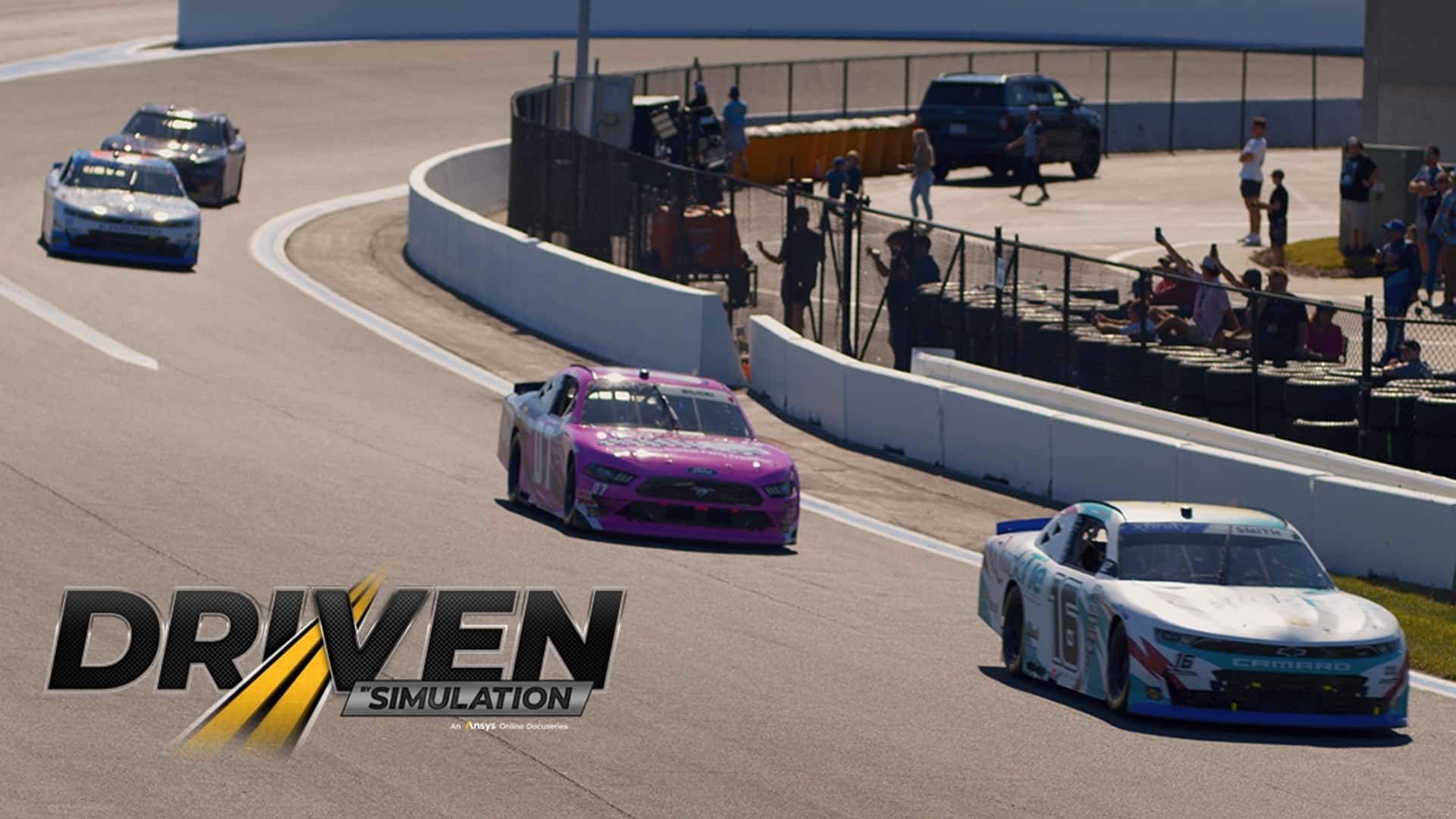
Last fall, driver Ryan Preece barrel rolled along the back stretch during the NASCAR Cup Series race at Daytona International Speedway. Reactions from the stands included gasps, groans, and tears, followed by audible sighs of relief and applause as Preece managed, with help, to climb out of the driver's side window to safety.
During the slow-motion replay, Preece's car could be seen going airborne, then flipping uncontrollably through the grass before landing upside-down. Yet somehow, he was cleared the following day to fly home to rest before eventually returning to the track.
To many, Preece's safe exit seemed nothing short of a miracle. However, it was NASCAR's dramatic safety upgrades, including head and neck restraints, all belts to seats, cockpit structure, and window nets that all came into play that day.
Undoubtedly stock car racing is dangerous—which is why NASCAR goes to extremes to ensure drivers walk away safely. During Episode 8 of Ansys online docuseries "Driven by Simulation," you'll hear how simulation enables the racing organization to continuously evolve its Next Gen vehicle designs to mitigate risk on the track.

