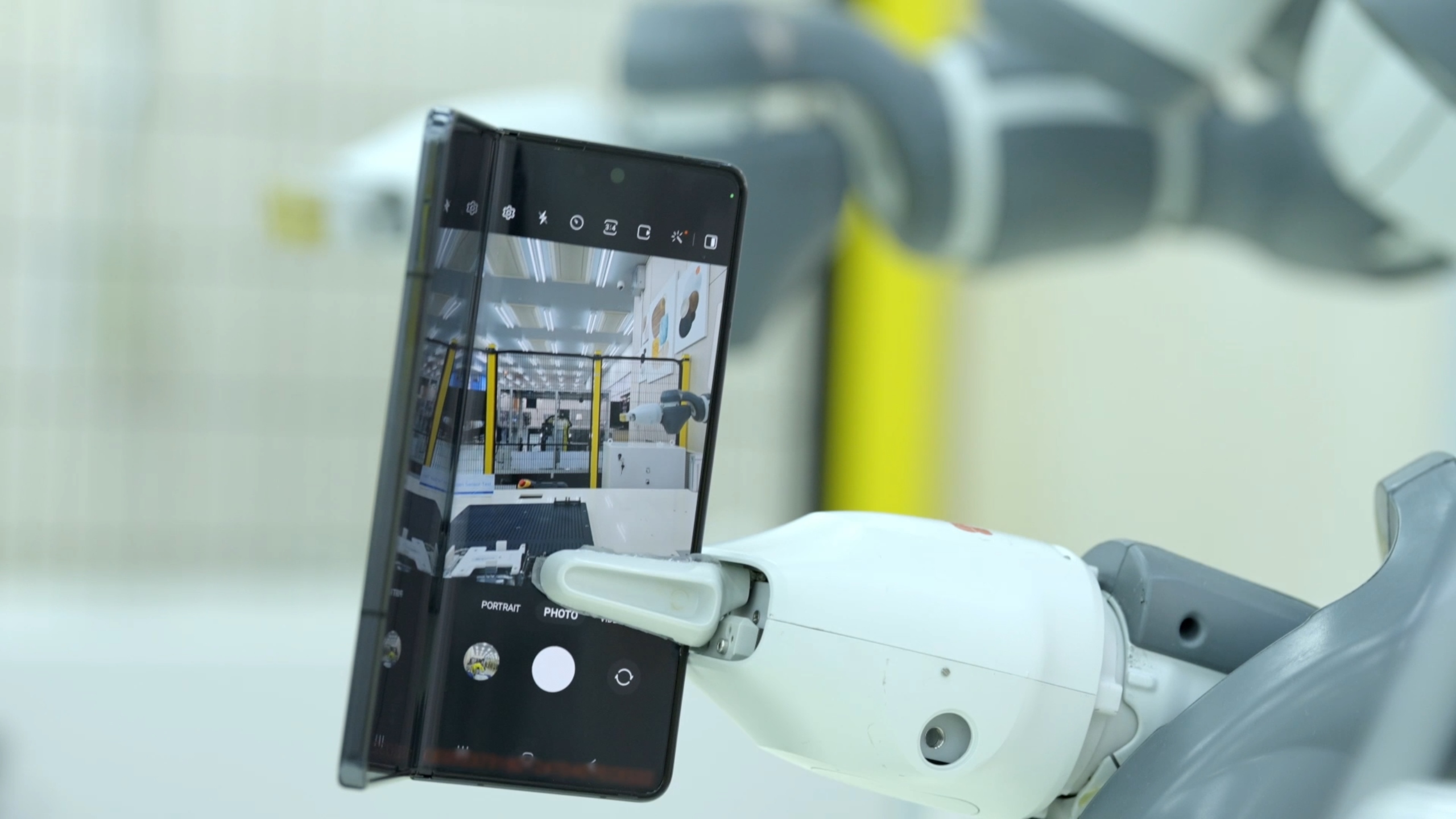
Twice a year, Samsung brings journalists from around the world to see their latest devices at Galaxy Unpacked. The new phones, foldables, tablets, smartwatches, and other devices that Samsung unveils at Unpacked are the result of years of R&D that we, the general public, aren’t privy to. When you stop to think about it, it’s actually incredible how companies like Samsung can pack so much tech into a device that fits into your pocket or sits on your wrist. That’s why when Samsung invited me to tour its so-called “Smart City” following the most recent Unpacked event, I knew I couldn’t miss the chance to see how they build the Galaxy Z Fold 5 and Galaxy Z Flip 5.
It’s not often that we get a chance to tour the factories where smartphone makers manufacture, assemble, and test their devices. I’ve only done it twice before, once with OPPO and later with Huawei, but both times were before the COVID-19 pandemic, so they may as well have happened over a decade ago in my mind. Plus, I wasn’t allowed to take any photos or videos while on those tours, and I’m still kicking myself for not taking detailed notes that I could look back on.
This time, however, I came better prepared. While I also wasn’t allowed to take any photos or videos of Samsung’s manufacturing or assembly lines, I jotted down eight pages of notes in the Samsung Notes app using the S Pen on my Z Fold 5 review unit (which was maybe overkill, but I needed an excuse to test the phone’s features out anyway). I also reached out to Samsung after the tour to get some of the presentation materials they showed us and a video showing a lot of the manufacturing and assembly steps we saw. Here’s a breakdown of the best parts of the tour.
Disclaimer: Samsung covered my travel and food expenses for this trip. However, they did not ask me to write this article nor did they have the opportunity to review this article or offer any editorial input before its publication. I did consult extensively with fellow attendee Dylan Huynh, however, as he also attended the tour and extensively took notes of his own.
Gumi: The city where the magic begins
Gumi is a city located southeast of Seoul, and it’s one of South Korea’s major industrial centers. Gumi is home to industrial complexes from literally thousands of different companies, but Samsung’s is among the biggest in the area. Samsung has two major campuses here, multiple dormitories, a hospital, a school, various welfare, fitness, and lifestyle centers, and other buildings to accommodate the many employees that live and work in the city. Collectively, Samsung refers to its Gumi operations as its “Smart City,” which is fitting given its size (~36 km²) and population (~14,000 employees).
