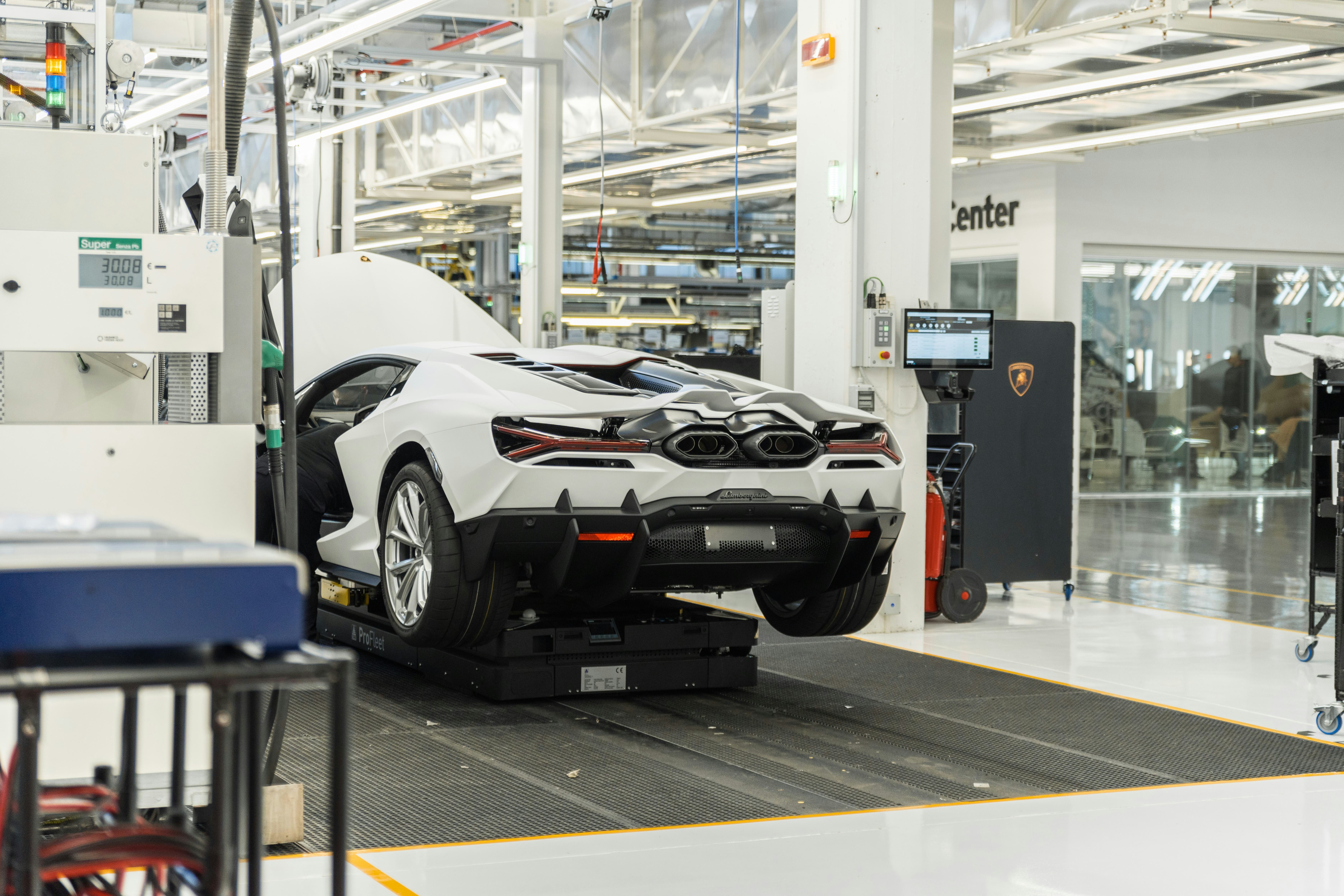
You know things are getting a little wild on the automotive landscape when Lamborghini releases a hybrid. Trust me, though, when I tell you that this isn't an Italian Prius. It's a car that has forced a historic brand to develop new technologies and establish new partnerships in order to build something far more advanced than what's come before.
This is the new Revuelto, Lamborghini's upcoming, 1,001-horsepower supercar. It'll sprint to 60 miles per hour in just 2.5 seconds and keep on going to a speed of... well, even Lamborghini isn't sure. “Over 350 [kilometers per hour or about 218 mph],” Massimo Delbo, a representative from Lamborghini's Heritage department, assured me, but he left it at that.
The Aventador was Lambo's biggest bull in its regular production line for over a decade, a period that saw radical changes throughout the entire automotive industry. The Revuelto is pretty radical, too, not only carrying Lamborghini's first plug-in hybrid system but having a carbon fiber construction so complex it requires three separate techniques for laying up the strong, lightweight material.
That's why, as a car enthusiast, I couldn't resist an exclusive visit to the factory where the first cars are just starting to roll off the production line.
