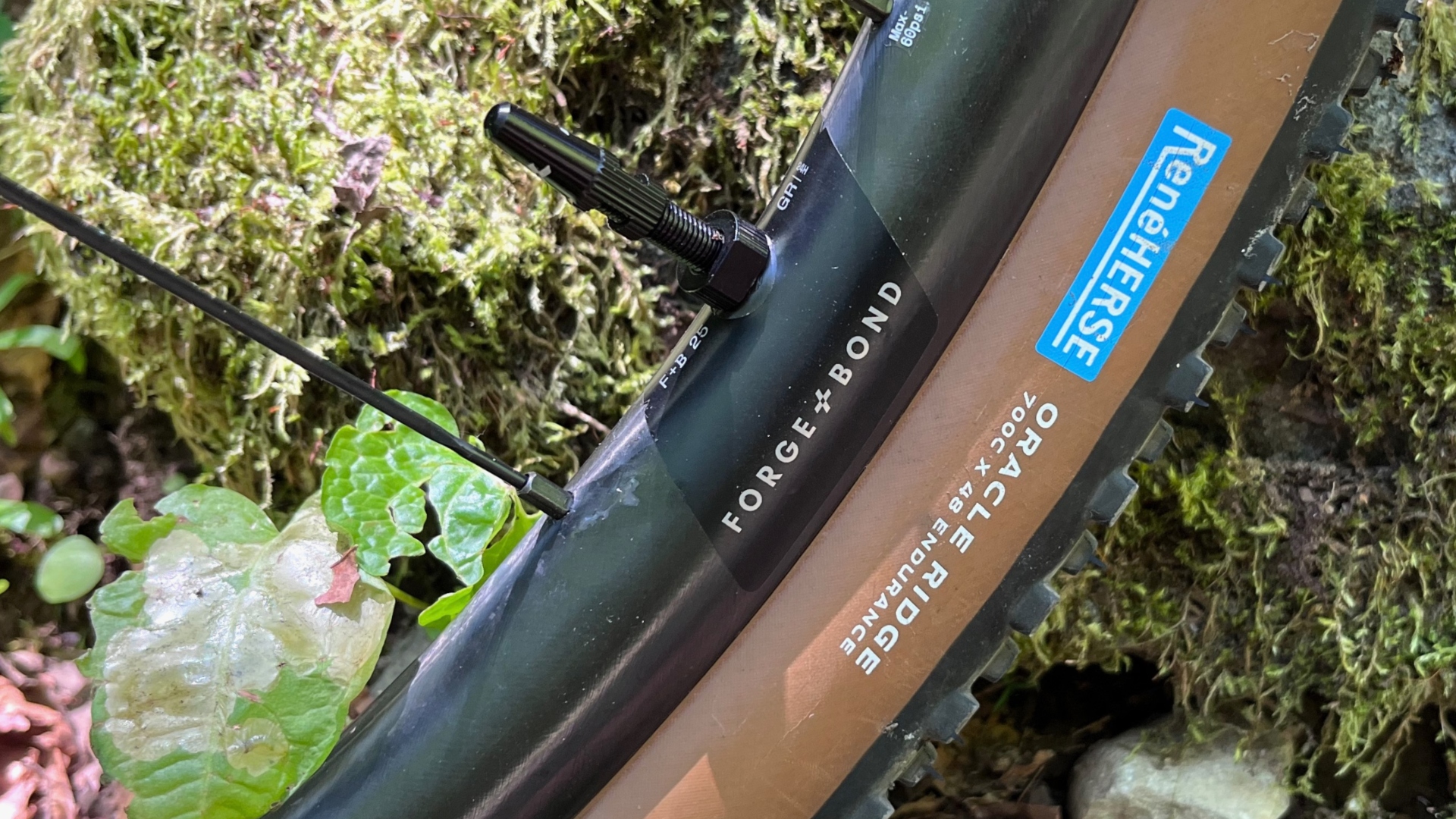
While the bike industry promotes healthy lifestyles and eco-friendly transportation, its environmental impacts are not insignificant. From the raw material extraction and the manufacturing processes to distribution and (lack of) end-of-life disposal –the bike industry at large is actively grappling with its carbon footprint.
Luckily, efforts are being made within the bike industry to reduce its environmental impact. Companies are increasingly using recycled materials, adopting more eco-friendly manufacturing processes, and using more sustainable packaging and distribution methods. In the past year, we’ve reported on Schwalbe’s inner tube recycling program, Ergon’s first completely recyclable saddle, Rapha’s new kits made of repurposed fabric scraps and Trek Bicycle Corporation’s nine-year plan to reduce its carbon emissions by 68% – just to name a few initiatives.
At the Sea Otter Classic, too, sustainability is a burgeoning trend with an increasing amount of ‘greener’ products on display. At this year’s expo, there were at least three brands promoting their CSS Composites-made FusionFiber wheels, which many are calling the future of carbon composites. Brands like Chris King, Revel and Evil are all in on CSS' mission of "creating products that stay out of landfills."
FusionFiber technology is said to make carbon rims that are not only more durable than traditional carbon fiber products; they're also highly impact-resistant, damping and recyclable. This means that once the wheels have reached the end of their lifespan or are simply no longer being used, they can be recycled into a new product.
FusionFiber Technology - What Is It?
