It is the season of all things slow. In the fashion world, slower production cycles, sustainable fabrics, and limited editions are now the norm among niche and luxury labels. This move includes the adoption of 3D technology which is not just resulting in cutting-edge designs, but also ranking high on the sustainability quotient. Perhaps why we are now seeing the likes of couture houses such as Dior, Burberry, and Louis Vuitton, among others, join the list of prominent sports brands who have been working with 3D tech for a while.
Recent fashion weeks are proof of this. At the Paris Fashion Week this January, five 3D printed shoes were launched, including Dior’s Carlo black lace-up Derbys with a lattice structure, a lightweight puffer boot by Danish brand Rains, and a sneaker by Reebok (in partnership with Dutch brand Botter), which was manufactured using advanced computational techniques and an HP Multi Jet Fusion 3D printer in 15 days.
The Indian take
While such experiments are now more common internationally, the Indian story is quite different.
Designer Vaishali S, who made her international debut with Milan Fashion Week (MFW) in 2021, followed by the Paris Couture Week, is known for her love for Nature, and a signature cording technique that she uses on a range of textiles. At the 2022 edition of MFW, Vaishali’s deconstructed saris and dresses with 3D-mounted flowers caught everyone’s eye. And who can forget American rapper Cardi B’s electrifying custom-made gown crafted by Indian fashion designer Gaurav Gupta for the 2023 Grammy’s? The royal blue cutout sculptural 3D dress with a trail and headgear covering one eye was trending online for days, making it to Gaurav’s list of experimental sculpted designs.
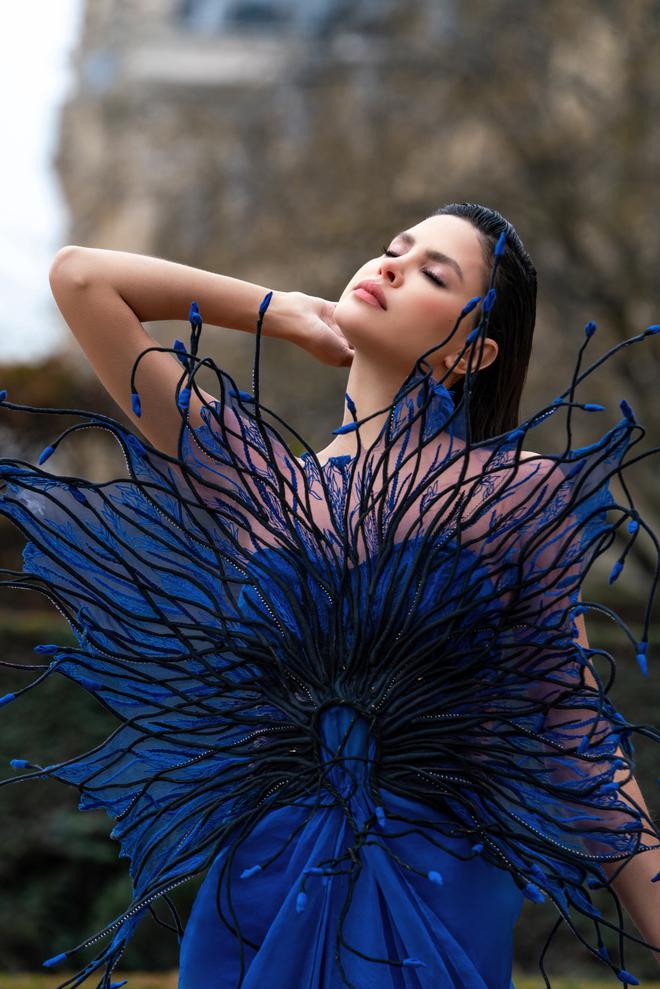
However, such experiments among Indian couturiers are few and far between. “3D fashion, for the time being, is a term that I use a lot, but with a different meaning. On my garments, 3D means my effort in making them with a 3D visual, like sculptures that can be admired from four different sides,” says Vaishali, adding, “I did try and use 3D for a better representation on my website, and also for a fashion show, but the end result is really still too cold and mechanic, well away with the sensations I want to communicate with my creations.”