Gorgeous Details
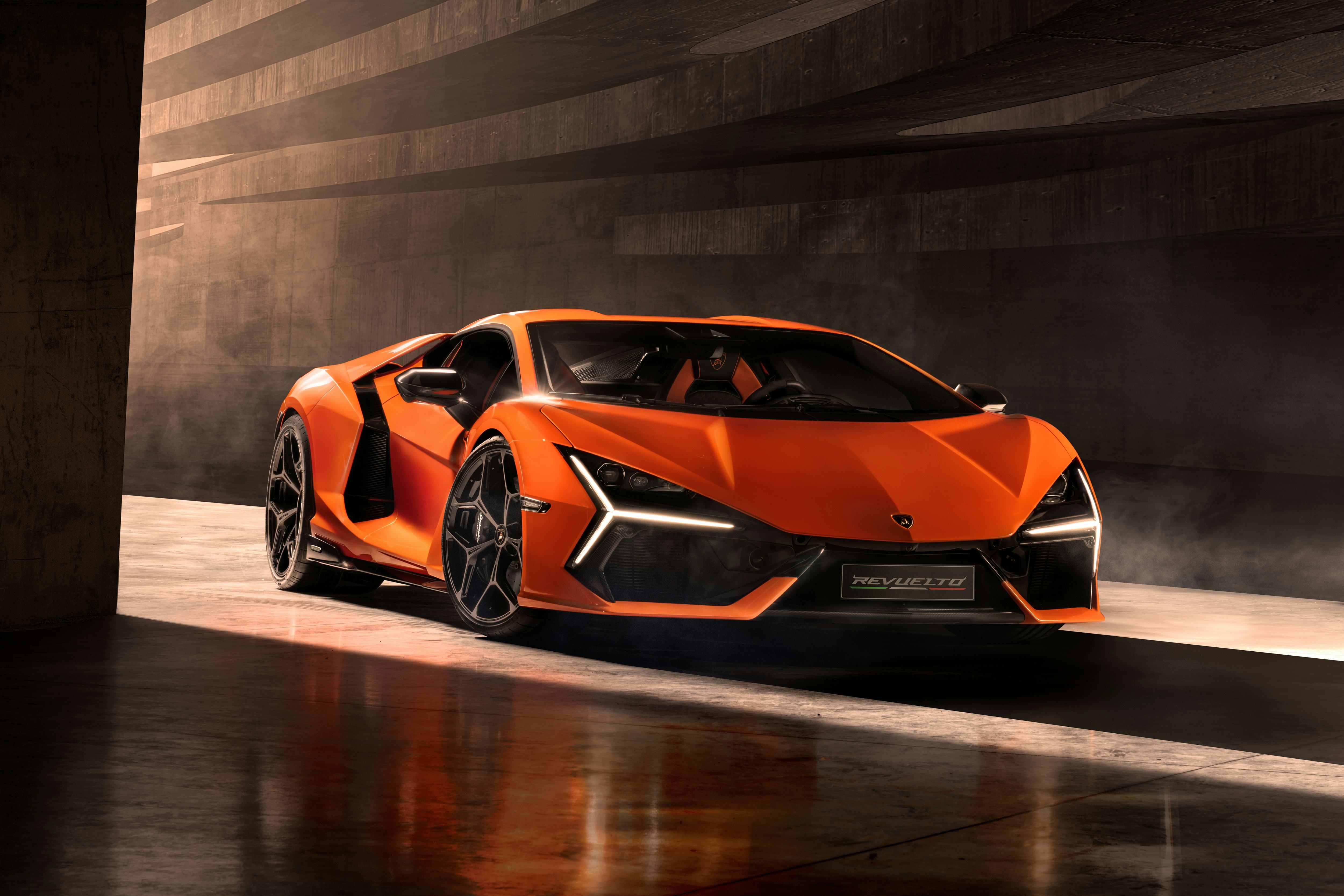
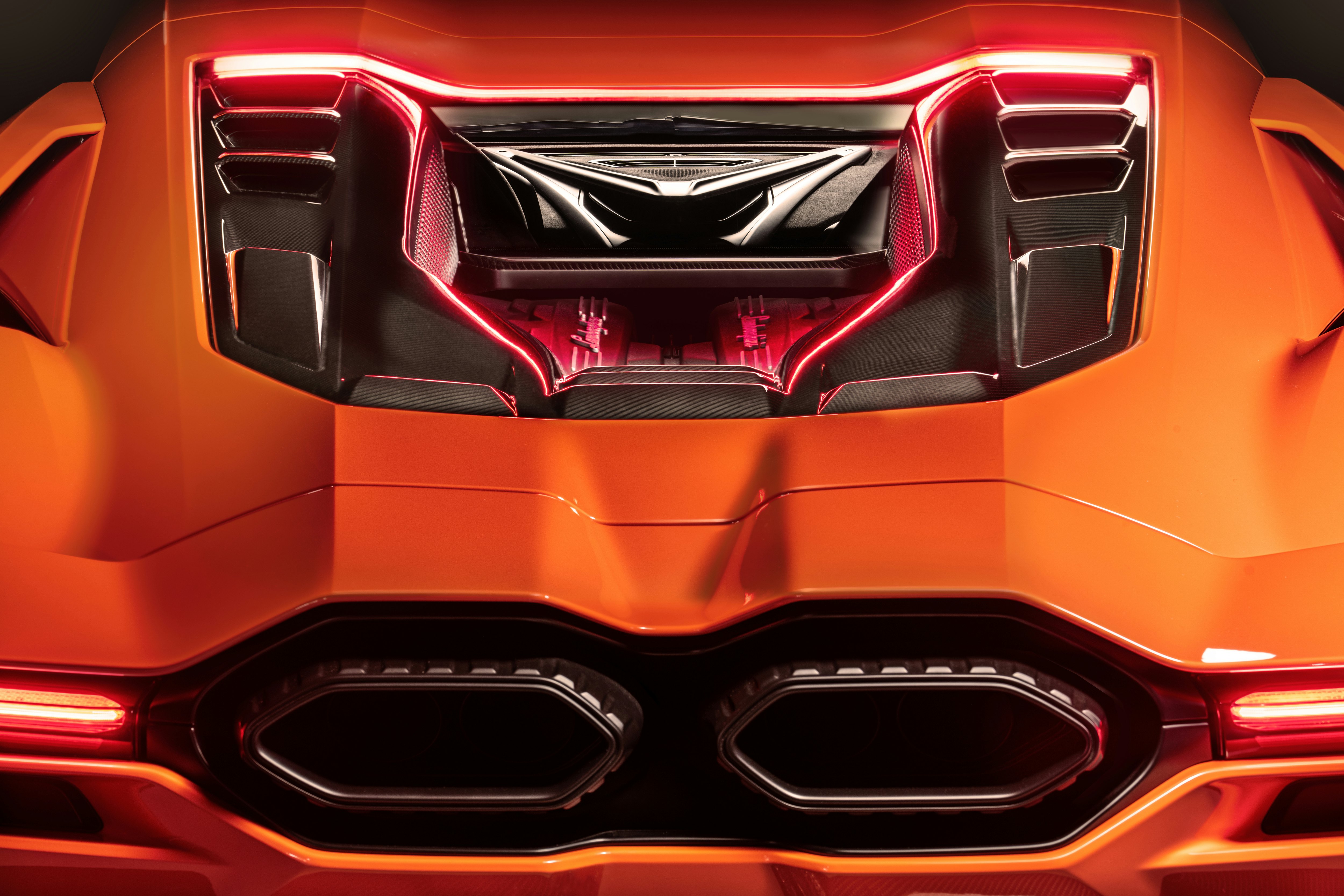
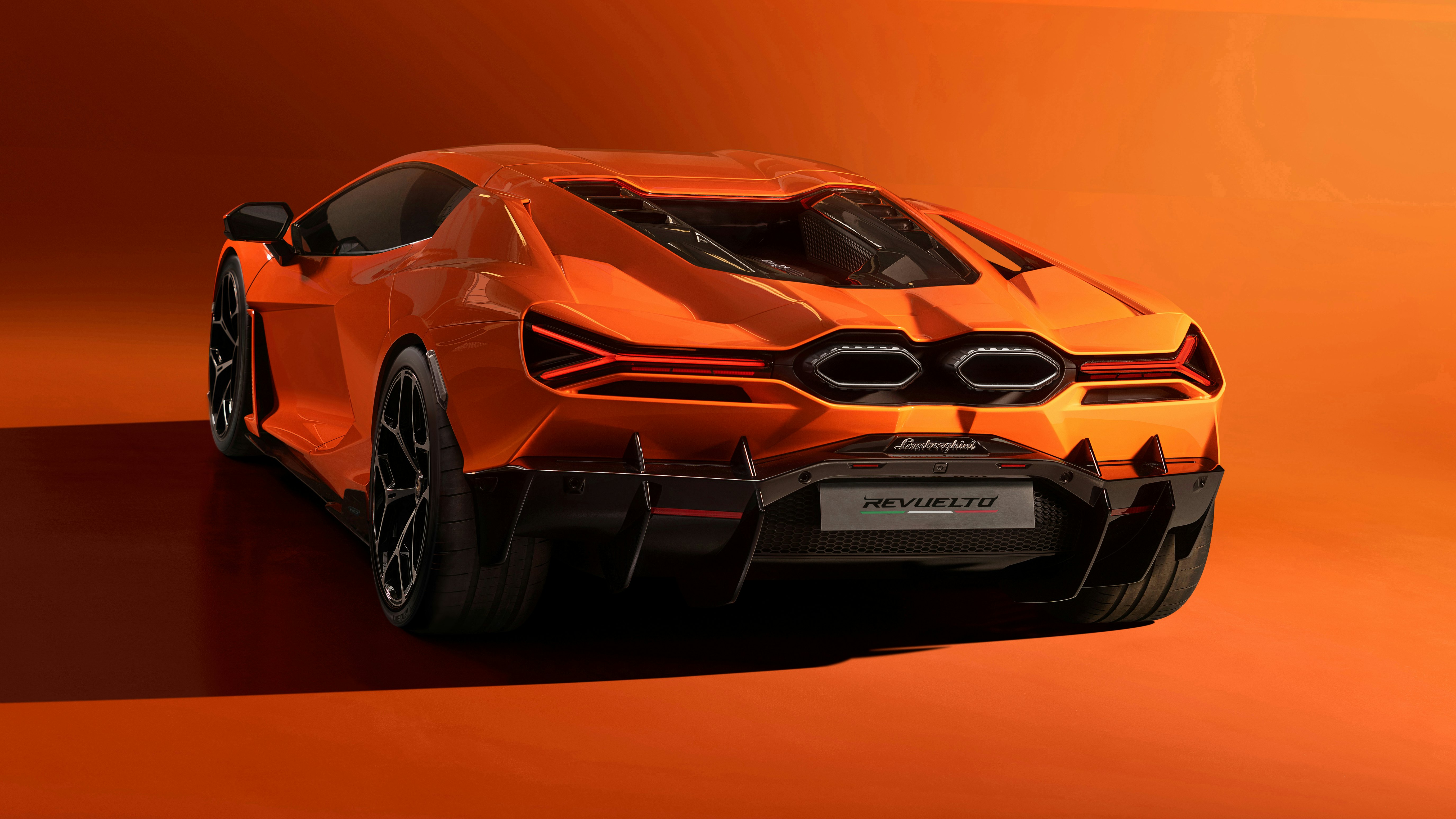
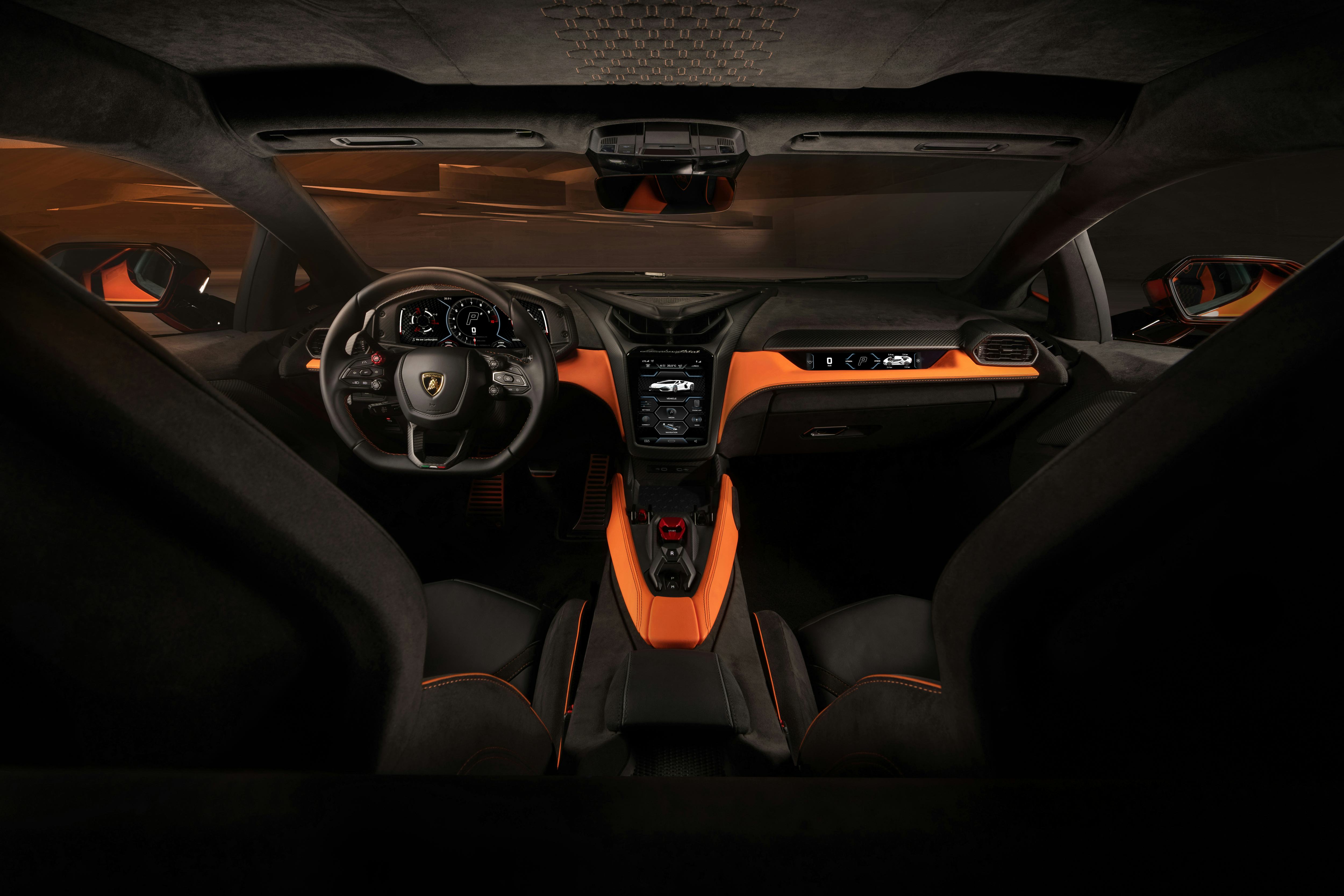
To some degree, the Revuelto seems like another extension of the big V12 lineage from Lamborghini that dates back to the iconic Miura back in the 1960s, the car that first earned the title "supercar."
The Revuelto is long and low, wide and mean, bearing an unmistakably angular and angry style. The main power source is also pretty typical for the brand: a 6.5-liter V12 sitting at the back making a whopping 813 horsepower.
That's all similar to the car the Revuelto replaces, the Aventador, but there's one significant difference to start: the engine is pointed the other way. On the Aventador, the engine is oriented such that the transmission and center differential, the part that sends power to the front wheels, is pointed toward the front of the car.
In the Revuelto, everything is backwards. The new, quick-shifting dual-clutch transmission hangs off the back of the engine. Lamborghini can mount it this way because that engine no longer needs to worry about sending power to the front wheels. Those wheels are entirely driven by a pair of 110-kilowatt motors, one per wheel.
