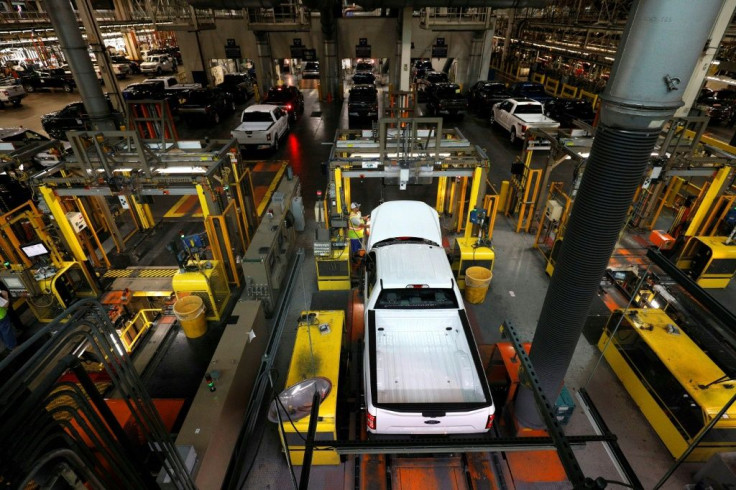
American manufacturing is staging a comeback. More and more companies are building new facilities stateside -- or expanding existing ones.
The biggest headwind? Companies are struggling to fill key positions on -- and off -- the factory floor.
Fortunately, there are three simple ways manufacturers can bring the talent they need on board. First, they need to sell potential workers on their enterprises while they're still in school and thinking about what comes next. Second, they need to make opportunity for advancement a priority. And third, they need to design a workplace that appeals to blue-collar and white-collar workers alike.
America is now home to nearly 400,000 manufacturing facilities, an increase of 11% since 2019. E-commerce, which makes up one-fifth of all retail sales, continues to grow and requires three times more industrial space than brick-and-mortar retail. Sixty-five percent of companies began strategically stockpiling inventory to prevent another supply chain disruption.
All this means that people looking for employment in manufacturing will not want for opportunity.
Deloitte estimates that American manufacturers will have 3.8 million new jobs to fill in the next decade. They're already struggling to fill 1.9 million roles today. The two biggest reasons? A skills gap and a shortage of applicants.
Companies need to evangelize, early and often, about their distinctive cultures and what they can offer their employees. They can do so by dispatching employee-alums to colleges and universities, technical and vocational schools, and business schools to tout their compensation packages, opportunities for advancement, and the advantages of the location of their facilities.
Next-level engagement can include partnering with schools and programs that have proven particularly good sources of talent to ensure that students are getting the skills companies need -- from logistics and supply chain management to operation and warehouse management.
Nearly 95% of manufacturers surveyed by Deloitte had at least one such partnership -- 48% with universities and 73% with technical colleges. Around half of respondents to another Deloitte survey said apprenticeships and internships were the best way to attract new talent.
Some things that manufacturers perceive as disadvantages in recruiting talent can actually end up being strengths.
For example, many young people are enticed by the idea of big-city life -- until they encounter the cost of living. Manufacturers in small towns and exurbs can cite their locations as a quality-of-life asset. In the age of next-day delivery and streaming services, many young people find they can access the goods and entertainment they want without enduring the high price of urban housing.
Manufacturers can also tell potential hires they offer faster paths to advancement than other employers. Six in ten workers who left their job in 2021 did so because they couldn't advance. Mastery of skills, enthusiasm, and commitment are often better metrics for promotion than "years of experience."
The current makeup of the manufacturing workforce offers tremendous opportunity for young people today. Manufacturing, transportation, and warehousing rank among the top industries with workers over 55. Nearly 3 million of the 3.8 million jobs needed in U.S. manufacturing will be opening up because their current occupants will be retiring. Young people who want to climb the corporate ladder quickly will have the chance to do so in manufacturing.
In addition, manufacturers should take a close look at potential workers who have opted out of college to avoid student debt. In some cases, such a move might warrant reward from company management -- rather than a penalty for failing to fulfill an unnecessary degree requirement.
Once new hires report to work, companies can offer them a thoughtful workplace design that fosters interaction and keeps them engaged with colleagues.
The days of a cubicle farm overlooking a factory floor are over. Research indicates that training rooms, café areas, and collaborative meeting spaces work great in an industrial office setting to keep employees productive and excited about coming to work.
One large manufacturer in Illinois created a "Main Street" social corridor in the middle of its technology team's office. The company found that employees from all departments sought out the collaborative space, even preferring it to their own desks.
The American manufacturing workforce is on the cusp of a generational turnover. In order to survive for decades to come, firms will need to prioritize recruiting young people, showing them the unique opportunities for advancement that manufacturing offers, and creating workplaces that people want to come to.
Jonathan Webb is director of workplace & healthcare markets at KI, a global furniture manufacturer in Green Bay, Wis.