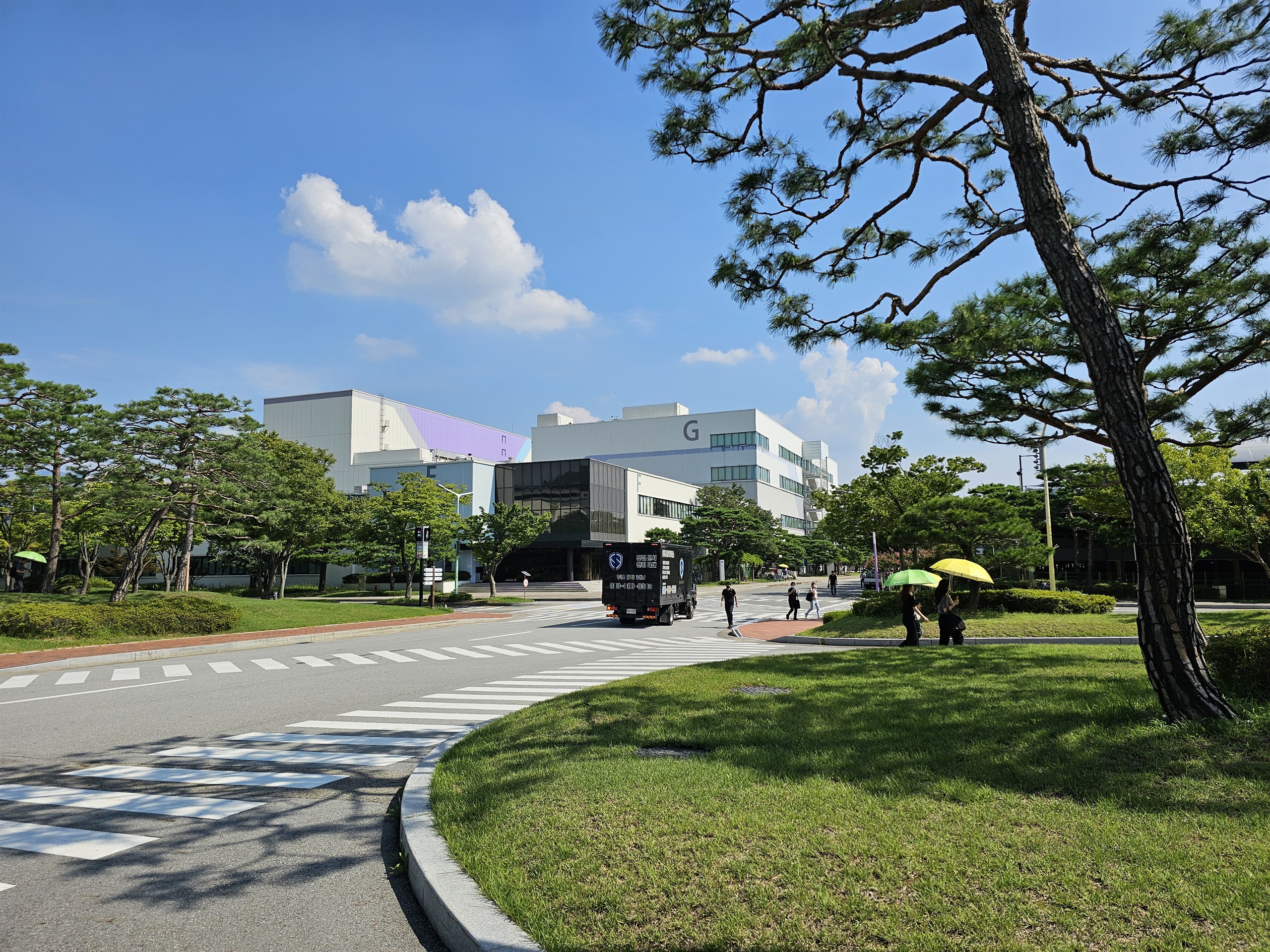
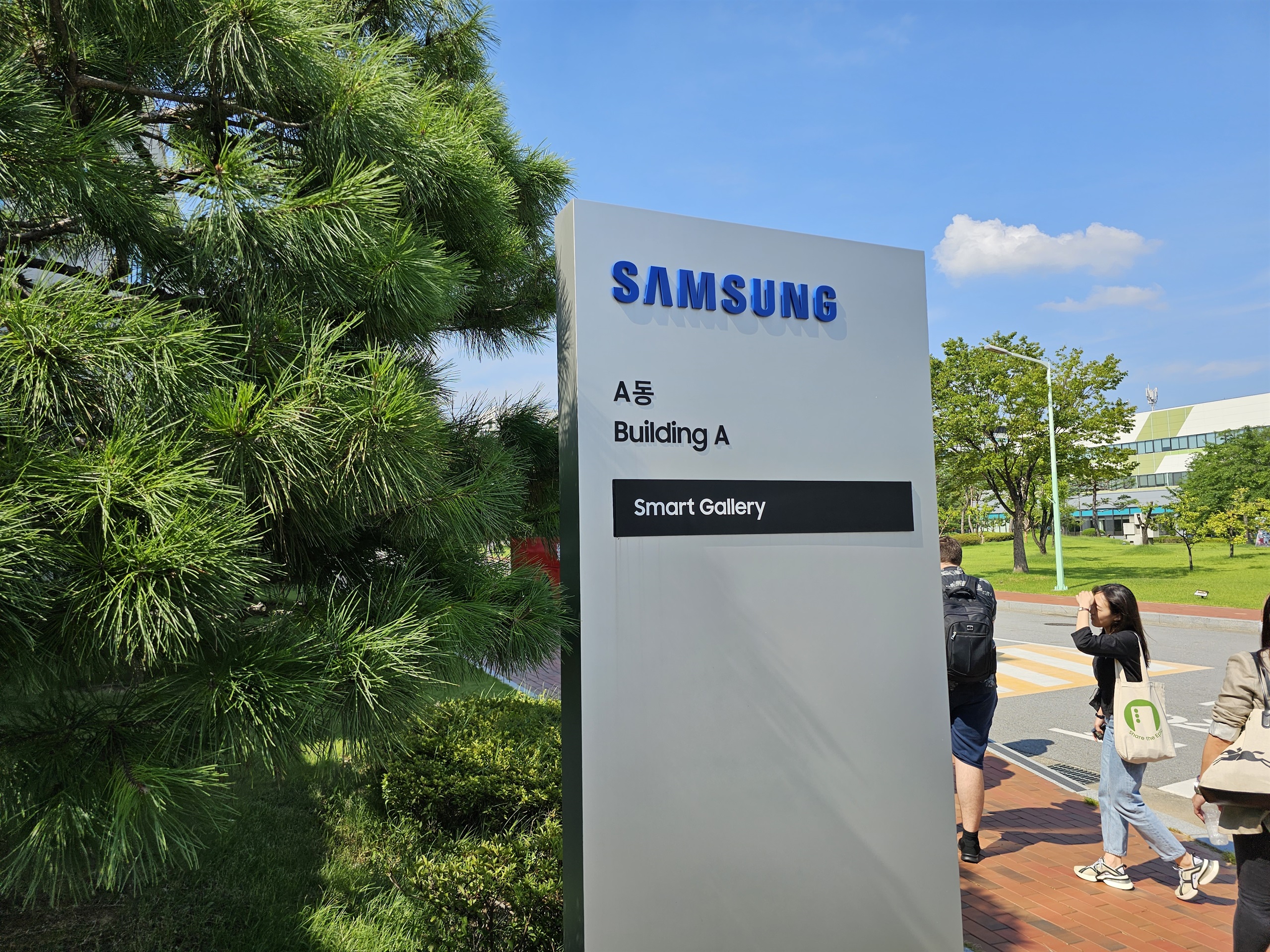
Samsung’s Smart City, of course, isn’t the only location where the company assembles devices, as they have assembly line hubs in Vietnam, India, Indonesia, Brazil, Turkey, and Egypt as well, but it’s where they do a lot of R&D on how to optimize the manufacturing and assembly of their latest devices. Thanks to these refinements, the company has been able to churn out over 6 billion smartphones to date across all its factories worldwide.
When you hear that figure, you might think that Samsung’s got it all figured out when it comes to automating smartphone production. While Samsung has automated a lot of its processes already and is working on automating even more, there are several steps that still require human involvement. But I’m getting ahead of myself here because I want to talk about some of the cool things Samsung teased us with before we walked down the manufacturing and assembly lines.
