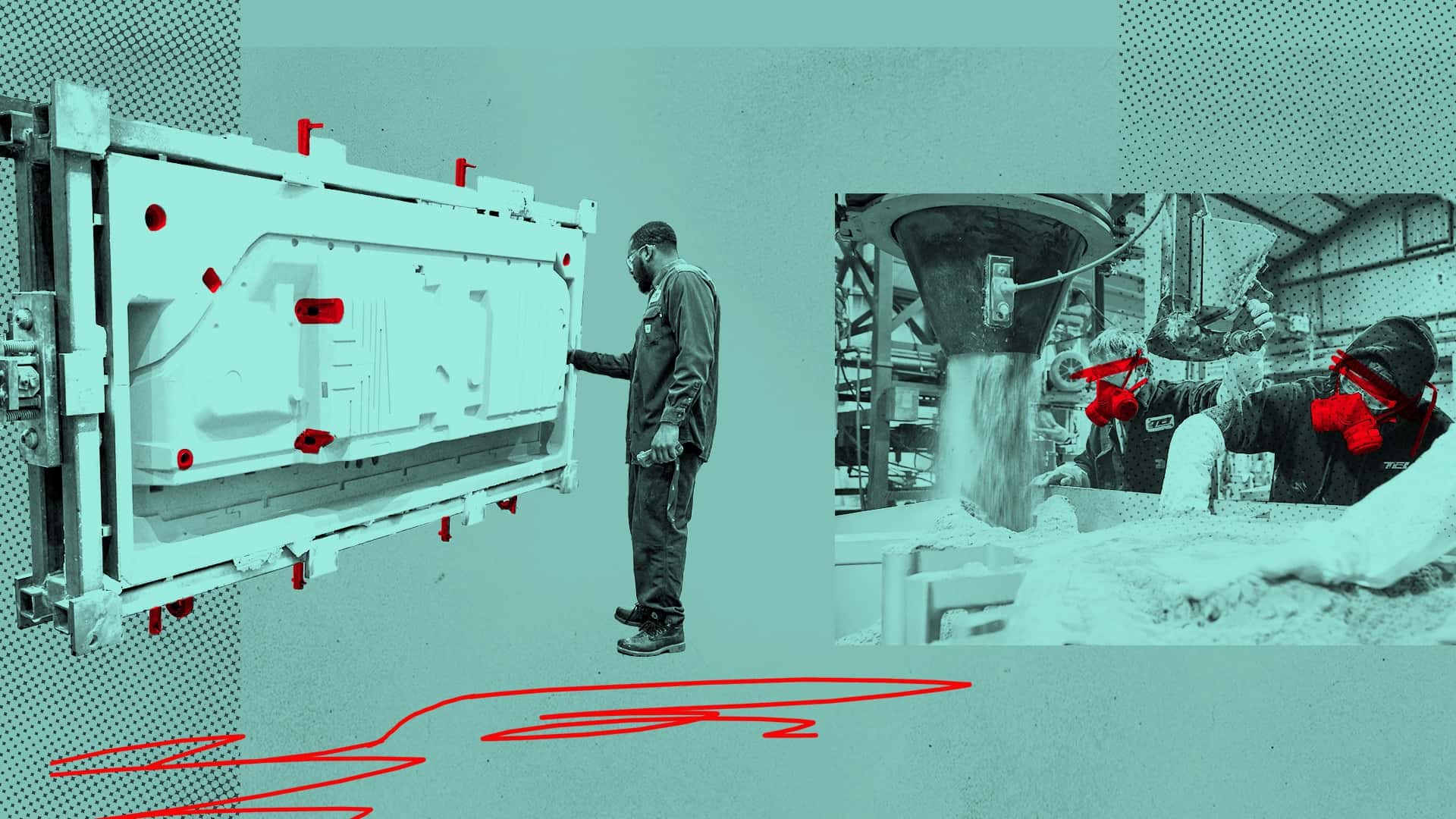
The auto industry is shifting. Roadsters are disappearing, compacts are dropping their two-door options, and affordable sports cars feel like forgotten history. The Miata is the last budget roadster standing. A new affordable mid-engine machine—like the old Toyota MR2—seems impossible.
The investment for automakers doesn’t add up. Oceans of hard tooling must be produced simply to build a new car. Since the cost of building a low-volume vehicle is so high, automakers often forgo the exercise altogether.
And the decline of the sports car—not to mention sports sedans—is truly shocking. Between 1984 and 1988, Pontiac sold nearly 350,000 Fieros. In the same amount of time between 2000 and 2004, Toyota sold 27,161 MR2s. Last year, Mazda sold just 8,973 Miatas stateside (up nearly 50% from 2022). You gotta wonder: What the heck has changed so much?
Just as it seems like we’re reaching enthusiast rock bottom, technology has delivered several gifts, as it tends to do. The face of low-volume manufacturing has changed drastically in the last decade. Once considered niche and expensive, 3D-printed and laser-cut parts are now a regular feature on many upscale vehicles. What’s holding these technologies back now is not their exotic nature, but the volumes. That’s finally reaching a tipping point.
“The whole reason why I started looking at [additive manufacturing] in 2011 was because I saw my first printed metal part,” Brennon White, a technical specialist for Advanced Manufacturing at General Motors, told Motor1. Back then, metal additive parts were small, expensive, and fragile compared to their cast counterparts. Using them in an automotive setting seemed hopelessly impractical. Now, though, everything has changed.