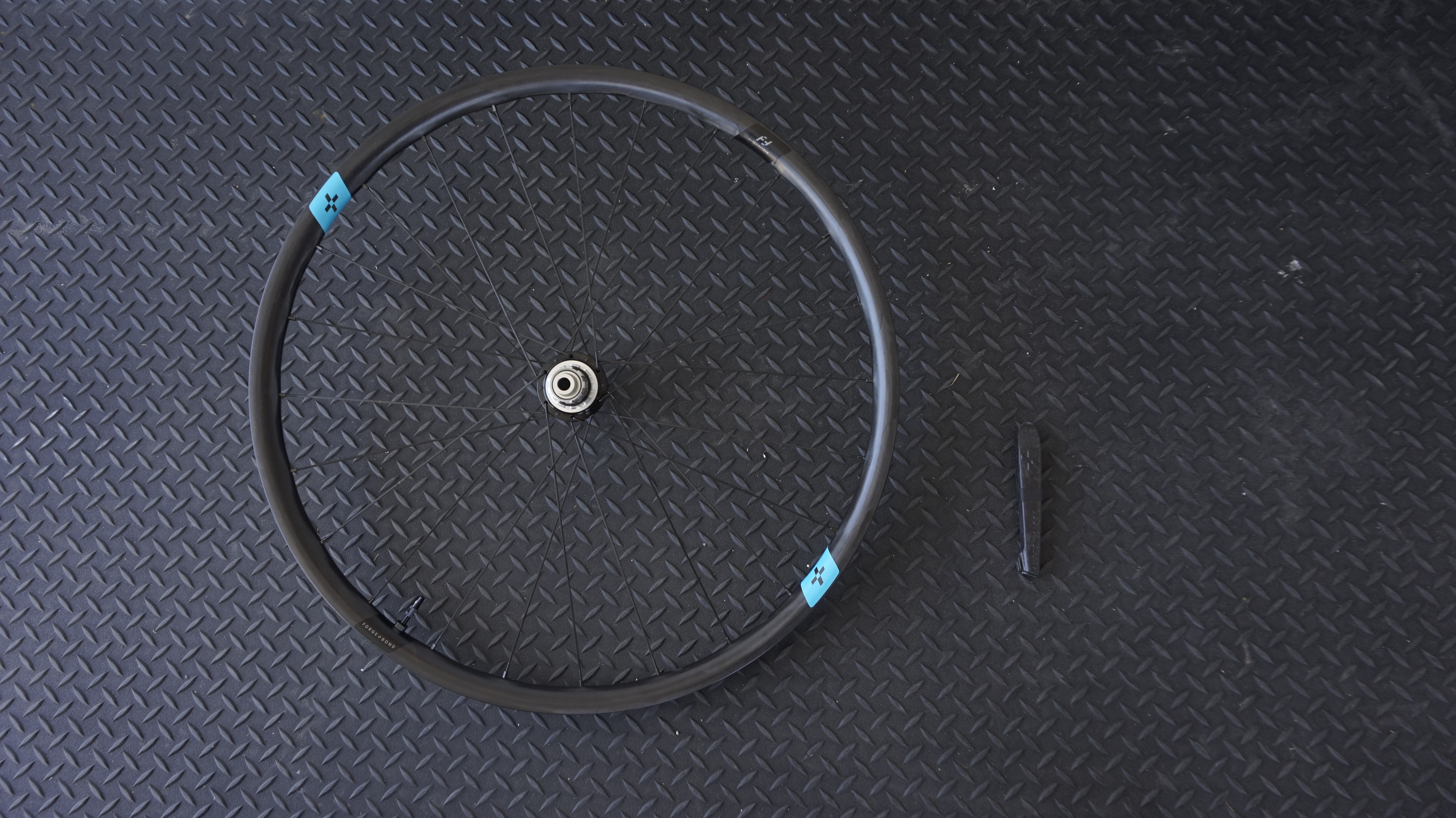
Traditional carbon products are extremely difficult, or simply too costly, to recycle, downcycle or reuse. And so, when the carbon product —be it a bike component, a boat or a spaceship— fails or reaches the end of its lifecycle, it usually ends up being discarded in landfill.
Most carbon components are made of sheets of epoxy-impregnated carbon fibers. Basically, the carbon fibers are 'glued' together with a resin that is cured in a chemical process called thermoset. Once cured, the resin cannot be returned to its previous form, meaning it cannot be broken down and remolded.
CSS Composites is a Utah-based engineering, design and OEM company aiming to change the way carbon bike products are made through its thermoplastic FusionFiber technology.
A wide variety of thermoplastics has been used in the aviation, aerospace, automotive and medical industries for some time but it’s only just emerging in the bike industry.
Unlike traditional thermoset epoxy-impregnated carbon fiber products, FusionFiber products utilize a long-chain nylon polymer as the matrix that is impregnated into the base carbon fiber material.
In this process, the "glue" — in this case the nylon polymer— can be melted and reused for a new or different product. Both the scraps from the manufacturing process as well as a broken rim can be melted down and shaped into a new short-fiber product.