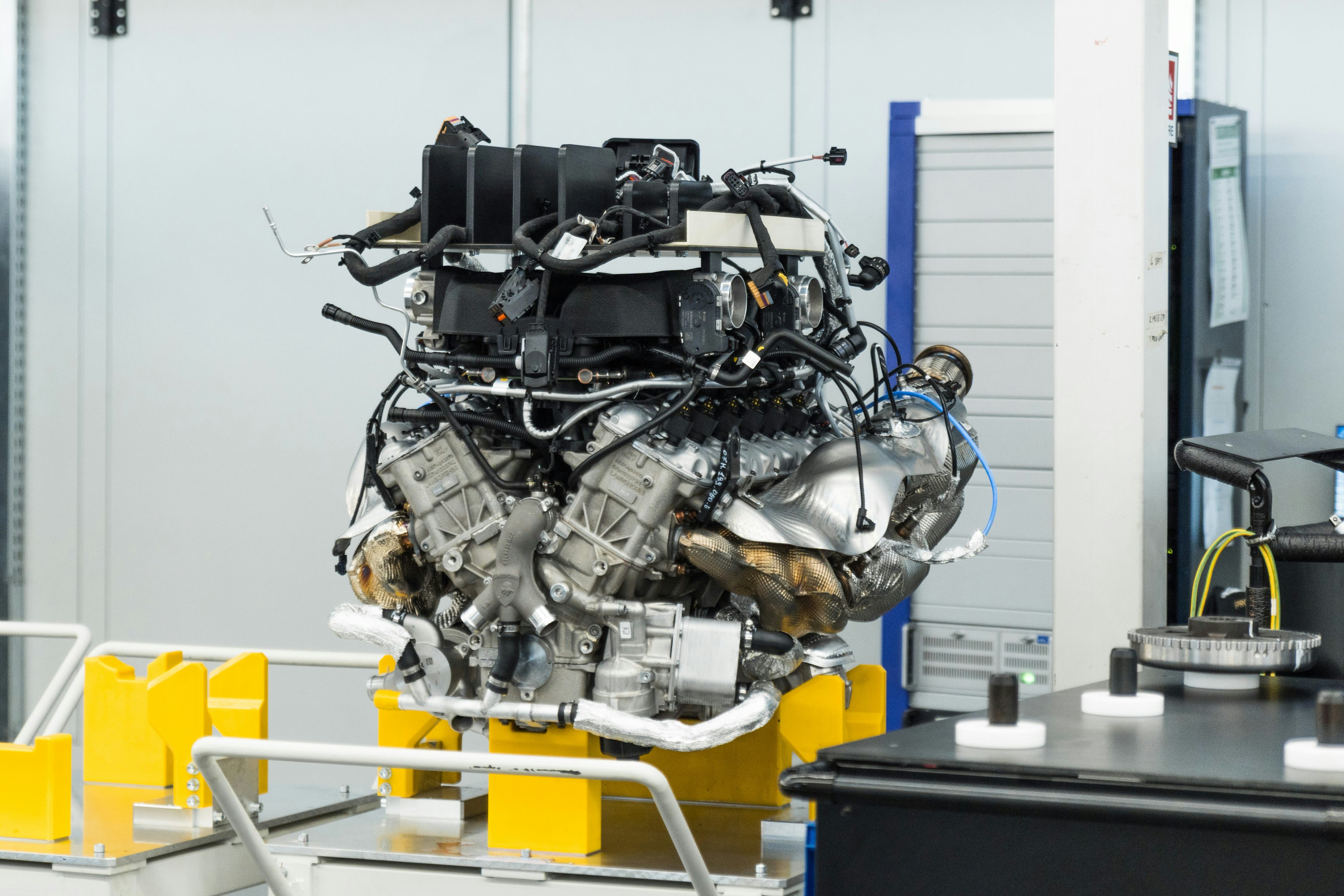
No longer needing a mechanical driveshaft running lengthwise to turn the front wheels, Lamborghini engineers filled that space with batteries, 3.8-kilowatt-hours worth, powering those two electric motors up front plus a third one situated on the V12 itself.
That's a pretty small battery by modern EV standards, about five percent of that found inside a Tesla Model 3. Unsurprisingly, the Revuelto won't get very far on just its battery alone — just about eight miles max.
But emissions-free range isn't really what this is all about. The Revuelto is designed for performance. Its 1,001 horsepower is 232 more than the outgoing Aventador.
Handling all that power while cutting weight to offset the new electrical bits required a new, more advanced chassis, and that required some big factory upgrades.
Factory Floor
For a massive, sprawling factory, the place where the Lamborghinis are built is full of light. Windows pierce the ceiling and endless lights make for an almost blinding space. The white, polished floors — crossed by robots shuttling parts one way or entire cars the other — just add to the effect.
It's a vastly different proposition from 60 years ago, where in this very spot, the first Lamborghini V12s were built.
There were no robots back in 1963, of course, but the process of building the Revuelto is still remarkably manual. “The activity, the assembly, is only done by the hands of our skilled people in Sant'Agata,” Chief Manufacturing Officer at Automobili Lamborghini, Ranieri Niccoli told me.