Designer David Abraham of Abraham & Thakore believes that 3D printing is “just one more form of technology that will be added to the many existing technologies that are being used in the world of textiles and garment making”. He adds, “It is sure to play a role, but we cannot forget that the most extolled form of fashion is the couture which is a celebration of handicraft.” Having said that, he agrees that the technology can be “enormously useful” in the creation of 3D prototypes such as footwear and bags, and small accessories such as buckles, button closures, etc.
The sustainability quotient
Since it is made on demand, 3D printed fashion does not produce much material waste, making it far more sustainable than fast fashion. Virtual fashion’s rapid adoption in gaming and virtual worlds is fast becoming mainstream, says Chandralika Hazarika, co-founder of Bengaluru-based BigThinx, which works on visualisation solutions for fashion and retail brands across the US, Europe, and India. “3D design techniques can help in prototyping and sampling for resource efficiency and is time saving. It also allows local printing, avoiding the need to ship ordered items from distant places. As a result, customer returns can be minimised and emissions associated with this are negligible compared to current methods,” she elaborates on the eco-angle to tech in fashion.
Take, for instance, Foundree, a 3D-printed jewellery brand launched by Sri Gupta in late 2019 at Lakme Fashion Week. Having started with the idea of making contemporary jewellery, trying to find a vendor to make samples in brass and silver was a big struggle. “The costs involved in getting samples made and the minimum quantity order demands from the vendors was overwhelming,” she says.
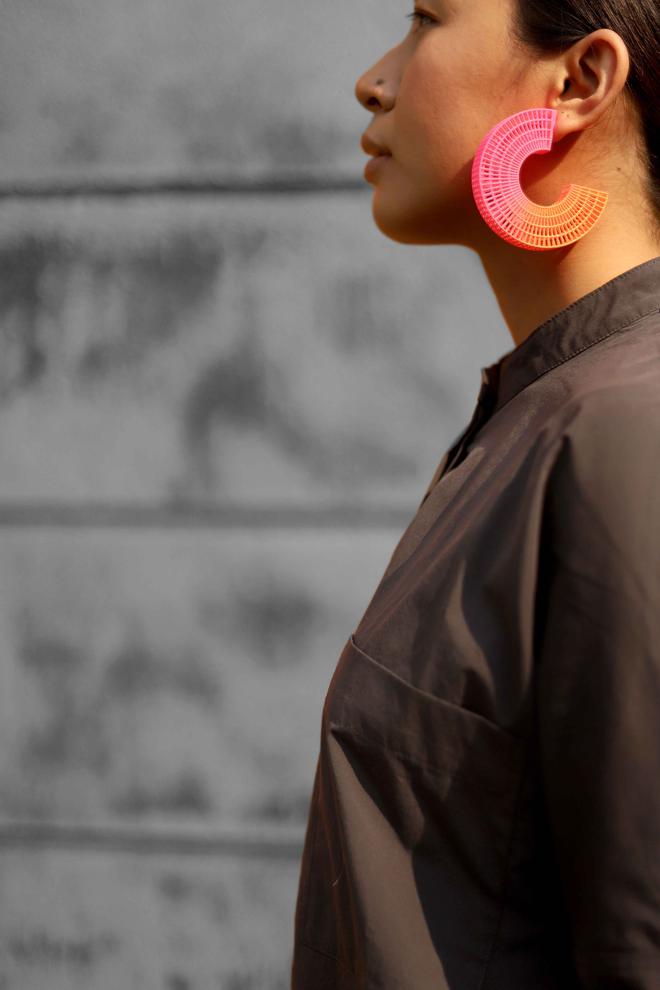
Sri chanced upon 3D printing and “fell in love” with 3D printed polyamide made by MJF (multi-jet fusion) technology. “It is a proto-typing material for industrial applications, but its material properties and the overall concrete-like appearance appealed to me,” says the designer whose latest collection, Flint, comprises lightweight 3D printed dome earrings, lattice bangles, and necklaces.