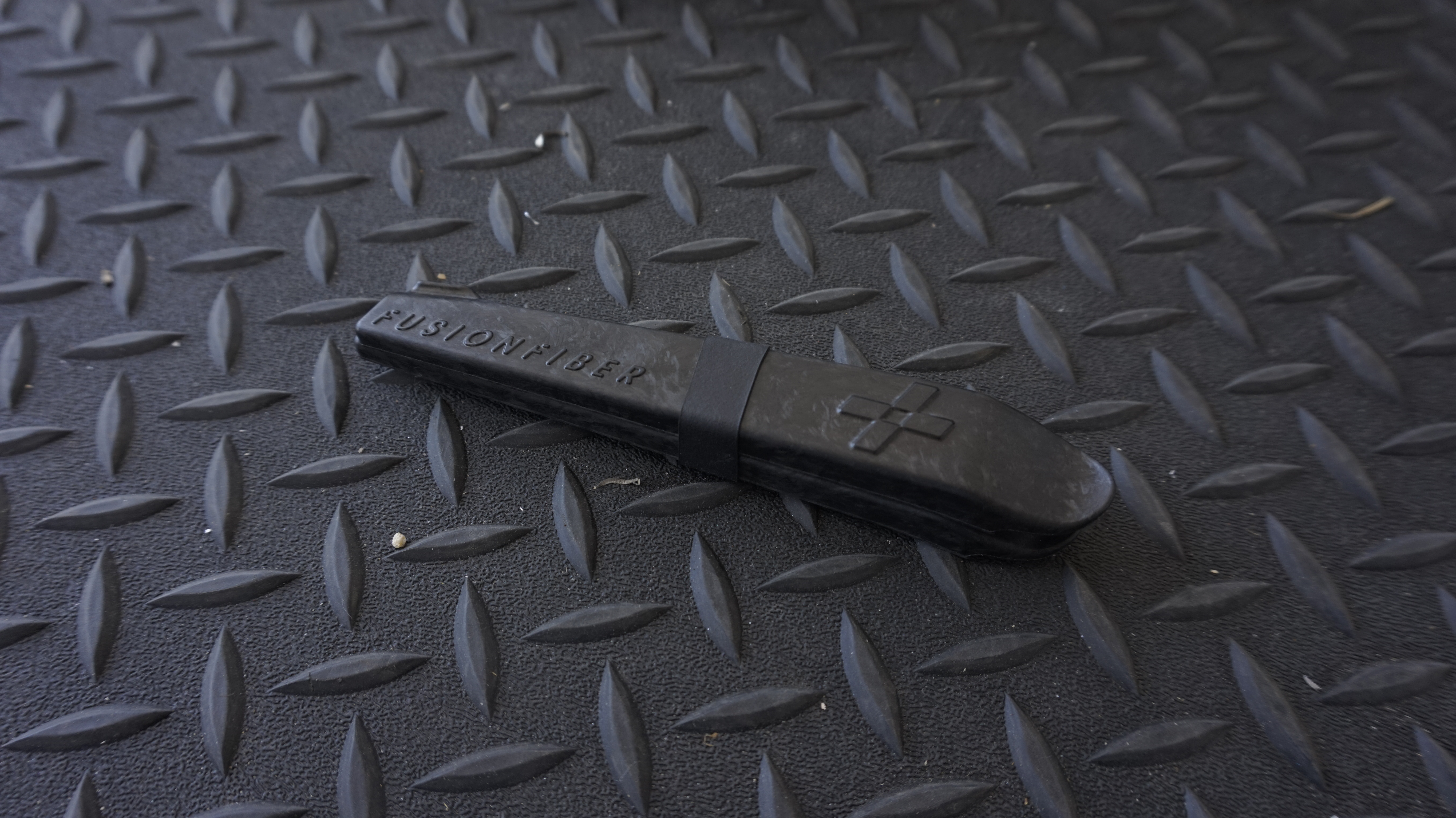
For Forge+Bond, CSS Composites' in-house brand, scraps and broken parts are currently only molded into tire levers, but we're told bike parts like stems and bars are in the near future.
Another benefit of FusionFiber is a simplified production process. FusionFiber doesn’t need to be refrigerated; the whole cutting-and-layup process can be automated and there's no sanding required. All of this not only reduces production time, it also significantly cuts down on energy usage, making FusionFiber an all-around greener option. All products are also made right here in the USA.
FusionFiber Ride Benefits
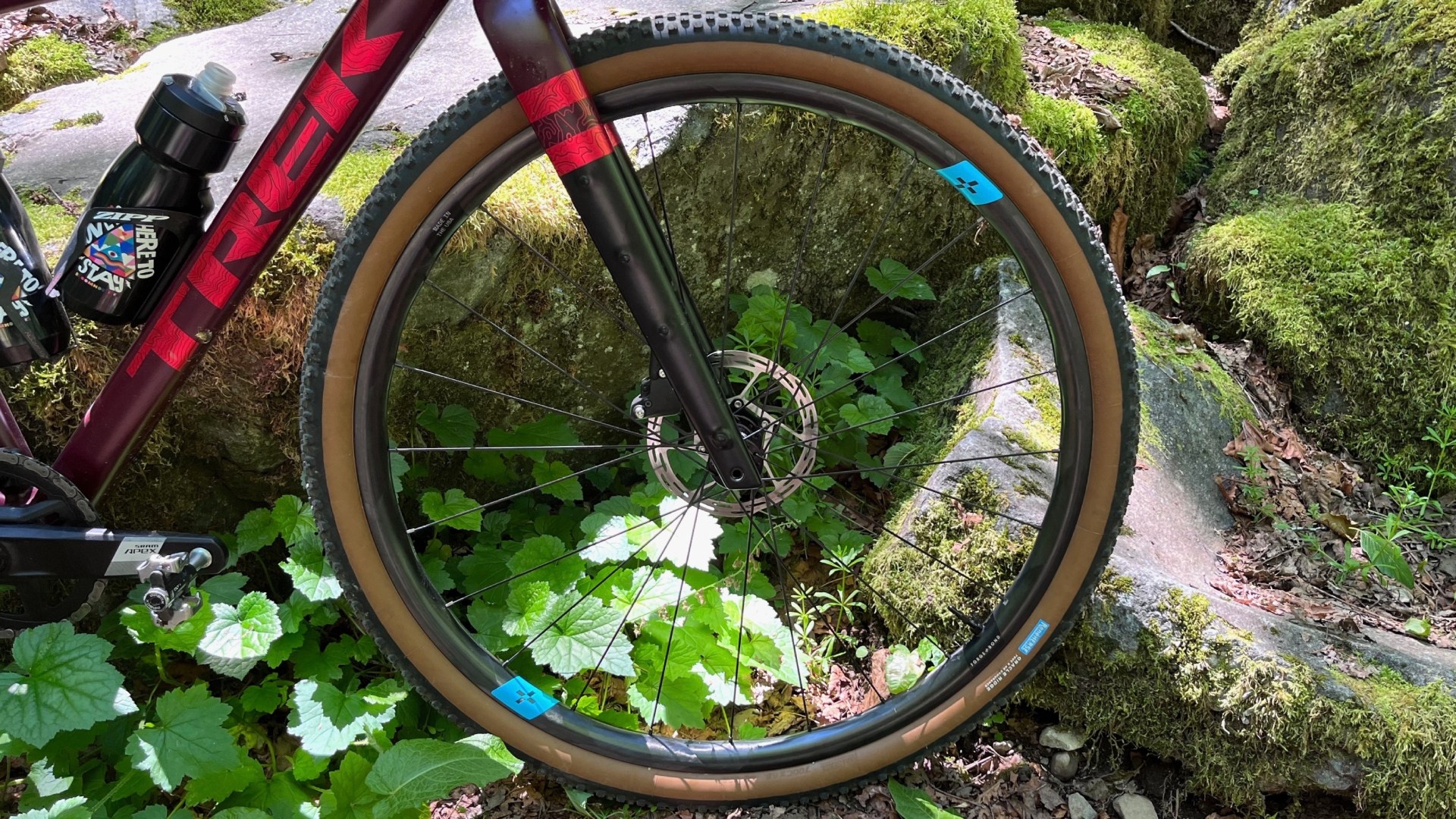
When it comes to ride performance, FusionFiber wheels are said to be light, damping and highly impact-resistant.
