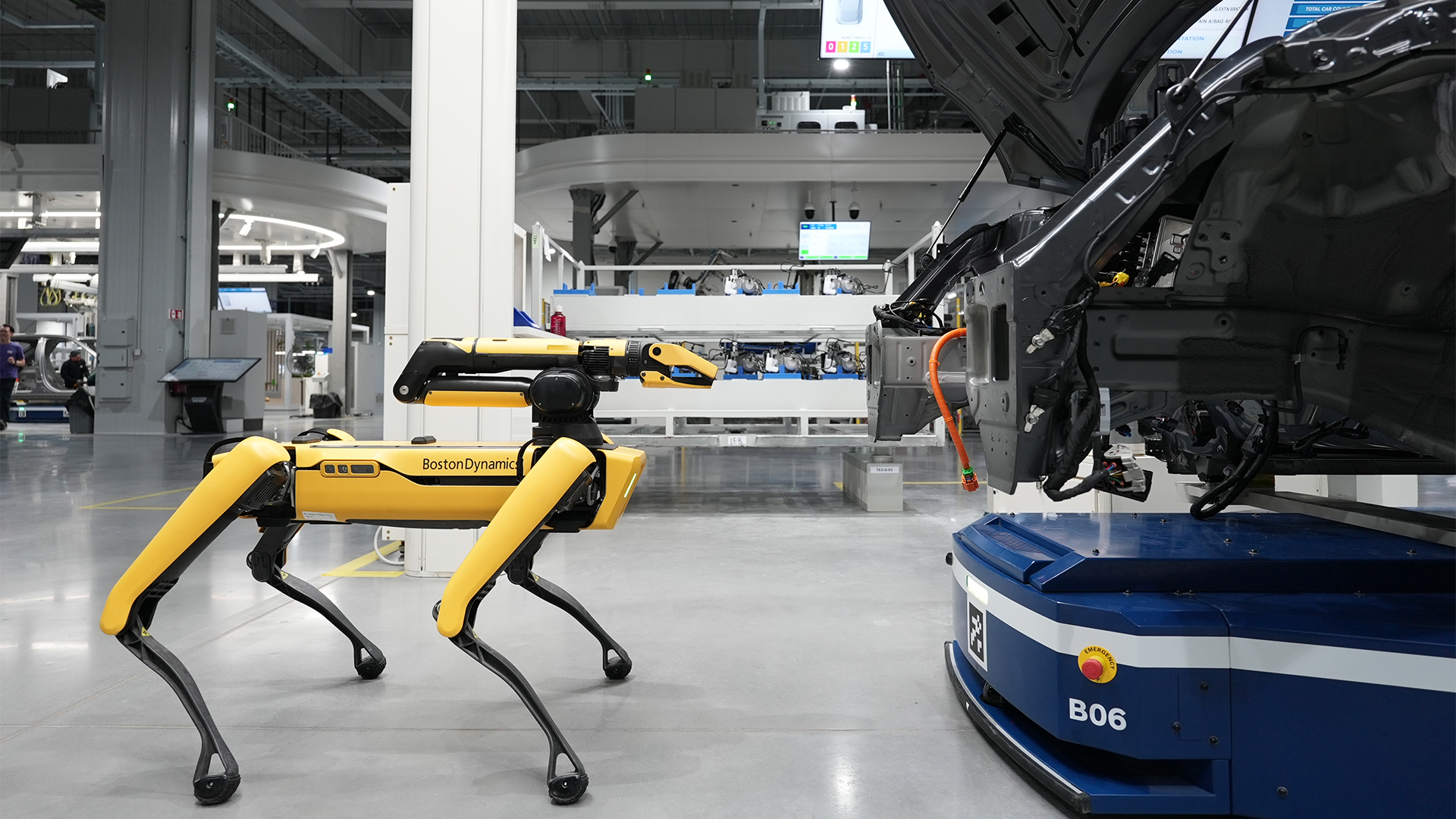
The factory floor is eerily quiet, the surface underfoot is polished to within an inch of its life and small robotic platforms autonomously scoot around delivering parts to production cells. It is here where factory workers wearing high-tech exoskeletons are working on an individual Hyundai Ioniq 5.