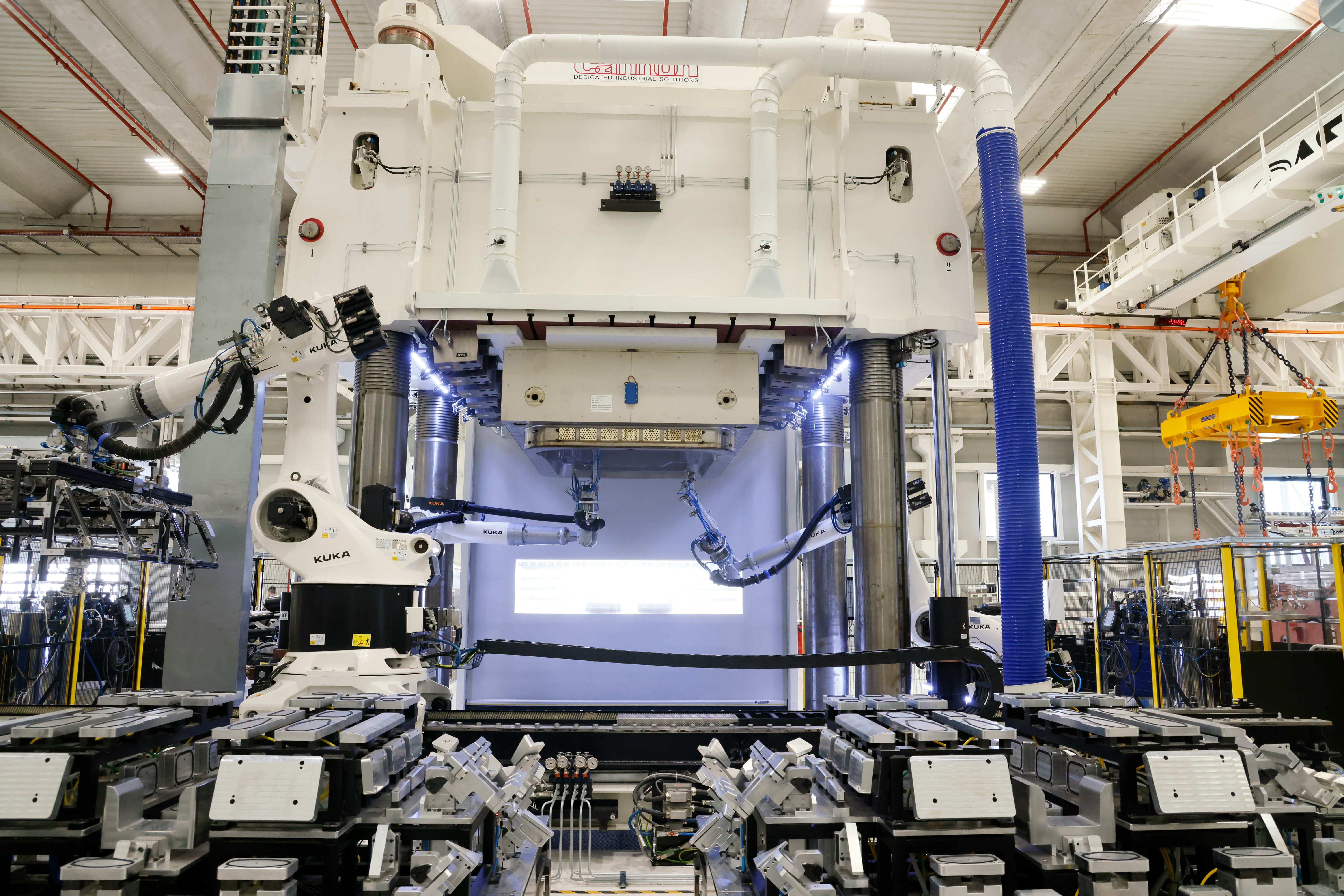
Niccoli ushered me through the place where the Revuelto comes to life, each chassis whisked from one build station to the next on a Dürr ProFleet Automated Guided Vehicle. These automated, mobile platforms mean no rigid assembly lines. Inside the factory, Revuelto chassis move from place to place, fussed over by squads of black-clad Lamborghini specialists at every stop. “They give us a lot of flexibility,” Niccoli said, of the robots.
Even the V12s are assembled by hand here, not far from where the leather interiors are stitched together, a fleet of 14 sewing machines staffed by as many specialists, bringing together hides all dyed in a range of eye-searing colors.
The bulk of the car, though, is made of a different sort of fabric: carbon fiber. To see that, I was ushered off from the oldest part of the factory floor to the newest.
Complex Carbon Fibers
Lamborghini's sprawling complex has grown deeper over the years, literally spreading farther afield, taking over once verdant pasture land as the company raises building after building to meet the demands for greater volume and, in the case of Revuelto, greater technology.
Lately, the big need has been in the creation of advanced carbon fiber techniques.
The composites facility is hidden in the back of Lamborghini's industrial complex, where sweet but noxious fumes of resins hang in the air outside. This facility was initially built for Aventador, which also has a carbon core, but has been expanded massively for Revuelto. It's split up into numerous rooms, serving to keep those fumes at bay but also ensuring that each type of carbon fiber is kept at its optimal temperature.
