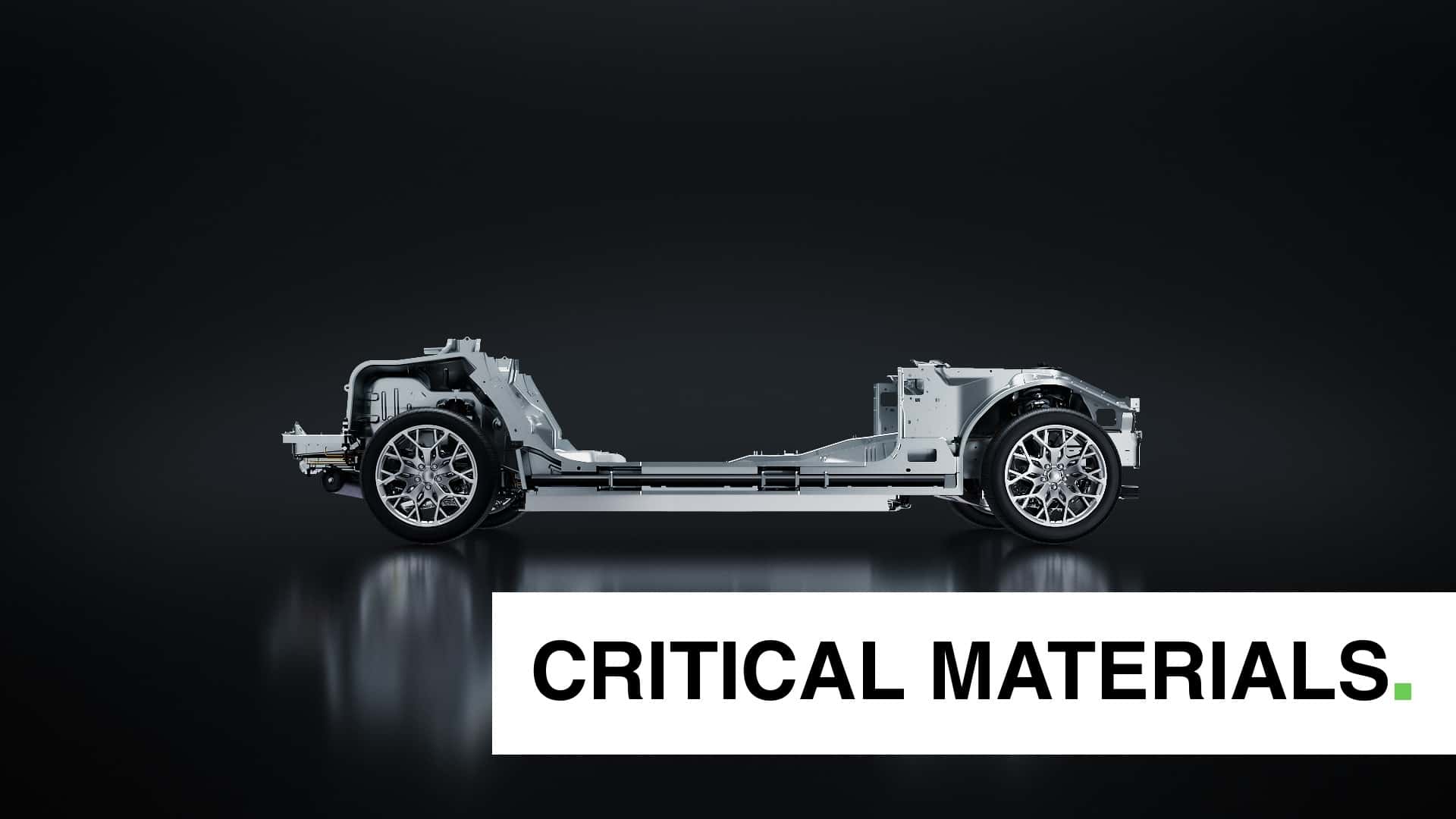
EVs are bloated. It's posing not only a safety problem, but also an efficiency one that sends automakers in a seemingly endless loop of balancing EV range, weight, and battery size. Stellantis CEO Carlos Tavares says that needs to stop.
Welcome to Critical Materials, your daily roundup for all things EV and automotive tech. Today, we're discussing Stellantis CEO's call for lighter EV batteries. Plus, Tesla begins scouting locations for a potential Gigafactory in India, and one shipping company stuck in the port of Baltimore says the Key Bridge disaster will cost it up to $10 million. Let's jump in.
30%: Stellantis CEO Says EVs Need Lighter Batteries