Samsung’s smartphone museum
Our Smart City tour began with a walk down memory lane through Samsung’s smartphone museum, where we saw an exhibit of the key devices Samsung made throughout its many years. We saw devices like the first Galaxy S, the precursor to the first Note (RIP), i.e., the Galaxy Edge, the first Galaxy Fold, and so on.
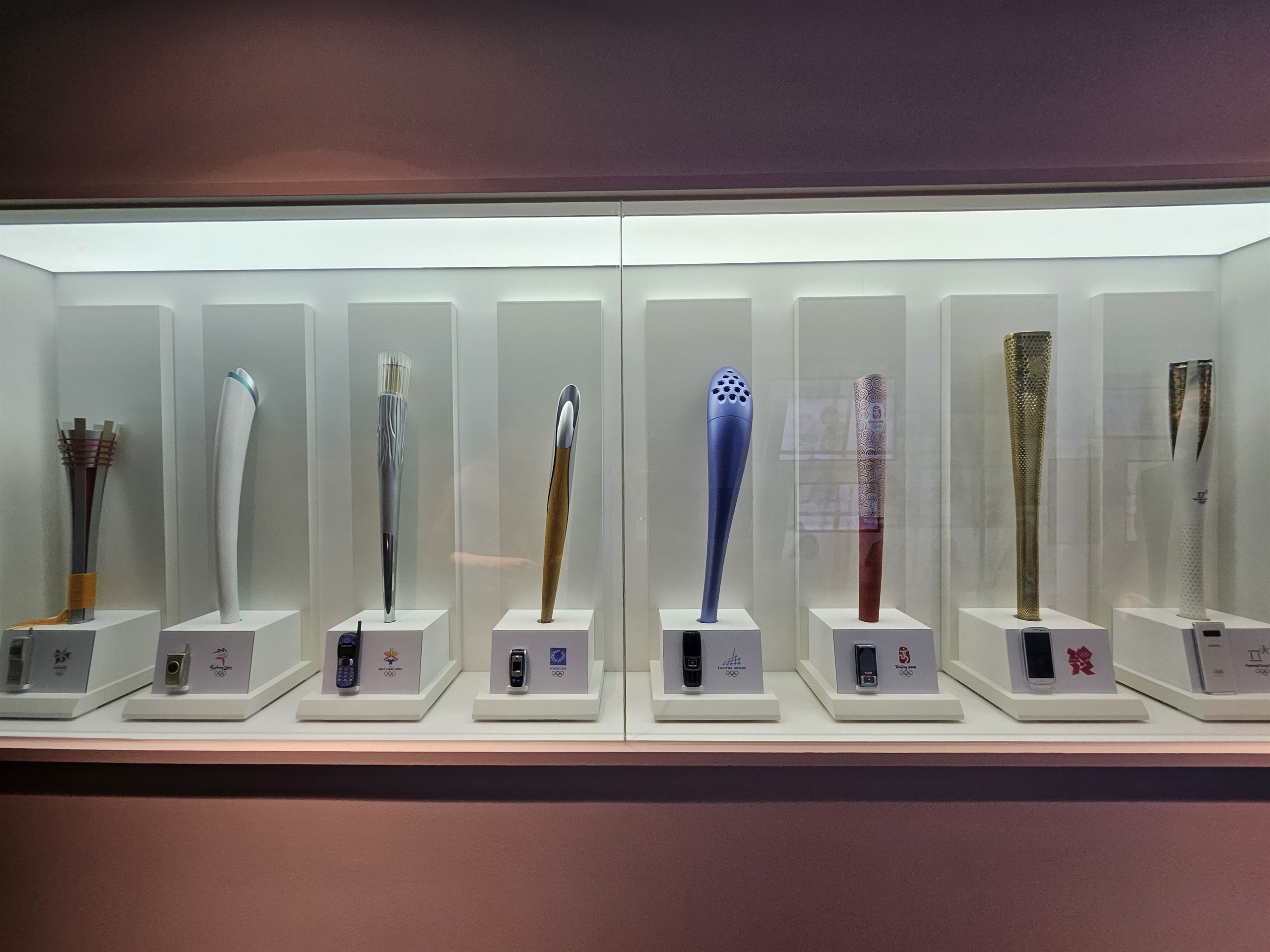
Better yet was the showcase of every smartphone model Samsung had ever made. Samsung filled a room with glass cases that held one phone of each model they made. We even got to see the limited edition Olympic-branded phones Samsung made, as well as the actual torch used to start the 2018 Winter Olympics in PyeongChang. As a reporter who has been covering mobile tech for years, I knew that Samsung made a lot of phones, but seeing literally every phone they ever made in one room was really something else.
Okay, I lied: There was one phone missing from the exhibit. I’m sure you know which one it is, but in case I need to spell it out, it was the Galaxy Note 7. I’m not surprised that Samsung basically pretends the Note 7 never existed, given the huge reputational hit they took by releasing that device, but it was still amusing to see it scrubbed from existence not only in the museum but also in other graphics they had that showed the timeline of their flagship device releases. (They did have the Galaxy Note FE on display, though.)
After the smartphone museum tour, we entered a room where we saw cross-sections of the Galaxy Z Fold 5 and Galaxy Z Flip 5. Every part was separated and arranged horizontally so we could see how the parts were stacked on top of one another. This was a precursor to the main tour, where we’d later get to see half-assembled prototypes of each phone where the hinge mechanism was fully exposed. Fun fact: the Galaxy Z Flip 5’s hinge actually has more parts in it than the Galaxy Z Fold 5’s (45 versus 41).
Before we could enter the manufacturing line, Samsung slapped stickers over the cameras on all our phones so we couldn’t take any photos. These stickers would be marked as “void” when removed, so Samsung would easily be able to tell if anyone tried to remove them, take photos, then slap them back on. That’s why all images from this point onward come from Samsung itself.
