
The Mercedes Concept CLA Class is just the sort of car that could not only take on the Tesla Model 3 if it becomes a reality, but could also feature a battery that is almost entirely made of recycled materials.
Mercedes-Benz wants to complete its plan for creating a greener, circular manufacturing process after building a new battery recycling plant in Kuppenheim, Germany. The automaker claims that, once it’s up to speed, the facility will be able to recycle up to 96% of the raw materials contained inside its electric car batteries.
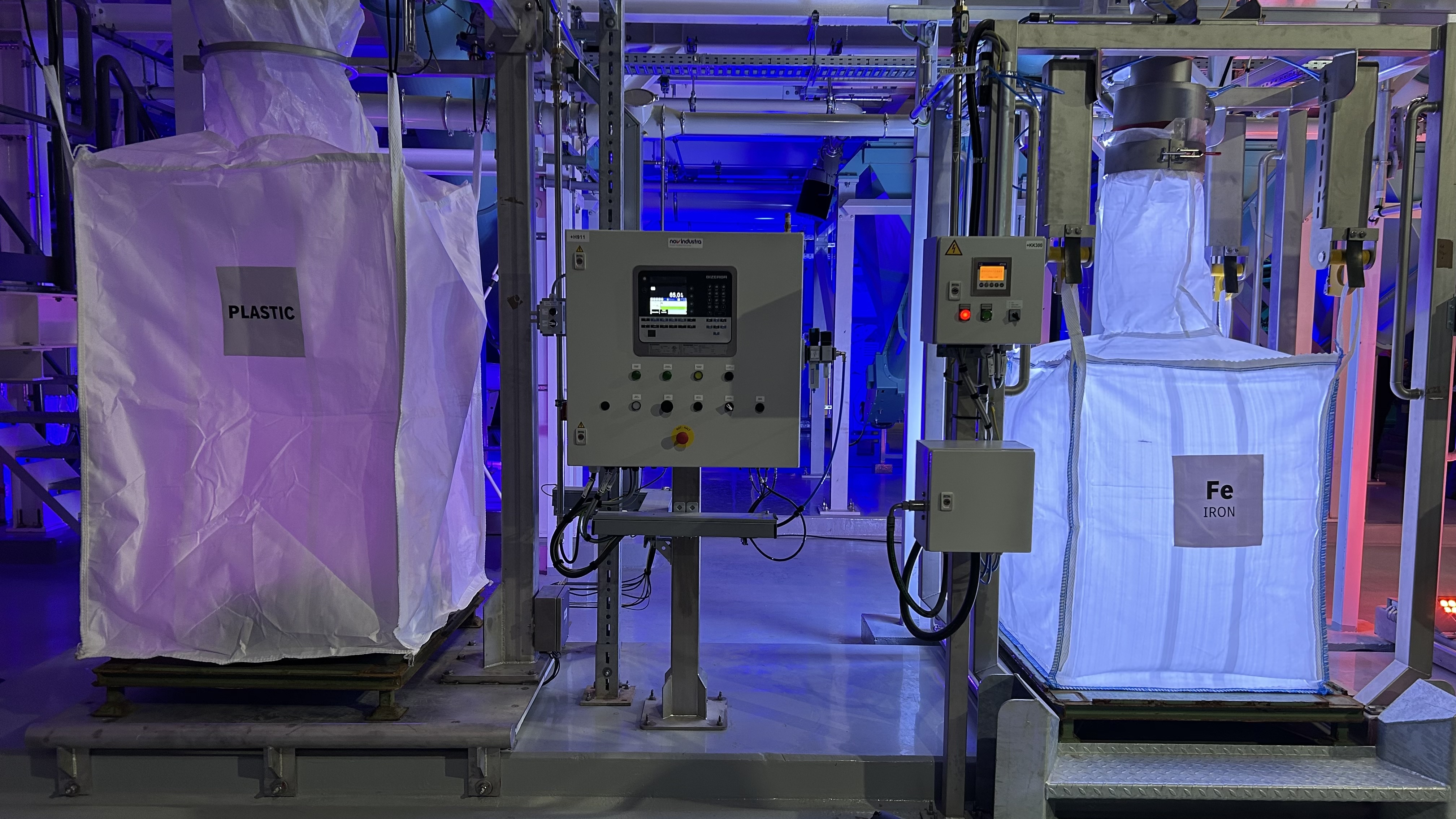
Peak production
At peak production, Mercedes-Benz forecasts that the high-tech plant will be able to deliver 2,500 tonnes of recycled materials from the production-line process. The extracted materials could subsequently be used to manufacture 50,000 battery modules every year, which equates in practical terms to 5,000 new EV batteries annualy.
