Tejas Sidnal, an architect, used to think about building carbon-negative homes, structures that absorb more Carbon dioxide than they emit.
A concept which has started taking off in the West slowly, it is still far from reality in India.
Sidnal realised that it is impossible to build a carbon negative house if you don’t have carbon negative products and construction materials in the first place. This was the beginning of CarbonCraft, a start-up which aims to convert carbon emissions into building materials.
Since the beginning of the 21st century, global greenhouse gas (GHG) emissions and larger air pollution have been on an upward trend - with the exception of the COVID-19 period - heating up the globe more and more, accelerating climate change and contributing to global health burden.
While the world is yet to see major success in reducing emissions and keeping pollution under check, a bunch of initiatives like CarbonCraft are trying to make a difference by harnessing emissions of different forms to make commercial value products.
Harnessing methane
Methane constitutes about 16% percent of total GHG emissions today.
Bengaluru-based bio tech start-up String Bio’s gas fermentation technology converts methane into commercial products such as protein for feed, crop inputs for agriculture and protein for human-grade food.
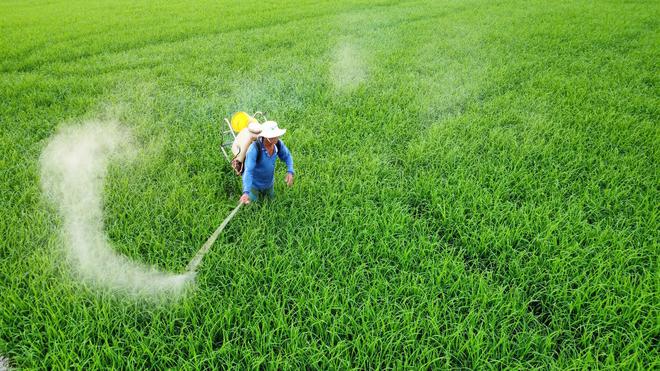
“All our products have a very differentiated USP for the customer in each market we are looking at. But the overall benefit of this is that there’s a certain carbon offset enabled both in the manufacturing process as well as from the point of use,” says Dr. Ezhil Subbian, CEO and co-founder at String Bio.
The company works with biogas plants as well as firms in the oil and gas sector to source methane. String Bio’s first plant was set up in Bengaluru about five years back.
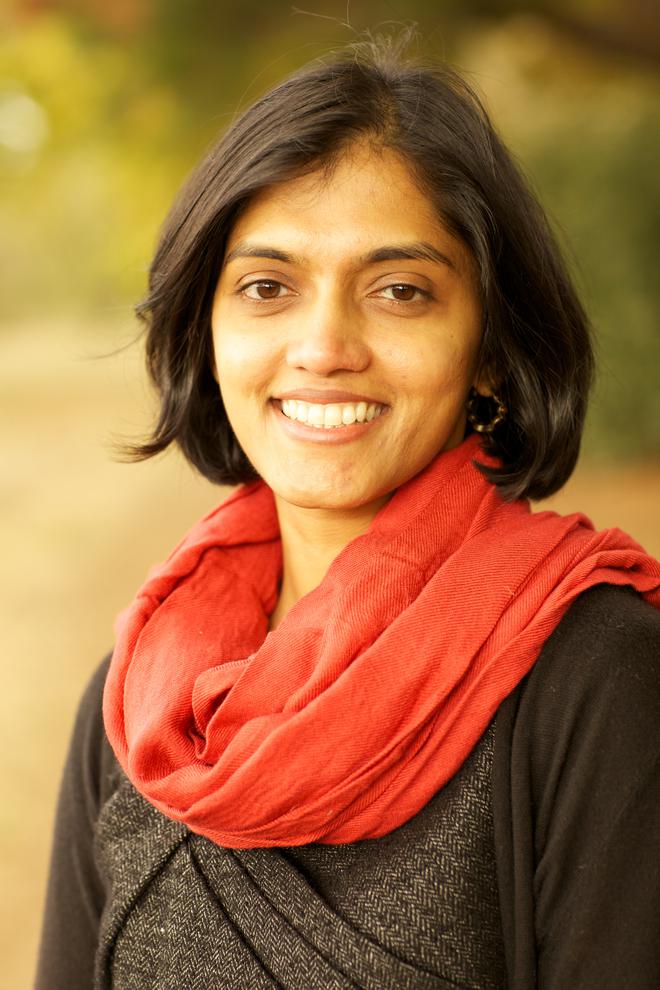
“At the plant, methane goes into our fermenters where it gets converted and processed into these products that we’re making,” Dr. Subbian explains.