From a block of metal to a smartphone
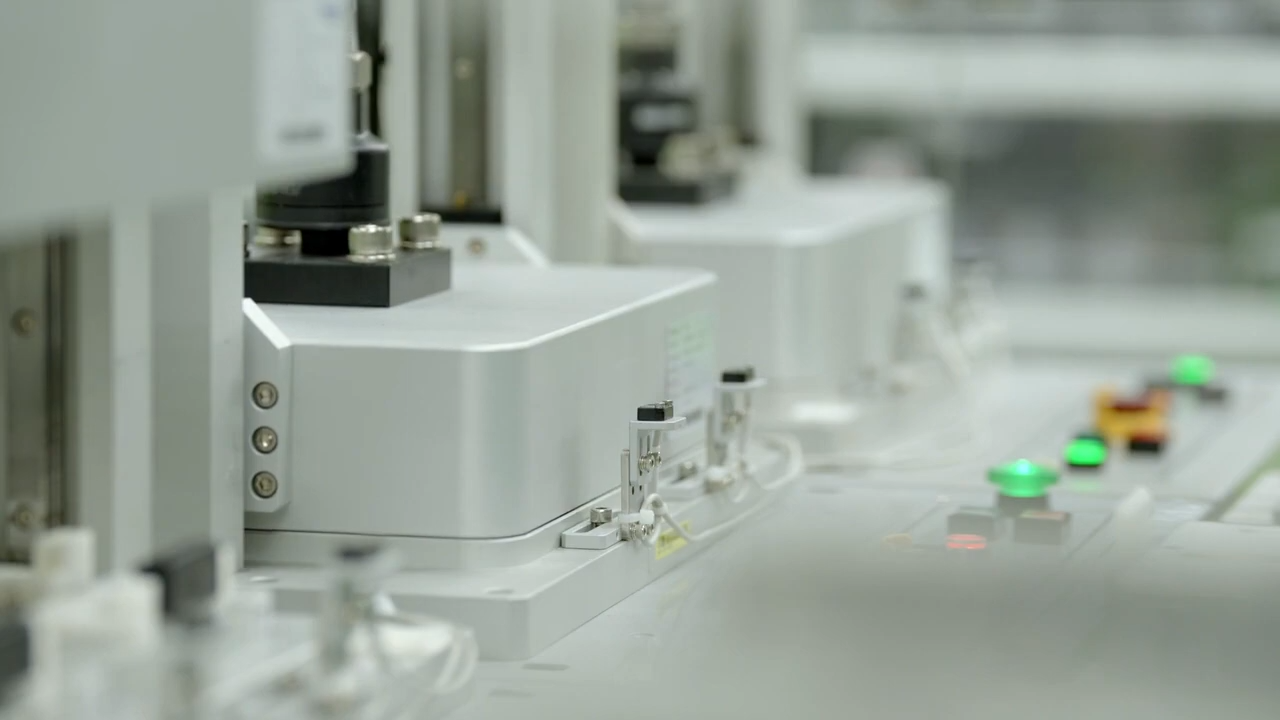
The first big leg of our tour covered how Samsung carves a block of metal like aluminum to make the mold used to mass produce a smartphone. This process creates what’s called an injection mold, and Samsung showed us how they used to only be able to make molds that could produce one phone at a time but eventually created molds that could produce multiple.
We also saw the CNC (computer numerical control) machines that Samsung designed to make these molds. They demonstrated the precision of their machining by carving out the word “Samsung” into a block of aluminum; the etching was so fine that the word “Samsung” was not only able to pop out of the block but also couldn’t be felt by hand when touching the metal. Samsung said each CNC machine had sensors that fed data to a nearby data center for further study and optimization.
The molds used to produce Samsung’s phones are carved with precision from a block of metal.
Samsung also showed off the different textured backs they tested, including some that were glossy and some that were matte. I really liked the feel of the different textures they experimented with, so I’m sad when a phone ships with a back that’s more “safe,” i.e., it appeals to more people, is cheaper to make, and is boring enough that it can be used to upsell people on other designs. Samsung does make a ton of different Galaxy phones, though, so not every single model can ship fancifully colored matte backs by default.
Speaking of color, Samsung repeatedly touted how it was working to reduce the environmental impact of its manufacturing process. They talked about how they recycled the aluminum scraps used to create molds so they could make more of them, and they also brought up how they were moving away from petroleum-based dyes for their metal backs in favor of more organic dyes. Samsung says that organic dyes like cocoa, gardenia, and cochineal now comprise up to 20% of the dyes they use for their devices.
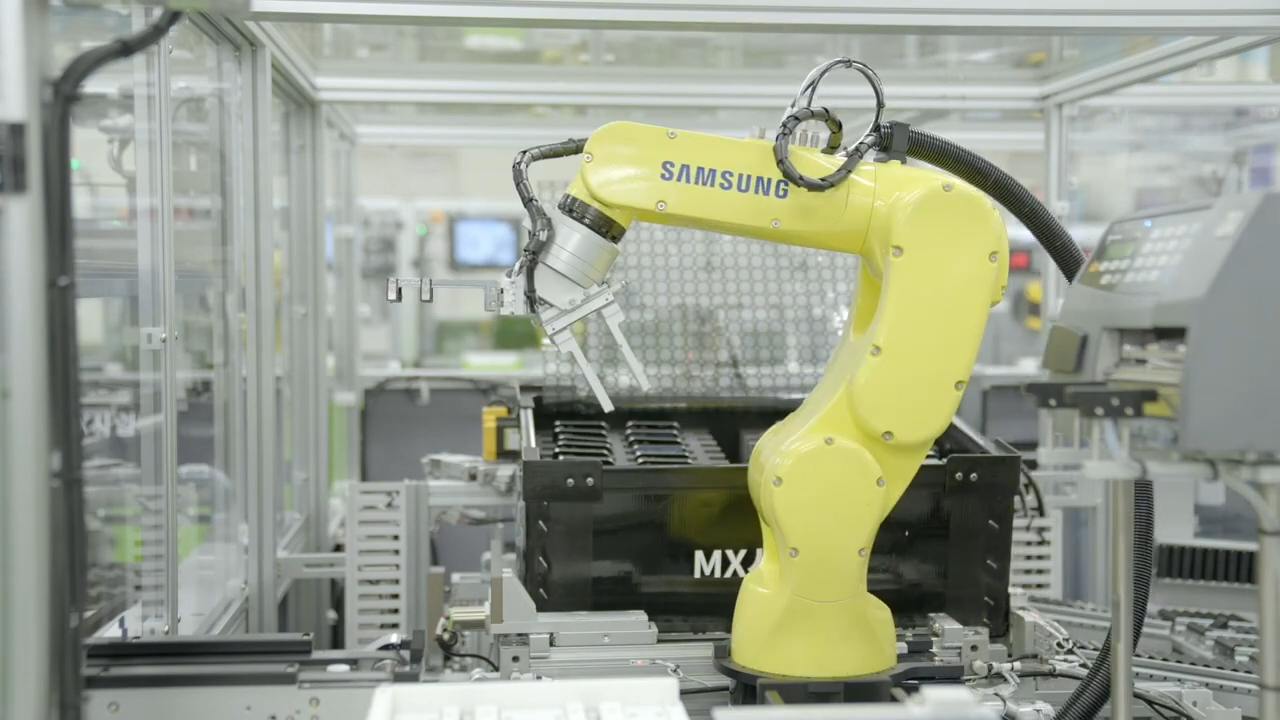
A lot of the really cool stuff we saw during this part of the tour came either from things Samsung showed us in a demo room off to the side or things they said or showed on screens, as we weren’t allowed to walk past a yellow line to get close to the CNC machinery or the machines used to polish, blast, and wash the metal blocks. This, however, was not a big deal to me, as at this stage of the manufacturing process, the metal blocks only barely resemble the design of a phone. You could notice things like rectangular cutouts for camera bumps, but that was it. Samsung even outright told us that they were actively working on their next Galaxy Fold, presumably called the Galaxy Z Fold 6, here because there was nothing we’d be able to discern anyway.
Before we headed over to the main assembly line, Samsung briefly showed us the area where the phones’ PCBs (printed circuit boards) were made. Using a surface mounting device (SMD) process, Samsung’s machinery rapidly mounts and solders components (about one every 0.047s) onto a large, dual-sided PCB that’s then cut into individual boards for phones. We weren’t able to see the SMD process up close, however, as the machinery was contained within a semi-clean room where the temperature, humidity, and number of dust particles were constantly being measured.
Because they were so concerned with dust particles entering the semi-clean room, Samsung asked everyone to put on a disposable shoe cover before we even peeked through the glass. Given how often people have to put these shoe covers on, Samsung actually had a machine that automatically wraps the cover around your shoe when you stick your foot in. And just for added protection, we had to walk over a bumpy part of the floor to catch any stray dust particles that we may have stepped on before entering but after putting on the shoe cover. We had to keep these shoe covers on as we toured the next area, too.