The 3D printing process does not involve mould making or casting and prints one piece at a time, making it cost-effective for an entrepreneur on a budget, says Sri. “The versatility of the new material and the process of getting samples 3D printed was done with such ease that I couldn’t go back to the thought of making jewellery in brass and silver!” Also, there are a lot of structures like interlinked forms, hollow objects, and living hinges that would be impossible to make using traditional jewellery-making techniques, she adds.
The Netherlands-based popular fashion-tech designer Anouk Wipprecht — who has designed apparel for the likes of Britney Spears and Black Eyed Peas — agrees. “There are possibilities to create complex shapes, cavities, and void spaces that you cannot do with other expensive manufacturing techniques like CNC and laser cutting” says the designer who is currently working on a brain-controlled design project with IT major HP that incorporates signals from the brain and biofeedback in the design.
Tech talk
Chandralika says the future of fashion is “made-on-demand”. “We will eventually see the death of fast fashion as slow fashion becomes more accepted and cheaper to produce. Digital fashion is also a big part of the future as people increasingly start to live their lives primarily in virtual worlds where physical limitations do not exist,” she says adding how technologies such as 3D printing are pivotal to this future because “production on-demand will require quick turnaround times for custom-made fashion”. Existing equipment is designed to handle repetition, but not variation and 3D printing will usher in the ability for fashion manufacturers to produce an infinite variety of customisations without investing in new equipment.
CEO Shivang Desai adds that among their top clients are two of the largest big box retailers in the US, and one from India, major global systems integrators, and luxury brands in Europe. “They are using our body scanning and virtual try-on technology for retail and the metaverse. In addition to solving returns and conversions related improvements, the biggest focus of brands this year is on customer experience, consumer engagement, and entering the metaverse,” he says, adding that for a brand to adopt 3D as a core part of their offerings, it could cost them as little as a few thousands of dollars each year.
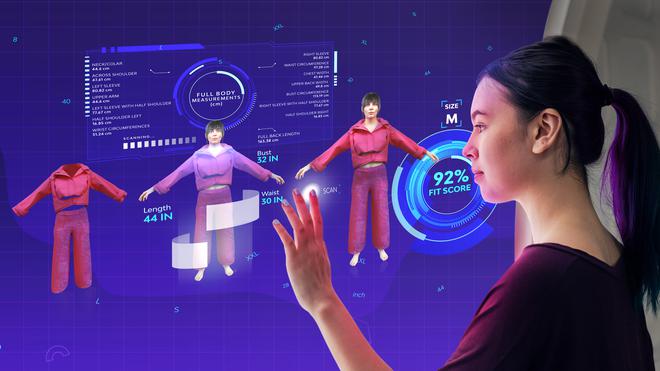
Substance 3D, the popular offering from tech giant Adobe, has recently seen fashion biggies such as Adidas, Hugo Boss, and Burberry, among others, “adopt 3D solutions as a part of their design workflow to present ultra-realistic images of cloth and textures in realistic product models”, says Francois Cottin, senior director of Marketing, Substance 3D at Adobe.
Anouk adds how 3D printing is great for customised design, and she has been using 3D printers since 2008. “The industry has expanded to a broad section of applications. For example, 3D Printing on fabrics with additive manufacturing company Stratasys’ new J850 TechStyle 3D printer which is the world’s first direct-to-fabric 3D printer,” says the designer who created fashion-tech creations for Journey, a theatrical gastronomy event that launched in New York this January.
“I use both 3D modelling software — currently OnShape on a project, but also play around with software like Rhino, Maya, SolidWorks, and Zbrush with collaborators — to shape and design my creations. I also use coding software (like Arduino/Python) to programme my designs. Tool-wise, I use a sewing machine for the fabric part (the dresses), a computer for both design and coding, and tools like a soldering iron and pliers to engineer my designs,” elaborates Anouk.