The company, which has used the products from its first plant to seed the market, understand product market fit and optimise operations, is currently in the process of scaling up production capacity and driving market adoption for the products. It also has plans to set up a larger facility in the coming days.
“Products for animal feed and Agri are in the market right now, and we are looking at driving market adoption for them. For products in the food protein sector, we are going through our regulatory process,” Dr. Subbian notes.
According to her, the future areas of interest of String Bio includes cosmetics and sustainable material space.
Capturing carbon
Carbon dioxide constitutes more than 75% of global green house gas emissions.

When Sidnal of CarbonCraft started working on carbon negative building products, his first idea was to make carbon negative bricks. But realising it was difficult to build a value proposition out of a commodity that goes inside the structure and is not externally visible, he switched to tiles, which, in his own words, ‘have more value addition to aesthetics.’
“We convert carbon emissions into building materials in a four-stage process involving collect, process, build, and cure,” says Sidnal.
The start-up partners with tyre recycling factories to collect solid carbon and is looking to work with Direct Air Capture companies to collect gaseous carbon.
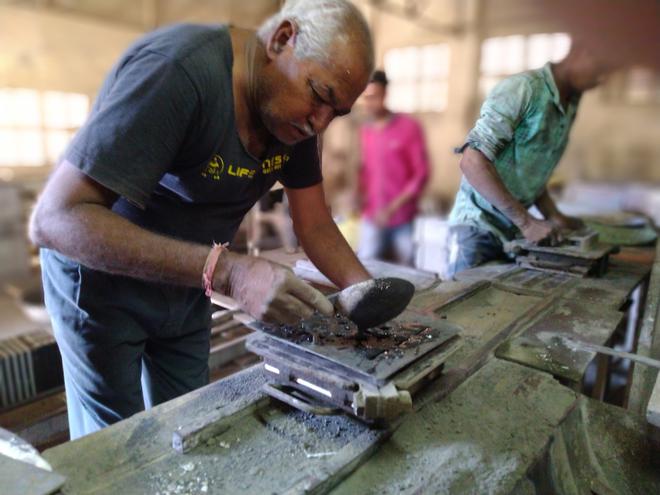
The collected carbon is processed at the start-up’s facility in Hubballi. It is fused with a mixture of binder and reinforcement materials to build the tiles. The manufacturing of tiles is outsourced to a unit in Morbi.
“The curing part is still under R&D. But we’re selling the tile produced after the first three stages. The challenge with the fourth stage is that it currently takes 30 days to cure the tile. We would like to reduce it to a day,” explains Sidnal.
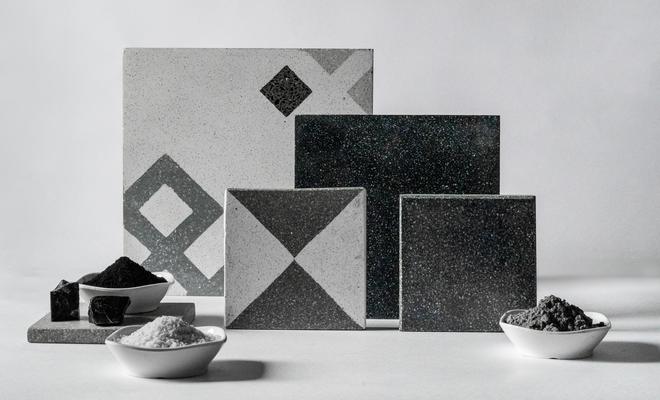
According to him while a conventional tile is 7 kgs CO2 equivalent per square feet, CarbonCraft’s carbon-negative tile has a CO2 equivalent of -1.1 kg per square feet. The startup is currently at a capacity of producing 10,000 square feet a month.
