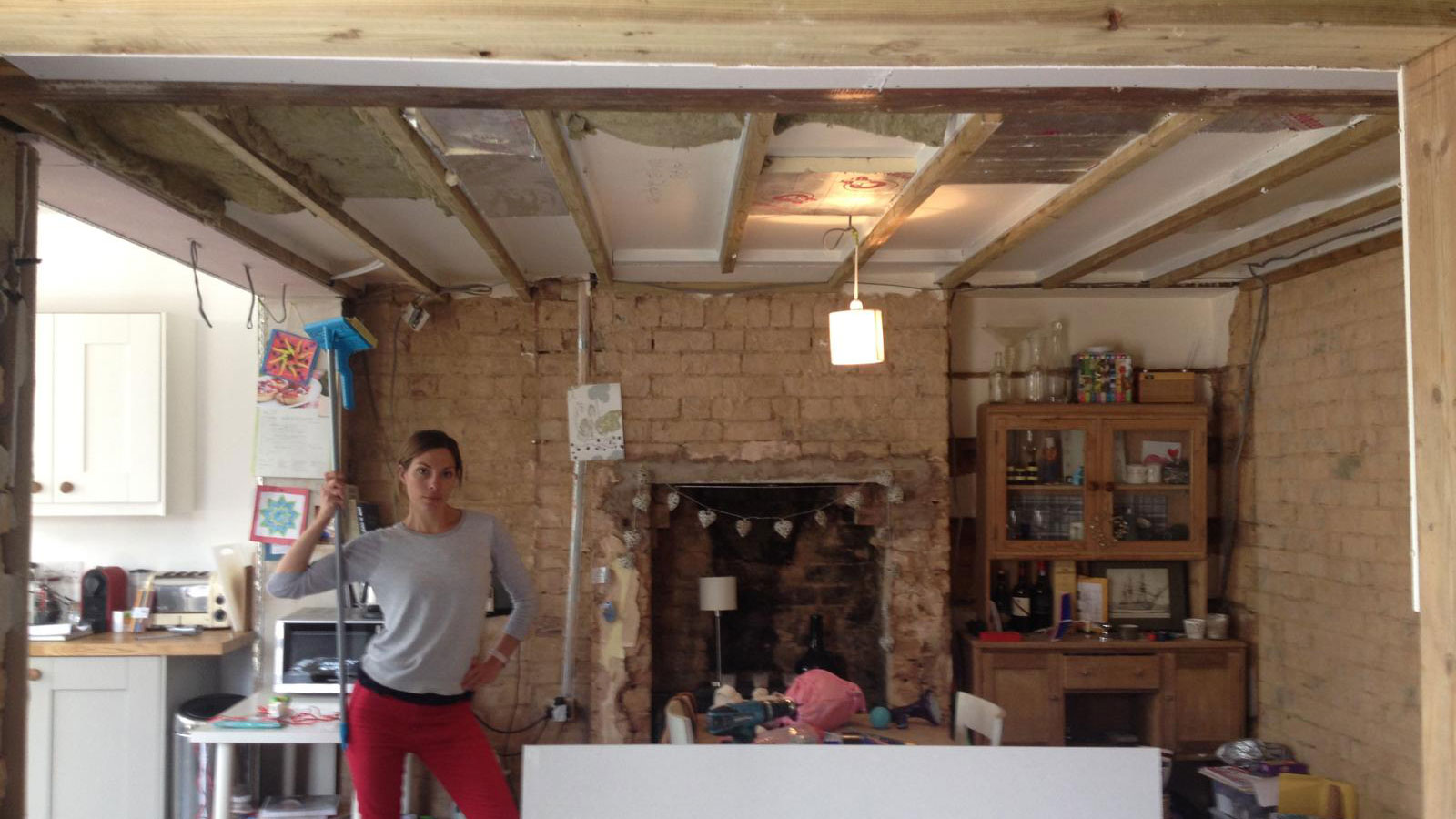
When we purchased our Edwardian cottage we were in something of a desperate situation. We had moved from the cute, but quite compact, Victorian terrace we’d renovated, into a rental. We rushed our decision, thinking that this would be nothing more than a temporary stopgap. Big mistake. We ended up staying in that too-small paper-thin-walled house on a new development.
Both my husband and I grew up in old houses and love the history and character that ‘lived-in’ properties have. We took one look around this cottage that we still call home, built in 1915, and knew it had to be ours.
