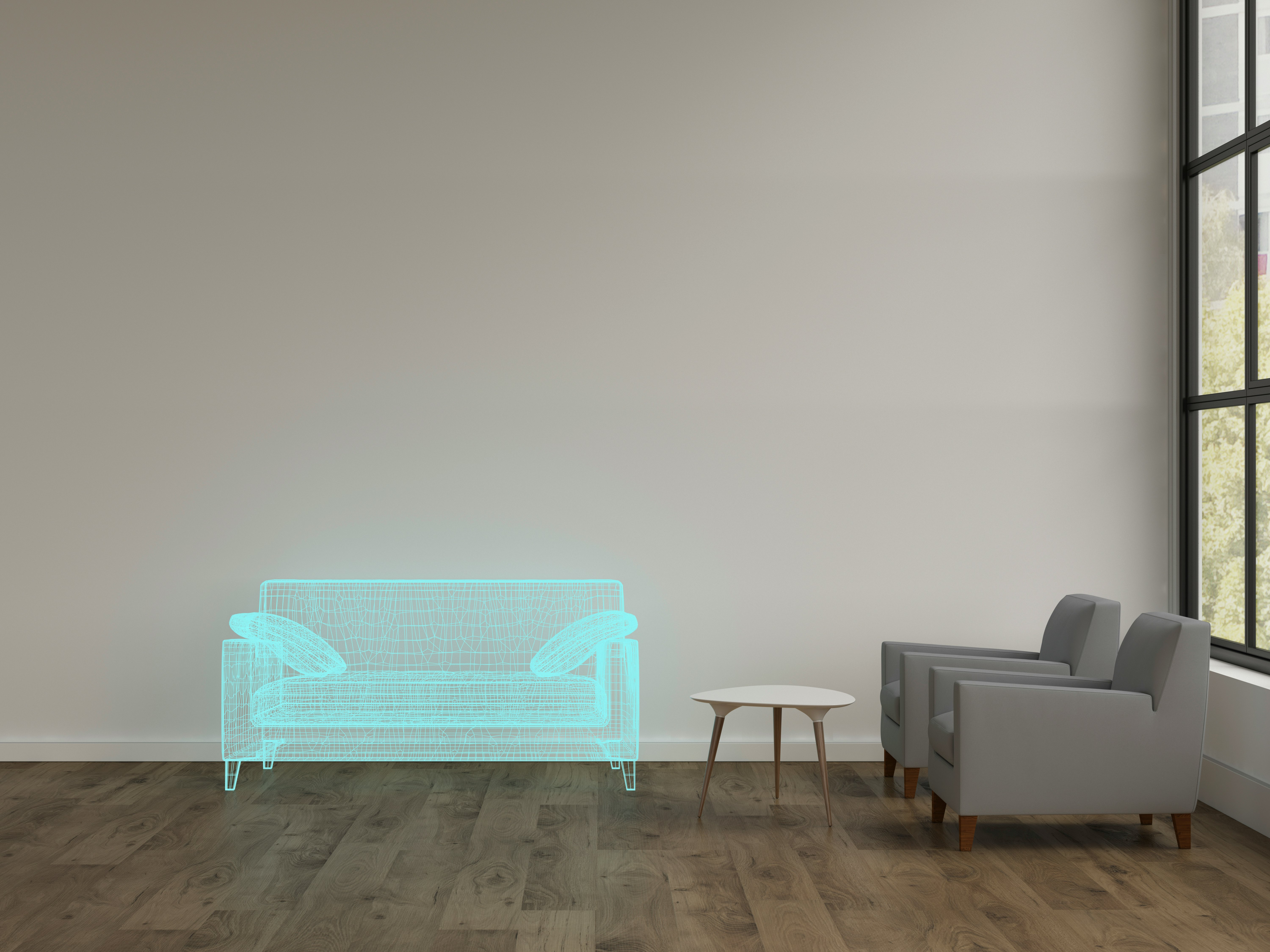
Picture this scenario: You ordered an ornate oak desk online, and when it arrives a few days later you breathlessly rip open your package. The box is lighter than expected, and only contains a flat piece of wood with wet ink that kind of resembles maple fudge. But after the ink dries, the wood miraculously morphs into the item you ordered online, avoiding the need for frustrating, hours-long assembly sessions.
Such a product isn’t possible. Yet. But it’s the goal for Doron Kam, a materials science PhD student at the Hebrew University of Jerusalem in Israel who recently presented his work with colleagues at the fall American Chemical Society meeting. Kam’s proposed printing technique creates wooden objects that don’t require us to saw, carve, or bend them, and can transform on their own thanks to what seems like magic — but in reality, took meticulous planning and a high-tech 3D printer.