Much of the Kuppenheim workforce will be made up of staff who previously produced transmissions for the company and who have since been retrained to tackle the ambitious recycling task. The plant itself has been built from scratch in just a year and a half, although it will be some time before the facility will be running at full capacity.
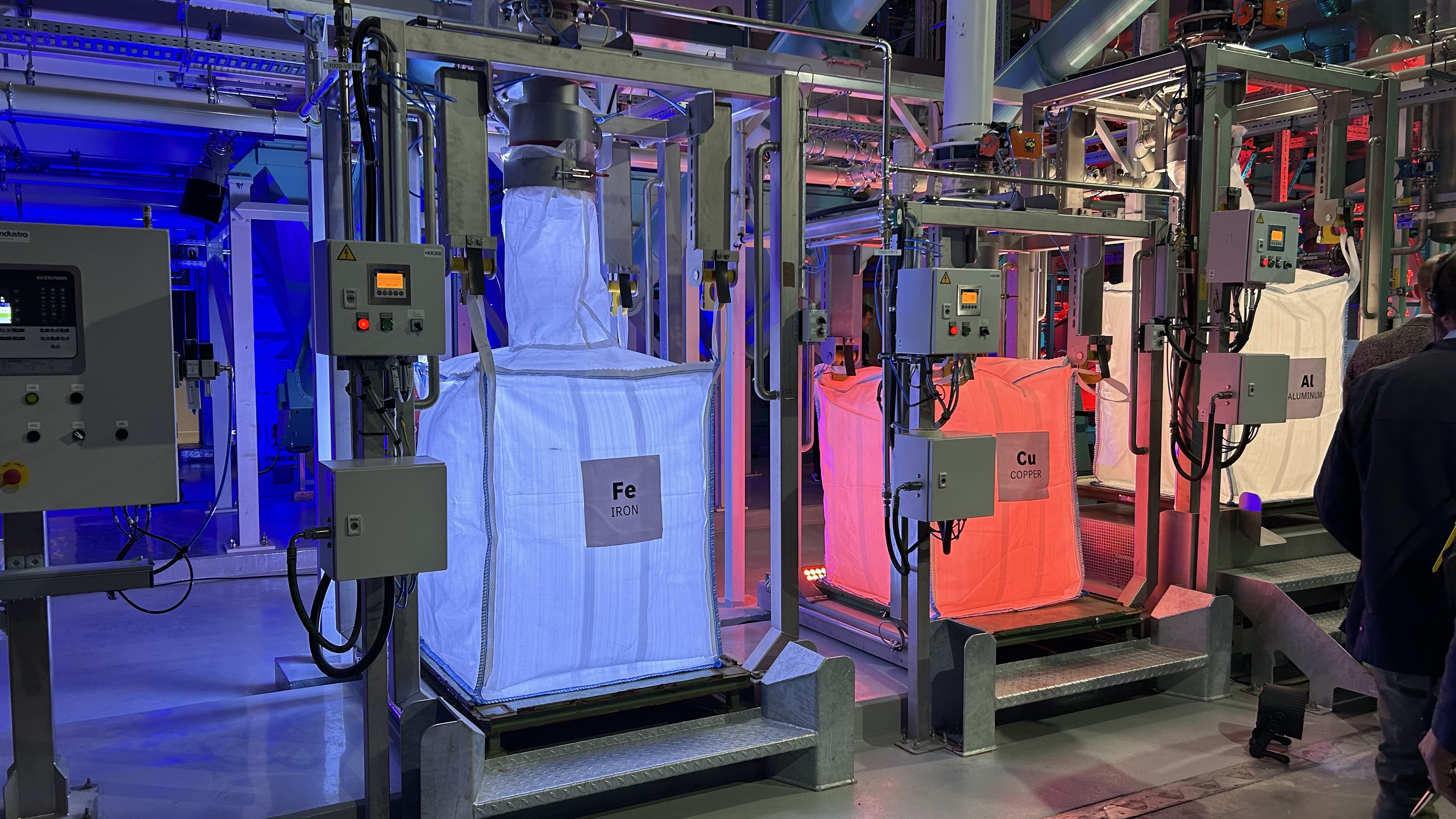
Optimum efficiency
Kuppenheim will initially be recycling batteries from the likes of production scrap and test vehicles until its production models start reaching their end-of-life stage, although that could take anywhere between eight and ten years. In the years running up to peak performance, the process looks set to be tweaked and fine-tuned to produce an optimal recycling production line
The mechanical-hydrometallurgical process involved in recycling EV batteries at Kuppenheim is complex, but much more environmentally friendly than existing processes that use blast furnaces, lots of heat and enormous amounts of energy to get the job done. During the various stages, the process separates plastics, copper, aluminium and iron in a production line-esque series of stages.
