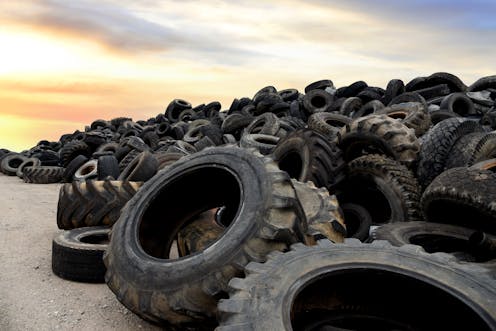
Production of natural rubber has claimed over 4 million hectares of forest in south-east Asia since 1993 according to a recent study. This destruction of tropical forest for rubber plantations is thought to be two to three times greater than previous estimates.
Natural rubber is vital to tyre production since it is stronger, more wear-resistant and more flexible than synthetic rubber. Multiple blends of natural and synthetic rubber are used for making different parts of a tyre.
If more of these tyres were recycled, it would reduce how much oil, energy and forest is consumed to make rubber-based products. Recycling tyres also means less waste accumulating in landfill or being burned.
Yet, most rubber products contain little or no recycled material. A 2021 paper claimed that, globally, less than 2% of rubber products are recycled or reused. So what’s stopping us?
Many materials can be melted and reset in new forms once they have been separated and cleaned. Not rubber. To make tyres and other products, rubber must be chemically treated in a process known as curing or vulcanisation. This produces a material that is resistant to chemicals and heat – and difficult to recycle.
But that could change thanks to a new recycling process my colleagues and I have developed.
A tough problem
Heated rubber will burn rather than melt, releasing lots of energy. In fact, rubber contains more energy per gram than coal. That’s why most waste tyres from Europe are burned for energy.
Burning only recovers 37% of the energy embedded in rubber, and generates toxic fumes. That’s why it’s better to recycle rubber, recovering more of its material value and limiting its pollution.
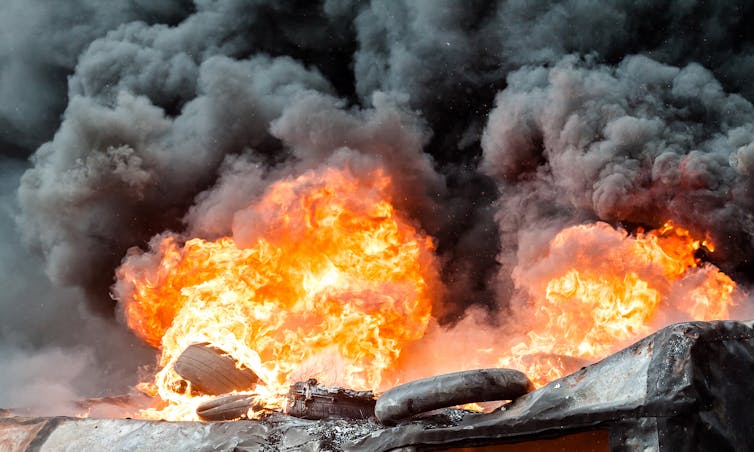
Several companies have recycling technologies which can break down waste rubber. Continental signed an agreement with one company to supply recycled rubber which claims to reduce CO₂ emissions by 90% compared with using the original material (known as virgin rubber).
However, raw recycled rubber can typically only be used in concentrations of up to 25% before the new product has inferior properties. Fortunately, my colleagues and I recently made a material composed of 70% recycled rubber that matched the stiffness of natural rubber.
How do we recycle rubber?
Recycling rubber requires breaking chemical bonds introduced by “curing” without damaging the bulk material.
I like to think of rubber like the mess of cables behind my TV, but on a microscopic scale. If I pull on one of the cables, there is some flexibility: it might snag on other cables, but I can probably free it.
Curing rubber clips those cables together. You can’t free them without either removing the clips or applying more force. In recycling, you have to be careful to break the clips without breaking the cables. The good news is that the clips are weaker than the cables, you just need a way to target them.
Early attempts at recycling rubber in the 1980s weren’t very good at doing this and broke clips and cables somewhat indiscriminately. Recycling rubber in this way means it cannot compete with virgin rubber.
As a result, recycled rubber (in the form of ground tyre rubber or “crumb rubber”) became a low-value material used as filler for artificial turf (those horrible bits that get in your boots if you play on older pitches).
There is already enough low-quality rubber to meet demand. Higher quality recycled rubber is needed to make tyres and seals which have a much greater value in the global market and so could incentivise more rubber recycling worldwide.
