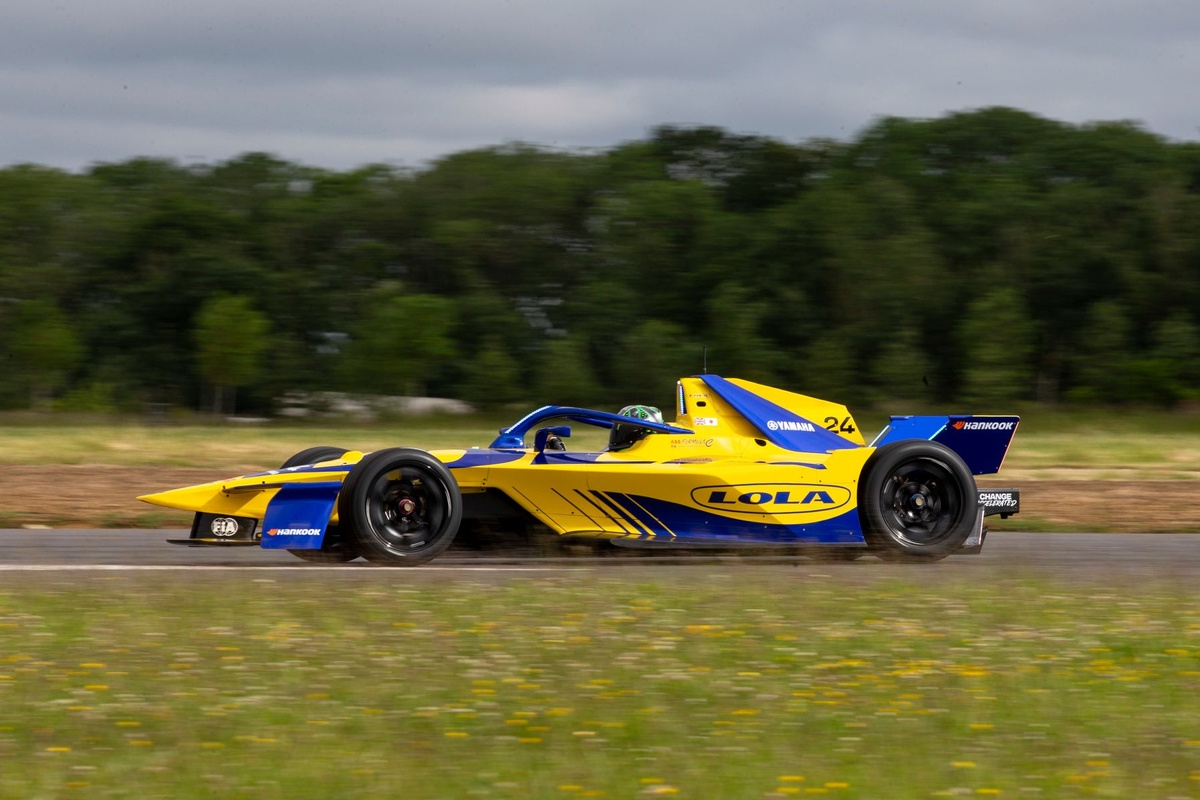
When developing a new electric powertrain for Formula E, multiple objectives must be balanced and prioritised. Power, efficiency and controllability are all crucial for manufacturers, and compromise is inevitable when determining the best overall package. A highly efficient powertrain is of little use if it cannot reach maximum power quickly enough, has too much inertia, or lacks the necessary software controls for energy management.
Each of these core elements also involves additional considerations, highlighting the extensive work required to bring a project from concept to the track. Since Formula E began a decade ago, and powertrain development was opened up in season two, several aspects of the design and development process have matured hugely. We now have more knowledge and better tools than we did back then.
Proof of this can be seen in the inverters, which convert DC current from the battery into AC current for the motor. The inverters are now over 99% efficient, and the electric motors we use are more than 98% efficient. This high level of development can largely be attributed to improvements in motor construction, electronics precision and speed, and advances in materials science, resulting in increased hardware capacity.
When Formula E first began with a standard powertrain capable of 150kW in race mode, we used a five-speed gearbox as we couldn’t achieve maximum power early enough. My team, Abt Sportsline, reduced this to three gears in season two, two gears in season three, and eventually one gear in season four.
Eliminating multiple gears was a major breakthrough in the Gen1 era as gear shifts result in time loss and hurt efficiency. Now, every team uses a single gear, which requires specific treatments for the gear teeth. These teeth are made wide and shallow to reduce friction, which improves efficiency and allows the cars to accelerate seamlessly from 0-300km/h.