One employee, supported by a robotic pack that allows him to work above head height for extended periods of time, steps away from his station to allow a robotic dog to enter the scene. Spot, the agile robotic pooch from Boston Dynamics (and your Black Mirror-induced nightmares), jogs into the workspace, extends its telescopic neck and begins scanning the floor of the Ioniq 5 for imperfections.
Harnessing the power of the latest camera technology, a suite of sensors and powerful AI, Spot the robodog then proceeds to dissect the workmanship. Only when it is happy there is nothing amiss, does he return to his charging dock for a lie-down. Welcome to the Hyundai Motor Group Innovation Center Singapore (or HMGICS, for short) - the factory of the future.
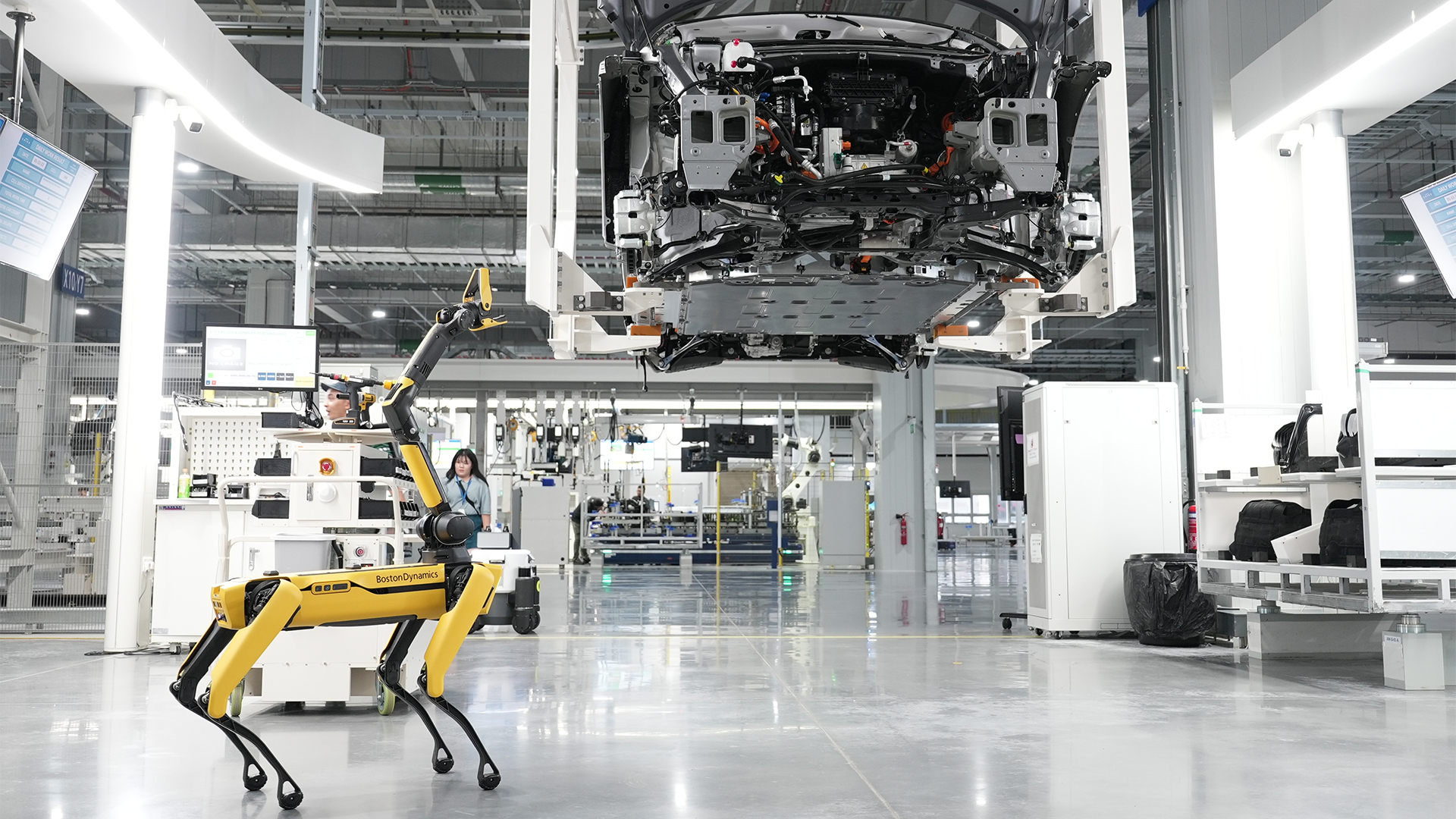
Recently opened, HMGICS plans to completely shake up the way cars, and other future forms of transport, are manufactured. It is nestled deep within the heart of Singapore’s start-up region and the facility spans seven floors, complete with a vertical farm in the lobby.