The futuristic concept takes advantage of warping, a natural occurrence in wood that’s usually dreaded by designers and homeowners alike. Wood gets wet and dries unevenly, creating some funky shapes, and nobody wants a creaky, sagging floor or oddly curved dresser. But Kam and his colleagues use this phenomenon to their advantage.
What’s new — Kam and his fellow researchers found a way to print flat wood sheets that form 3D shapes when prompted by a certain stimulus, such as a change in pH, temperature, or moisture. They were inspired by the natural bends in warped wood. It may seem interesting in a forest, but warping can ruin human-built items like furniture, flooring, or even wooden structures like a gazebo or cabin.
Unlike in the wild (or a flooded home), the researchers found a way to dictate just how a piece of wood will turn out when wet. They achieved this by adjusting several factors in the printing process, including the printing speed and the precise placement of ink. Eventually, this manufacturing process could create custom pieces of furniture that are easy to ship and require no effort on the customer’s end (besides, well, opening the box).
But the project is intended for more than just tables and chairs, Kam explains. “If we invest enough time and resources, [this method] can produce really interesting and valuable products,” he says. “The way that we’re showing it is just by woodworking.”
The broader aim of Kam’s research: To create the objects of the future, we need to rethink design entirely.
Here’s the background — Kam’s team isn’t the first to propose materials that contort over time. He’s among a growing community of researchers working toward 4D printing, which aims to take its 3D predecessor a step further by manipulating how the objects will change after they’re printed.
This idea challenges the way we’ve approached design for centuries, Kam says. Until recently, he explains, the goal was to create structures that stay the same over time to ensure durability. “What we’re proposing is a bit different … a more responsive material,” Kam says. “It’s changing the concept of engineering.”
These evolving materials reflect the dynamic character of our environment, says Tiffany Cheng, a PhD student who researches bio-inspired 4D printing at the University of Stuttgart in Germany.
“In nature, things are always kind of in flux, always adapting,” she says. “There’s never really a single state of being.”
But the current tools used for 3D printing limit our creativity, Cheng and Kam say, since they’re devised to generate static objects.
Like the team from the Hebrew University of Jerusalem, Cheng looks into printing materials that can transform when introduced to certain stimuli, such as increased moisture or temperature. She says it was “mind-blowing” to learn about responsive design, which opens up countless possibilities for a single item.
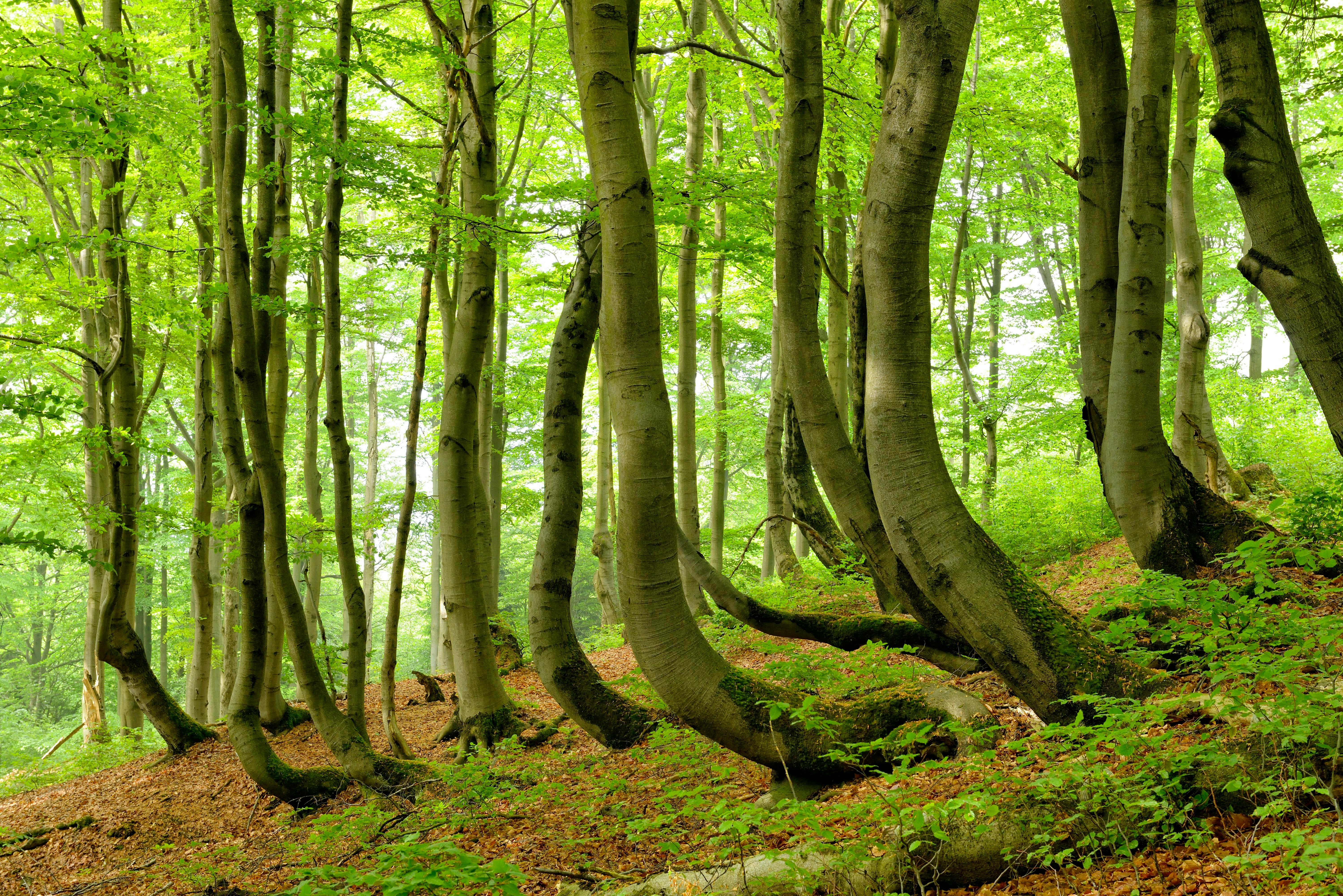
Why it matters — Right now, Kam’s team has only made small prototypes and is still figuring out how to scale them up successfully. After materials scientists like him get the basics down, he says, it’s up to designers to put them to work.