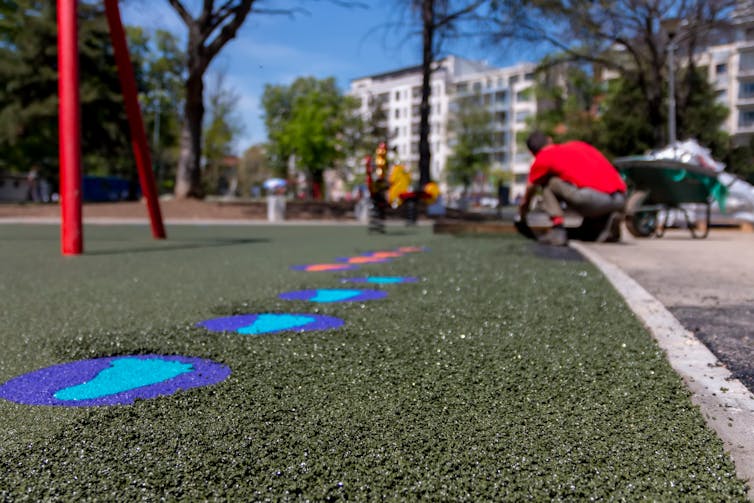
At the University of Bradford, we selectively broke down rubber using a technology developed by collaborators at Sichuan University in China over the past 30 years that shears away the “clips” and leaves the “cables”, producing a kind of powder that could be used to make new rubber products. By keeping the cables intact, the powder more closely matches the properties of virgin rubber.
A circular solution
Ultimately, the amount of virgin rubber that can be replaced by these new recycling methods will depend upon manufacturers, and turning the powder into products will require further work. Tyres contain a complex mix of synthetic and natural rubber, fillers, processing oils and other chemical additives.
Similar to plastic recycling, it’s hard to tell apart and separate different types of rubber before recycling. We found a huge range of rubber and metal impurities in rubber waste sent to recycling facilities in China.
Tyre manufacturers have set targets for increasing the recycled rubber content of their products. Figuring out the best way to blend recycled rubber with virgin rubber to match the quality of existing products will require their input.
In future, with sufficient funding, my colleagues and I hope to study what happens to the chemistry of rubber as it is recycled. This could encourage more manufacturers to trust and accept recycled rubber in their products.
Today, defunct tyres are still treated as waste and cost money to dispose of. But if recycled tyres can be used in the making of high-value products, they will finally be seen as a valuable resource.
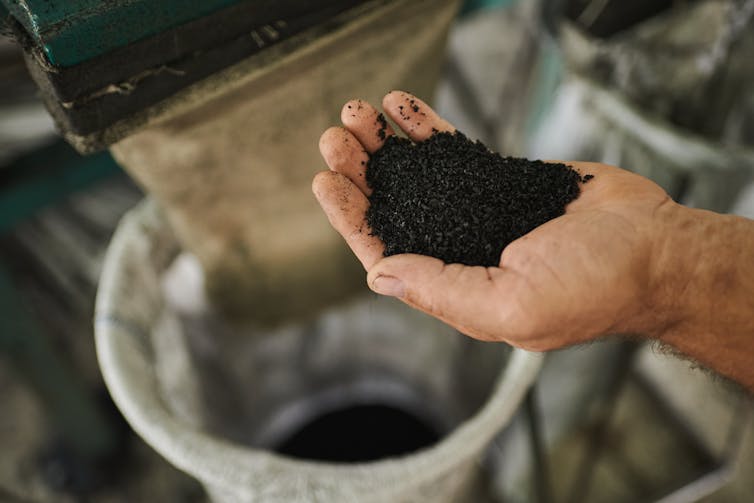
An increase in the material value of waste tyres would prevent their illegal storage, which can lead to toxic fires. More uses for recycled tyres could also help prevent the export of waste tyres to developing countries where they are burned.
Further investment could help make the circular economy for tyres a reality, giving new life to the 1.5 billion wasted every year.
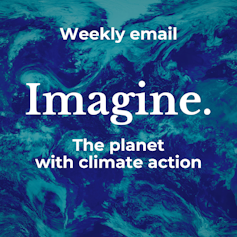
Don’t have time to read about climate change as much as you’d like?
Get a weekly roundup in your inbox instead. Every Wednesday, The Conversation’s environment editor writes Imagine, a short email that goes a little deeper into just one climate issue. Join the 30,000+ readers who’ve subscribed so far.

James Robert Innes received funding from the Engineering and Physical Sciences Research Council (EPSRC).
This article was originally published on The Conversation. Read the original article.