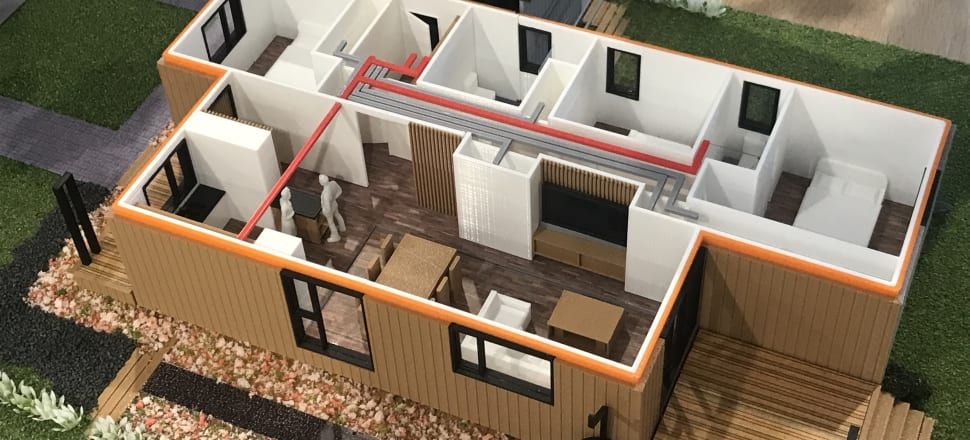
The average Kiwi home needs to be seven times more carbon efficient than it is now to meet global 1.5C warming targets. Nikki Mandow checks out a home design that could get us there
Four Fletcher Building 1.5C pilot homes – blueprint houses to help New Zealand reach the global climate change goal of no more than 1.5C of warming – are ready to go to council for building consent.
The homes are part of the 700-home Waiata Shores development in South Auckland. Construction could start in three months, says Steve Evans, chief executive of Fletcher’s residential and development division. The first homeowners should be in within the next year.
After almost two years in the design phase, Fletcher wants the LowCO homes – one standalone three-bedroom house and a three-unit terraced home block – to provide research data and practical costings to push the building sector and Government to address greenhouse gas emissions coming from residential housing.
Construction industry research body BRANZ estimates buildings are responsible directly or indirectly for almost 20 percent of New Zealand’s greenhouse gas emissions.
This comes through a mix of energy use over the decades the building is occupied, and emissions from the extraction, processing, transport and installation of building materials, plus maintenance of those materials (repainting, or replacing roof or carpets, for example).
However until now there have been few economic incentives to encourage action to reduce emissions from residential properties, including nothing in the New Zealand building code to force buildings to be net-zero carbon, BRANZ said in a paper in 2020.
“Even if the demand were there, the industry has significant gaps in skills and knowledge.”
The Low Carbon 1.5C pilot is designed to help fill that gap, Evans says, providing information on what works and what doesn’t to build a home that is not only low emissions in terms of building materials, but also in terms of energy efficiency over a 90-year lifespan.
Why 90 years? Well, you have to draw a line in the sand somewhere.
Step one: Keep the physical footprint of the house really basic, says Nicola Tagiston, head of sustainability at Fletcher Living and in charge of the LowCO project.
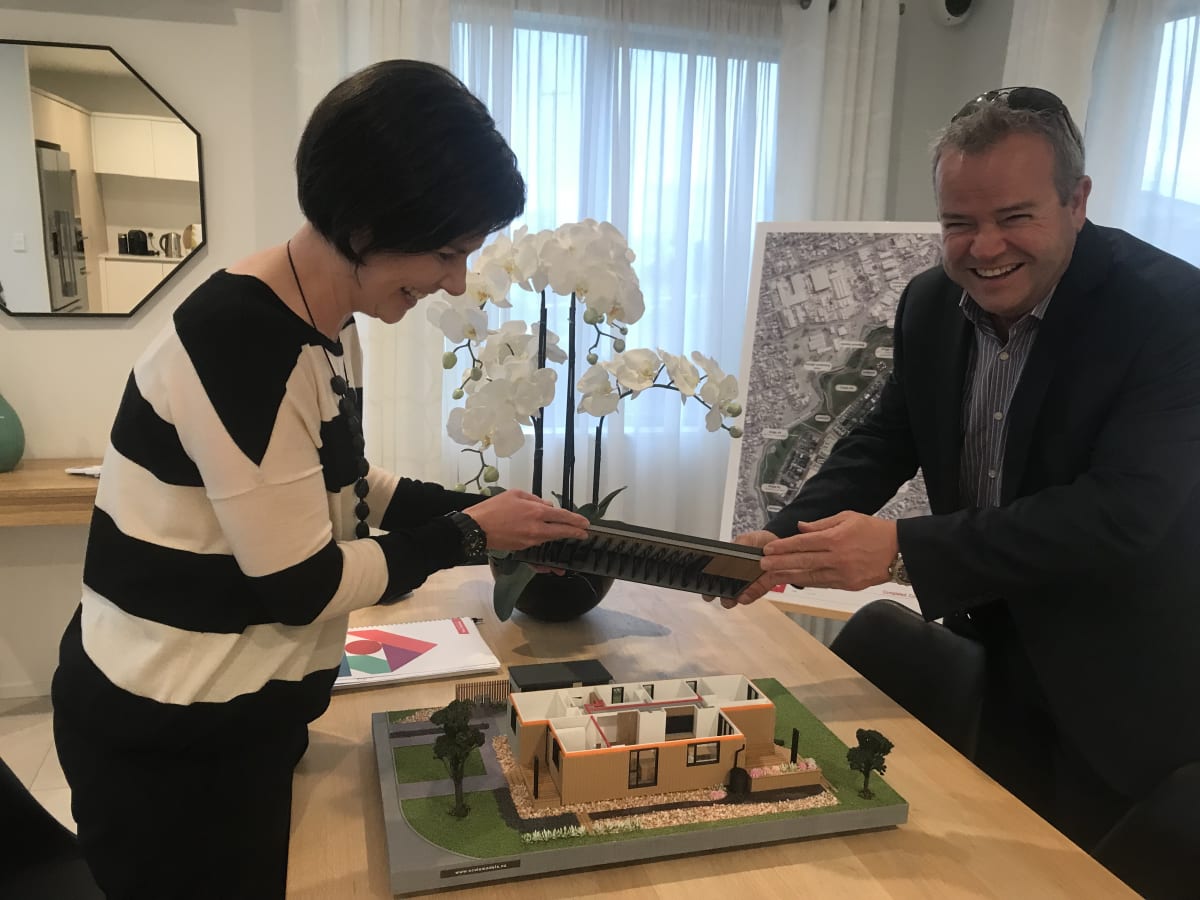
“A simple, uncomplicated square or rectangular box is the best from a carbon perspective, because it uses fewer building materials,” she says.
