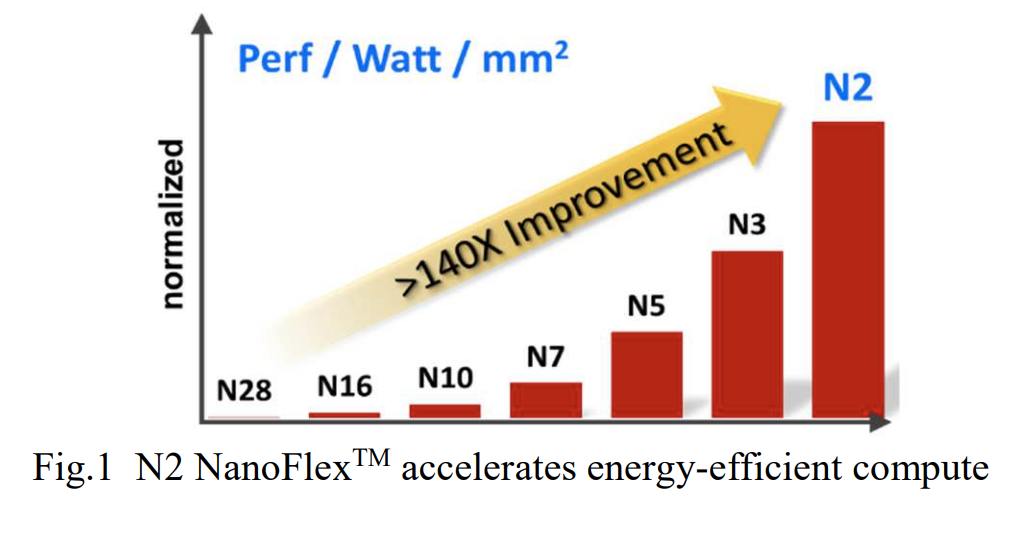
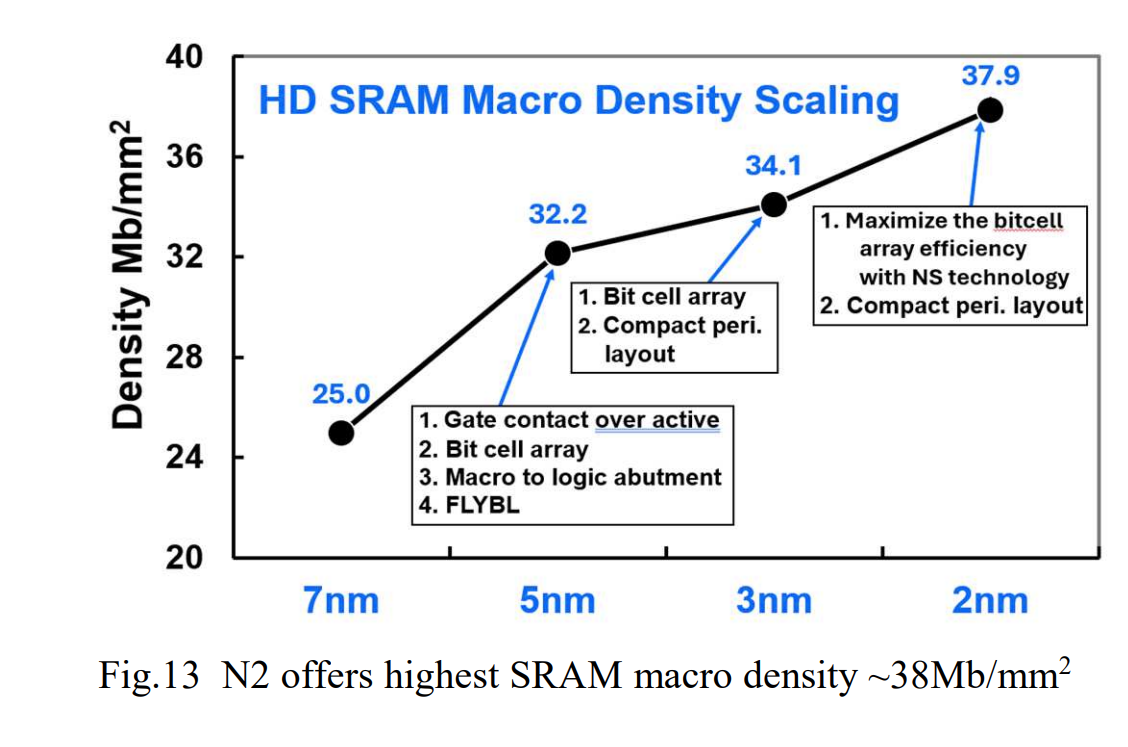
N2's innovations introduced at the process and device levels target not only boosting transistor drive currents by refining sheet thickness, junctions, dopant activation, and stress engineering but also reducing effective capacitance (Ceff) to achieve class-leading energy efficiency. Collectively, these refinements yield I/CV speed gains of about 70% and 110% for N-type and P-type nanosheet transistors, respectively.
Compared to FinFETs, N2 nanosheet transistors deliver noticeably better performance per watt at low supply voltage ranges of 0.5V to 0.6V, where process and device optimizations boost clocks by around 20% and cut standby power consumption by about 75% at 0.5V operation. Moreover, integrating N2 NanoFlex and multiple threshold voltage (multi-Vt) options enables additional design flexibility for energy-efficient processors at high logic densities.
Transistor architecture and DTCO advantages directly affect SRAM scalability, which was tough to achieve with leading-edge nodes in recent years. With N2, TSMC has managed to achieve a record 2nm SRAM density of about 38Mb/mm^2. In addition to hitting record SRAM density, TSMC also lowered its power consumption. As GAA nanosheet transistors feature tighter threshold voltage variation (Vt-sigma), N2 achieves about a 20mV reduction in minimum operational voltage (Vmin) for High Current (HC) macros and a 30–35mV reduction for High Density (HD) macros compared to FinFET-based designs. These improvements enable stable SRAM read and write functionality down to approximately 0.4V while maintaining robust yields and reliability.
In addition to new transistors, TSMC's N2 employs all-new middle-of-line (MoL), back-end-of-line (BEOL), and far-BEOL wiring to cut resistance by 20% and improve performance efficiency. N2's MoL now uses barrier-free tungsten wiring, which reduces vertical gate contact (VG) resistance by 55% and increases the ring oscillator's frequency by about 6.2%. Additionally, the first metal layer (M1) is now created in one EUV exposure pass followed by a single etch step (1P1E), reducing complexity, lowering mask counts, and improving overall process efficiency. TSMC says that using EUV 1P1E for M1 cuts standard cell capacitance by nearly 10% and saves several EUV masks. In addition, N2 cuts metal (My) and via (Vy) resistance by 10%.
In addition, N2's extra features for HPC applications include super high-performance MiM (SHP-MiM) capacitors providing around 200fF/mm² of capacitance, which helps achieve higher maximum operating frequencies (Fmax) by reducing transient voltage droop.
Finally, TSMC's N2 technology features a new Cu RDL option with flat passivation and TSVs that is optimized for face-to-face and face-to-back 3D stacking with an SoIC bond pitch of 4.5 μm, which is set to become a usable feature for AI, HPC, and even mobile designs, according to TSMC.
TSMC is set to start production on its N2 process technology in the latter half of 2025.