In testing its FusionFiber wheels against the leading epoxy-based carbon wheels, CSS claims that epoxy-based carbon wheels reached their initial failure point with substantially lower impacts and failed to the point where the wheel isn't rideable in only 2 or 3 subsequent drops in a basic drop test.
“Basically, the underlying characteristic of epoxy is that it is brittle and when it is exposed to enough force, it simply cracks/breaks when the impact is significant enough. With Forge+Bond wheels, the testing shows the failure point 1) requires substantially higher impacts to reach an initial failure and 2) substantially more impacts to reach a complete failure point (8 - 12 subsequent drops),” Garin Fons, the brand’s public relations representative, told Cycling Weekly.
Fons explained that this is due to the microflexing ability of nylon and the wheel’s unique carbon layup.
Forge+Bond is so confident in the strength of its wheelsets that there is no rider weight limit and the products come with a lifetime warranty.
The Forge+Bond 25GR carbon gravel wheelset in action
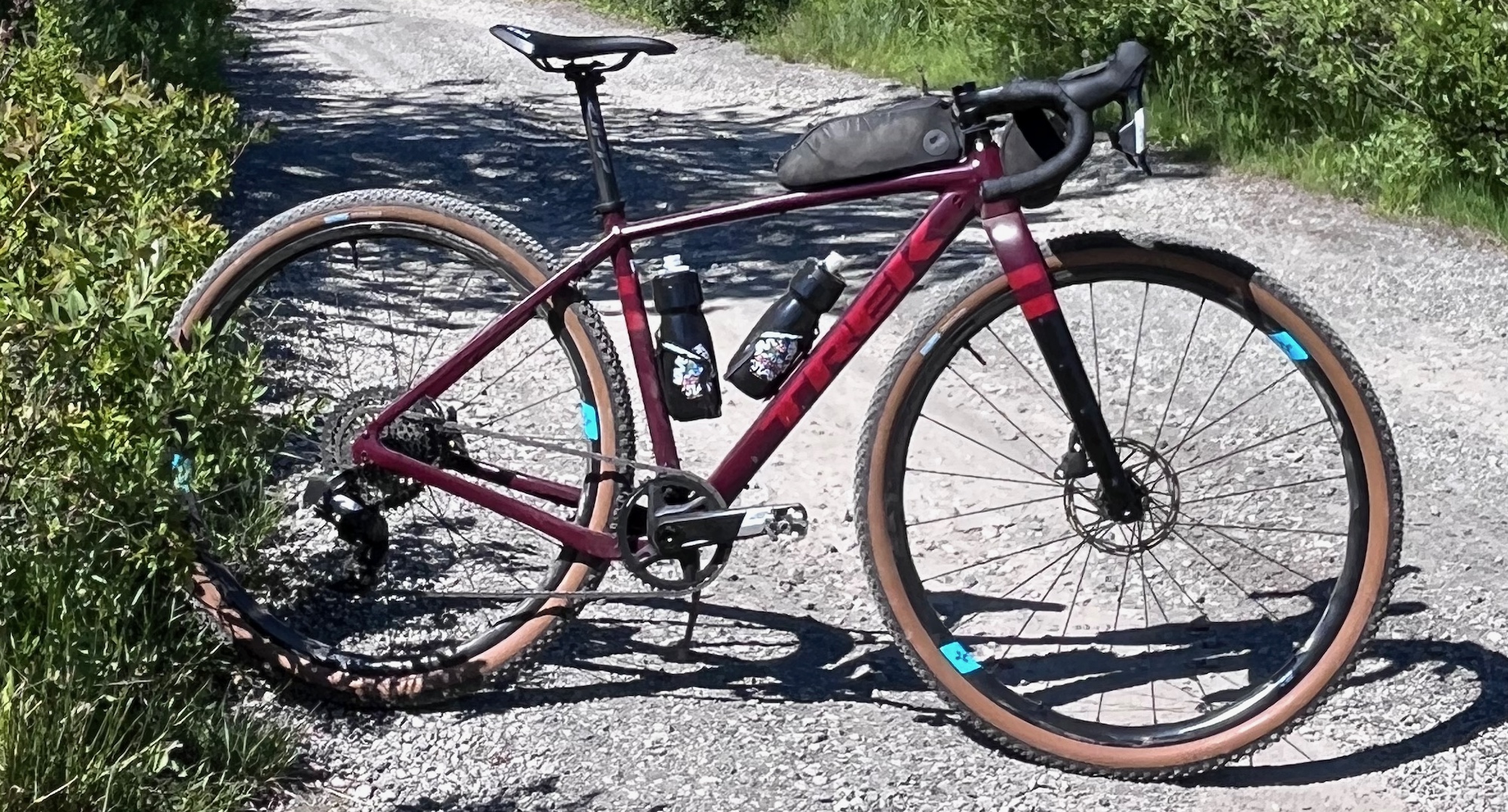
Forge + Bond’s 25GR carbon gravel wheelset
- FusionFiber rims (carbon and nylon)
- 25mm internal rim width / 31.4mm external
- Hookless rim bead
- Tire size compatibility: 32-47mm
- Max tire pressure: 60PSI
- No rider weight limit
- J-bend Sapim spokes
- External nipples
- Tubeless ready
- 100% recyclable
- Lifetime warranty and crash replacement
- Manufactured & hand built in Utah USA
- 1395 grams
- $2,199
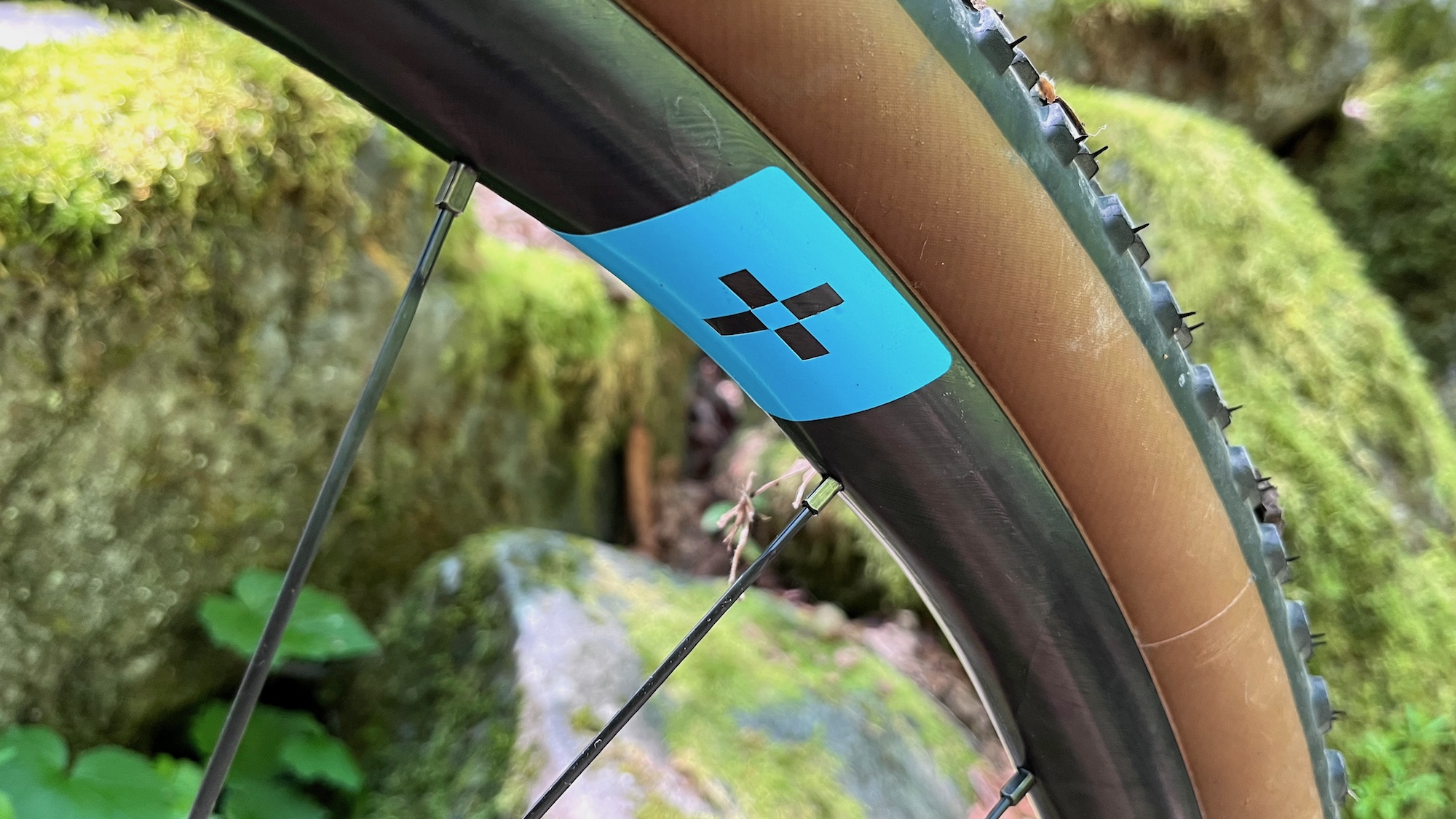
I received Forge+Bond’s 25GR carbon gravel wheelset in for review and promptly took it out for some seriously gnarly outings on gravel and a fair bit of singletrack around Oregon’s Mt. Hood.
