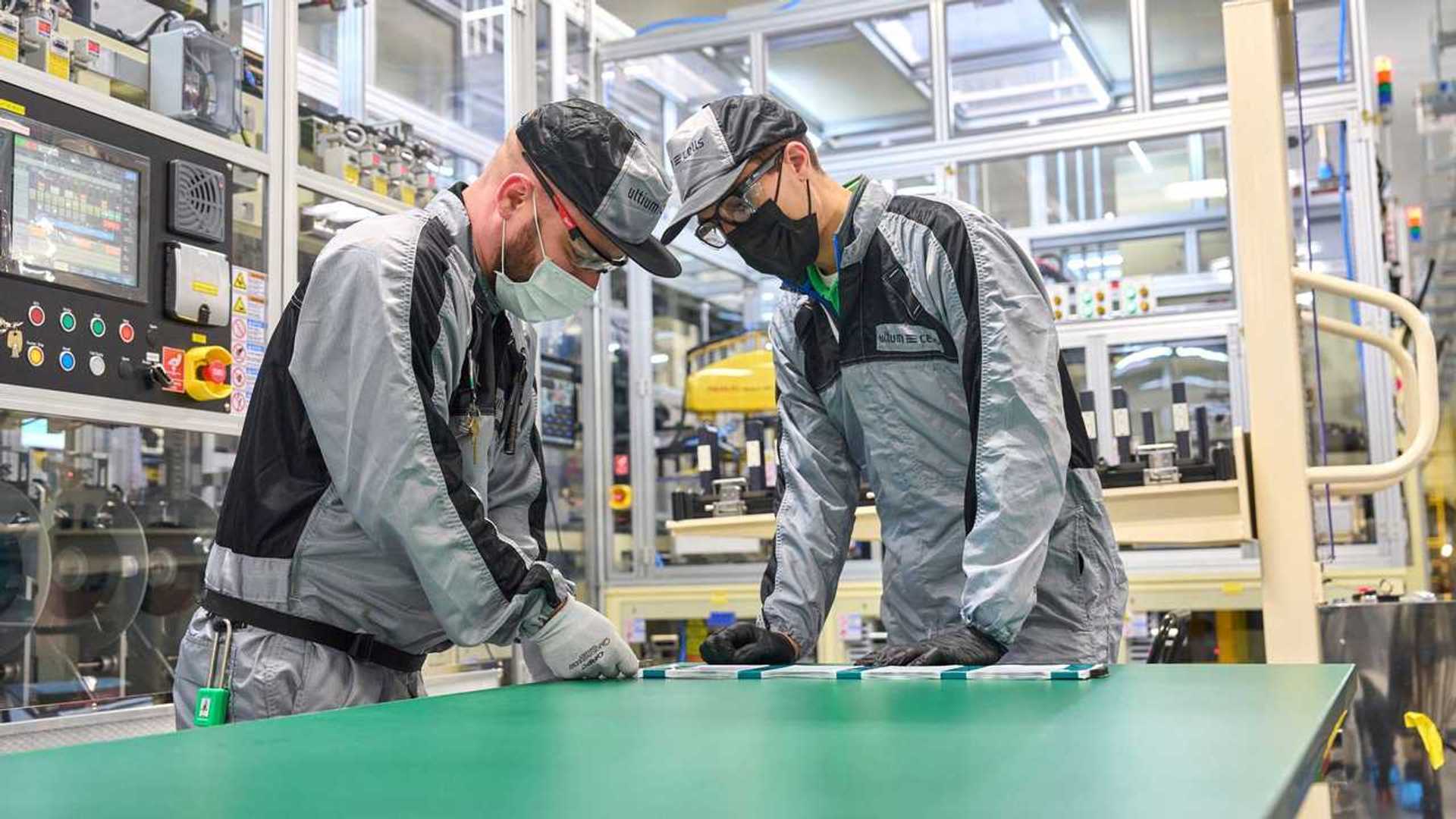
The lithium-ion battery is often considered the most expensive component in an EV. However, its prices have fallen at a remarkable rate over the past 10 years.
In 2013, the average price of a lithium-ion battery was $780 per kilowatt-hour, according to the Bloomberg New Energy Foundation (BNEF). Fast forward by a decade, and the average battery cost is $139/kWh, which BNEF says is a record low—12 percent lower than prices in 2022. This decline can be attributed partly to the expanded production capacity and the decreasing costs of raw materials and components.
The idea seems straightforward: cheaper batteries should mean more affordable EVs for consumers. But the reality is a bit more intricate. Some battery manufacturers have faced lower factory usage, and the growth in EV demand hasn't quite met the ambitious expectations of several carmakers. In fact, battery prices actually shot up in 2022 for the first time in several years, increasing from $150/kWh to $161/kWh, before falling again this year.
"Lowering battery prices has been key in making EVs more affordable, but the lower prices do not pass on to EV costs immediately. Automakers with larger volumes tend to get lower battery prices," Evelina Stoikou, energy storage senior associate at BNEF, told InsideEVs. "Different automakers will pass on lower costs to customers in different ways. Many of them are still working on scaling up in-house battery manufacturing which requires large investments," Stoikou added.
The mass production of EVs hasn't reached a level where the benefits of reduced battery costs can be fully reflected in the final price—Tesla being an exception. As Stoikou indicated, automakers might not always pass on the cost savings to consumers. We already know that OEMs are losing a significant amount of money on EVs, and they might be aiming to cut those losses where they can. One could also argue that cheaper batteries are probably not enough to offset the capital-intensive EV production and associated costs.
For instance, General Motors has pushed back the launch of the Chevy Equinox EV, Silverado EV, and GMC Sierra EV citing challenging market conditions and the “need for engineering upgrades.” Its Ultium Cell plant in Tennessee, part of a joint venture with LG Chem, is also delayed until next year. Ford has also announced delays at the BlueOval SK battery plant in Hardin County, Kentucky, citing slower-than-expected EV adoption.
However, it appears that things are headed in the right direction. “It is another year where battery prices closely followed raw material prices. In the many years that we’ve been doing this survey, falling prices have been driven by scale learnings and technological innovation, but that dynamic has changed,” said Stoikou. “The drop in prices this year was attributed to significant growth in production capacity across the value chain in combination with weaker-than-expected demand,” she added.
One study found that North America was now the fastest-growing planned battery cell manufacturing hub in the world, an effort fueled in part by incentives and provisions from the Inflation Reduction Act. The Biden administration recently announced another $3.5 billion for the domestic production of advanced batteries and battery minerals across the country to reduce reliance on China. Moreover, at least 10 new battery plants are under construction stateside, and more are on their way.
One thing is clear, it's a steep learning curve here for carmakers and that's why it’s safe to assume that it could take a few more years—hard to predict how many—before consumers can reap the advantages of falling battery prices.