So if they pan out, responsive materials could revolutionize a variety of fields. For example, imagine a cast for a broken arm that settles itself into the proper position, Cheng says, instead of having to visit the doctor every month to have it adjusted. Besides medical applications, she is currently working on a building facade that can adjust its shading depending on factors like outside temperature.
Forward-thinking 4D printing research also prioritizes sustainability. Currently, multi-dimensional printing relies on synthetic materials, including gels and elastomers, that produce mountains of waste.
But eco-friendly ingredients can change that: A few years ago, the Hebrew University team created a water-based ink made of wood-waste microparticles called “wood flour,” which are mixed with binding substances from plants (including nanocrystals made of cellulose, or the main component of a plant’s cell walls). This concoction can even be created with leftover wood, avoiding the need to chop down trees.
Kam sees a future where “you can make your own product, and after a few years you can rebuild it again and again and again,” he says.
What they did — The researchers found that they can lay the wood ink down in certain directions to dictate how it will morph when the material dries. For example, a series of lines that emanate from a central point can dry into a cone-like structure. Stacking also helps achieve more precision: piling up two rectangular layers that have been printed in different orientations can create a helix shape after the ink dries.
They can also adjust the print speed to dictate the object’s final shape. The material shrinks in a direction that is perpendicular to the ink’s wood fibers, and the specific print speed shifts the alignment of the wood fibers. Ultimately, slower printing guarantees a more random alignment of the particles and causes shrinking in all directions, while quicker printing aligns the fibers and can control shrinkage in a specific direction.
What’s next — In the future, Kam and his fellow researchers aim to combine specific shapes, such as saddles, domes, and helices, to produce more complex final objects. Currently, it’s difficult for the wood to dry without cracking due to its brittle texture, so it needs to be placed on a sheet when aired out. They’re also considering how to make the shrinkage reversible.
Both Cheng and Kam also hope to create software that anyone can use to design and print their items of choice, such as a medical technician looking to create a custom splint or even a homeowner with a specific type of desk in mind.
But several hurdles remain. For one, multidimensional printing is currently extremely slow — it can take hours to days to manufacture a single part. Some applications likely demand a quicker timeline, though, particularly in the medical field. And today’s printing materials are fairly limited: You can get pretty creative when manipulating an item in the printer, Cheng says, but a given material can only do so much.
Going forward, it’s up to experts like Cheng and Kam to test these limits. The sooner they can achieve that, the sooner we can say goodbye to indecipherable Ikea instructions.