The only thing was, we were a little limited budget-wise so were keen to save on house renovation costs wherever we could. We had to quite quickly become experts in the field of DIY renovation. I’m here to reveal which jobs were surprisingly easy and that you are probably quite capable of tackling, just like we did.
Easy DIY jobs that will save you money
There are loads of DIY house renovation jobs that are well within the capabilities of most people - we found that the key to success was researching what was involved thoroughly, getting prepared by ensuring we had all the necessary tools and materials to hand, and setting aside enough time for each task. Oh, and lots and lots of measuring - then measuring again!
1. Laying the engineered wood flooring
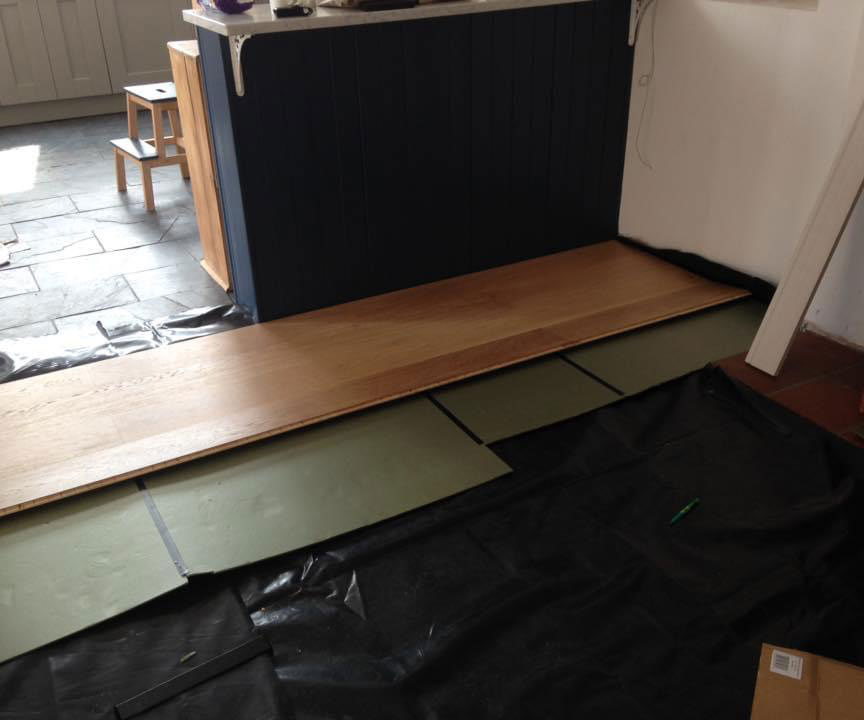
Who knew that installing an engineered wood floor was a job that could transform a house in a day? Seriously, when we set out, cutting and fitting the underlay, I had no idea that later that day I’d be admiring a finished floor.
In our previous renovation, we’d laid an engineered wooden floor all wrong. Don’t misunderstand me, it was a beautiful floor, a rich walnut, but oh my, it was more than a little bouncy underfoot.
That meant that I was a little dubious when it came to installing a floating engineered floor in our shiny new home. I needn’t have worried though. Turns out, if you prepare your subfloor properly and use a good quality underlay you’ll be just fine.
Our flooring was from Kahrs and is an engineered oak. It, like most of the best engineered wood flooring, has tongue-and-groove edges that simply fit together and we used a circular saw to cut the boards to length.
This Bruce Frisco Natural Oak flooring from Lowes has a similar appearance.
Price: $20.99
We used a rubber mallet to knock our tongue-and-groove boards together, but this chunky tapping block would have been a great alternative and I think it would probably have been easier to use too. With a mallet, there was a fair amount of finger bashing and the odd damaged board.
Price: $48.98
This foam underlayment is suitable for both hardwood-engineered flooring as well as laminate. It is really easy to cut and lay thanks to the fanfold design - easier than rolls that keep rolling back up on you while to try to measure. It also has integrated thermal insulation to help your floor feel warmer underfoot.
Price: $59
This 7-1/4 inch circular saw will speed up the time it takes to cut boards to the right size. In addition, it has a 45° bevel capacity that helps when it comes to making angled cuts. This is actually a pretty affordable piece of kit and if you are renovating your whole house will no doubt get plenty of use.