Francois says the company recently added breakthrough capabilities in Substance 3D to capture real-life objects in 3D models simply by taking a series of photographs. “This creates an efficient way to digitise products or prototypes with extremely high fidelity and modify them to explore variations or use them for marketing/retail imagery production.” This way, he says, brands can save time and attain unbeatable realism for product design and visualisation with “access to thousands of high-end and ready-to-use materials, such as wood, marble, concrete, and tiles in the 3D assets library, or create custom materials from pictures using Substance 3D Sampler or create them from scratch with Substance 3D Designer”.
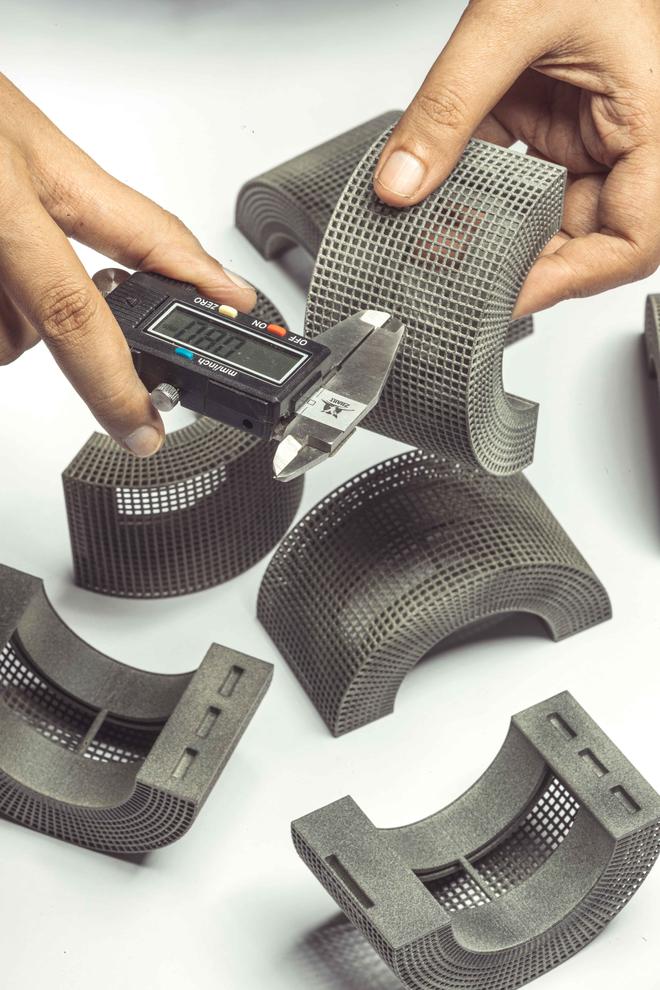
Challenges
Addressing her primary challenges, Anouk says washability, maintenance, and powering designs (batteries) “are things people that work in my field are always working on”. “How can new batteries to power electronic designs be shaped? What about safety? Given water is our biggest enemy, how can we clean electronic or 3D-printed designs that have interwoven electronics? How do we maintain these designs in terms of physical appearance or even updates and upgrades?” are the questions she raises. Perhaps queries that many designers closer home have too.
For Sri, working with a new material and technology was a challenge in itself. “When it’s a known material, like wood, a manual of sorts exists that tells you about its limitations and benefits, and how to design for that material. For me, this manual did not exist,” she says, adding, “When I started making earrings in 3D printed polyamide, one of the challenges was to integrate the earrings with the 3D parts. Another challenge was to figure out what kind of paints work on polyamide.”
Into the future
While still far from mainstream, these experiments prove that it is possible to create a future where 3D printing completely replaces traditional methods of production, says Chandralika. “However, we are still a long way from the realisation of this eventuality as brands need to first invest heavily into 3D printing technology.”
