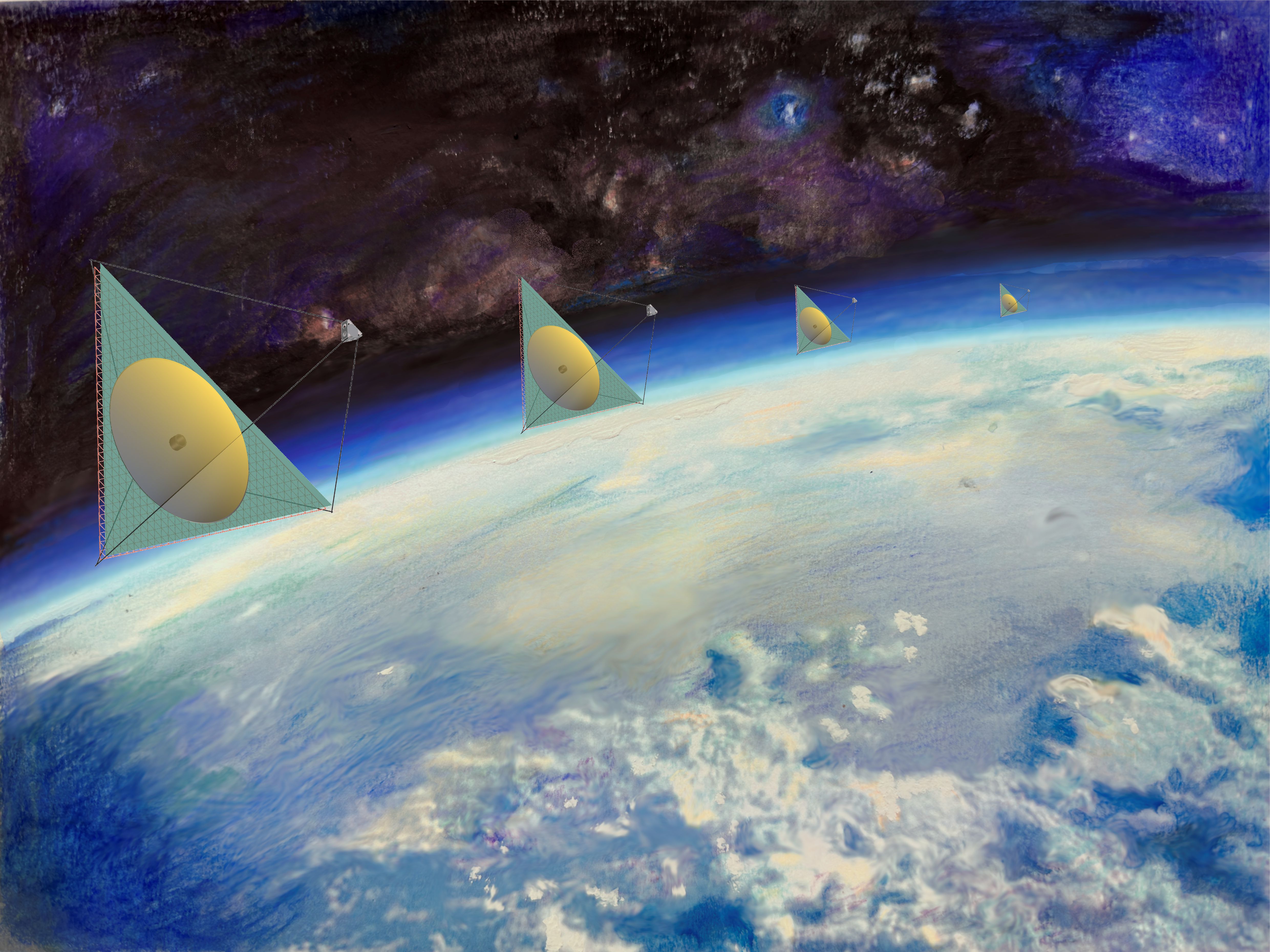
A scientist says it may be possible to create low-cost foldable telescope mirrors that are more than twice the size of those onboard the James Webb Space Telescope (JWST), whose giant iconic golden honeycomb mirror is the largest ever sent to space.
JWST's network of 18 gold-coated segments make up a primary mirror that's 21 feet, 4 inches (6.5 meters) in diameter. Now, a scientist has come up with a new method to produce extremely large telescope mirrors that he thinks will be thinner, lighter and more affordable than many of the optics currently in orbit.
This new way "could help solve weight and packaging issues for telescope mirrors, enabling much larger, and thus more sensitive, telescopes to be placed in orbit," Sebastian Rabien, a scientist at the Max Planck Institute for Extraterrestrial Physics in Germany and the sole author of a new study detailing the tech, said in a statement.