2. Fitting the wall paneling
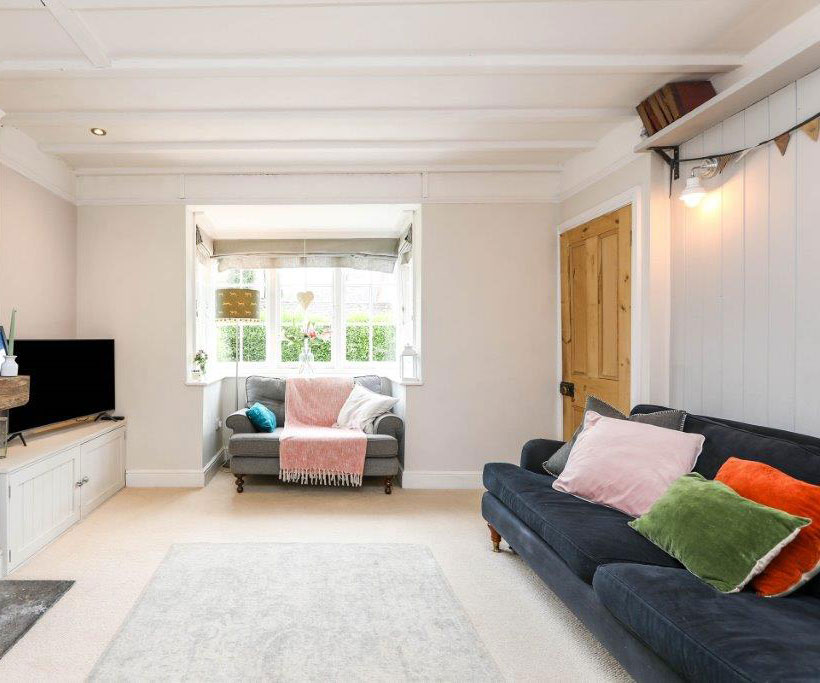
I love timber wall paneling and was keen to introduce it into our living room design scheme to add a bit of interest.
We were aiming for a modern country look throughout. There are lots of original features and little quirks that naturally lend character to the house so we introduced some more up-to-date features to work alongside these. This included looking into wall paneling ideas that would add a fresh finish to the space.
In the living room, we stripped the walls right back to the bare brickwork as the plaster was in such bad condition, falling away. We had three of the walls plastered but chose one wall to fit the paneling. Rather than buying a kit, we bought pine boards with tongue and groove edges.
We attached timber battens horizontally across the width of the wall before nailing the boards to these.
Finally, we primed the boards and painted them a soft creamy gray - similar to Valspar’s Seashell Gray from Lowes.
3. Building the stud walls
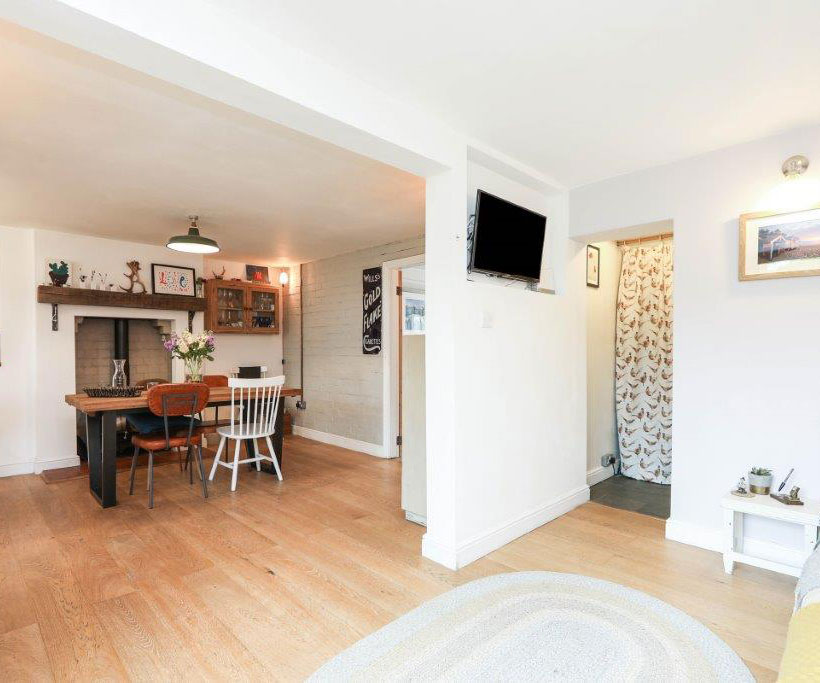
While adding two new extensions, we also totally remodeled the existing layout of this house to make it work better for us. This meant blocking up some doorways, knocking down some internal walls, and building some new stud walls.