CO2 in construction materials
Researchers at the Centre for Sustainable Technologies (CST), Indian Institute of Science (IISc), have also been exploring ways to harness carbon dioxide emissions produced from industrial flue gas and store them in excavated soil and C&D waste, which could then be used to partially replace natural sand.
Flue gas is a mixture of gases produced as a result of combustion in factories, industrial units and power stations and pushed out through tall chimneys.
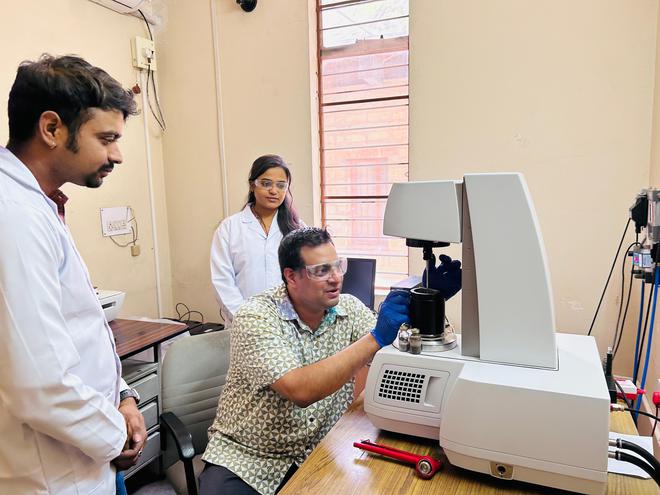
Souradeep Gupta, Assistant Professor at CST, and team has been working on the technology.
According to the institute, the team has shown that replacing natural sand with carbon dioxide-treated C&D waste in mortar and then curing it in a controlled, CO2-rich environment can speed up the development of the material’s engineering properties, and enhance its compressive strength by 20-22%.
Clean air and coasters
Aayush Jha started thinking about air purification solutions when his father, who moved to Delhi a few years back, was admitted in hospital with difficulties after inhaling PM2.5.
PM2.5 are fine particulate matter that is produced mostly as a result of emissions resulting from combustion of gas, oil, wood and so on, and a major reason for the severe air pollution in Delhi during winters.
Jha cofounded Bengaluru-based Clairco which has developed a filter that would help to clean the air once retrofitted in the AC systems, and offers ‘clean air as a service’ to large commercial establishments. With Orion Mall in Bengaluru as their first client the startup today manages around 100 buildings that add up to about 15 million square feet and.