Related: Giant next-generation space telescopes could be built off Earth
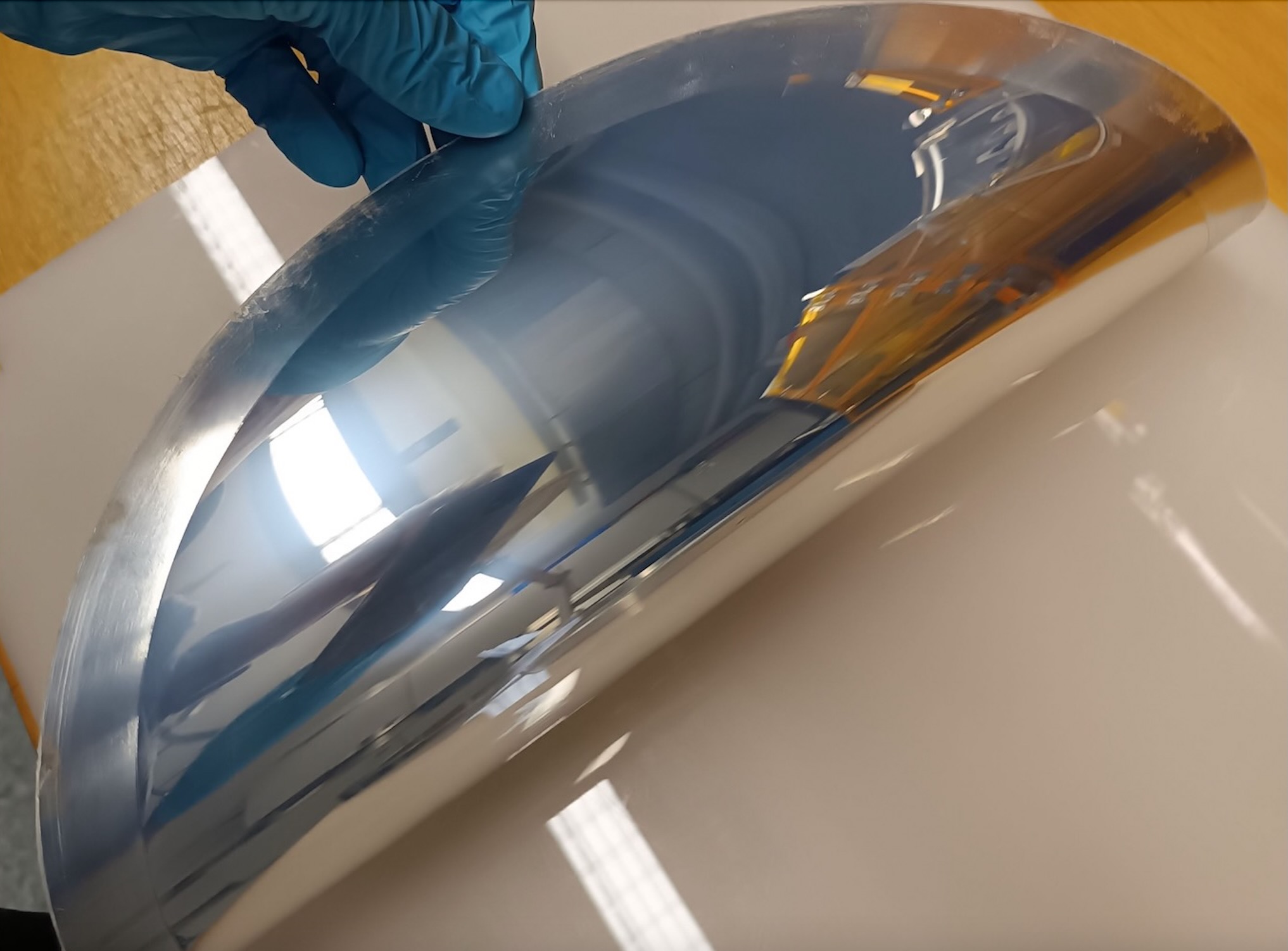
Using his new method, Rabien built a mirror 0.9 feet (30 centimeters) wide. He created what is called a membrane mirror by placing an evaporated material, the identity of which is not disclosed in the statement, into a vacuum chamber. Soon after, a lightweight polymer membrane, likely as thin as household plastic wrap, began to form.
Next, to mold this membrane into a parabola — a necessity for space telescopes, as the shape allows better focus by directing incoming light into one spot — Rabien added a "rotating container filled with a small amount of liquid" to the inside of the vacuum chamber. This allowed the polymer to grow and form the base of the mirror. Coating the mirror with a reflecting surface like aluminum would make it telescope-worthy, according to the statement.
Rabien proposes using his new method to create massive telescope mirrors, which are usually complicated and expensive to put together. (For example, it took the JWST team eight years to build the telescope's mirrors.) The method has the potential to create mirrors that scale beyond the sizes of those onboard current space telescopes, the statement notes.
"Although this work only demonstrated the feasibility of the methods, it lays the groundwork for larger packable mirror systems that are less expensive," Rabien said in the same statement. "It could make lightweight mirrors that are 15 or 20 meters [49 to 66 feet] in diameter a reality, enabling space-based telescopes that are orders of magnitude more sensitive than ones currently deployed or being planned."
These large mirrors could be "rolled up" to fit compactly onto rockets to ride safely to orbit, Rabien believes. Once aloft, Rabien envisions flawless deployment of the mirrors, thanks to another method he developed that would use heat to ease out any kinks that would form after the mirrors unfold. Such gigantic sizes would, in turn, make telescopes bigger and more sensitive, allowing astronomers to collect higher quality observations.
Rabien details his research in a study published this month in the journal Applied Optics.
A similar was undertaken in 2010 by the U.S. military’s advanced research wing, the Defense Advanced Research Projects Agency (DARPA), which funded a project to explore replacing traditional telescope mirrors with a polymer membrane. The goal was to create a lightweight foldable space telescope that could capture real-time videos and images of Earth in high resolution.
DARPA's funding for the project — known as the Membrane Optical Imager for Real-Time Exploitation, or MOIRE — was mostly intended for the country's warfighters, but the project's scope extended into planetary exploration too. MOIRE's prime contractor, Ball Aerospace & Technologies Corp., said at the time that the "game-changing approach" would "dwarf" any telescope projects under development at the time, including JWST.
However, there has been little news after the project prototype was tested in late 2013, and it has apparently not been used as a part of a space mission to date.
Follow Sharmila Kuthunur on Twitter @Sharmilakg. Follow us on Twitter @Spacedotcom and on Facebook.