For testing the wheelset, I alternated between Rene Herse’s beefy and knobbed Oracle Ridge tires and the supremely supple Barlow Pass slicks. I used the wheels on an aluminum Trek Checkpoint ALR5 as well as my Specialized S-Works Crux.
Swapping between tubeless tires can be a bit of a pain but thanks to the hookless and wide rim and decent rim tape, the setup was a breeze. At 1395 grams with Industry Nine’s Torch Road CL hubs, they’re decently light and I quite like the wheel’s raw finish and minimal branding as well. The brand’s bright blue logo is not an easy color to match with one’s bike, but when you’re a new brand –Forge+Bond only launched in April of this year– one wants to be seen.
To me, the use of J-bend spokes, external nipples, a serviceable I9 hub and a shallow rim indicate that this wheel is made to play and be ridden hard. This isn't an aero wheelset to help you save watts as you sail over smooth, champagne gravel. This is closer to a mountain bike wheel than a road wheel and, in fact, Forge+Bond doesn’t even make a road specific-wheel yet—mountain and gravel only.
The wheels came with the encouragement to “ride like there's no tomorrow” so I decided to put the wheels' claimed damping and strength characteristics thoroughly to the test by riding more trails than roads. Spoiler alert: I’m kind of surprised, though pleasantly so, that the wheels remain true and nick-free.
The wheels are playful and responsive. They spin up quickly, snap into action under power and handle tight, twisty switchbacks with precision. More than anything, they keep you planted and in control. Lively and planted may seem like a bit of an oxymoron but it’s important to note that the wheels are by no means dull. They do, however, feel connected to the ground. And perhaps this is where the damping characteristics come in.
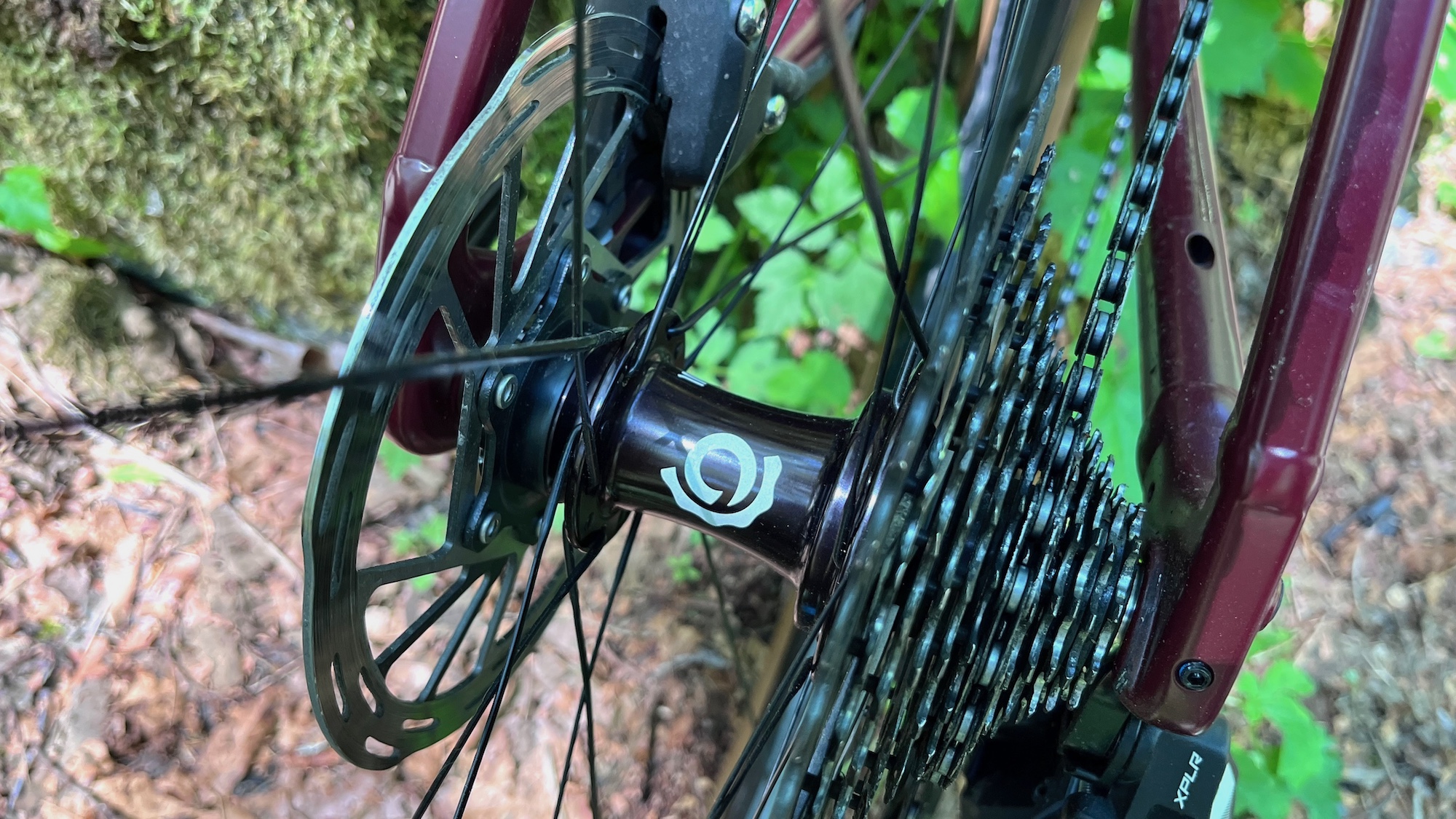
My first impressions were actually that the wheels were pleasantly reactive for a low-profile rim, more so than muted. On the road or smoother gravel, there are definitely wheels out there that initially feel more dampened – Enve’s SES wheels come to mind. It wasn’t until I was riding some rough terrain that I could appreciate the marketed damping. Wide, 45mm tires will add some plushness to any wheel but the difference here is that over rocks and chunky surfaces, the FusionFiber wheels appear to bounce less. You stay planted, which makes the ride feel less harsh and more stable. It also gives the rider more control and confidence on fast and loose descents.