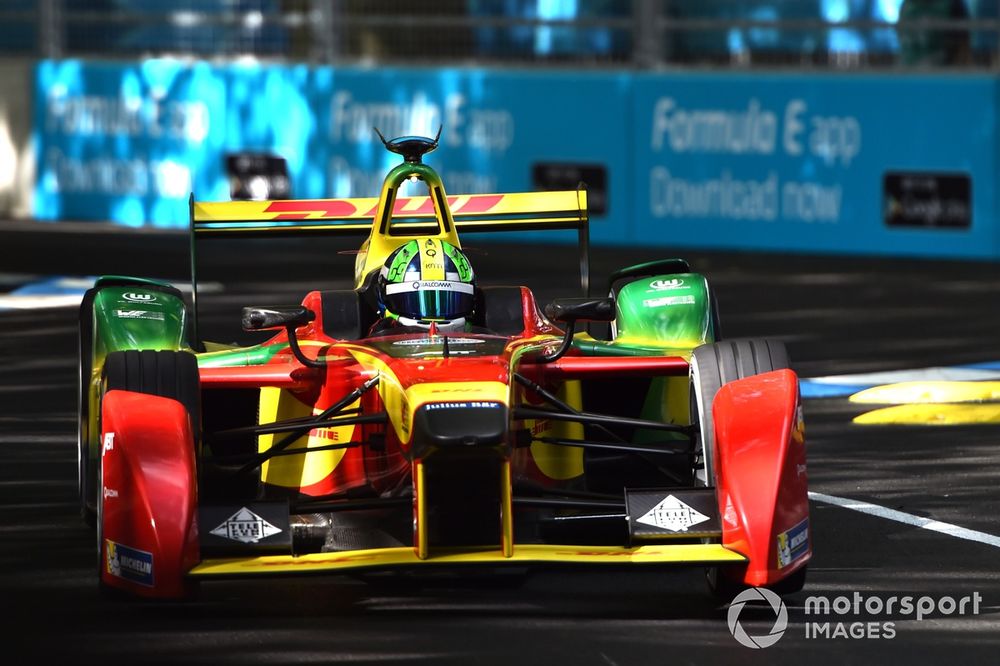
Arguably the biggest difference between past and present development lies in advances in software calculations and predictive engineering. These impressive advancements allow for more precise simulations of reality, streamlining the development process and enabling faster innovation. Instead of producing several powertrain iterations and testing them physically to find the best solution, much of the optimisation can now be done virtually before parts are manufactured.
So, what are the main criteria we look for in a Formula E powertrain? First, it’s essential to achieve maximum power across all revs as early as possible. We are limited to 350kW, so the motor must operate at its peak without exceeding that limit, which would result in a penalty. Power control is challenging, particularly when the motor, gearbox and driveshaft oscillate over kerbs or bumps.
A throttle map that delivers torque smoothly is a key area where the driver can influence development. I focus on how the motor behaves under braking, how its positioning affects the car’s balance, and optimising software controls, like how the motor responds to regenerative braking.
A larger motor with thicker copper wiring typically has less resistance. However, a larger motor also means more mass and weight
Incremental gains in efficiency are a continuous area of focus. We’re always looking for an extra 0.1% or 0.2%. The important thing is achieving efficiency across the entire package, not just in the motor and inverter.
In addition to high peak efficiency, we aim for high average efficiency, which requires a large motor. A larger motor with thicker copper wiring typically has less resistance. However, a larger motor also means more mass and weight, so other factors must also be considered. Lightness has clear benefits for efficiency, and low inertia is also critical.
Striking the right balance is a complex task that always requires compromises, but the advances made over the past 10 years have been truly remarkable.
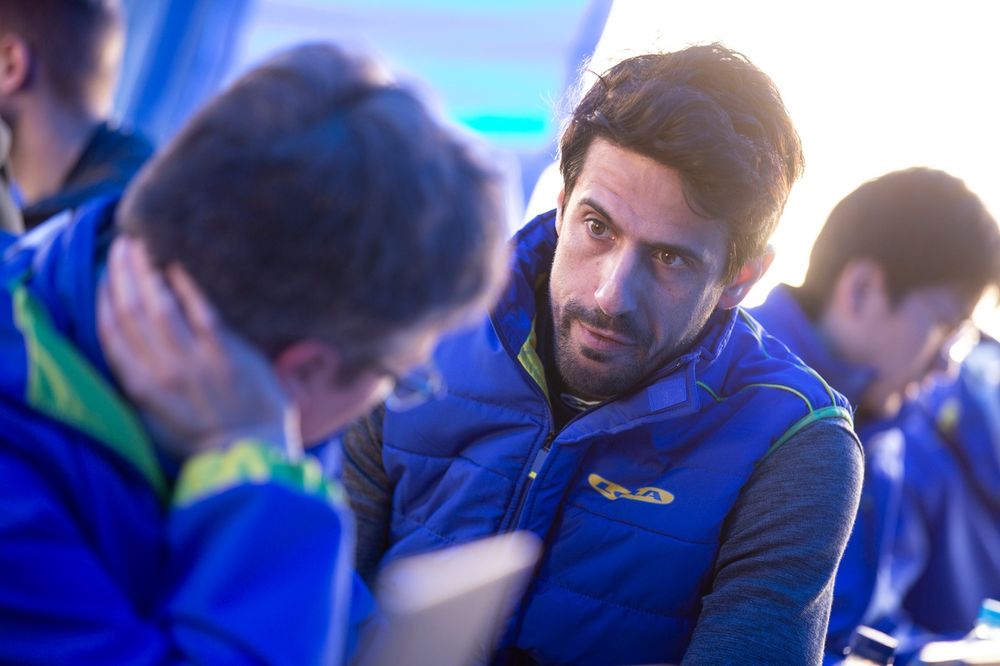