White’s team is responsible for the additive parts in the company’s Cadillac Blackwing sports sedans and the six-figure Cadillac Celestiq. While the combustion Cadillacs use small 3D-printed metal and plastic parts to add visual jewelry and solve manufacturing headaches, the Celestiq leverages advanced manufacturing methods in ways never seen before on a production car.
The Celestiq starts at over $300,000, but with around 150 3D-printed parts scattered around the car—some the size of a shoebox—it’s pushing manufacturing volumes and embracing the technology in a way no major OEM has before. The high price of the Celestiq is relevant, to be sure, but that’s missing the point. Additive manufacturing finally has its foot in the door at a major automaker.
“We’re seeing the opportunity to hit not just hundreds, but thousands of units,” White told us. In his mind, we’re at a “tipping point in the industry.” The biggest hurdle to overcome now is not how to make the filaments, powders, and resins to feed the machines, but building volume to lower their cost precipitously. In other words, if more automakers get on board with additive manufacturing, its rise to mainstream status will accelerate.

Additive manufacturing gets most of the attention when it comes to advances in car building. Still, other methods of processing raw sheet metal and tubes have also advanced rapidly. The Celestiq uses several laser-cut, brake-bent parts which require little, if any, hard tooling to produce. They aren't as sexy as 3D-printed pieces, but they enable rapid scalability and access to metal parts for hobbyists and tinkerers who could never use them before.
One of the most impressive players in this space is Utah-based Oshcut. The company’s CEO, Caleb Chamberlain, understood the capabilities of this impressive technology but struggled to get parts made by businesses using these new machines. In 2018, he and his brother founded Oshcut to change that. It now offers laser-cut and brake-bent metal parts as well as tubes in a massive variety of shapes, materials, and sizes.
The company’s online software suite can instantly unfold a complex part, understand its geometry down to fractions of a millimeter, and immediately provide a price for the component. No emails are involved, no minimum order quantities must be met, and other added-value services like tapping, deburring, and powder-coating are also offered in the same web-based software suite.
“We serve so many different industries, it’s pretty crazy,” Chamberlain told us. Oshcut already supplies a number of aftermarket accessory companies, and he sees a great opportunity to use his services for automotive manufacturing, “especially when it comes to tube.”

My own project to develop a small hybrid sports car would simply not be possible without Oshcut. With several sizes and shapes of aluminum, stainless, and mild steel tubing available, the possibilities are seemingly endless. Chamberlain is likewise looking to expand into other exciting areas of fabrication to widen the business’s horizons and give his customers access to even more impressive capabilities.
Getting custom metal parts will only get easier and cheaper. Oshcut has a growing slate of competitors, and the price of metal additive manufacturing is coming down while the technology’s capabilities are growing. Neither of these trends will translate into a revolution overnight, but for the first time in decades, the way cars can be made is changing considerably, and for the better.
Hard tooling will one day be only a small part of the picture when it comes to making cars. As a result, the cost of developing a platform will decline, and smaller batches of roadsters, coupes, and other shrinking segments will be far easier to justify. Niche parts of the automotive landscape won’t be an afterthought, but an opportunity.
No one knows this better than Kevin Czinger, the founder of the eponymous car company and its parent organization, Divergent. Growing up in Cleveland, Ohio, Czinger watched as the industrial powerhouse built around his hometown eroded into the rust belt.
“All of that industrial base got wiped out because they couldn’t retool vehicles, they couldn't refit [their] factories,” he told Motor1. He founded Divergent as an alternative to the rigid way of making things. Thanks to advances in computing power and manufacturing technology, Czinger is turning that system on its head.

Czinger isn’t so interested in any particular manufacturing technique as much as he is in the digital systems that enable their use.
“Any of these technologies are of relatively little use when you use them in isolation,” Czinger said. The key is understanding, integrating, and developing these tools into one common platform that maximizes the productivity of a small number of talented engineers.
Czinger has the design and testing side covered, too. Immense computing power enables machine learning to rapidly accelerate the parts development process. Czinger says components that used to take engineering teams months now take individuals less than a day. And with testing as well as simulation happening in-house, the company can not only iterate quickly but correlate physical and digital testing data with immense efficiency.
Divergent contracts with several automakers—including Bugatti, Aston Martin, McLaren—as well as the Department of Defense. Speaking to Czinger, I realized his company’s work represents a huge step for manufacturing. That Divergent also makes cars almost seems like an afterthought.

But Divergent’s work seems almost inseparable from the automobile, simply because, as far as I could tell, Kevin and his son Lukas are both car enthusiasts.
“This is a mass manufacturing technology that [will] be applicable to over 50 percent of all the cars manufactured on the planet by 2030,” he said.
Advances in computing and manufacturing will enable a new era for the automobile. The technology to develop and build automobiles is being rapidly democratized, with costs and barriers to entry lowering by the day. The first to jump on these opportunities will be the visionaries like Czinger, but eventually, even the massive, conservative players will be forced to change.
What seems like a bleak moment for enthusiasts will be altered rapidly in the years leading up to 2030. Sooner than you think, the market will diversify again, dotted with affordable sports cars, coupes, and convertibles enabled not just by the relentless march of manufacturing, but by the boundless creativity of enthusiasts who demand more.