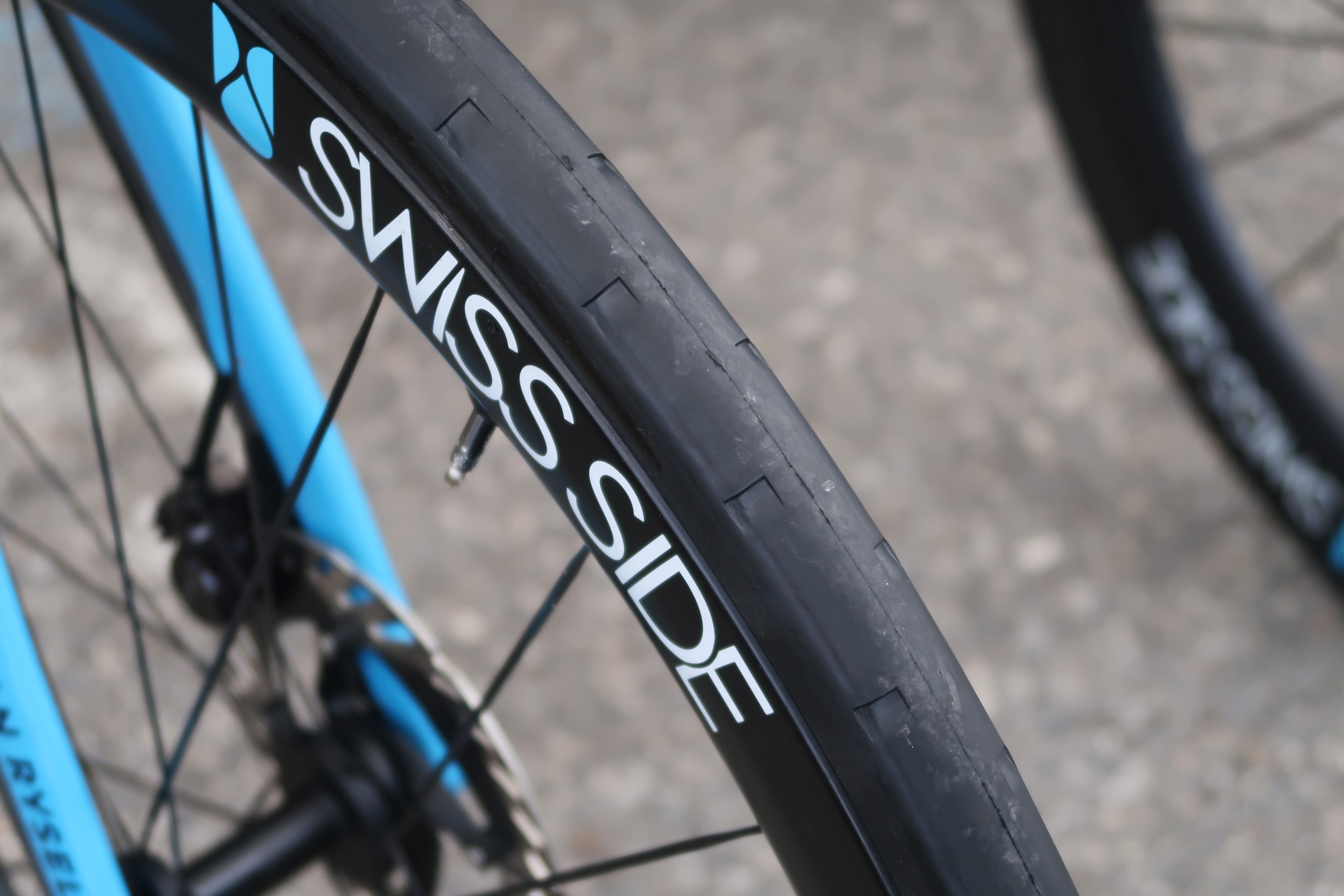
Increasingly, the cycling industry is realising the necessity of developing system-wide approaches to aerodynamics instead of looking at individual parts and cobbling them together without a thorough understanding of how they interact on the road. A good example of this in practice can be found in Formula One. Individual pieces of a car may appear less than optimally designed to move through the wind, but in concert, every bit works together to make the whole as quick as possible.
Of course, the engineering in motorsports must take very different speeds into account and also must factor in the downforce that keeps cars on track at these speeds, which are things not applicable to cycling. The fact remains, however, that the reason these cars have success in races is because the whole is engineered in concert. In many ways, cycling lags behind in this regard.
We are, however, beginning to see more collaborations between brands to look at the whole picture, with rider, wheels, and frame all optimised together. One of these is a collaboration between DT Swiss and Swiss Side with tyre manufacturer Continental, which officially launched today but was already spotted in action at the Tour de France.
