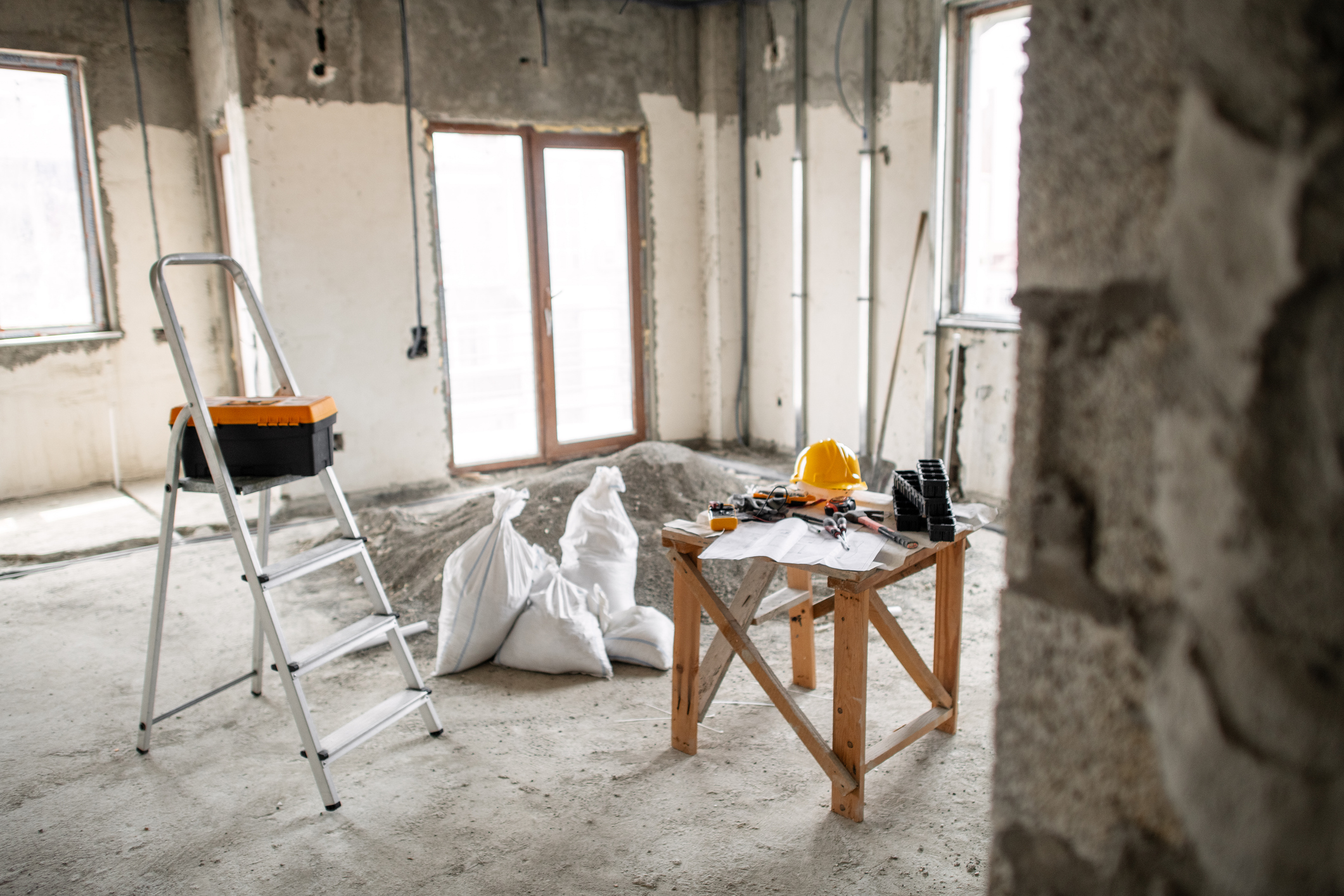
A looming shortage of construction workers is putting the Los Angeles region on a potential collision course with one of its most urgent policy goals: building new housing to lower costs for buyers and renters.
The city of Los Angeles alone has set itself the goal of creating almost half a million new homes by 2029, according to its Los Angeles Housing Element.
But finding the workers to build those homes has been a challenge for several years. In a 2020 report, the Los Angeles County Economic Development Corporation said the industry is facing an “acute shortage” for many of the mid-range skills required in construction — including training for jobs like sheet metal workers, structural iron and steel workers, operating engineers, and welders and cutters.
