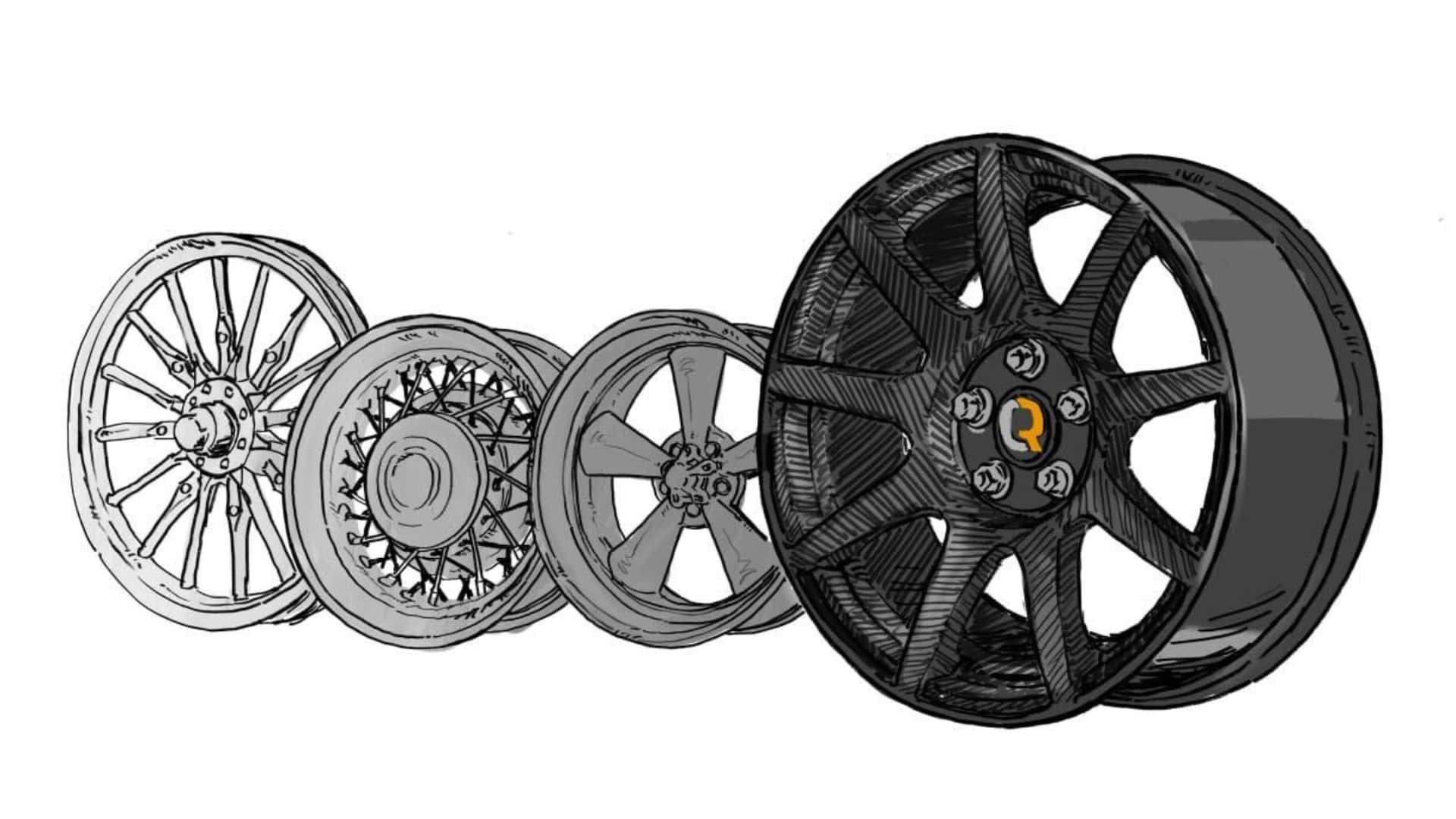
Carbon-fiber wheels aren’t new. Honda ran them on its 1984 grand-prix bike, yet only in the last decade have carbon-fiber wheels really started to impact the production-car world.
It’s almost entirely thanks to Australian company Carbon Revolution. It started making carbon-fiber wheels for the aftermarket, but a contract with Ford for the 2016 Shelby GT350R turned them into a volume manufacturer.
Carbon Revolution now has more than 80,000 wheels on the road and supply contracts with Chevrolet, Ferrari, Land Rover, and Ford. (Koenigsegg also has carbon-fiber wheels, though obviously in very low volumes. Porsche also built them in-house for the previous-generation 911 Turbo, though hasn’t offered them for a few years.)

The potential upsides of carbon-fiber wheels are huge. Carbon fiber is both very light and very strong. Any automotive engineer will try to save weight, but some weight savings are more impactful than others.
”The basic physics lesson that I like to give everyone is that the wheels are the second most important weight in the car,” says Dr. Ashley Denmead, founder and CTO of Carbon Revolution. (The most important being the tires.)
A car's wheels are unsprung and rotating masses. Reducing unsprung mass means less work for the suspension to do, improving ride quality. Reduced rotating mass cuts down on inertia, bringing small improvements in acceleration, cornering, and braking. And compared with all of a car’s unsprung and/or rotating masses, it’s easiest to save weight with wheels.
This is why we have aluminum-alloy wheels—they’re more expensive than steel wheels, but the benefits from their weight savings are generally worth the tradeoff in added cost. While currently far more expensive than aluminum units, carbon-fiber wheels promise to extend the benefits of lighter wheels.