A Design Series without Missteps
It's been said NASCAR is to stock car racing what the NFL is to football—both have achieved tremendous acclaim in their respective sport. The Cup Series is NASCAR's premier racing event featuring its Next Gen stock car built on a standardized parts platform. Single-source manufacturers are responsible for the new car parts and a more flexible, durable carbon composite body. Engines and vehicle stylings vary among Chevrolet, Ford, and Toyota resembling Camaro, Mustang, and Camry passenger cars, respectively.
Gen-7 is the latest iteration of the Cup Series car. It features two V-8 engine packages—one that pushes 510 horsepower on the Superspeedways, and another that pushes 670 horsepower on the intermediate tracks. Both are mated to a five-speed transmission offering a wider range of gear options than its four-speed predecessor. Other improvements include a low-downforce 4-inch rear spoiler (7 inches for Superspeedways), an upgraded braking system, and an independent rear suspension with adjustable dampers in all four corners for fine tuning.

What is perhaps the most compelling aspect of the Gen-7 story, apart from these impressive specs, is the timing and extent of the re-design. In setting aside decades of innovation, NASCAR built an entirely new platform that would be used by all race teams in the Cup series. Stepping away from older design elements (some dating back to the 1960s) would certainly make the series more relevant to original equipment manufacturers (OEMs) and fans. But was it a safe move for NASCAR?
Yes, it was, thanks to simulation.
"On the racetrack there are multiple ways that the cars can crash—some that we can't even imagine," says Dr. John Patalak, vice president of safety engineering at NASCAR. "But with LS-DYNA we can run all of those without having to commit to the physical test to really have the confidence that we have a very robust design."

Gen-7 Safety Gets the Green Flag from Ansys LS-DYNA
Driving at high speeds requires shorter reaction times. When you have as many as 40 cars tailgating each other at 200 miles per hour for more than 200 laps, there's bound to be issues. Once you've hit your groove, it only takes a split second and a single misstep to cause a pile up. NASCAR engineers are keenly aware of this, which is why they rely on simulation to develop and fine tune their "Gen-7" Next Gen vehicle platform for performance and safety.
Introducing Ansys software into the mix proved to be a pivotal moment. For the first time in the history of NASCAR, the bulk of the crash testing would be handled by simulation. Meshing out and building a full Ansys LS-DYNA car model enabled the team to immediately assess all the different crash modes that NASCAR race cars encounter, including frontals, roof crashes, lateral side impacts, rear impacts, and oblique impacts.
"We have the opportunity to use LS-DYNA," says Patalak. "We can run hundreds or thousands of simulations to assess all the details and nuances of how we want that car to perform before we commit to spending those dollars on the race cars."
Running LS-DYNA in Ansys Cloud Direct enables the NASCAR development team to quickly test, tweak, and fully optimize their designs within limits before evaluating them at a crash test facility. Considering the cost of running physical crash tests (approximately $500,000 per test), the savings can really add up. In this case, the payoff was big. After more than 5,000 LS-DYNA crash test simulations, it took only a few physical crash tests to verify and validate NASCAR's Next-Gen design.
Digital Dummies Unlock Crash Test Insights
One of the most important factors for the team during design evaluation is the response of the occupants in the racing environment.
So, if you were to ask a crash test dummy about its experience after months of testing on the sled, what would it say? Well, nothing, of course. However, when you're looking at multiple simulations of impacts involving crash test dummies in a virtual environment, it's easy to see the effects a crash will have on them in the driver's seat if they hit a barrier at a certain angle and speed, for instance.
"(We) use advanced human body surrogate models in the NASCAR seating environment to evaluate the restraint system, the safety systems, (and) the different injury mitigation systems that we have in our car," says Dr. Sayak Mukherjee, simulation engineer, safety at NASCAR. "The idea behind this is to reduce the injuries to the driver in case of any on-track incident."

Modeling drivers in a virtual environment enables the team to study occupant response in different crash test scenarios, look at different injury metrics, and try to incorporate the safety or mitigation systems that can reduce the risk of injury to ensure everyone walks away unscathed.
It's a practice that began early in the Next Gen design process. Elemance, an engineering company dedicated to human-centered design, used a virtual human body model developed by the Global Human Body Models Consortium (GHBMC), and performed tests for NASCAR with the help of Ansys LS-OPT, a design optimization and probabilistic analysis package.
At that time, thousands of bumper simulations were run using LS-OPT with positive results. NASCAR was so satisfied with the outcome that they committed to having these parts built before any physical crash test data, which of course added up to a sizeable savings. Still, the end goal for NASCAR on the track is safety.
"(Simulation) is very, very cost effective, but from my standpoint, I really measure the importance of the tool and the improvements it can make to the design and the confidence it gives us in that design," says Patalak. "The dollars are really secondary when it comes to safety for us, but we can really go and run a test, and literally not be surprised with what happens because of the simulation work."

Time to Shift Gears
Don't miss Episode 9 of our online docuseries "Driven by Simulation." We'll be shifting gears to consider how automotive suppliers APTIV and Infineon are using simulation to develop the software systems, and systems of systems that will define our travels in the future.