The lack of workers is also nationwide, which likely means there are fewer workers who might move to Southern California for jobs. The national workforce needs to expand by 6% a year in order to meet current demand, according to projection models from Associated Builders and Contractors, a construction industry trade association.
“More than 1 in 5 construction workers are 55 or older, meaning that retirement will continue to contract the industry’s workforce,” said Anirban Basu, chief economist for Associated Builders and Contractors. “These are the most experienced workers, and their departures are especially concerning.”
A shrinking pool of workers bodes ill for the region’s ability to build its way out of the current acute housing shortage. The convergence of high demand and short supply has driven up housing costs to the point where renters in Los Angeles County need to make nearly three times the minimum wage in order to be able to afford the average apartment, according to the California Housing Partnership.
“We’re looking to strengthen our numbers at the very same time that we are losing many workers to retirement,” said Anne-Marie Otey, communications director of Los Angeles/Orange Counties Building and Construction Trades Council, which represents 48 local unions and district councils in 14 trades. She says they are in “recruiting mode” right now.
Even with the current supply of labor, contractors are finding that jobs are taking longer to complete, which also drives up costs. Tim Cheng, co-founder of Modus Development, a property development firm focused on single-family residential construction, says he now builds in a three- to four-month delay due to both labor and other unexpected changes in the building process. Reduced supply also means higher wages.
“We just can’t do everything nowadays based on how construction costs,” Cheng said.
Construction employment has historically waxed and waned along with business cycles.
Hamid Behdad, president of Central City Development Group, said that during the COVID pandemic, many left the trades and the new generations don’t seem interested.
“To re-attract them to the industry is really a monster job,” Behdad said. “That’s what I’m hearing from executives and people who are involved with labor.”
What’s alarming about the current labor supply issues is it’s not clear where the next wave of workers will come from. Most construction projects require a broad set of specialized skills — for example, welding and electrical work — that can only be acquired through years of training.
Immigrant labor comprises 40% of the construction workforce in California, according to the National Association of Home Builders Economics and Housing Policy Group. That means that the labor pool can fluctuate due to a variety of factors, such as border policy and economic cycles.
“It’s not easy to find a good worker, a loyal worker, for [the] long term,” said Val Fomin, general contractor at Katz Design & Builders Inc. “It is challenging. It’s almost like full-time work.”
In the 1980s and 1990s the building industry could depend on a steady stream of new workers emerging from high schools with trade programs. Many of those programs gave students basic skills in welding and carpentry. But many of those programs were phased out for more high-tech pursuits, such as coding or healthcare. Now, with a crisis looming, parents, teachers and students are advocating for these programs to come back.
Call time for the advanced welding class at La Mirada High School is 7 a.m. each weekday, or the “zero period” in the school schedule. Instead of a traditional lecture and attendance sequence, advanced welding students get straight to work on projects to simulate a real-world shop experience.
La Mirada High School’s Welding Pathway program began in 2010 and is led by teacher Brent Tuttle.