Also, personalisation and customisation come at a premium today, but with 3D printing, it is very likely to become a norm since each piece can be printed on demand, says Sri. Think custom-fit shoes, eyewear, jewellery, and garments. “Designers will not be restricted by the limitations of standard manufacturing processes. We can also foresee a future where you can download a 3D file from a designer’s website and print the object right at home with your own 3D printer.”
So, would David look at experimenting with 3D fashion in the future? “Only if necessary,” says the designer, who explains the concept is yet to pick up pace in India because the tech is simply not accessible. “Designers in India are fortunate to still have access to workshops and high-level hand skills and crafts which play an important role in the prototyping of products. If 3D technologies are more accessible then, at some point, we will see an interesting combination of technologies that draw both from modern futuristic technology as well as human hand skills,” he says.
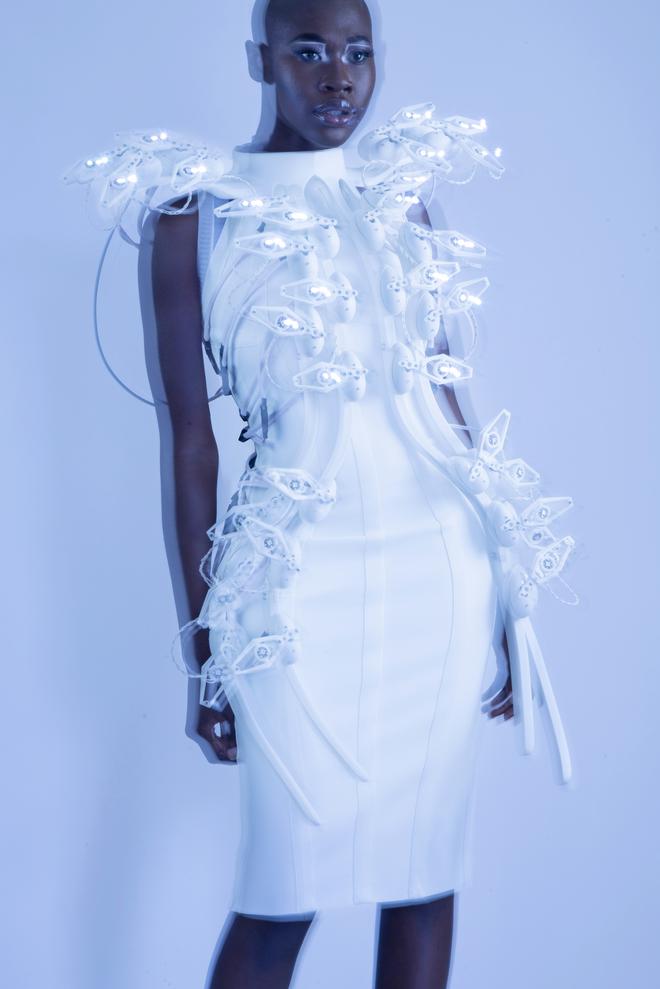
While Vaishali agrees tech has amazing advantages in terms of sustainability, she finds it difficult to adopt “because I am a very emotional and manual person”. “I like to have a close relationship with the materials and depending on their reaction in my hands I drape them around the bodies. Indeed, 3D fashion helps save a lot of material, is extremely fast, can adapt to different situations, and given the right inputs can create perfect pieces with fewer mistakes. I believe large groups will follow this path aggressively, while more couture bespoke designers will use it only marginally.”
Having said that, she will look at experimenting with tech “eventually”. “In some time, yes. When everything will become more ‘human’, or when I will become less passionate about my creations! But not for the time being. The creative style and process doesn’t allow for it, and the bespoke nature of my garments also doesn’t really fit.” She adds, “We designers are still more creative tailors, and the workmanship is still very much the focus of our creations. Eventually, especially with the rise of bigger and more commercial groups, and younger, tech-savvy designers, 3D may get popular.”
The future of fashion will get “wilder, more custom to personalities and more electronic — with sensors embedded, that measure your vibe or emotions,” says Anouk, adding, “It will be able to showcase personal elements of yourself to the outside world.”