Think, minimising your wall to floor ratio, and keeping the number of corners to a minimum. Heat sneaks out through corners.
Next step: look at your building materials. Tagiston says it was important to minimise the amount of concrete, which is estimated to be responsible for 4 to 8 percent of the world’s CO2 emissions. Instead they settled on a wooden floor without concrete foundations – the “suspended timber floor” design used in the original colonial villas.
Where concrete is unavoidable – on the garage slab – it’s made using what Evans calls “low carbon cement” from Fletcher’s waste tyre-fuelled plant in Northland.
“We said ‘Can we design and build a home which would meet that one and a half degree future?’ And we decided we should do it.” – Nicola Tagiston
Same with the roof. With steel manufacture being a carbon-intensive industry, Tagiston and her team tried to keep it to a minimum.
“The original design had a larger expanse of steel on the roof – a pure aesthetic decision by the architect. But we were looking to eliminate as much carbon as we could, so we asked them to push further and maximise the amount of timber used instead. So we’ve been able to cut down the amount of steel.”
“For every component of the building, we’ve analysed what the carbon could be, and where possible we’ve designed to eliminate, and where we can’t eliminate, we’ve looked at how we can lower the amount of carbon used, and where we can’t do that we can offset with the likes of solar photovoltaic panels on the roof."
Turning 270 tonnes into 39
In 2020, Tagiston attended a BRANZ seminar and heard for the first time about Massey University/BRANZ research breaking down New Zealand’s total carbon footprint by sector – right down to an individual building level.
The total amount of CO2-equivalent generated by a standard three-bedroom New Zealand home over the course of its construction and a 90-year life was 270 tonnes, the study found.
“Then what they did was took the 1.5C budget needed to meet New Zealand’s 2050 global warming targets. And they took that right down to a single three-bedroom home, and they said one home can only use 39 tonnes of carbon equivalent over its 90-year lifespan,” Tagiston says.
That’s just one-seventh of the standard home.
“So we came out of that seminar and we said ‘What a challenge to have. Can we design and build a home which would meet that one and a half degree future?’ And we decided we should do it."