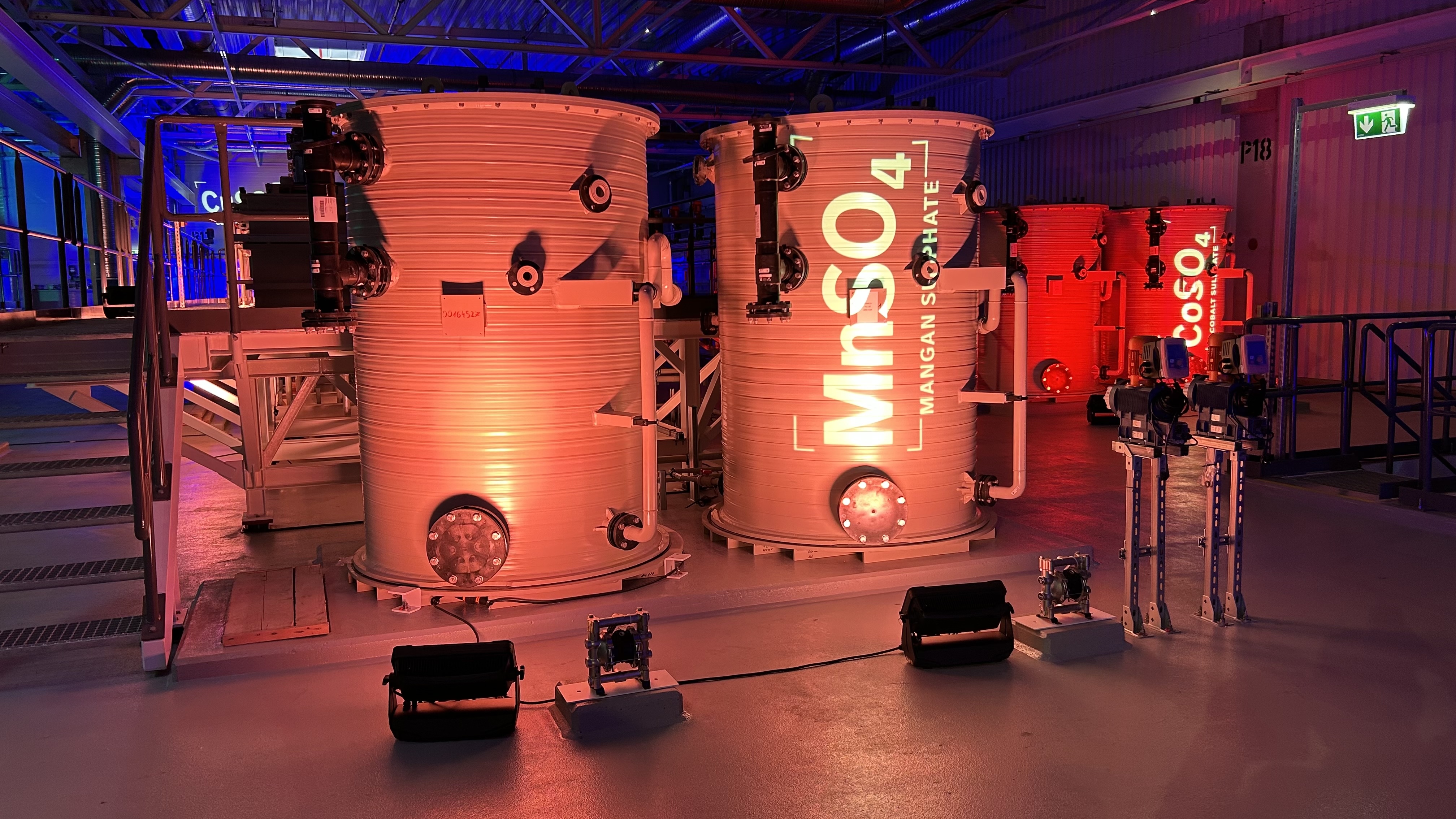
Production line process
First, old battery modules pass through a shredder, followed by a friction washer and the materials then move through an air separation section of the line. Electromagnetic separation pulls out more elements before the material is passed through a vacuum dryer and mill, followed by a filterpress. This results in an end product known as ‘black mass’ containing vital chemicals from the shredded electrodes.
The material recovered from this process then continues its journey, moving through leaching, another filterpress area followed by a neutralisation section before solvent extraction and, finally, crystallisation methods are used to complete the process.