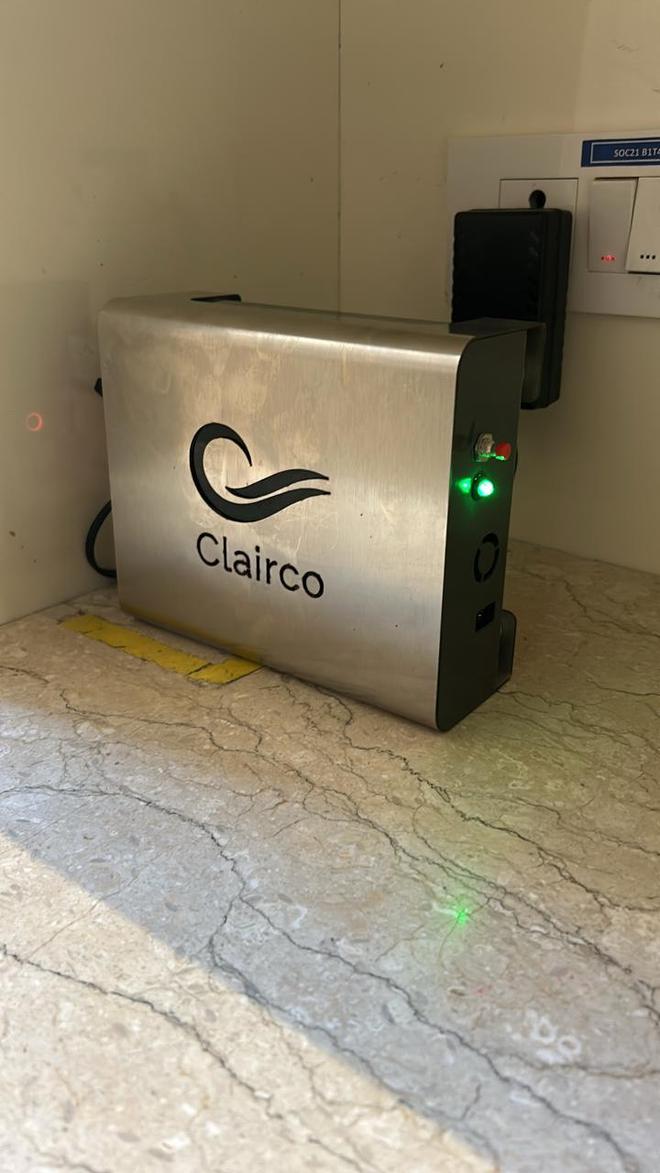
The second business model of the company is ‘energy efficiency as a service’ where Clairco retrofits its IoT sensors to the air conditioning systems of its clients. These sensors that can measure about 11 parametres in real time optimise the functioning of the AC. According to Jha this helps to save around 30% energy.
While the primary business model of Clairco has been around clean air and energy efficiency, the company partners with a Gujarat-based upcycler to make coasters and tiles using PM 2.5 emissions. The coasters are made out of PM 2.5 and filters, while the tiles have the extra ingredient of ferrous oxide to make them stronger.
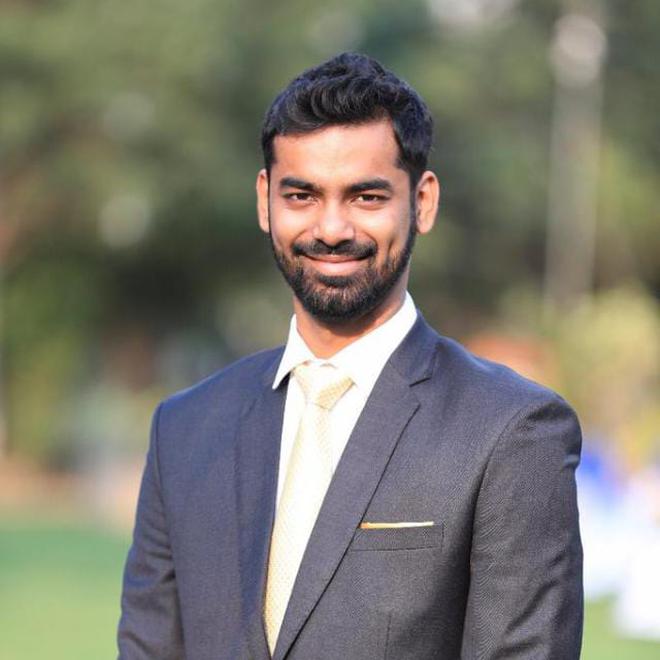
With Air Conditioners being responsible for around 4% of global GHG emissions, Clairco also attempted capturing the CO2 emissions from the AC systems, without much success, nevertheless.
“We will try again once we have some funding for it,” says Jha.