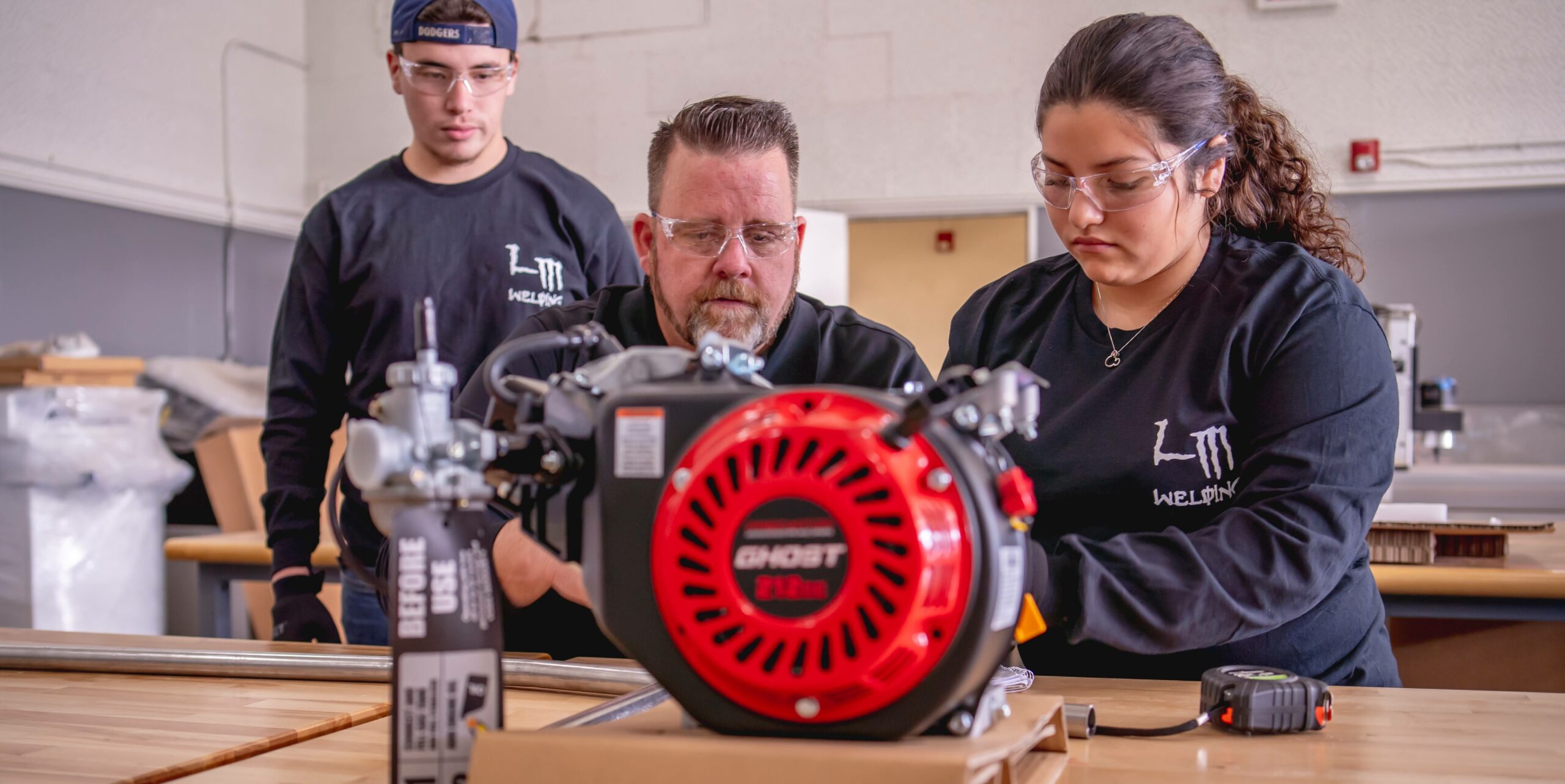
“It’s just a matter of getting the kids to understand that there are options in life,” said Tuttle, who has been teaching the trade for over a decade at La Mirada. “The kids that decide not to go down that four-year path, or maybe not even a [community college] path, at least we’re giving them the skills to go out there and get a job.”
Several schools in the Norwalk-La Mirada Unified School District have “flagship” programs including culinary and robotics, according to Tuttle. In 2020, Tuttle received a teaching prize from Harbor Freight Tools for Schools, a program of the Smidt Foundation, that provided additional money for the program. Tuttle has transformed the shop into a robust avenue for his 180 students to receive transferable certification and career opportunities.
“I was probably failing four classes my freshman year,” said Jacob Pittman, a recent graduate of La Mirada High School who was in the Advanced Welding Pathway program. “This program has motivated me to get a job, a hands-on job, and make money.
“My dad, when he was in high school, there was a welding shop, and then they closed it down,” Pittman added. “When I joined La Mirada High School, he said, ‘You better take welding, it’s a good skill to learn.’”
The welding students have recently built new workstations for the shop in collaboration with engineering students, a project that was estimated to cost roughly $30,000 from an outside contractor, according to Tuttle. The students built the stations using about $10,000 worth of materials. Because welding consumes a lot of materials, Tuttle estimates his program has a budget of roughly $30,000 a year, which is a challenge for cash-strapped districts.
“Do districts want to spend that much money every year on a program like this, or is it easier just to spend maybe $25,000 one time [to] buy 30 computers?” Tuttle said. “That’s the hard part.”