Putting it all together, one step at a time
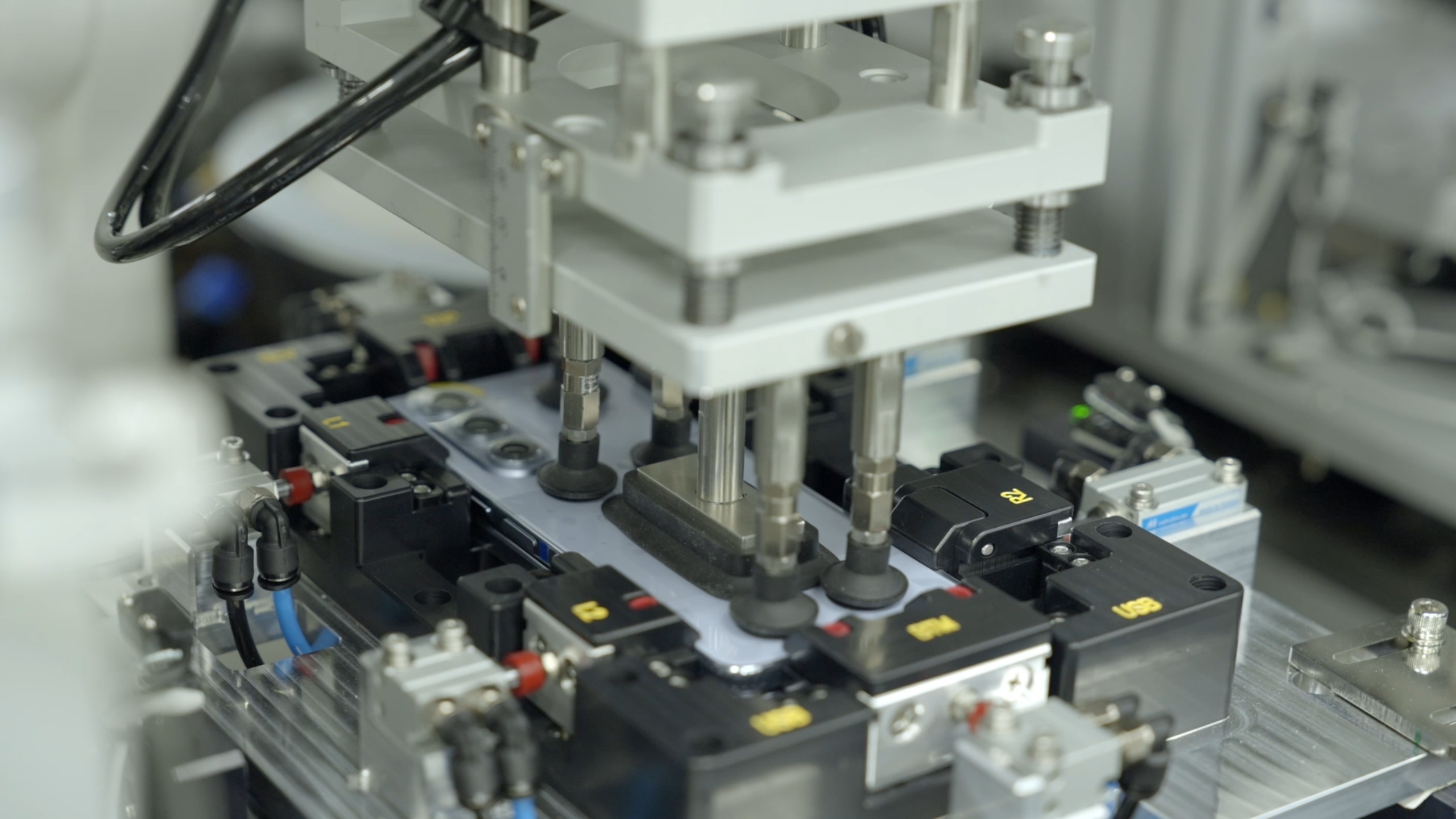
After all the individual components, like the chassis, SoC, display, battery, etc., are manufactured or brought into the facility, it’s all put together in the main assembly line. In the Gumi facility, there are a total of 25 assembly lines, though only 16 were actually in use at the time of our tour. Because of this extra capacity, Samsung is able to act as a contract manufacturer for other OEMs. But we were there to see Samsung phones being made, and that’s exactly what we saw.
Samsung guided us down the middle of two assembly lines: To our left was a line that was assembling the Galaxy S23 Ultra for Verizon, and to our right was a line for the Galaxy Z Fold 5. There was also a line for the Galaxy Z Flip 5, one line further to our right, but we weren’t allowed to walk over to it. We did, however, get to see how materials are transported around the room while we were confined to our lane: Big robots called AGVs (automated guided vehicles) patrol the floor on designated paths marked by silver lines.
Samsung showed us two massive assembly lines where it builds the Galaxy Z Fold 5 and Galaxy S23 Ultra.
Each assembly line is massive, which makes sense since there are so many individual components that need to be put together and then inspected. Many components can only be tested once they’re added to the basic frame of the device since the motherboard needs to power up to load the testing tools Samsung uses during assembly.
One of the more interesting tests during the assembly process was the one for water resistance, which, contrary to what one might think, didn’t involve submerging the phone in water. Instead, the phones were inserted into a chamber, and 15 kPA of air was pumped inside; if the sensor detected any expansion after 20 seconds, then it failed the test.
Another interesting test is the one that corrects for camera parallax. A machine takes photos of a specific pattern with each rear camera and then calibrates accordingly. Then there are chambers to test the various radios, like WiFi, Bluetooth, Ultra-Wideband, and NFC (specifically, Samsung Pay).
