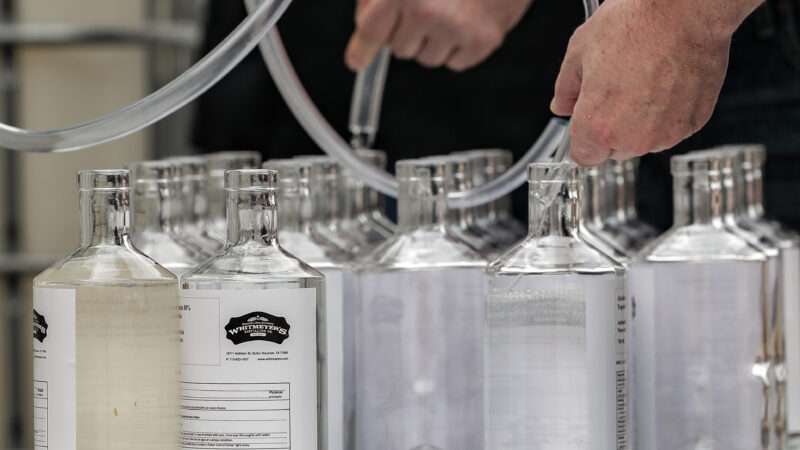
One year ago, when distiller Aaron Bergh of Calwise Spirits in Paso Robles, California, donated the last of the hand sanitizer he had produced to address shortages during the early days of the COVID pandemic, he assumed that this unexpected detour in the life of his small business was behind him. Then, in June, he received an unexpected letter from the Food and Drug Administration (FDA) informing him that a sample of his sanitizer taken in December 2020 exceeded temporary limits of two impurities and demanding extensive records of his production and distribution.
Bergh isn't the only one. Rebecca Harris, president of the American Craft Spirits Association, says that at least 11 distillers in nine states have received similar letters from the FDA. At primary issue is acetaldehyde, a chemical that occurs naturally in fruits and dairy products, as well as in beer, wine, and spirits. The FDA sets limits on its presence in hand sanitizer at 50 parts per million (ppm). The sample from Bergh's distillery tested at 160 ppm and 167 ppm of acetaldehyde and acetal, respectively.
There are valid reasons to limit levels of acetaldehyde in hand sanitizer. The chemical is a potential irritant and is considered a known carcinogen. Yet, it's also one that most of us consume on a regular basis due to its natural occurrence in many foods and drinks; it's also produced in our bodies whenever we have an alcoholic beverage as part of the process of breaking down ethanol. If you've enjoyed a banana or a beer recently, you've consumed acetaldehyde. As with any potentially toxic substance, the risks vary with the level and route of exposure.
The new round of letters from the FDA raises two questions. The first is whether the levels of acetaldehyde in sanitizer produced by distillers rises to levels where they pose a real risk to users. The second is, if there is a genuine risk, why has the agency waited more than 18 months after taking samples to begin acting on the test results, long after the sanitizer was distributed to health care workers and consumers?
There is surprisingly scant research on the first question. In May 2020, noting the demand for emergency ethanol-based sanitizer, Todd Pencarinha and Mark Myers of Altiras Chemicals compiled a report synthesizing existing research on the presence of acetaldehyde in foods and drinks, workplace exposure in the air, and absorption via the skin. They concluded that "hand sanitizer manufactured with ethanol containing 1000 ppm acetaldehyde exposes consumers to a far lower acetaldehyde dose than many common acceptable foods, beverages, and occupational activities, and therefore 1000 ppm is a reasonable limit."
The FDA ultimately settled on a far stricter standard of 50 ppm. This likely reflects the agency's very cautious approach to regulation. The FDA acknowledged in a recall notice from October 2021 that "the exact risk from using hand sanitizer containing benzene, acetaldehyde, or acetal is unknown."
Whatever the reasoning, 50 ppm became the standard for distillers contributing to emergency sanitizer production. Distillers I spoke to have no objection to complying with the FDA's standards, but they are frustrated that the agency is raising the issue long after they stopped producing or distributing sanitizer. "They took our samples, we didn't hear from them for a year and a half, we assumed there was no issue," says Jesse Lupo, owner and distiller at Mossy Ledge Spirits in Etna, Maine.
Acetaldehyde and acetal are commonly found in distilled ethanol, although distillers also question whether the long delay between when samples were taken and tested has contributed to the detection of impurities. They raise the possibility that, depending on how the samples were stored, hydrogen peroxide in the sanitizer may have reacted with ethanol to produce higher levels of acetaldehyde than were present at production. Bergh has requested chain of custody information from the FDA, which it has yet to provide.
Distillers do not know whether they will face recalls that might damage their reputations or be required to pay fines. Some distillers have hired legal counsel to advise them on working with the FDA, according to Rebecca Harris, which can become costly in itself. At a minimum, the letters from the FDA require the distillers to comply with complex and time-consuming records requests and to provide an "action plan and timelines for conducting full chemical and microbiological testing of retain samples within six weeks of the date of this letter to determine the quality of all batches of hand sanitizer drug product distributed in the U.S. within expiry."
Reason reached out to the FDA's press office on August 2 to ask what potential risks concern the agency with regard to distillery-produced sanitizer, why it has taken so long to address the results from testing, and what potential penalties distillers may face. At the time of publishing, the agency has not responded to these questions.
Whatever the propriety of the FDA's 50 ppm standard, the year-and-a-half gap between taking samples and notifying distillers of noncompliance raises questions about the agency's enforcement priorities. If the standard is unreasonably low, then it is imposing costs on distillers for no real benefit. If the standard protects against a real danger, then the action has come far too late to protect consumers.
Distillers "feel like it's been one thing after another," says Harris, referring to a surprise notice distilleries producing sanitizer received from the FDA in December 2020 informing them that they were obligated to pay a surprise $14,000 fee as registered drug production facilities. That fee was waived by the Department of Health and Human Services following reporting by Reason and other sources and vociferous public objections. The unexpected compliance costs some are facing now strike many as yet another undue burden. "No good deed goes unpunished" is a phrase that came up often in conversations with distillers.
The guidelines allowing beverage distillers to produce hand sanitizer when it was in short supply during the pandemic were intended to remove regulatory roadblocks, acknowledging that the emergency justified easing restrictions that make sense in normal times. Distillers saw making sanitizer as a way to stay afloat while helping their communities, but the lesson many are learning is that dealing with government regulation turns this into a mistake they would not repeat.
"At a point in time, I was so glad of sanitizer, and right now, I wish we'd never done it," says Lupo, who reports taking out a $45,000 loan to produce sanitizer at a very marginal profit. "I will not put myself on this same chopping block again."
The post FDA Can't Stop Harassing Distillers Who Made Hand Sanitizer During the Pandemic appeared first on Reason.com.