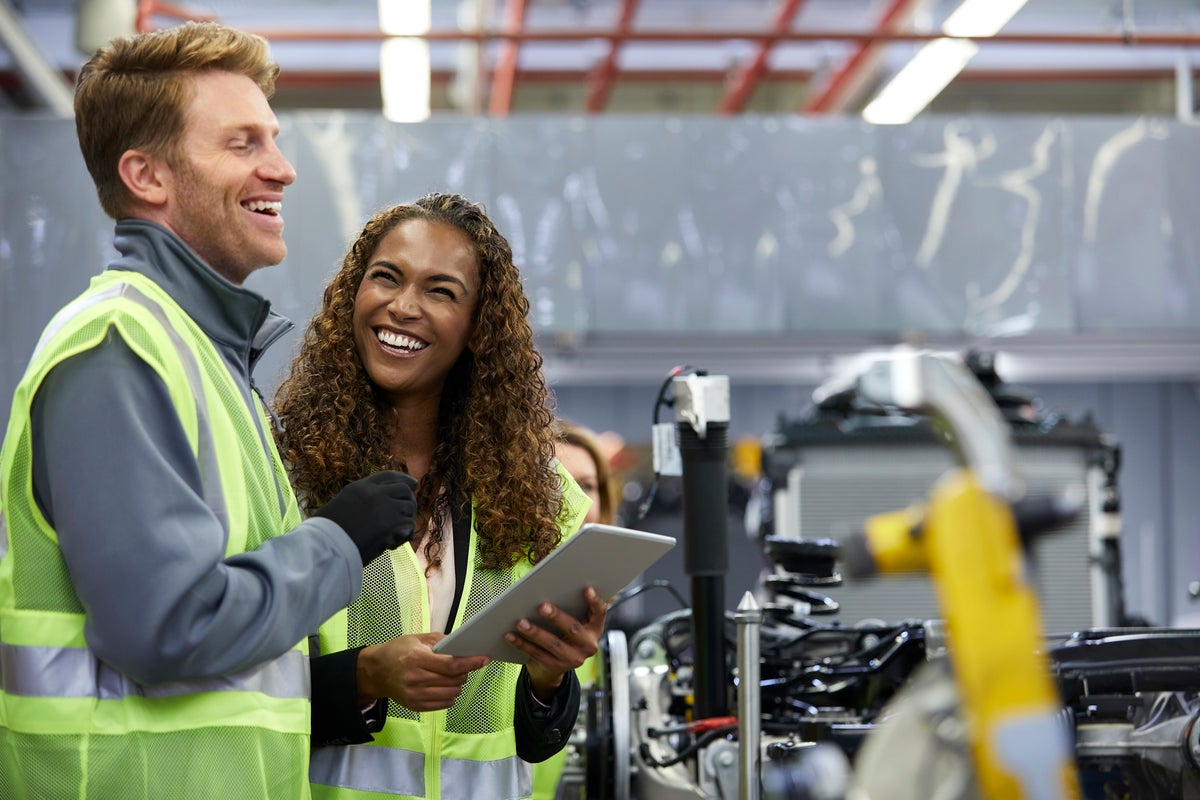
Schneider Electric is a Business Reporter client.
One of the UK and Ireland’s greatest historic strengths in industry has always been the ability to sweat assets. More than a strength, it is perhaps a trait – an engineering mentality – that we tend to prefer to fix things and work around problems, rather than rip-and-replace equipment and technology. In many ways it has served us very well – the UK remains in the top ten largest manufacturing nations of the world. I believe though, that if this mentality hasn’t already started to hold us back in the brave new world of industry, it soon will.
I also believe, from what I see first-hand in the UK and Ireland, that the tide is turning, and we are on the brink of un-stoppering the huge productivity and efficiency potential that is ready to be exploited across our industrial landscape. It’s one key element of a shifting mindset that I believe is crucial to achieving success in the modern digital transformation era. The UK and Ireland have the infrastructure, the talent pools, the creativity, and the ingenuity to benefit massively from proven productivity and efficiency boosts associated with digitalisation, and it’s time to up our game.
It’s also worth mentioning that two of the most widely cited challenges faced by industry here, namely, the skills gap and the productivity puzzle, are closely related. It’s dangerous to think of digitalisation as a panacea for these well-publicised and broadly recognised ills, but it is the one lever we can pull that can do the most to correct our course.
Digitalisation and skills
Let’s break that down a little further. Two fantastic tools for mitigating the skills gap in industry are directly related to digitalisation. First, we need to make industry more appealing to young people. All young people. We need the best talent to come from diverse backgrounds (gender, culture, disability, neurodiversity, etc) to be successful and to meet the challenges of the modern world. There is a wealth of research that supports this viewpoint, and I’d recommend anyone with doubts to do an internet search around the benefits of diversity in industry.
To attract young people, we need to recognise that they are digital natives, born and raised in the digital era, who expect digital solutions and data to help drive decision making. They expect digitalisation to be baked into their lives in the same way we, as consumers, have come to think of streaming services and home automation as a part of the fabric of daily lives. Moreover, young engineers will have an even greater appetite for the power and potential of data in industry – it is in the engineering psyche to want to push the boundaries of what is possible, and digitalisation is at the cutting edge of industry today.
Second, and of equal importance, the skills gap is seeing a huge amount of domain knowledge and experience retiring from the workforce each year. Digitalisation holds a unique power to retain a very useful slice of knowledge and to help retirees share it with young people in the business through technologies such as extended reality (xR) and associated, data enabled communications tools. This is something we have directly experienced in our own award-winning UK smart factories, where the introduction of augmented reality and digital twin technologies has enabled us to empower decision making on the shop floor and has played a vital role in helping to drive the structural and cultural changes that are central to successful digital transformation.
Digitalisation and productivity
The other “ill”, the productivity puzzle, has a more obvious link to digitalisation, but it does bear considering where the UK, ranked the ninth-biggest manufacturing nation on the planet, sits in terms of robotisation (24th). Despite the rapid growth of robotisation here, we are not yet keeping pace with growth elsewhere, let alone making comparative progress. This, to me, suggests a huge existing potential for the UK to become much more productive if the digital infrastructure that robotisation and automation required is brought to bear. Put simply, we need to up our digitalisation game.
The how
In the world of digital transformation – the process of digitalising your business to harness the power of data to transform it for the better – there are many people and organisations who will tell you what you need to do. Most of them, most of the time, are right, for two reasons.
First, it is vital to the future of your business to digitalise and those telling you how (technology vendors such as us at Schneider Electric, industry bodies, trade associations, governments and so on) are likely to be in a position to help in some way. Second because there’s no single magic-bullet method, just as there are many ways to be “right”.
In fact, the best way for your company is as unique as your business. Your journey will likely need input from various suppliers of IT, software, hardware and machinery and your systems integrator, as well as a lot of buy-in from inside your organisation and, potentially, your supply chain.
It’s all quite simple, but it is far from easy. We know, because digitalisation is a journey we are on with our own manufacturing sites and we live the change first hand. We meet and overcome the hurdles for ourselves and use what we’ve learned, together with what we learn helping our customers, to shape our offering, industrial automation technology and software, right through to opportunity, training and talent acquisition.
UK and Ireland industrial companies keen to survive and thrive must digitalise. Mend and make-do won’t cut it. The tide is turning, the opportunity is immense and the time is now. I find that very exciting.
For more information please visit www.se.com.