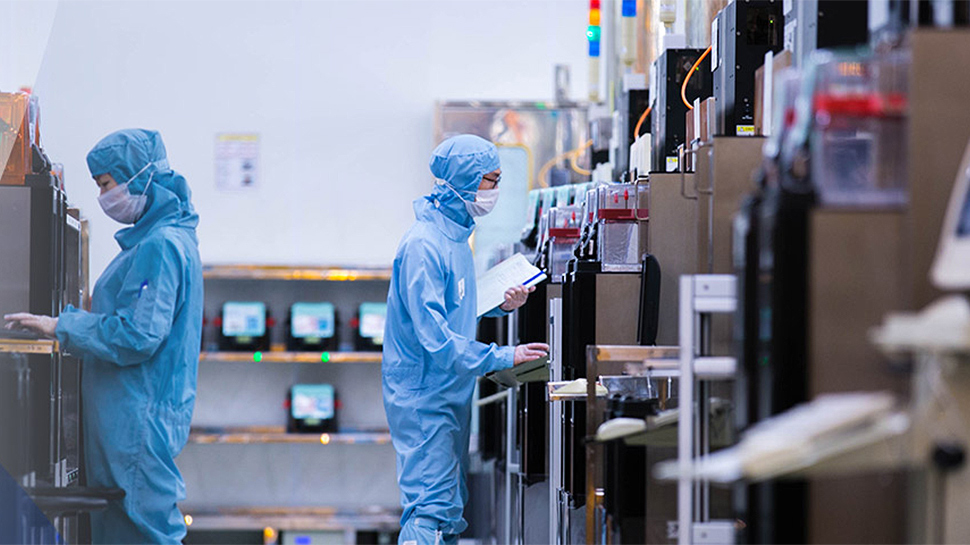
China is on track to achieve basic self-sufficiency in building chipmaking equipment by this summer, reports the South China Morning Post. The publication cites Gerald Yin Zhiyao, chief executive of Advanced Micro-Fabrication Equipment China (AMEC), a China-based maker of wafer fab equipment (WFE).
Chip fabs are equipped with thousands of tools and machinery, and they are usually made in the Netherlands, the U.S., Japan, South Korea, and Taiwan. However, these countries recently restricted the shipments of tools necessary to make chips on advanced nodes to China. Hence, the country accelerated its efforts to build its own supply chain for chipmaking equipment. While this supply chain is not yet world-class, and the tools can only be used to make chips on basic process technologies, it is about to become a reality, according to Gerald Yin Zhiyao, who formerly worked at Intel, Lam Research, and Applied Materials.
"I had thought we need at least 10 years to find a solution, but with joint efforts from hundreds of companies over the past two years, we can reach basic self-sufficiency by this summer," he said.
China's semiconductor supply chain is growing quickly, thanks to collaboration among hundreds of companies over the past two years. Gerald Yin Zhiyaoo expressed confidence that China could achieve self-sufficiency, albeit with ongoing challenges in quality and reliability.
Advanced Micro-Fabrication Equipment China (AMEC) produces etching systems and metal-organic chemical vapor deposition (MOCVD) tools. Some of these tools are reportedly good enough to make chips on 5nm-class process technologies (in collaboration with tools made by ASML, though), but it is impossible to verify this.
AMEC now sources 60% of the parts for its etching tools and 80% of the components for its MOCVD tools from within China. This shift towards domestic sourcing has been crucial in reducing reliance on foreign imports. Given that most parts AMEC uses are now from China, we could say that the company is about to achieve 'basic' self-sufficiency.
However, significant gaps remain in China's semiconductor tool sector. Locally produced equipment currently constitutes only 15% to 30% of the tools used by Chinese foundries. The most notable deficiencies are in lithography systems (as the best that China's SMEE can produce in volume are good enough for 90nm-class process technologies and thicker), ion implantation tools, and electron beam inspection systems.