It’s difficult to find exact figures for wheel weights, but we do know that Carbon Revolution’s C8 Corvette Z06 wheels are 41 pounds lighter in total than the car’s standard forged-aluminum wheels, a significant amount of weight.
To the casual observer, carbon fiber might seem an odd wheel material. It’s obviously very light and strong—hence why it's used in so many race-car chassis—yet when carbon-fiber fails, it can shatter. A shattered wheel is a scary occurrence to consider; Objects made of steel and aluminum tend to deform, not shatter.
Denmead says those concerns are unfounded.
“In terms of solid carbon fiber, there's parts of the wheel which are nearly two inches thick,” he tells Motor1. “That stuff doesn't break easily or with a low amount of energy by any means.”

There are very high standards for wheel performance laid out by both the Society for Automotive Engineers (SAE) and the automakers themselves. A study done by Ferrari and the University of Modena on Carbon Revolution wheels outlines the extremes of wheel testing. The SAE’s standards are lofty, and Ferrari’s are loftier. Other automakers have similarly high benchmarks. As Carbon Revolution CEO Jake Dingle puts it, wheels are a “safety critical” component on their cars.
Dingle tells a story of the company’s early work with Ford. The automaker actually bought Carbon Revolution’s aftermarket wheels and abused them relentlessly on Detroit’s potholed streets before committing to work with the company.
“They just kept plowing these things into potholes and only actually lost air,” Dingle said. “They chewed up the flanges, as you would expect, but they convinced themselves.
“So, it's one thing to do all the laboratory testing and everything, and that's all very mature and well understood. But introducing a brand new material type into a safety-critical product, they just decided they had to just take it into the real world and see what would happen. And so that was several months of just trying to bash these things up and that convinced them.”

The eventual GT350R wheels, like all of Carbon Revolution’s subsequent OEM products, were made to even higher standards than their aftermarket products. Dingle even has stories of some automakers cutting notches into the wheels with angle grinders to simulate cracking, and one where a tire blew out at 180 mph and the wheel held up. The failure mode of these wheels after a bad impact is also not exactly what you’d expect.
”We use the analogy of the carrot versus the celery, which is an interesting one. If you imagine you had a stick of carrot and a stick of celery,” Denmead says. “The celery is much more like a composite material which is fibrous. compared to a metal which is more homogeneous and isotropic. So imagine if you had a piece of aluminum and a piece of carbon fiber and you tried to snap them like you would a piece of carrot and celery. You may not be able to do it in your hands, but if you force the issue, the aluminum tends to snap like a carrot, whereas the composite material tends to break more like a piece of celery where the fibers tend to still be holding together in some way.”
In extreme fatigue testing outlined by the Ferrari paper, this failure mode also occurs. Denmead explains that as a result, a failed wheel spoke never loses its load-carrying capacity. Carbon Revolution says it can make wheels with huge strength without adding too much weight. Dingle and Denmead say that for one wheel program, Carbon Revolution added 50 percent impact strength with only a 10-percent weight increase.
This is a benefit of the unique way carbon-fiber is made. You can add or subtract layers of the woven material—called the layup—as needed. So in areas where you need lots of strength, you might have a thick layup, whereas in others, the layup can be thinner. It’s a key advantage over aluminum wheels.
“One of the big constraints with aluminum wheel manufacturing is you've got to be able to pour the liquid molten aluminum into a mold before it solidifies and it's got to fill the whole cavity,” Denmead says. “So you know quite often. You can't have thin sections.”

Currently, Carbon Revolution only supplies wheels for performance cars, but Dingle says this will soon change. The company is after EV makers looking for a new way to lose weight and gain efficiency.
“The Ferraris of the world and the Corvettes of the world, they'll always be there and you can imagine that they'll always want the 1.5 second lap time improvement that the technology brings,” Denmead says. “But when we talk to the customers that have the real problems in industry today, the real problems are in weight and they're really scratching their heads about how they're gonna meet targets with EV drivetrains… They really don't have a lot of options that save them significant weight to get them back within an acceptable level, so this is something that seems to be one option where they could save 100 pounds.”
Denmead even talked about how carbon fiber can be used to create unique aerodynamic features, something that hasn’t been explored yet to its fullest. Both and he and Dingle are also quick to point out that the weight and strength benefits brought by carbon-fiber wheels grow with wheel size.
The company is looking to expand production in its native Australia and into North America to meet growing demand to the tune of hundreds of thousands of wheels per year. A huge jump from the 80,000-plus it’s made to date.
“We are today pretty much what aluminum wheels were in the early 1970s,” Dingle says. “A new technology that has the capacity to really disrupt the industry.”