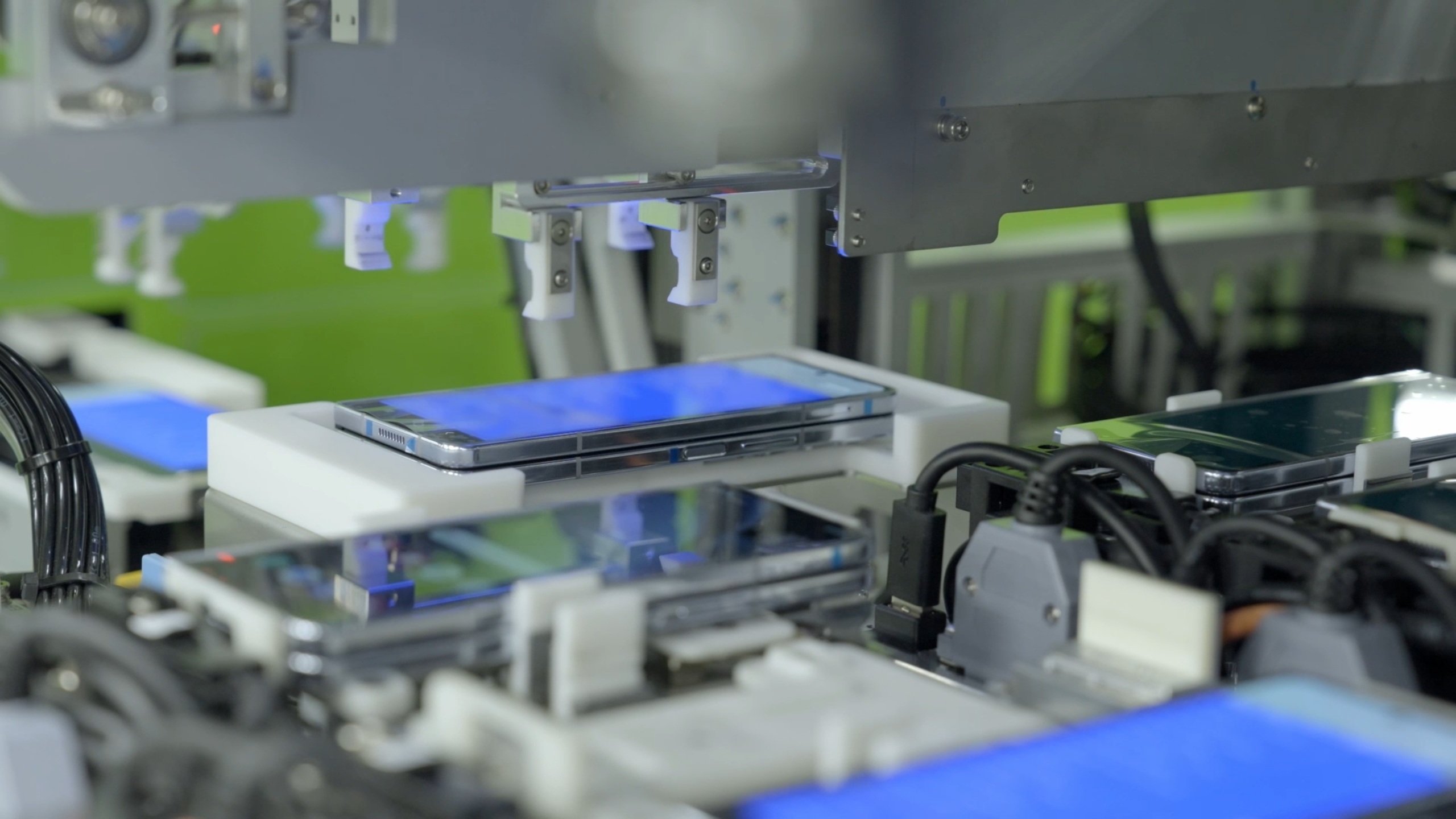
Given how many components there are, some are bound to fail inspection. Devices that fail a test are ejected from the assembly line and placed on a rack for a human worker to inspect. This is seemingly rare, however, as Samsung told us during the tour that the failure rate is only 0.7%.
The low failure rate can be attributed to the quality of parts, of course, but also to how optimized and automated the process has become. As I mentioned before, though, Samsung has yet to fully automate every step of the assembly process. Notably, the last step, packing, has yet to be automated. Samsung still relies on manual labor to pack the assembled phones into boxes and apply labels to them.
However, Samsung is actually running a pilot line that fully automates the entire assembly process, which includes packing. The line that assembled the Verizon Galaxy S23 Ultra was actually part of this pilot program, whereas the line for the Galaxy Z Fold 5 still had workers manually applying the screen protector and packing the device into boxes (with the help of various tools and machines, of course). Samsung told us that it’s working to fully automate the entire assembly process by the end of this year; it’s already automated 9/12 steps in the process but is still working on automating the intake and verification of materials from vendors.
It’s not over once the phones are assembled
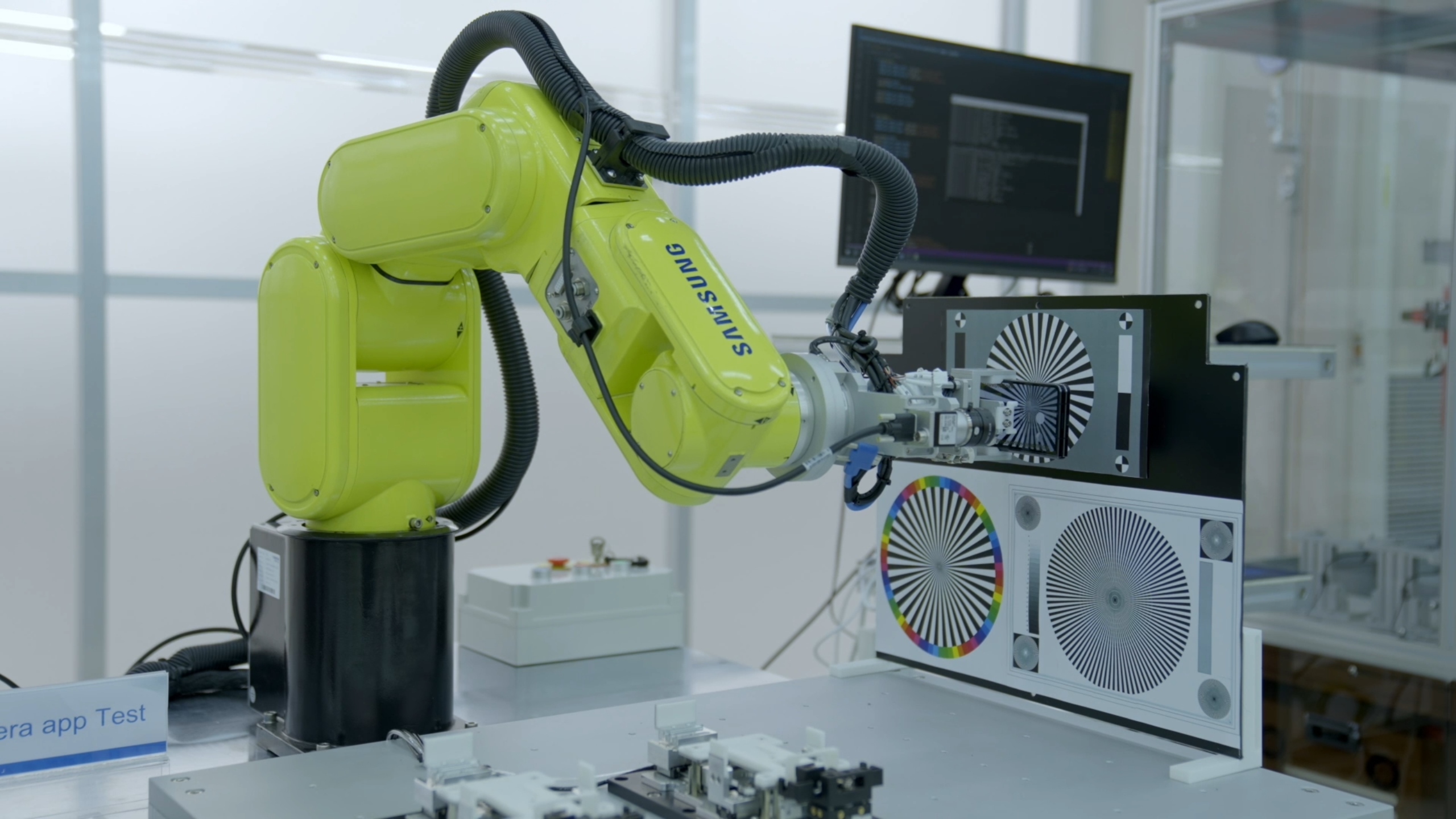
The tests that Samsung’s robots run during the assembly line are hardly representative of real-world use, but that’s not the point. Those robots only test that the hardware works to specification. In their automation testing lab, Samsung puts its phones and smartwatches through a variety of different conditions to test various features and mimic real-world use. These include:
- Accelerated aging: Samsung runs a script that continuously loops through various actions, like making a call, watching a video, etc., in order to extrapolate how the phone might behave and perform after years of use.