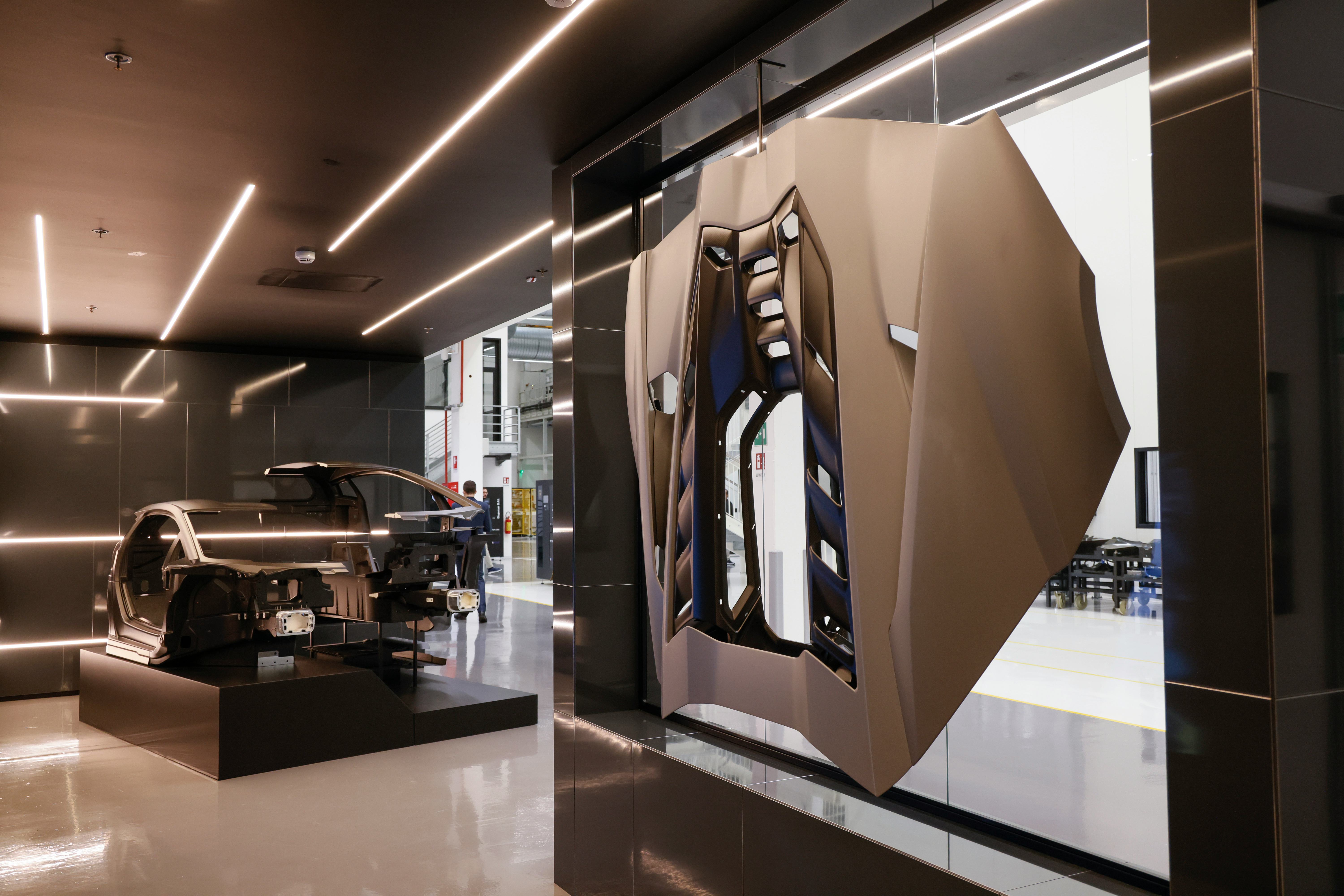
Carbon fiber is exactly what it sounds like, strands of black material woven or mixed together and suspended in resins that harden through a complex curing process. Though initially flexible and soft like fabric, cured carbon fiber is incredibly strong and light. Formula One cars are entirely made of the stuff, while the Revuelto has more than any Lamborghini before.
Three different carbon fiber techniques are used to make up the Revuelto's monocoque, the very core of the car to which everything else mounts. For the first time, that carbon fiber extends all the way to the nose of the car, including the front crash structure, while a slender aluminum subframe bolts on the back to cradle the V12 and rear suspension.
The first technique is the most traditional, involving what's called long-strand carbon fiber. Long-strand means that this carbon has the beautiful, delicate weave that you may have seen on the interiors of some high-end sports cars. It's beautiful to behold and also creates a smooth surface for painting, so this is the technique that Lamborghini uses for the exposed surfaces of the Revuelto, like the A-pillars and roof.
This fiber comes in massive rolls that are laid out and precision-cut by machines in a process that's exactly like creating a pattern for a dress —if that dress were made of wildly expensive, resin-impregnated material. Workers assemble those cut pieces into kits, then another group starts the assembly process.
Piece by piece, the technicians wrap individual sheets of fibers around molds to form the key structures of the car, trimming and pressing each piece so that it sits just so, fibers perfectly aligned with the others.
Once everything is in place, the entire component (which could be as large as the car's roof) is put in a vacuum bag, sous vide-style. The air is sucked out, which spreads the resin evenly throughout the part. Parts are then loaded into giant ovens called autoclaves, where they'll bake for hours at a precise temperature.
Creating a single part in this way can easily take a full day.
A second technique uses what's called short-fiber material, or forged carbon fiber. Here, shorter, fragmented strands are mixed together to create a rather more chaotic looking sheet that's a little less aesthetically pure but every bit as strong and, crucially, a lot easier to work with. Lamborghini uses fewer, thicker sheets of this to create the complex structural elements of the car.