Here, a giant glass room houses several robots that tend, day and night, to various saplings, nurturing seeds and turning them into edible salad leaves and herbs for use in the on-site restaurant.
Again, Black Mirror instantly comes to mind, but considering 90 per cent of Singapore's food is imported, this could be the only sustainable answer.
"This isn’t like a traditional production plant," explains VP and head of smart factory technology, Alpesh Patel.
"We plan to produce around 70 cars a day here, so it's no mass production line, but that’s not the point. The speed at which we can react to customer personalisation demands and cater to bespoke project requirements is like little else," he adds.
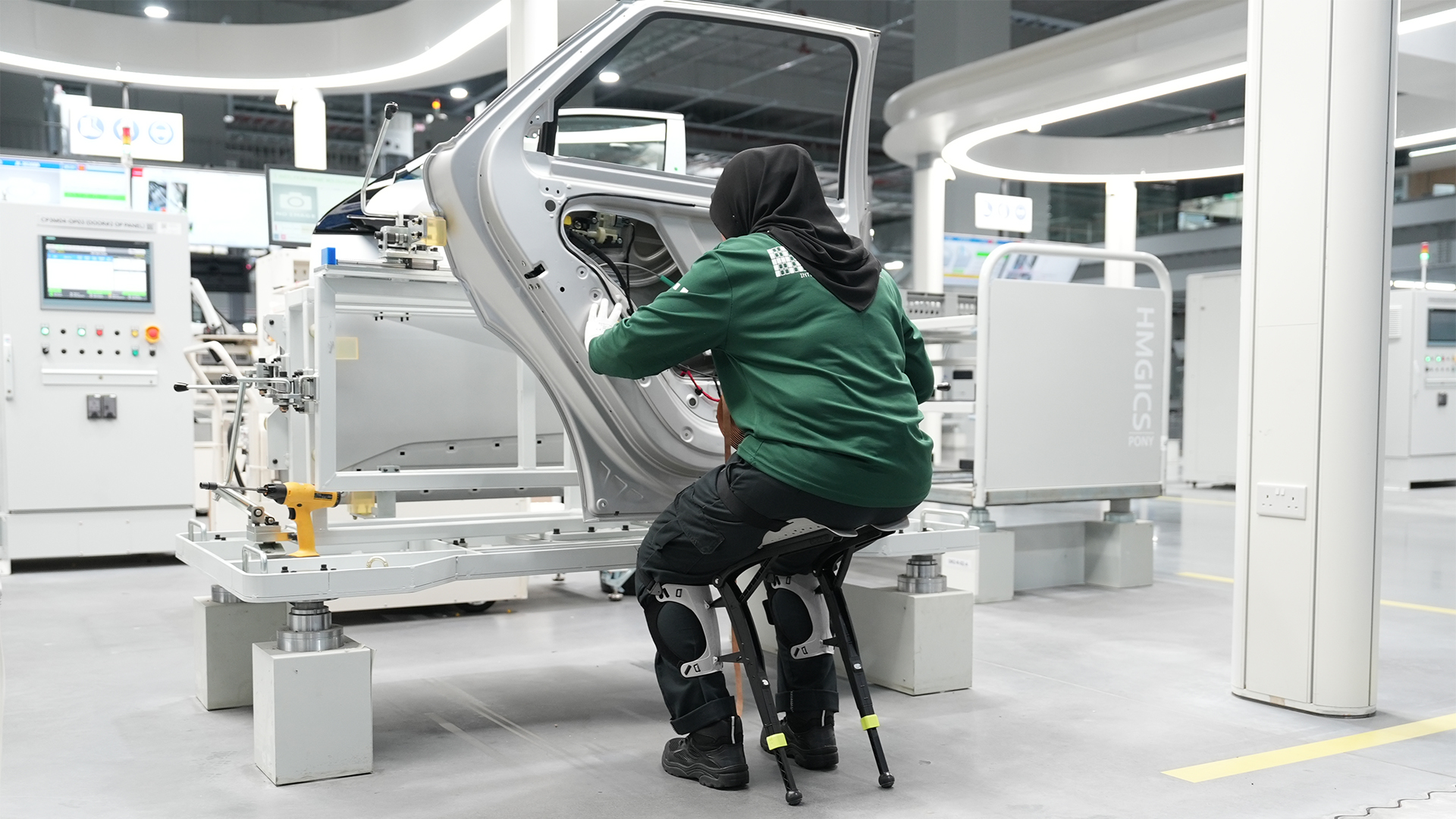
With approximately 50 per cent of all tasks carried out by some 200 robots, HMGICS only currently employs some 29 factory floor workers, most of which are highly skilled engineers that work on one vehicle at a time. The bulk of the assembly is quickly and efficiently handled by robots.