If you are thinking of building a new stud wall, I’m here to tell you that this is a pretty straightforward task - although it is better if you can rope in a helper.
To partially divide the dining room and snug, we built a four-foot-wide stud wall between the two.
We began by fitting a section of timber - often referred to as the floor plate - to the length of the floor that the new wall would cover. We used screws but you could use a nail gun if you prefer. Aim to get the screws or nails into the floor joists if you have them. We had a solid concrete floor so plugged and screwed directly into that, ensuring we didn't penetrate the damp-proof membrane.
Next, we fitted a length of timber to the ceiling - the head plate. Again, you want to aim for the trusses or ceiling joists so you might need to go upstairs and lift a floorboard or two to find them. A stud finder such as the Mecurate Stud Finder Wall Scanner Sensor from Amazon will help here and can also alert you to the presence of pipework and wiring.
Next are the wall studs - these should be fixed to the walls that the new wall is being built off between the floor and head plates.
Then we fitted more studs between - at 600mm centers. To strengthen the whole structure we then fitted noggins (small horizontal pieces of timber) between the vertical studs.
Before fixing the drywall into place we ran in the electrics as we wanted an electrical outlet on the snug side of the wall. We also added in some insulation to make the new wall a little more soundproof.
The whole thing was finished in around half a day.
4. Putting up drywall
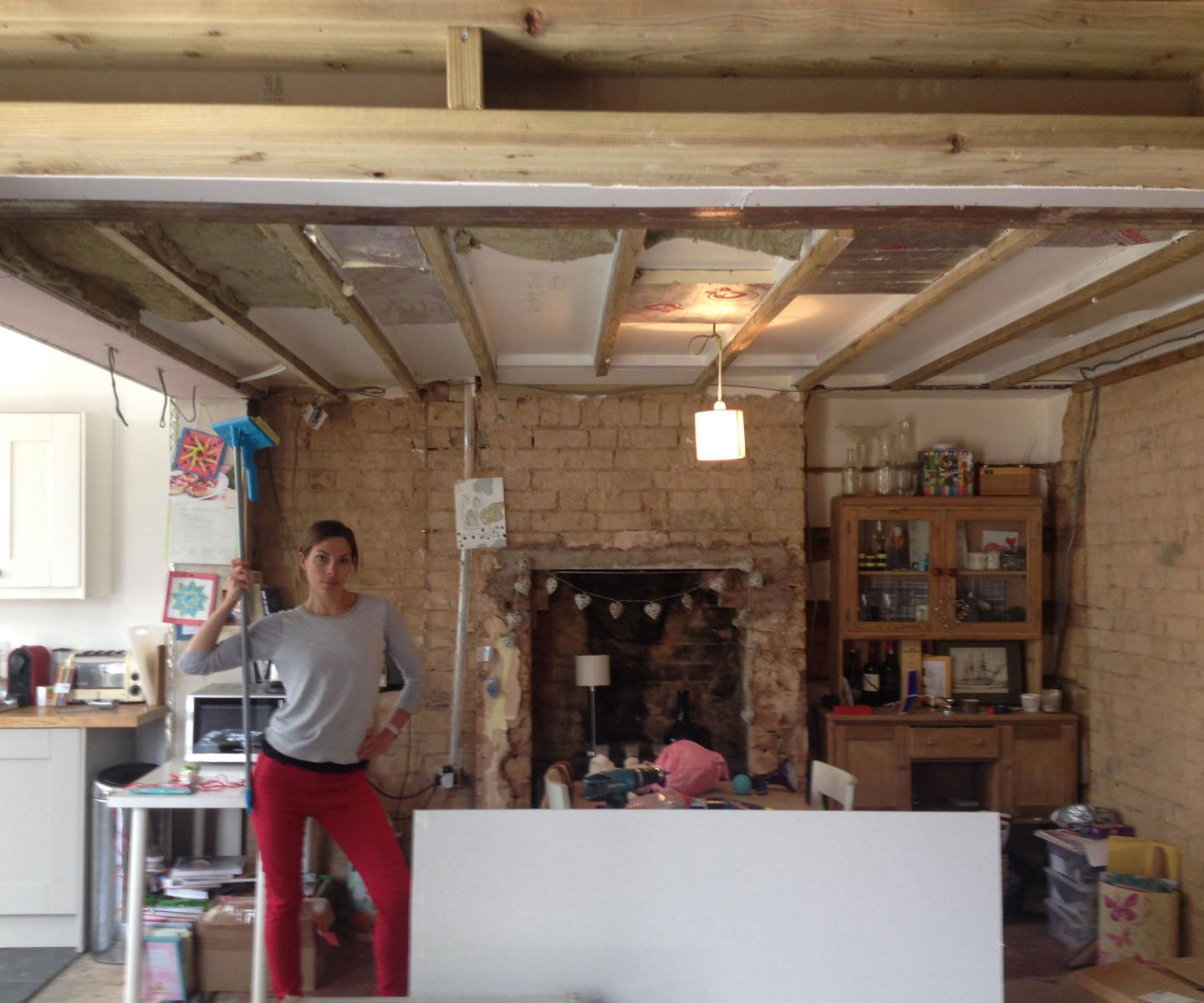
To save on labor costs we decided to put up the drywall ourselves. Honestly, this is a job pretty much anyone could undertake although you’ll want to get someone to help you as large sheets of drywall are heavy and awkward, and holding them in place while fixing them up - particularly to the ceilings - is hard work.