The Aero 111 tyre is a front-wheel specific design offered in two widths, 26 and 29 mm.
The tyre has specially designed aero cavities that function as vortex generators to create turbulent airflow around the tyre and wheel to delay the separation of air from rim, maximising sail effect.
The Aero 111 is tubeless ready, uses Continental’s Black Chili compound and features a Vectran breaker for puncture protection. Stated weight is 250 grams for the 26 mm and 280 grams for the 29. MSRP is $120.95 USD / 119.95 EUR.
At the Tour, the Aero 111 was spotted being used by the Decathlon AG2R La Mondiale team. The team bikes had the Aero 111 fitted on the front wheel and a GP5000 tyre on the back.
Q & A
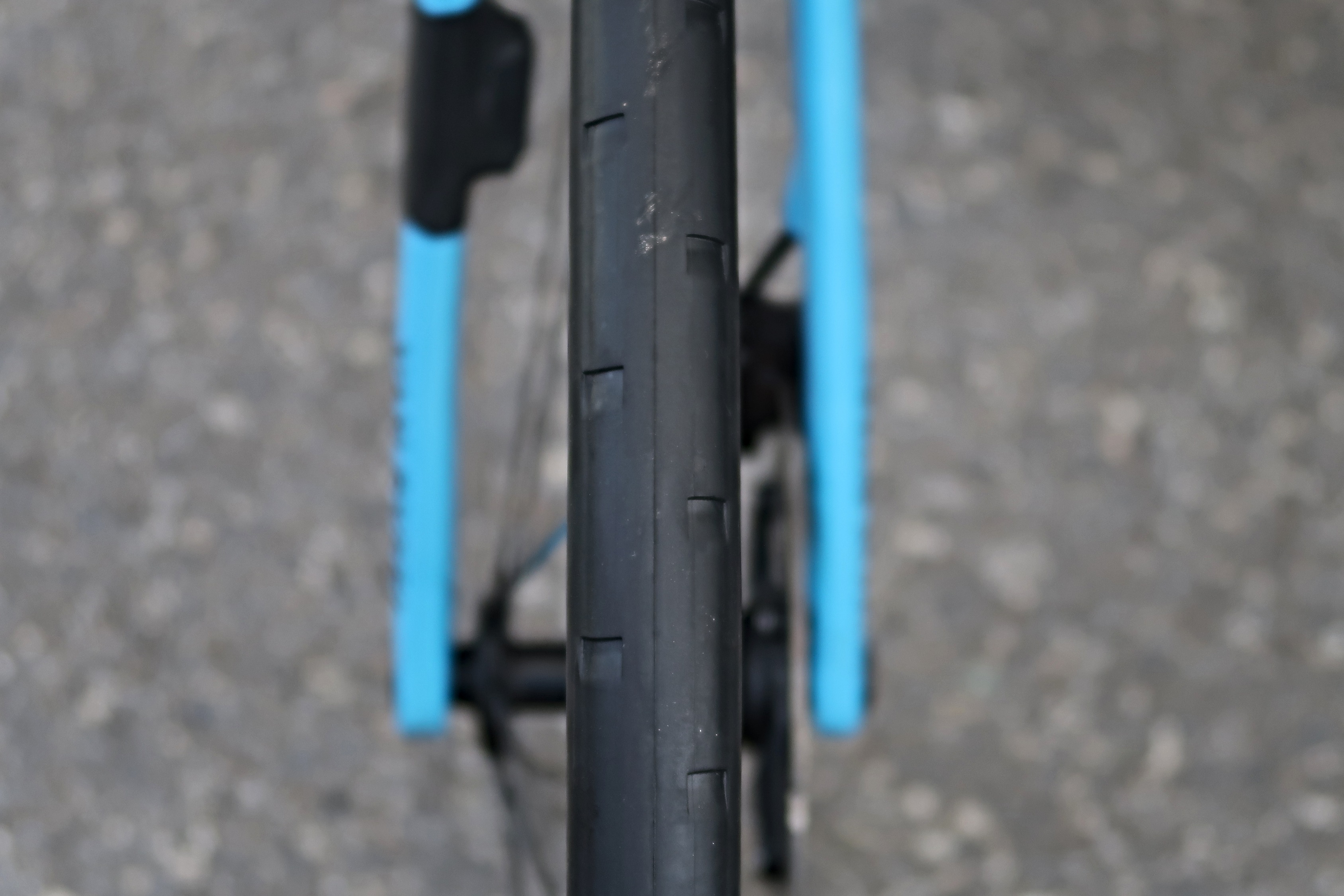
Cycling Weekly spoke with DT Swiss Marketing Manager Ralf Eggert to find out more about the process behind the development of this new tyre.