Compare that to the 3,134 employees that pump out more than 350,000 cars every year at Hyundai’s sprawling manufacturing plant in the Czech Republic, and it seems small fry. However, there's more to the innovation centre than pure output figures.
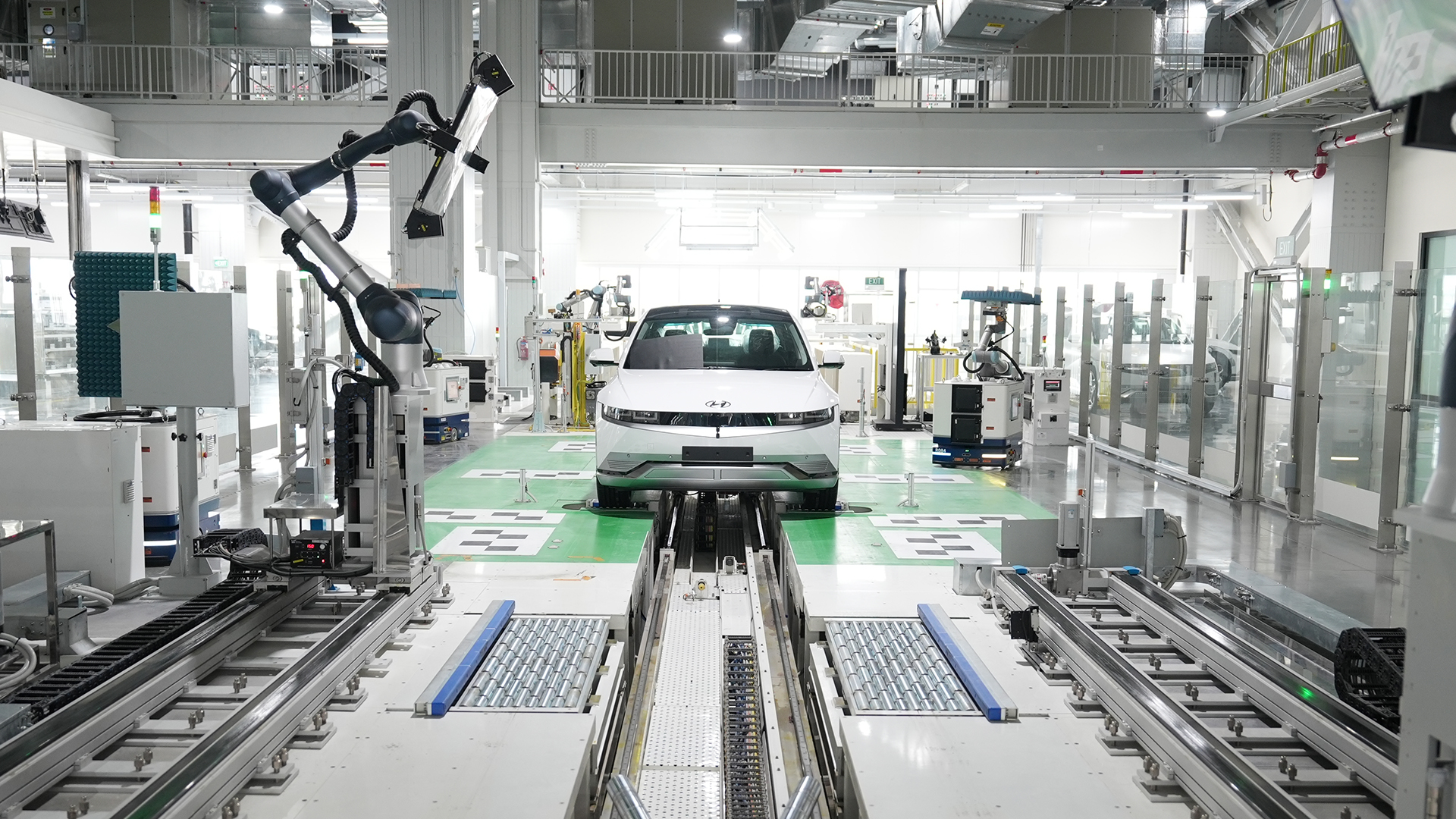
Customer demands
In short, this small but highly automated workforce is able to quickly react to a customer's needs and can implement changes to any particular project without the need for masses of re-tooling and downtime.
According to Patel, customers will be able to order a Hyundai vehicle via a smartphone app "from the comfort of their own home" or they configure their new ride via a flashy Brand Experience area within the building.