Stellantis CEO Carlos Tavares says that EVs need to go on a diet.
More specifically, their battery packs are causing the scales to move in the wrong direction. That's not exactly new information—we've known that EVs are generally heavier than their gas-powered counterparts, but Tavares believes that it's a bigger problem than it's currently made out to be.
Tavares says that it takes about 1,000 pounds of raw materials to construct a battery that achieves a "decent" range of 250 miles. He might not be far off either, as the battery pack in a Tesla Model 3 weighs in at as little as 1,060 pounds. On the other side of the scale, the GMC Hummer EV's humongous pack weighs as much as a Honda Civic at 2,818 pounds.
To do that, automakers must look at increasing the energy density of cells. Here's what Tavares has to say:
The industry, based on new chemistries, needs to achieve in the next decade a breakthrough in terms of power density of the cells, so that we reduce by at least 50 percent the weight and the raw material usage of EVs. I think that that's on the way.
That is going to be broken over the next decade by a new chemistry, which, by the way, hopefully, will solve the problem of the scarcity of lithium."
He's not wrong, you know. One of the biggest drawbacks to current EVs is the weight. Most of that extra poundage comes from large battery packs needed to achieve the 300-plus range that many consumers want—all in the name of avoiding the possibility of an extended charging session at a public charger.
All of that extra weight requires wasted energy to move. According to the U.S. Department of Energy, a gas-powered vehicle's efficiency is reduced by about 2% for every extra 100 pounds it carries. It's likely that translates into a similar efficiency loss for EVs. So, as Tavares is alluding to, shaving that pack weight by half (or more) would increase range.
Lighter EVs could potentially mean less tire maintenance, less road wear, and safer collisions. It seems like shaving off a few pounds would be a great move, no?
In actuality, it seems like automakers are going to need to perform a complex balancing act. These next-gen batteries must be quick to charge, energy-dense for lighter packs, and still achieve great range. It almost seems like an impossible task when it would be so easy to keep vehicles at the same weight and stuff denser batteries in them for the bragging right of "class-topping range."
60%: Tesla Begins Scouting India for Plant Location

Tesla is reportedly sending a team to India this month to scout potential locations for a new factory.
According to the Financial Times, Tesla has finally initiated the process following India's decision to lower tariffs on EVs priced at $35,000 or more to 15%. Previously, India taxed imported EVs over $40,000 between 70% and 100%.
There's just one gotcha: in order for the tariffs to be dropped to 15%, automakers must commit to building a domestic factory within three years, hence Tesla's potential $3 billion investment to capture the EV market in India.
From FT:
The people with knowledge of Tesla’s plans said it would send a team from the US by late April to study sites for the plant, focusing on states with existing automotive hubs, including Maharashtra and Gujarat in the west and Tamil Nadu in the south.
Some automakers have plants in Haryana state neighbouring New Delhi and one of the people said they thought Tesla might also scout potential sites around the capital. However, the second person said the focus of Elon Musk’s company would be on the other three states because they had ports, making it easier to export cars.
The aspect of exporting cars appears to be an important factor for Tesla's decision on a location. Potentially, Tesla could export the vehicles built at a plant in India globally, which may be a huge cost-cutting win as it explores the plausibility of its $25,000 EV.
The biggest savings would likely be labor given that India has a highly competitive job market that has tanked annual wages of production workers. This could potentially lead to labor rates significantly cheaper than Gigafactory Shanghai and Tesla's yet-to-be-built plant in Mexico.
Tesla isn't the only automaker looking towards India given the new regulations. VinFast has recently pledged to build a $2 billion plant in Tamil Nadu and BYD has been working to score approval for its own plant since last year.
90%: Auto Shipper Says Baltimore Key Bridge Collapse Will Cost It $10 Million

Wallenius Wilhelmsen, one of the world's largest maritime automotive logistic companies, says that it will take a hit as hard as $10 million due to the Francis Scott Key Bridge collapse in Baltimore.
The Norwegian shipping company (which services large automakers like BMW and Volvo) has had at least one of its ships, the Carmen, stuck in the port of Baltimore since the bridge disaster last week. Crews have been working to clear channels to begin moving vessels out of the port, though the logistics company believes that operations will result in shipping complications lasting up to a month.
Wallenius Wilhelmsen put out the following statement on Wednesday:
We have estimated that the aggregated provisional total financial impact on EBITDA of the situation is in the range of $5-10 million, assuming the disruptions last for up to a month. We currently expect the closure to last for weeks and have based our impact estimates on that assumption.
Once open, we anticipate the terminal will also promptly resume normal cargo operations as vessels begin to make port calls as previously scheduled.
Baltimore is the largest port in the U.S. for importing and exporting passenger cars and light-duty trucks. This means automakers and private shippers that utilize the port will need to either delay shipments, or arrange to have their vehicles transported to other ports like Newport News, Virginia, Newark, New Jersey, or Savannah, Georgia.
The $10 million hit to this shipping company is just a drop in the bucket compared to the overall costs of the disaster. Analysts predict that the entire impact is as high as $4 billion, a record for insurers to cover related to shipping losses. The ship's owner and managing company have filed a petition in Maryland to cap its liability at $43.6 million.
Audi, Bentley, Ford, General Motors, Jaguar Land Rover, Lamborghini, Mazda, Mercedes-Benz, Nissan, Subaru, Toyota, and Volvo all utilize the Port of Baltimore for importing and exporting vehicles and parts, according to Automotive News.
100%: Would You Sacrifice Range for Charging Speed?

As Stellantis is looking to improve energy density in batteries to drop weight, charging companies are fighting an equally important battle: faster and denser DC Fast Chargers.
One quick way for EVs to drop weight would simply be to drop battery size. In theory, if charging companies are able to quickly deploy DCFCs across the nation, an EV with a smaller battery could operate more efficiently and cost a lot less than a car with a huge 200-kilowatt-hour battery pack. Kind of like what Mazda attempted to do with the 100-mile MX-30.
That being said, if DCFC was more accessible, would you be willing to give up some range for cheaper, lighter cars?