- Activity detection (swimming): Two smartwatches are placed on the wrists of robot arms that simulate a swimming motion.
- Bluetooth connections: A robot constantly opens and closes the case of a pair of earbuds to rapidly test Bluetooth connection/disconnection behavior.
- Fingerprint authentication: A robot arm tests the precision of under-display fingerprint scanners by repeatedly authenticating using fingerprint data from dozens of employees.
- GPS testing: A robot moves a phone slightly in different directions to test satellite accuracy.
- Neck stretch reminders: A pair of earbuds are inserted into a robot head in order to trigger neck stretch reminders.
- SmartThings integration: Samsung constructed a mini home in their lab complete with mini curtains and light bulbs next to a full-size Samsung refrigerator and washer in order to test various SmartThings integrations and routines.
- Temperature variation: A Fold and Flip are placed in a temperature-varying chamber and subjected to constant folds and unfolds as the temperature is adjusted.
- Walking: A robot holds a phone while slightly vibrating and moving back and forth in a line to simulate a phone being held in your pocket.
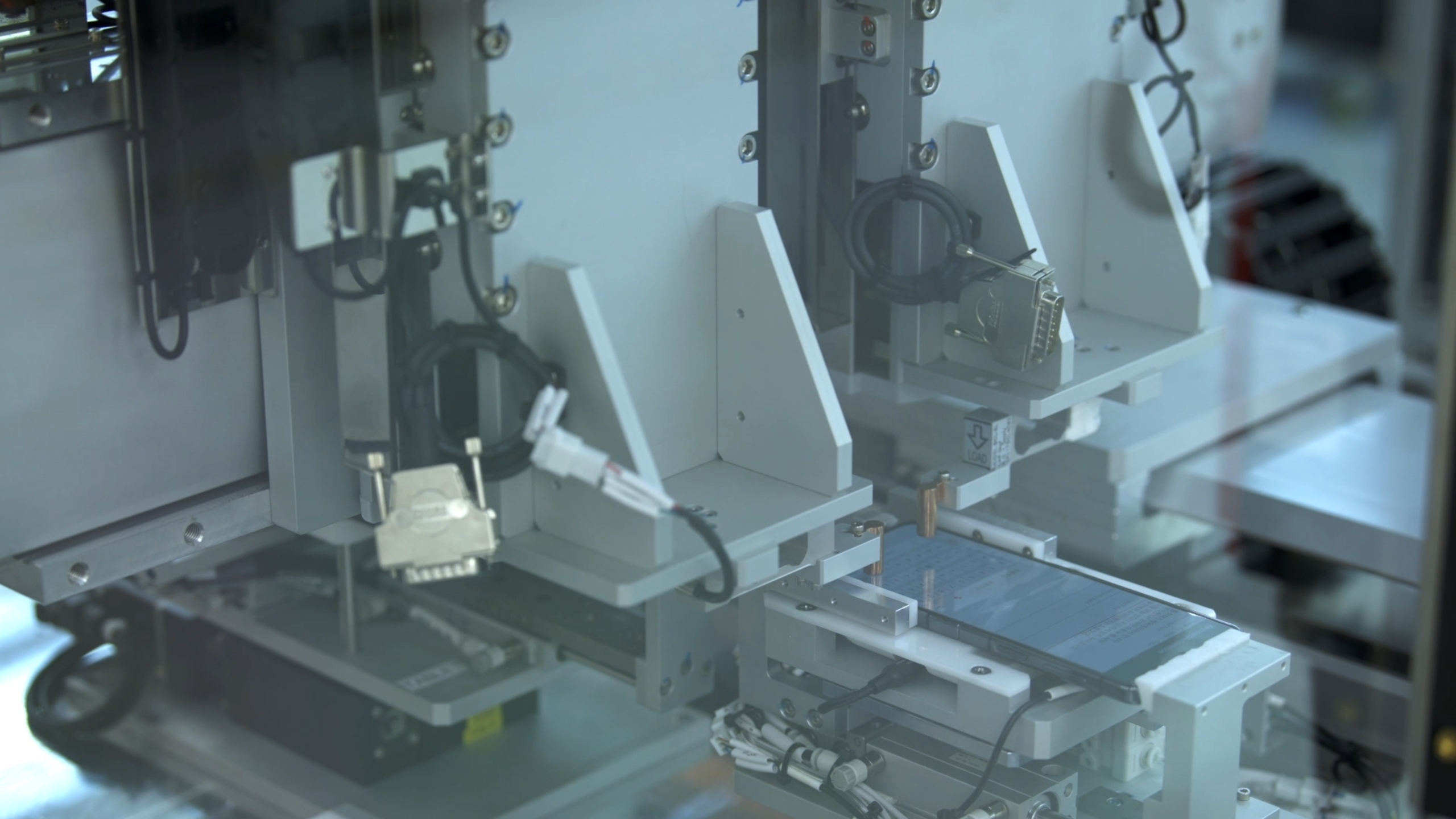
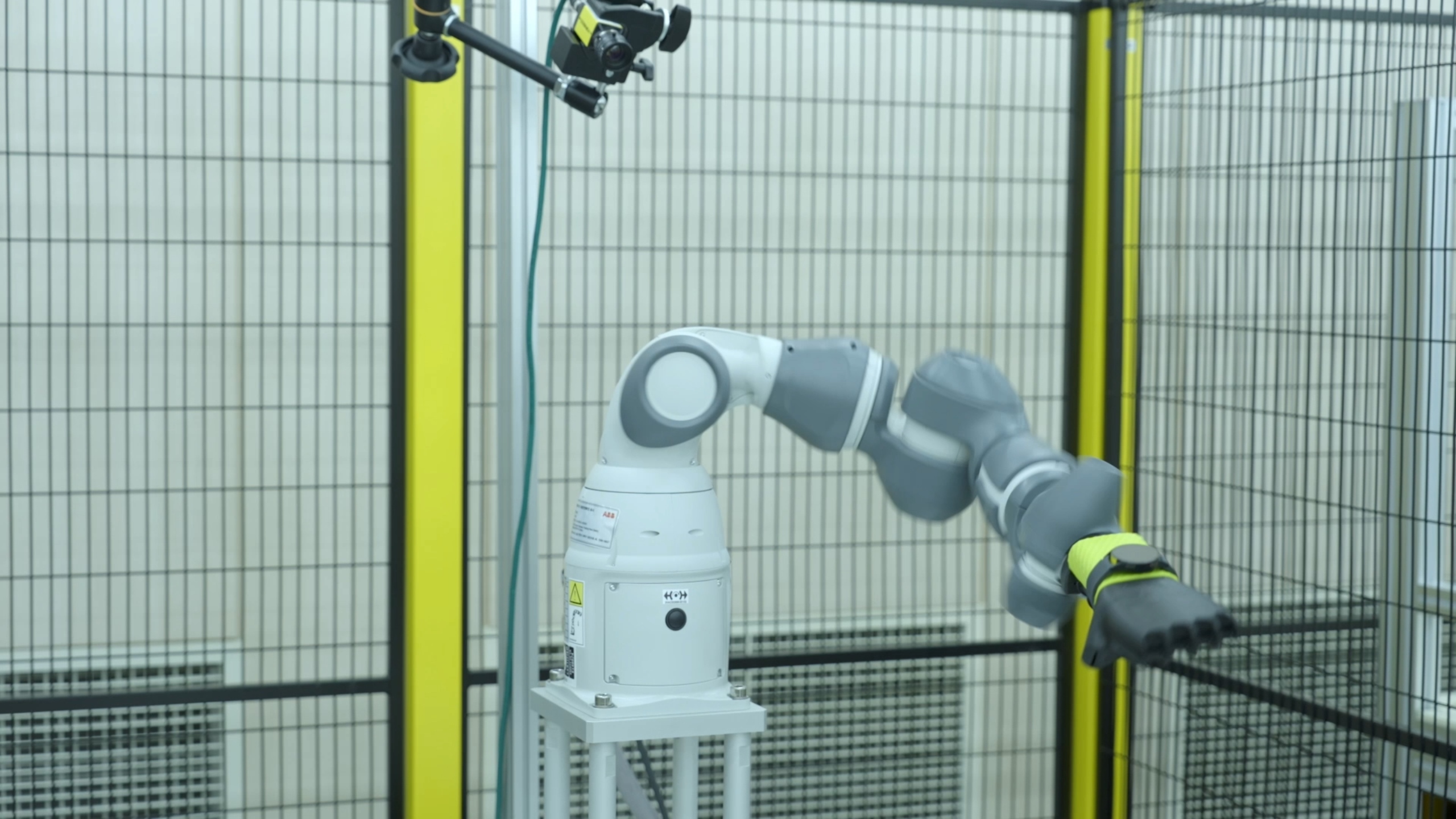
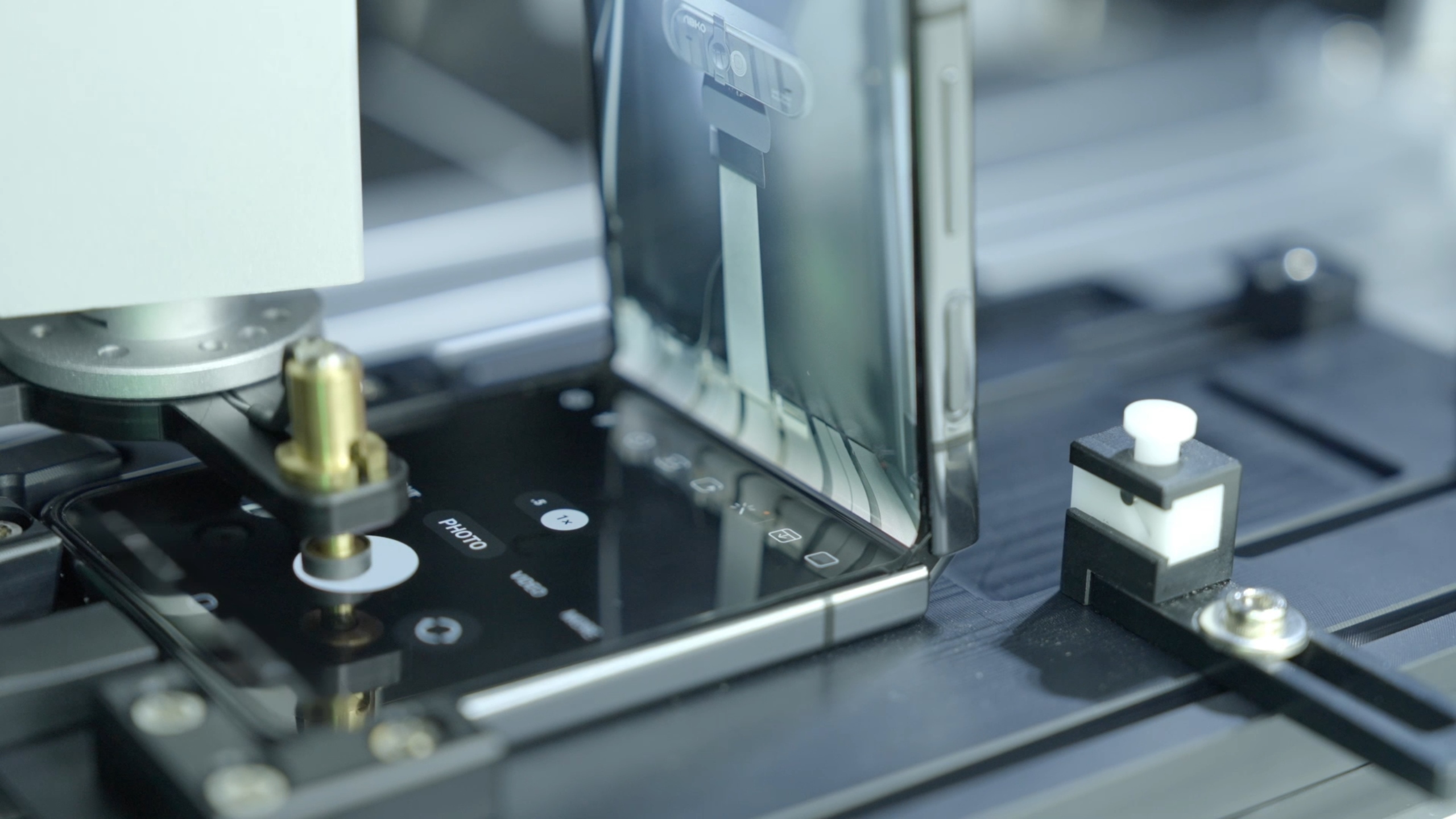
There were a variety of other automated tests being run in this lab that I can’t remember now, but I definitely remember walking by a bunch of different benches where PCs were running various ADB commands to automate button presses or app launches.