From here, they can select a colour, choose trim details, apply various wheels and even inject a little personality with a customisable centrepiece, such as insignias in the headrests or a 3D-printed dashboard. From this point, Patel says it only takes a matter of hours for the finished vehicle to be ready, thanks to the innovative use of cell manufacturing methods and Spot the robotic overlord's penchant for rigorous quality control.
Once the vehicle is finished, customers can go for a test-drive on the facility’s 620-meter rooftop Skytrack, or gorge on vertically-farmed salads in the dining area.
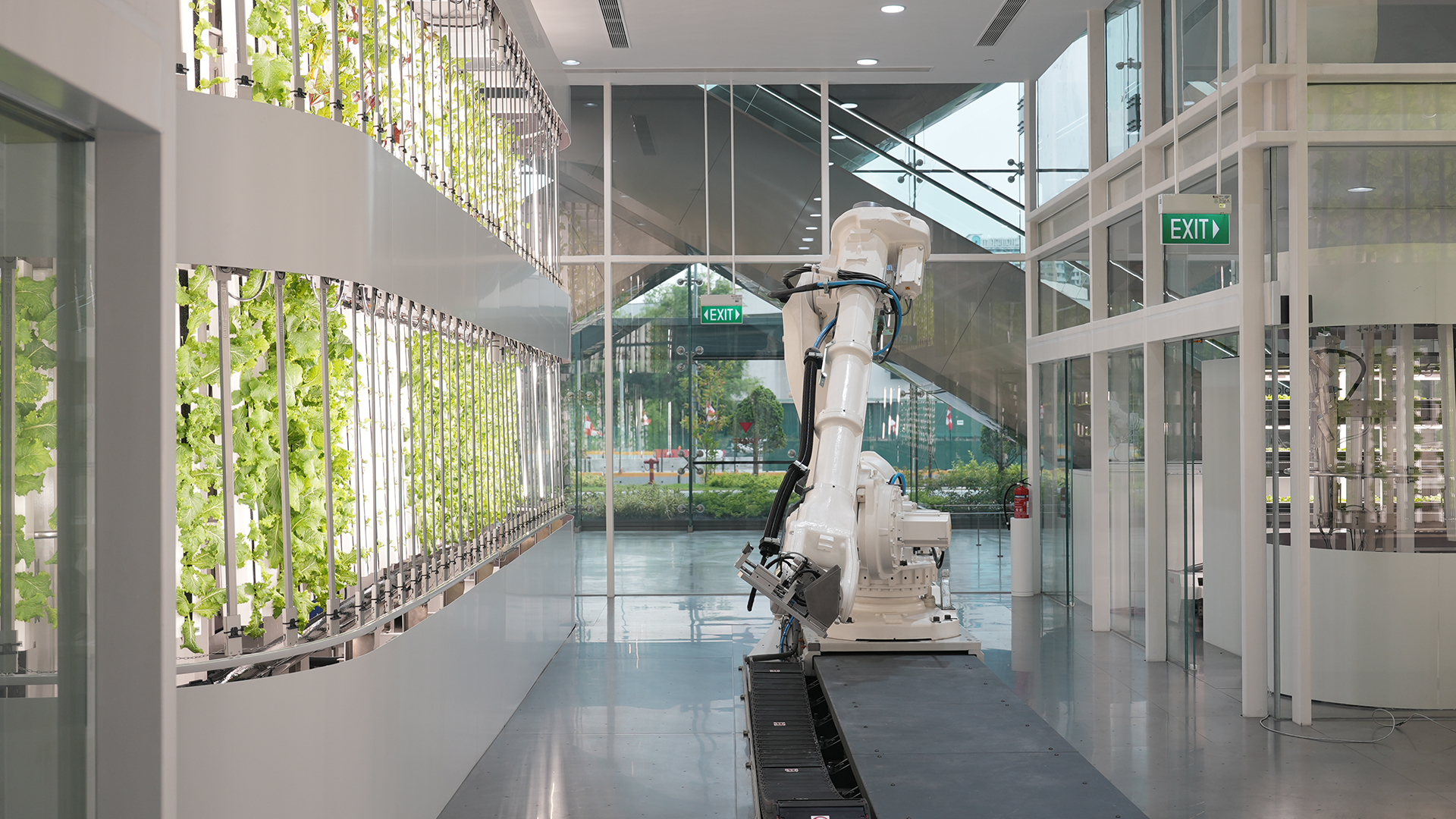
A factory of the future
Not simply a facility to wow well-heeled customers, HMGICS will be integral to the design and build of Purpose Built Vehicles (PBVs) in the future. "We want to invite future mobility providers in and allow them to realise their ideas," Patel explains.
"This facility allows us to be highly reactive, creating vehicles for specific requirements, rather than just the individual’s desires."
In order to run such a highly automated production process, the HMGICS features a Digital Command Centre, where a handful of highly skilled operatives work in a NASA command centre-esque environment, able to instantly pull up a wealth of smart factory data, checking in on efficiency levels of each production cell, and predicting when a robot requires servicing or a part needs to be ordered long before the need arises.
What’s more, Hyundai has developed a digital twin of the factory floor (or meta factory) that allows it to run simulations for when new production process requirements arise.
Currently, the operatives in the command centre have to use numerous pieces of software to implement changes on the factory floor, but Patel says in the coming years, this will be possible simply by interacting with the digital twin, while he expects AI to take care of the majority of day-to-day tasks.
