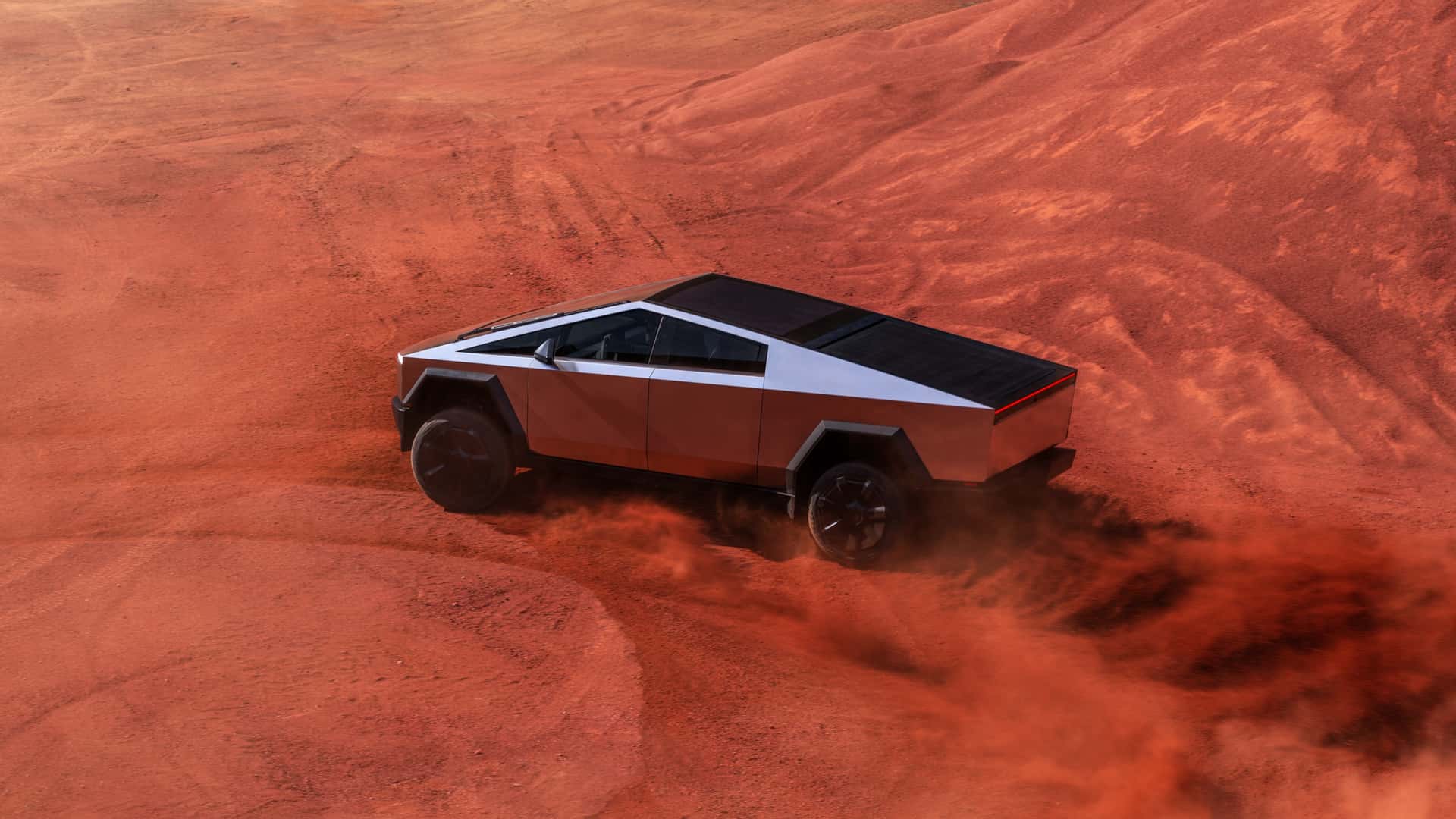
Inside Tesla’s Gigafactory Texas, it seems like the robots are the full-time employees, and humans are just there to supervise them. The sprawling floor of the stamping building—with its white walls, red stripes, and massive presses scattered all around—appears to be quite a neat setup, almost fully geared up and all set for mass manufacturing, Munro Live’s latest video showed.
Before we dive into how the door panels are made, here's a quick recap on how long it took Tesla to reach this stage: Tesla dropped the news about the Gigafactory Texas back in 2020. Construction started in July that same year, and in April 2022, Musk inaugurated the site. In just a few years, Tesla has not only started cranking out the popular Model Y at this location but also managed to solve the engineering nightmare that was the Cybertruck.
The factory tour showcases how Giga Texas isn't merely Musk's pet project—it's quite an engineering feat. It also helps us understand what might have caused the long delays in its development cycle and deliveries.
For starters, huge steel coils come in and undergo a series of processes before turning into bulletproof door panels (Not to all guns, obviously). In the video, Lars Moravy, Tesla’s vice president of vehicle engineering explains each process that leads to coils becoming fully assembled door panels. It all starts with a machine that straightens the coils before entering laser cutting booths, where they’re cut into sheets with micron-level precision. One of the engineers said the laser was the first of its kind, and was a special development between Tesla and German industrial equipment manufacturer Schuler.
Tesla operates 21 furnaces at the site, where the materials are heated to 900 degrees Celsius before getting stamped, one of the engineers explained in the video. The furnaces are manufactured by the Swedish company AP&T. And this is how they work: a stainless steel sheet, that would go on to become the body side inner door, is first heated in the furnace, and it then gets swiftly picked up by a robot before being dropped into the stamping press—all within a matter of seconds.
I’m no engineer, and yet it seemed clear to me how Tesla is aiming to revolutionize manufacturing and make it more efficient. “Simple is usually better,” Moravy told Sandy Munro. While the different stations and booths aren't seamlessly integrated—manual forklifts are required to bring the components to the final door assembly line—the factory tour indicates that most of Tesla's nightmares related to the Cybertruck might now be history.
Some things, though, remain unproven. “[Tesla is] ready to roll [the Cybertruck] at high volume. Now it’s just like, how do we ramp and how do we get the quality right,” Moravy added.