To cut the drywall we used a drywall saw, but you can use a Stanley knife too. The Jorgensen Drywall Saw from Amazon would do the job well.
You want to start at one corner of the wall you are covering and make sure that the end of the drywall sits midway across the stud it is being fixed to so that the next board can butt up to it. In areas where there was no stud to fix the drywall, we fitted noggins between studs. Make sure you use drywall screws designed for the job.
Once all the boards were in place we used drywall tape over the joins and then joint filler. We left the plastering to the pros but some homeowners do choose to look into how to plaster walls and decide to give it a go.
5. Fitting the push-fit plumbing
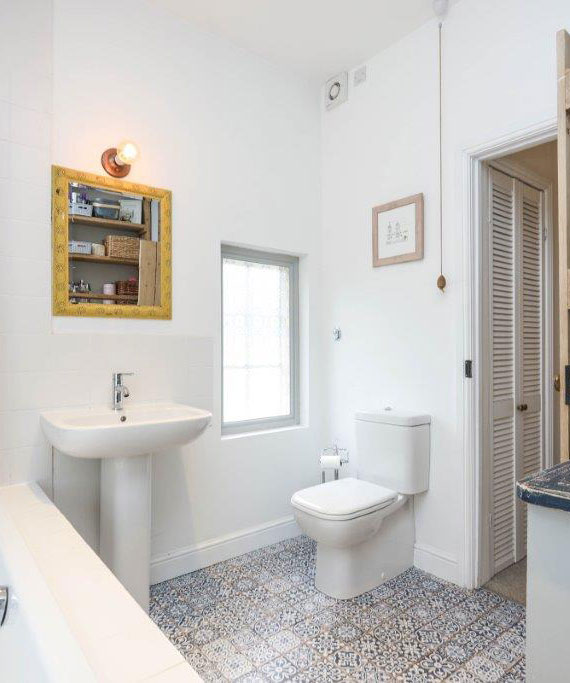
Plumbing was never a task I thought we’d be taking on ourselves and, in all honesty, this was a job where I played more of a support role to my husband who seems to have a knack for picking up new skills pretty quickly.
There are now lots of products out there that make it far easier for DIYers to get to grips with plumbing - namely plastic push-fit connectors and pipework.
There are a number of brands that manufacture the push-fit system but we opted for JG Speedfit plastic pipe and fittings which you can buy from Amazon. The system works by securely grasping the pipe inserted with a toothed grip ring and sealing it with an o-ring seal.
The use of inserts is also important, these are pushed into the pipe before inserting into the coupler. The benefits of using plastic pipe rather than copper are there are no expert plumbing skills involved such as soldering and you can also use longer sections to connect as they can be manipulated easier to fit. This makes the whole process quicker and more accessible to the DIYer. It’s also worth noting you can also use the push-fit system with copper pipe as well and can even get push-fit copper couplers.
We connected all the faucets for the bathrooms and kitchen sink using these systems and as a result, significantly reduced our new bathroom costs.
While the sense of achievement that you get from DIYing certain aspects of a home renovation is undeniable there are also a whole host of DIY jobs that aren't worth the effort in my opinion. Some things are just best left to the pros if you want a perfect final finish.