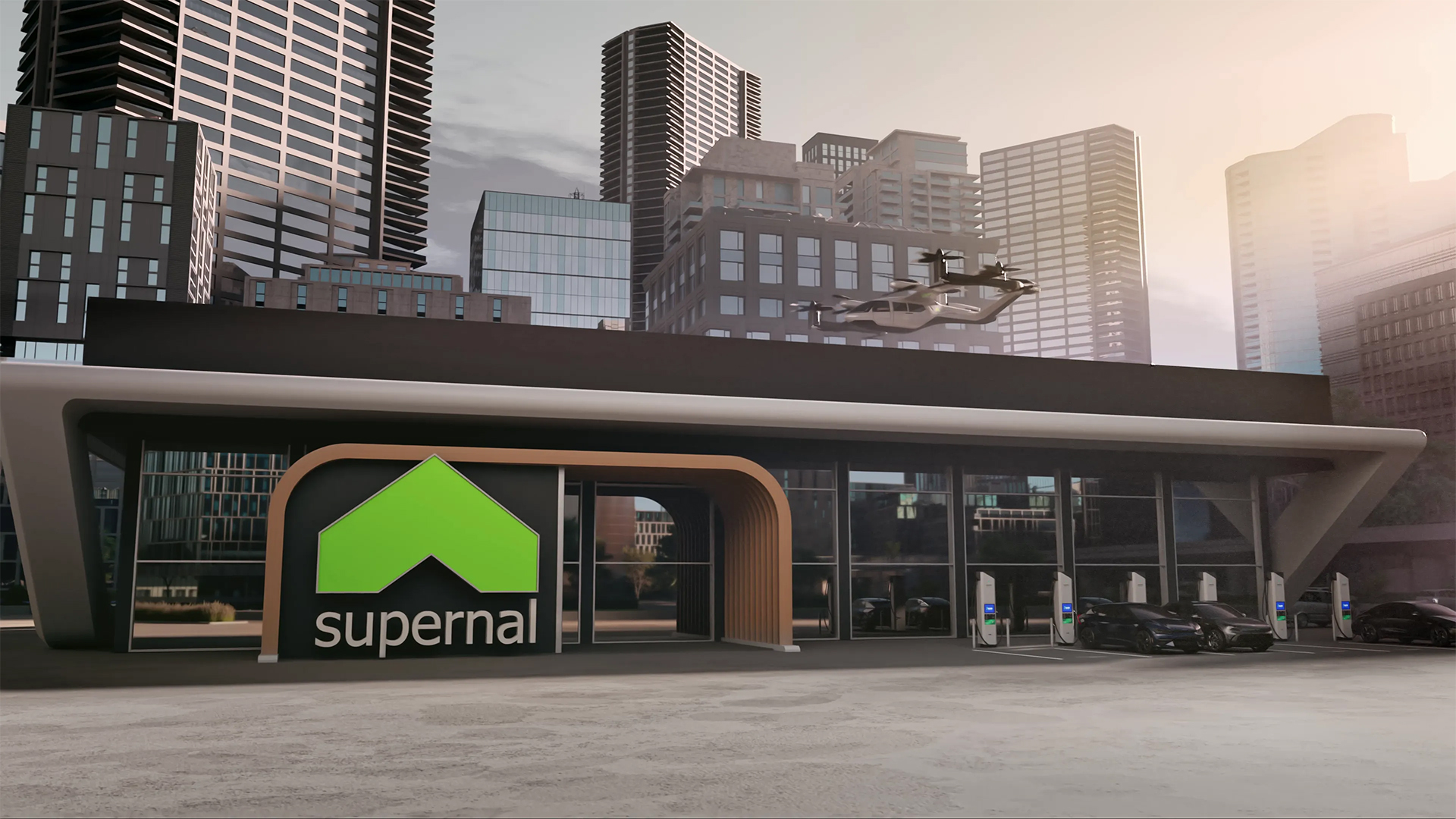
Cleared for take-off
Currently, Hyundai says it has the capacity to produce around 30,000 EVs per year, with HGMICS tasked with the production of Ioniq 5, Ioniq 6 and an Ioniq 5-based robo-taxi for its autonomous driving partners Motional.
But, the near future could look very different, as Patel says the highly flexible manufacturing process can be configured to produce pretty much anything within reason.
Part of this drive towards creating more sustainable transport solutions and PBVs for the city of the future lies in Hyundai’s partnership with Advanced Air Mobility provider Supernal, which is currently working in the field of electric vertical take-off and landing (eVTOL) craft.
During discussions at the Innovation Centre, Jaiwon Shin, the man in charge of Urban Air Mobility at Hyundai Motor Group, says HGMICS will be "integral" to the production of advanced air mobility in the future, stating that we could start to see aircraft operational as early as 2028.
Currently, there's no eVTOL craft landing pad on the roof of Hyundai's Innovation Centre, but it won't be long before staff are taking to the skies of Singapore in order to escape the traffic... or the all-seeing eye of Spot the robotic quality control dog.