CW: What was the impetus for developing this tyre?
We wanted to bridge the gap of the tyre and rim interface and create a real aero tyre that works on all aero rims (heights) and at all speeds.
In order to take the optimization of the entire wheel tyre system to the next level, it was clear that an aerodynamic tyre would have to be included in the development. We found no tyre that met our expectations including aspects of low aero drag while maintaining manageable riding characteristics and thus, decided to start the development of our own tyre from scratch.
The long cooperation between Swiss Side and DT Swiss made the search for an aero expert in the cycling industry very easy. While form and function were determined at an early stage, the project needed more help from an expert in rubber. It became clear that Continental was the best partner who not only understood the concept but was also able to implement the most advanced features into this patented aero tyre concept.
CW: How did the partnership between DT Swiss, Swiss Side, and Continental happen? Did one company initiate?
DT Swiss is patent holder and initiator of the tyre concept and Swiss Side is our aero cooperation partner. Swiss Side knows how to use CFD simulations in aerodynamics and DT Swiss [provides expertise] in wheels and components. The only thing we weren’t able to do was to find the right partner in the tyre industry. Continental took the challenge of not just copying [something], but making a new tyre with performance like their best tyres, including grip, rolling resistance and puncture protection.
CW: What did the development process look like?
We work with a privately operated wind tunnel. This wind tunnel serves as a development centre for the bike industry and independent magazines. When a product has been calculated in a CFD simulation only very few 3D prints are used in the wind tunnel and mostly just verify what’s been calculated. Same with the tyre. We are always trying to be as objective as possible in these tests and thus we communicate results with competitors. However, the weighting distribution of yaw angles can be individualised. With Swiss Side’s expertise, real world data collected over more than a decade are reflected in the most accurate weighting distribution. Thus, this weighting distribution is subject to change depending on the development goal of the product.
CW: How much aerodynamic advantage can be gained with these methods?
Using the high speed assumptions of professional riders, very high or very low yaw-angles occur less often than the travelling speed assumptions of amateurs riding 30 km per hour. Here, higher yaw-angles occur more often leading to larger gains in drag reduction.
At 45 km/h we see an aero advantage of 2.1 watts measured on a 62 mm high rim (vs. GP 5000 STR, approx. 21% less drag); at 30 km/h the advantage is “only” 1.2 Watts, which is 33% less drag! In more extreme wind situations (cross winds), the aerodynamic gains can grow up to ~18 watts and the wheel itself is creating thrust due to negative drag. The front wheel is the only component on the bike/rider system that is able to create propulsion due to the drag reduction of the sailing effect.
CW: Do Continental and DT have any other projects in the works together?
I think this is a good start and the tyre concept with two widths currently might be extended in the future.
Conclusion
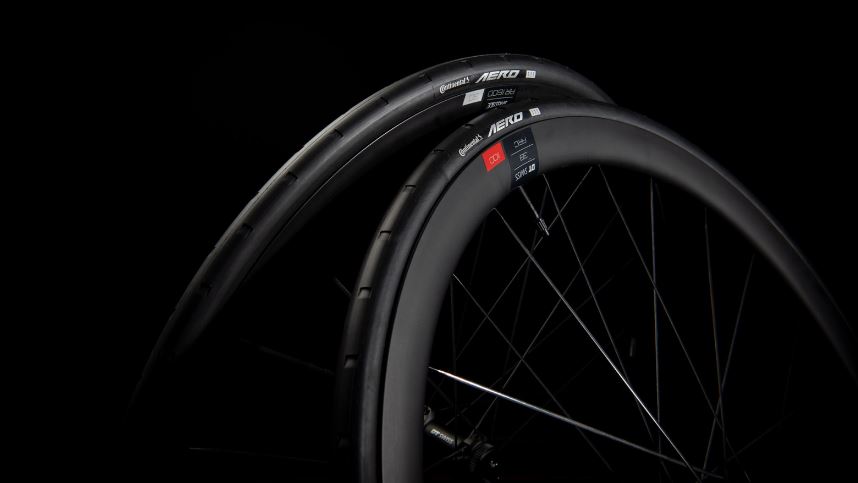
I expect to see this type of collaboration becoming increasingly common across the industry as different bases of knowledge are combined in the name of finding new and faster ways for bicycles to slip through the air. It remains to be seen just how much advantage can be eeked out at the margins, but it is a good sign for cycling that problems are being tackled collaboratively instead of exacerbated by manufacturers at loggerheads with one another. With that said, bigger companies, with more vertical integration of products, are perhaps the ones with the most to gain from this approach.