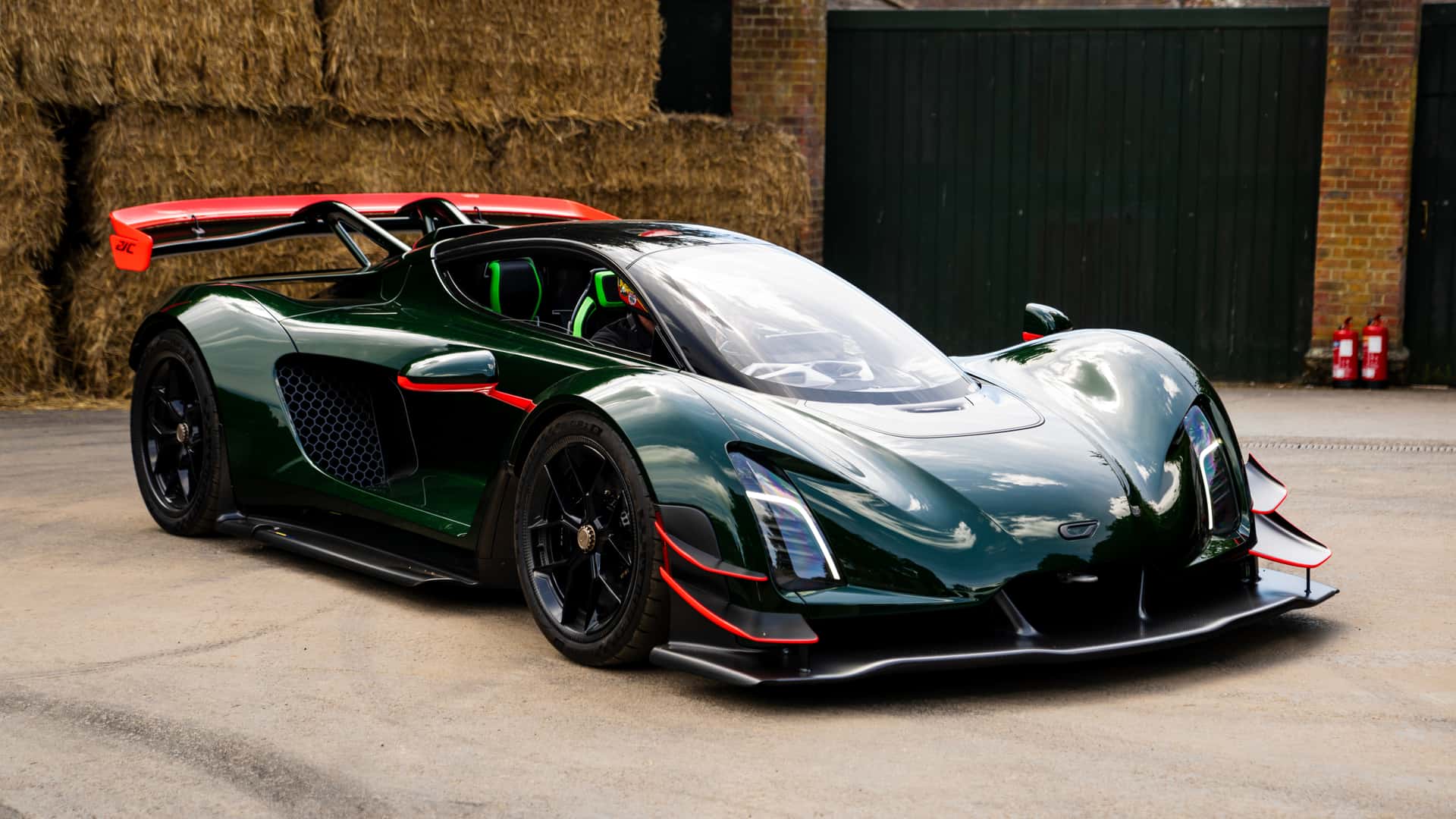
To stand at the back of the Czinger 21C, rear clamshell open, is to understand that this is like no other hypercar. There are bits that look familiar, yet for every one of those, there’s seemingly two more that look alien. That is, of course, by design.
Czinger is the automotive offshoot of Divergent, a Southern California firm specializing in a unique approach to additive manufacturing. Ran by father-son duo Kevin and Lukas Czinger, Divergent has its own production method, the Divergent Adaptive Production System (DAPS). Essentially, you plug in a set of parameters for a part into Divergent’s ultra-powerful computer system, and through AI iteration, the part is designed with the minimum material required to hit the required parameters. Then the part is 3D printed on Divergent-designed machines with unique alloys devised by the system.

“The idea was to start with a clean sheet of paper, and the one thing we know we have right now is growing computing power,” Kevin Czinger tells Motor1. “So you can fully simulate all of the load cases plus all of the manufacturing and all of the assembly.”
With that growing computer power, Divergent can “build a full-model simulation generating the minimal amount of material and energy that go into a structure while meeting all of the linear and nonlinear requirements—everything from stiffness to durability to crash plus optimizing manufacturing and optimizing assembly. All done as one total model simulation,” Czinger says.
The result, in Czinger’s view, is something that more resembles the natural process of evolution. Albeit evolution that happens within hours inside a computer, not over eons.

“Go out into your garden and go look at that insect, look at that animal, that squirrel, look at any flora, any plant, you’re like ‘Wow, it’s incredibly adapted,” Czinger says. “Same thing here. Form follows function right? Like obviously taking a single gauge of steel and stamping it: Is that form following function? No. It's human beings crudely doing what these things are out there.”
“This is literally, within the design space, simulating what evolution is,” he continues. “Adding, subtracting material against environmental requirements, perfectly optimizing. Because out there in nature, material and energy are being fought after. With this simulation, using supercomputing and machine learning, you’re fighting for the same thing. And then form follows function.”
One of the more illustrative parts of the 21C is what Czinger calls the “BrakeNode,” which combines rear suspension, upright, and brake caliper into one unit.


“All of the thermal management, all of the stiffness, all of the structure, all of the simulation is being modeled as this is being generated,” Czinger says. “So you get better thermal management by incorporating it throughout the structure… same thing with hydraulics.”
Czinger tells Motor1 that the BrakeNode has about 40 percent less mass than a system with a traditional fixed brake caliper, but 30 percent more stiffness. Plus, better thermal management.
It’s got a lot of other car companies interested. Divergent will manufacture suspension components for the new Bugatti Tourbillon, and recently began a partnership with McLaren and Mercedes-AMG. Czinger told us more automotive partnerships are soon to be announced, and that’s in addition to Divergent’s existing work with Aston Martin, in aerospace, and defense.

Of course, designing parts is one thing. Making them is a different matter.
“To print at this speed, with this quality, you have to design your own materials, your own printers, each in a feedback loop where you're simulating as to what you're going to build,” Czinger says.
The mind boggles at the complexity. Computers define the parts themselves and also define the materials they’re made of, and the tools you use to make them.
“That microstructure relates to material elements that are being generated by a machine-learning based material system, what the microstructure is, what the parameters with which it’s being printed,” Czinger says. “If you were to take the tiniest piece of microstructure and look at what it actually is, you fall down a light-years deep hole of engineering.”
As a kid in Cleveland, Czinger read about John von Neumann, the programming pioneer, and his theory of self-replicating machines—the robot that makes the robot. He realized around a decade ago that the computing power to make the self-replicating machine was available.
“I was like, shit… finally, that massive amount of data processing to do model simulation here, we have it.”
“Then if [you] don’t give an F and are ready to do stuff, you sit down and go ‘I’m going to create a company.’ Boom,” he says.