Reminiscent of the equally shallow Reserve 25|GRs wheels I enjoyed so much last year, the FusionFiber wheels are highly capable, light yet robust. A wheel made for underbikers and those who prefer a Grinduro and Grodeo event over the long, smooth gravel of FNLD or SBT GRVL.
Or, in their own words, “Forge+Bond is built for those that live at the intersection of performance and creativity. Those courageous enough to demand change and crazy enough to make it happen."
Value and Verdict
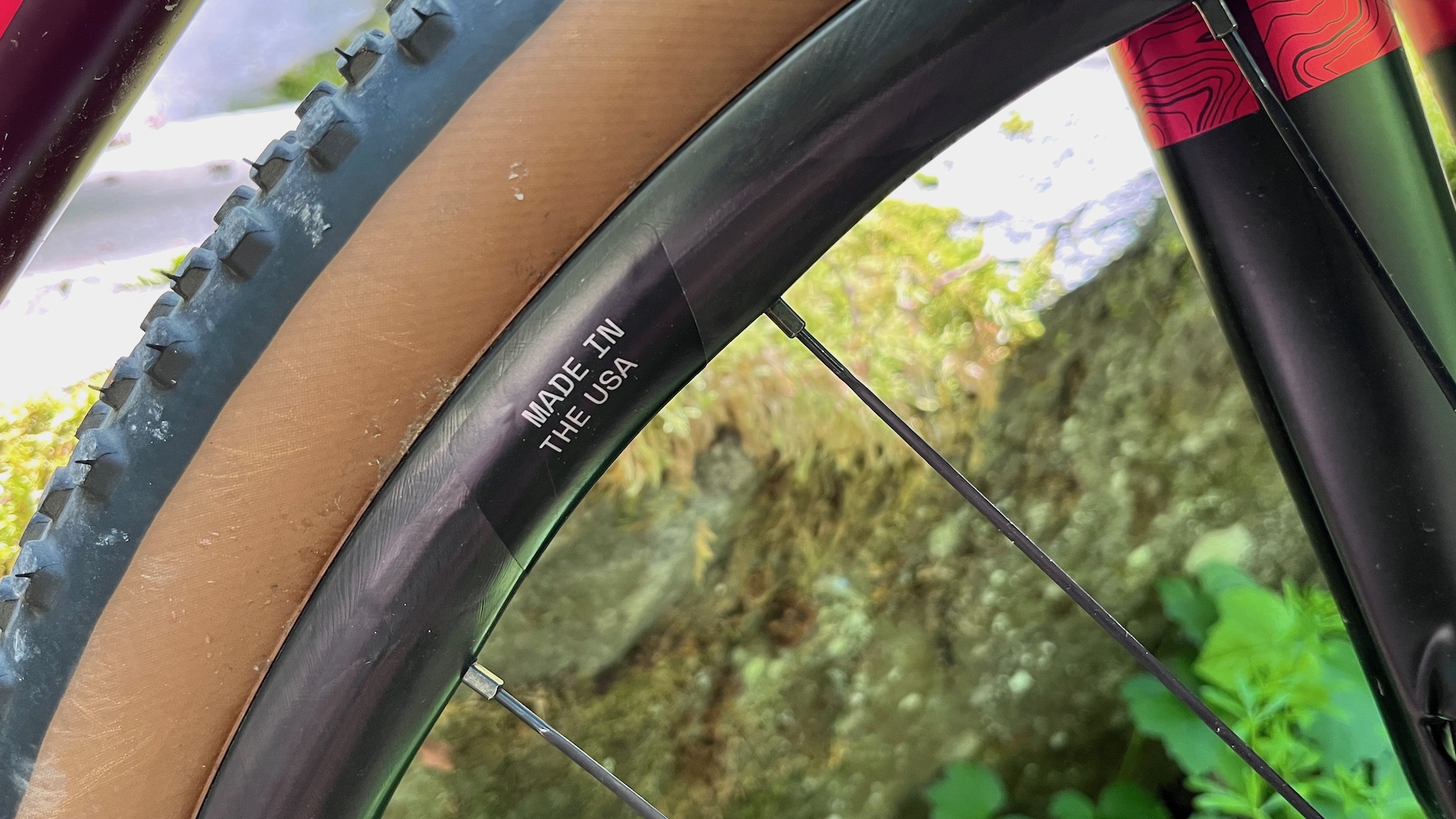
There’s a lot to like about Forge+Bond’s 25GR FusionFiber wheelset. It’s a playful, light yet robust and damping wheelset that’s also durable, serviceable and will serve you for years to come. It’s backed by a lifetime warranty and when the rim does reach the end of its lifetime, it can be recycled into a new product.