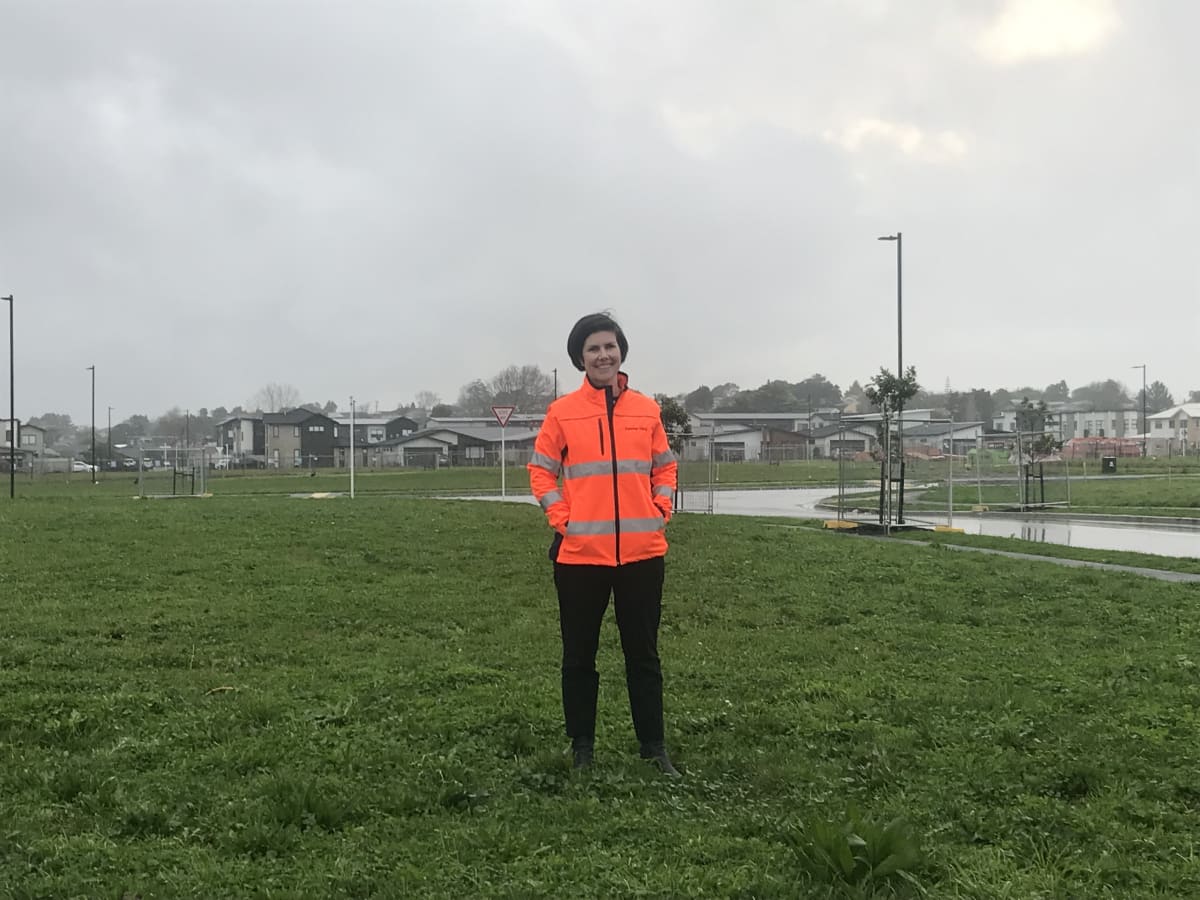
It hasn’t been easy. Sometimes it’s involved a trade-off between the building and the 90-year ‘live in’ part of the project, Tagiston says.
For example, they looked at whether triple-glazed windows would produce enough additional reduction in heat loss over the life of the home to mitigate the extra emissions from manufacturing an additional layer of glass. The answer to that one was ‘no’.
At other times, it’s been about unexpected solutions sneaking carbon emissions down a fraction. Like using French doors not ranch sliders – apparently you can get a better seal with a door. Or switching out lawn for ‘meadow’ at the front of the section to cut down on mowing.
One of the more surprising findings was that using a battery to store electricity from the solar panels was not a good idea, emissions wise.
While it would cut down energy use during the life of the home, the huge amount of CO2 produced making lithium ion batteries and the relatively short lifespan of batteries at the moment made not having them a better proposition.
“Throughout the process we’ve been very clear we wanted to make data-driven decisions and decisions based on good, robust scientific arguments,” Tagiston says. “So it's certainly been helpful in that we've got firm analysis sitting behind the calls that we've made on the design stage.”
Having that rigour will also be useful for the next stage – persuading Government and other industry players.
Once the homes are finished around March or April next year, Fletcher Building will have a better idea of how much the 1.5C house will have cost to build – or rather, how much more expensive than a normal house it will have been, Evans says. Until then he's not prepared to take a guess.
But those numbers and lessons learned from building the homes will start the debate.
“I think what we would be asking the Government to do is enter into a more fulsome conversation on what we need to do in the residential space in New Zealand to meet the aspirations not just of Government but of individual people to address climate change,” Evans says. “We can't say, at this stage, whether that means we need to increase the regulations or do x, y, or z. But it might be possible once we get that information.”