Personally, the software tie-in is what made the automation testing lab the highlight of the tour for me, and I was sad that we weren’t able to take any photos or videos of it. Fortunately, the video that Samsung shared with us actually shows off a lot of what I saw while touring the automation testing lab. Plus, this lab is actually where some of the devices that Samsung puts up on its Remote Test Lab actually come from, so keeping that tidbit in the back of my mind will definitely jog my memory about this visit.
I hope I get the chance to do another factory tour like this again because I definitely learned a lot during my visit to Samsung’s Smart City. My focus is more on the software side of things if you haven’t noticed, which is why a lot of what I saw in Gumi was new and exciting to me. There are still some details about the tour that I couldn’t find a way to slot into this article, like how Samsung tests its Ultra-Thin Glass for foldables and how Samsung implemented machine learning and remote work into their processes, but I have to end this article somewhere.
I’ll leave you with something amusing, though: Samsung’s Bixby-powered Galaxy Home smart speakers made an appearance during our tour. Samsung announced these speakers way back in 2018, but they never actually launched. These speakers were inconspicuously placed at the back of a table in one of the demo rooms, though I don’t remember if they were actually being used. So I really did get to see every Galaxy product Samsung ever made except for the Note 7.
If you want to check out the full video Samsung sent us of the assembly and testing of the Galaxy Z Fold 5 and Galaxy Z Flip 5, you can see it here.