It does come with $2,199 price tag, however, and looking at performance alone, there are plenty of wheelsets at that price point or less that are lighter and faster with or without aerodynamic benefits. The comparable Reserve 25|GRs, for example, feature an equally shallow yet wide rim, are bombproof and weigh 50 grams less, and retail for 'just' $1599 with a DT Swiss hub or $1899 with the same I9 hub as used in the Forge+Bond wheels. On the other end of the price range, there's the Chris King GRD23 R45D wheelset, which also features a thermoplastic rim made by CSS Composites using its FusionFiber process. These wheels sport a Chris King hub but weigh 100 grams more than the Forge+Bond wheels and will set you back an extra $716 (MSRP being $2,915).
Ultimately, choosing these recyclable carbon wheels fromForge+Bond isn't just about the benefits of having a sturdy, high-performance product — it's also about contributing to a more sustainable future and minimizing the environmental impact of our industry and the products we use.
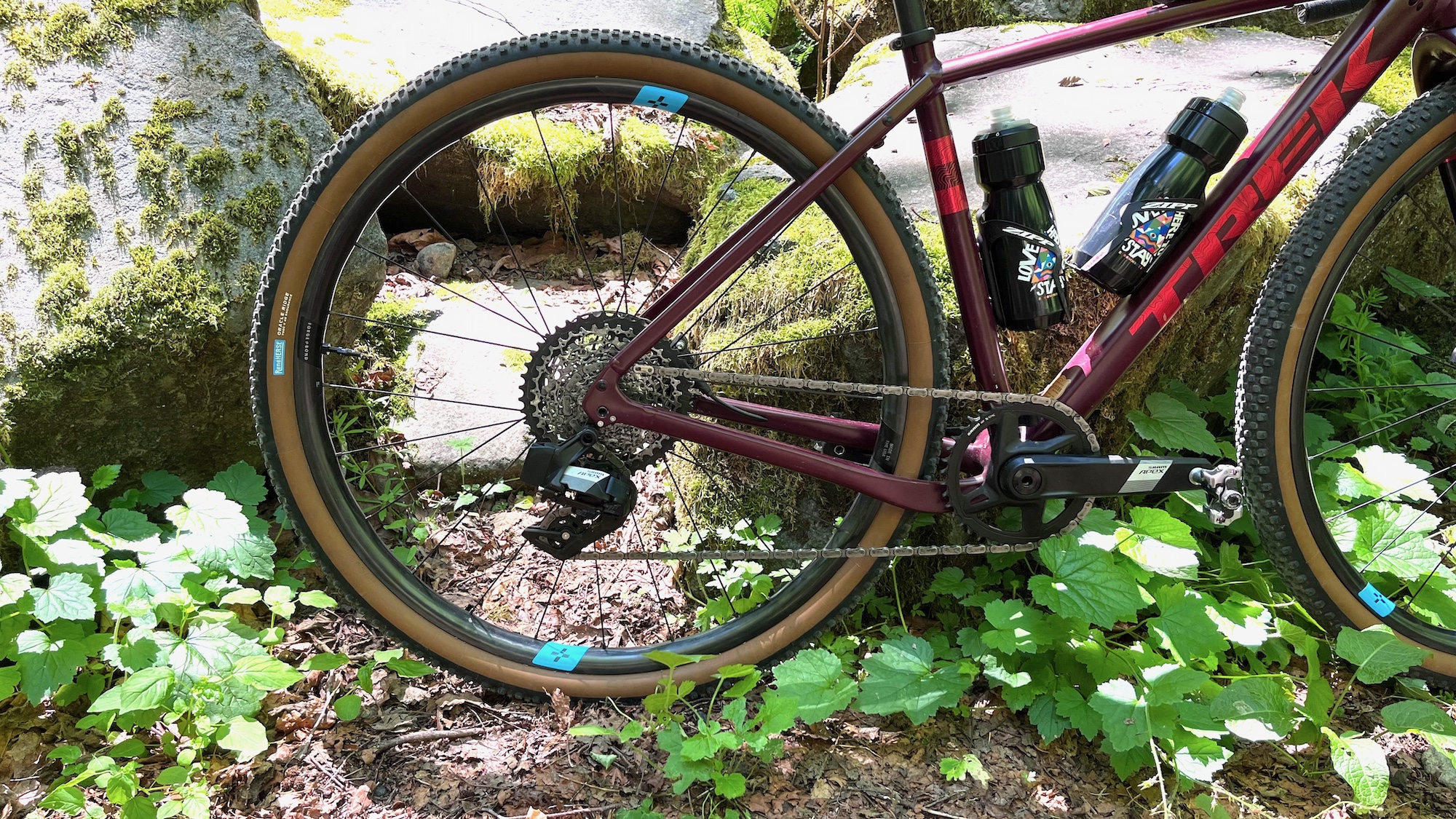