While the recycling aspect is undeniably high-tech, there’s a good deal of chemistry involved in the extraction stage. This is comprised of mixing, settling and scrubbing using Sulphuric Acid and finally stripping of the material prior to the process completing its various stages.
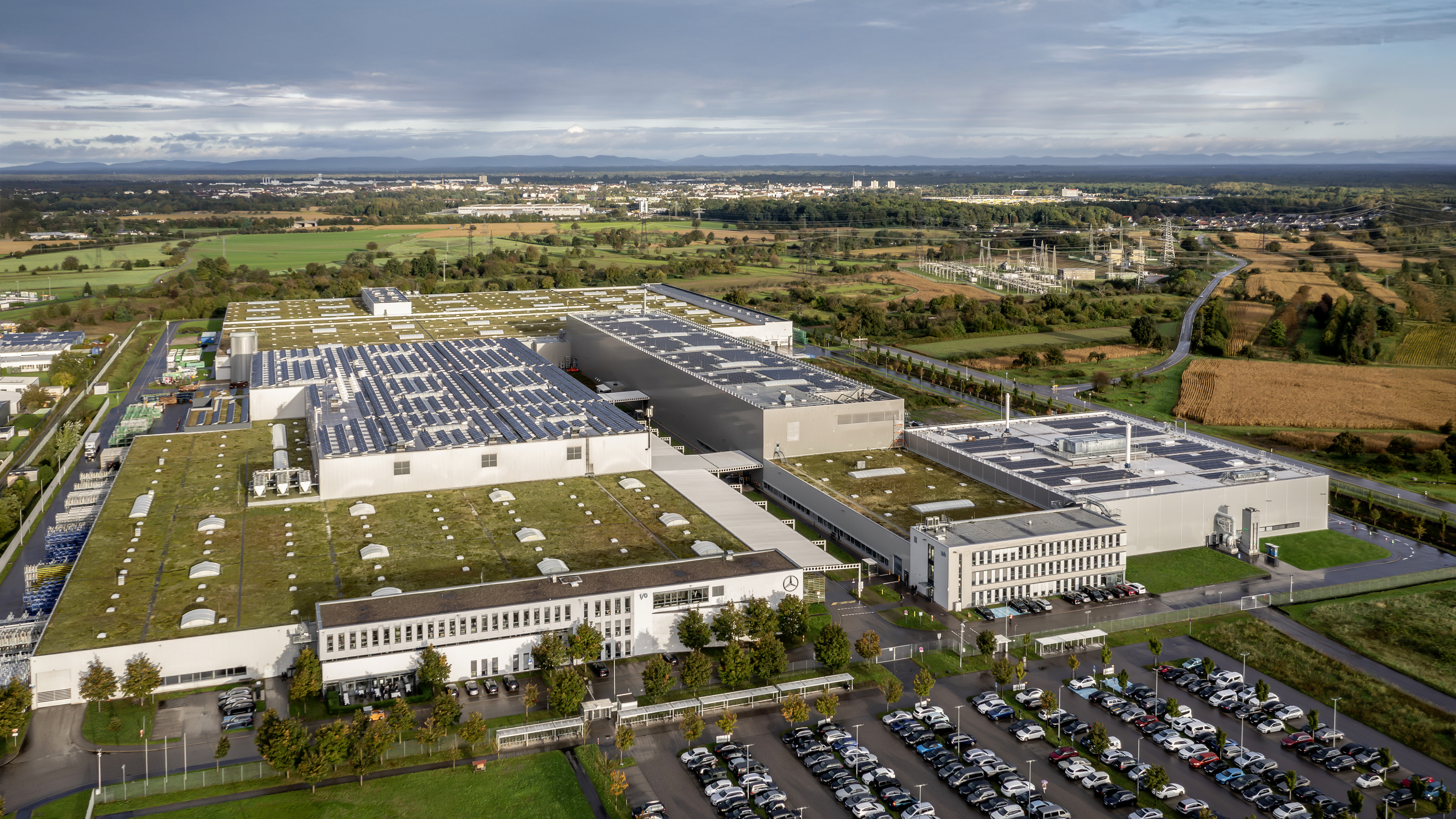
Achieving carbon neutrality
Adding to the greener credentials of the location is that the 6,800 square-metre facility itself has been built with efficiency in mind. The plant will be generating energy from photovoltaic panels on the roof and wind turbines on the surrounding land as part of its goal of becoming carbon neutral.
Mercedes-Benz wants to be become fully carbon neutral by 2039 and, thanks to the work going on at Kuppenheim, that now seems more possible than ever.