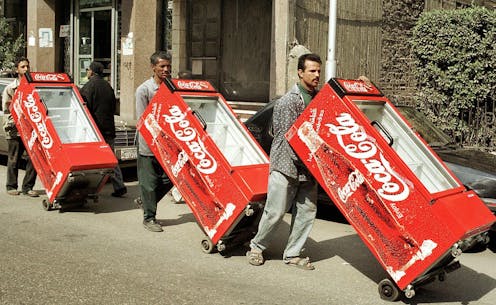
Coca-Cola is one of the world’s most widely recognized brands. Its global reach, spanning more than 200 countries, was the theme of a 2020 commercial that showed families drinking Coke with their meals in cities from Orlando, Florida, to Shanghai, London, Mexico City and Mumbai, India.
Operating on that scale creates a big carbon footprint. The company uses over 200,000 vehicles to distribute its products every day and runs hundreds of bottling plants and syrup factories across the globe.
But Coke’s single largest contribution to climate change comes from its refrigeration equipment.
Running refrigerators uses a lot of electricity, and some coolants in these systems are greenhouse gases that trap heat in the atmosphere. Almost two-thirds of the climate impact of refrigeration comes from electricity consumption, and refrigerants account for the rest. As of 2020, refrigeration produced nearly 8% of global greenhouse gas emissions.
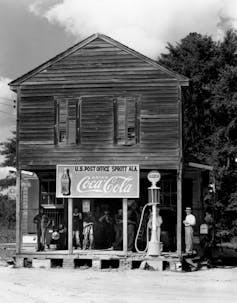
History suggests that the most effective way to shrink Coca-Cola’s refrigeration emissions may be to question whether the company needs that cooling equipment running around the clock at convenience stores on street corners worldwide. That’s a heretical notion for a company obsessed with making sure Coca-Cola is always within “an arm’s reach of desire,” as one Coke president put it.
As I show in my new book, “Country Capitalism: How Corporations from the American South Remade Our Economy and the Planet,” major companies like Coca-Cola have profited handsomely by making their products readily available worldwide. In doing so, they have created a fast-paced, long-distance form of commerce that is a major driver of our planet’s current ecological crisis.
Wanted: An ideal refrigerant
Refrigerants first became an environmental issue because of concerns about ozone loss, not climate change. Before the 1980s, the primary coolants used in refrigerators were chlorofluorocarbons, or CFCs. Discovered in the 1920s by a chemist at General Motors, these compounds were odorless, nonflammable and seemingly nontoxic – all properties that made them useful to industry. In the following decades, CFCs became the chief refrigerant used to keep things cool.
Then, in the 1970s, researchers at the University of California found that CFCs could destroy stratospheric ozone, a gas in the atmosphere that protects life on Earth from the Sun’s ultraviolet radiation. Nations ultimately moved to ban use of CFCs through the 1987 Montreal Protocol, one of the most successful environmental treaties on record.
Chemical companies such as DuPont led the way in promoting new chlorine-free refrigerants, called hydrofluorocarbons or HFCs, that would not deplete the ozone layer. Like CFCs, HFCs appealed to industry because they were odorless, nonflammable and posed no serious threats to human health.
But HFCs had a big drawback: They were powerful greenhouse gases that trapped heat in the Earth’s atmosphere, warming the planet’s surface. Some HFCs had warming impacts more than 1,000 times greater than carbon dioxide, the most abundant greenhouse gas.
HFC politics
Companies like Coca-Cola knew about HFCs’ climate-warming effects when they began transitioning to this new refrigerant in the 1990s. Bryan Jacobs, a Coca-Cola engineer who worked on this transition, told me in an interview that early on, refrigeration technicians in Europe recommended another promising path instead.
Greenpeace advocates in Germany had worked closely with refrigeration engineers to develop what came to be known as Greenfreeze cooling equipment: machines that used hydrocarbons, including isobutane and propane, as refrigerants. These refrigerants, which had a global warming impact radically lower than HFCs, offered the prospect of protecting both the ozone layer and the climate.
Jacobs told me that Coca-Cola was “pretty dismissive,” largely because his team feared that these refrigeration units filled with flammable material might explode – especially in rural areas lacking technical support. Instead, Coca-Cola shifted to HFCs.
In response, Greenpeace launched a major campaign at the 2000 Sydney Olympics to expose how Coca-Cola’s HFC units were warming the planet. Doug Daft, an Australian who was Coke’s CEO at the time, committed the company to eliminating HFC refrigeration from its systems in the years ahead.
Always within arm’s reach
Since 2000, Coca-Cola has become a world leader in developing HFC-free refrigeration equipment. At first it invested heavily in a novel type of refrigerator that used carbon dioxide as the key refrigerant. Soon, however, the company recognized that hydrocarbon refrigerants posed fewer safety risks than they had initially feared, and began adopting these units as well.
Coca-Cola also convinced other companies to shift away from HFCs. Partnering with Unilever, Pepsi, Red Bull and other big firms, the company launched Refrigerants, Naturally!, an organization committed to transitioning major food and beverage companies toward HFC-free refrigeration. In 2010, Coke CEO Muhtar Kent persuaded some 400 consumer goods companies to commit to eliminating HFCs from their refrigeration systems.
By 2016, Coke reported that 61% of all new cooling equipment it purchased was HFC-free. Four years later, that figure reached 83%.
Still, as of 2022, more than 10% of Coke’s new refrigeration units contained HFCs, and refrigeration remained its single largest greenhouse gas emissions source. Part of the problem is that all of these units run on electricity, much of which is generated by burning fossil fuels. With Coca-Cola selling roughly 2.2 billion drinks every day, keeping Coke cold still has an enormous carbon footprint. The same is true for Coke’s competitors.
In an interview with Coca-Cola’s former chief sustainability officer, Jeff Seabright, I asked him whether the company had ever considered thinking more broadly about the necessity of cooling all those Cokes around the clock. Seabright’s response was an emphatic “No,” and that the company was still driven by the mantra of making Coke available for immediate consumption at the point of sale.
Despite the resources that Coca-Cola has invested in changing refrigerants, its cooling equipment is still warming our planet. As I see it, perhaps it’s time for Coke to question whether it needs all those machines in the first place – and for consumers to consider whether their have-it-now expectations are worth the environmental costs they impose.

Bart Elmore received development funding from The University of North Carolina Press in support of the book discussed in this article. Based on his past work, including his 2015 book "Citizen Coke: The Making of Coca-Cola Capitalism," he was a recipient of the Dan David Prize in 2022. He was a fellow at the New America Foundation in 2017-2018.
This article was originally published on The Conversation. Read the original article.