The process is much the same, but quicker, with material being put into a form and pressed. Since these short-fiber pieces come out rougher, they're used for less visible components, like the core of the monocoque.
Finally, Lamborghini is using a newer process called forged composite molding. Here, large, flat sheets of carbon fiber are put into a giant press, much like those used to stamp out traditional automotive body panels. However, this press simultaneously heats and cures the resin. Once it comes out of the press, the part simply needs to cool down and be trimmed and then it's ready to be bolted on the car. The whole process takes only 90 minutes.
Assisted Craftsmanship
All that composite work, plus the bulk of the Revuelto's assembly, still happens manually, but new technology is in the loop here as well. For example, to run the car's complex wiring harness through the chassis, Lamborghini engineers use Microsoft HoloLens 2 augmented reality headsets to get visual prompts on where to mount which wire.
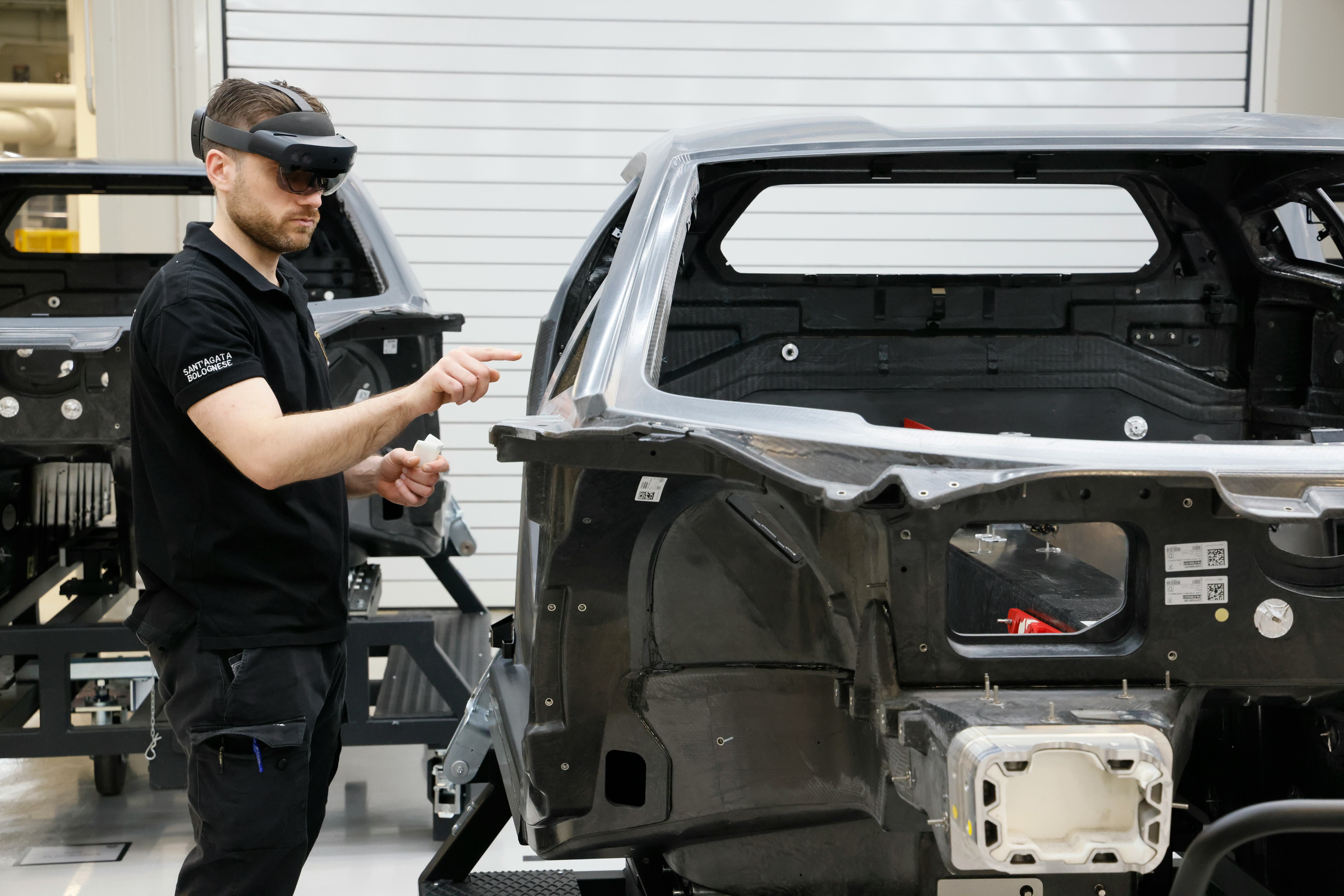
Though there is plenty of automation, robots used to precisely cut edges of carbon fiber components or apply exact amounts of adhesives to bond them together, the process is always guided by the hands of talented workers.
Appropriate, then, that all these advanced facilities have grown out from Lamborghini's original factory, where Ferrucio Lamborghini's first cars were built, by hand, 60 years ago.
Lamborghini is just beginning to ramp up Revuelto production, with plans to eventually produce seven of the hybrid monsters per day out of its factory. First deliveries are due by the end of the year, but if you're hoping to get one, mind your turn. Two years' worth of production is already spoken for.