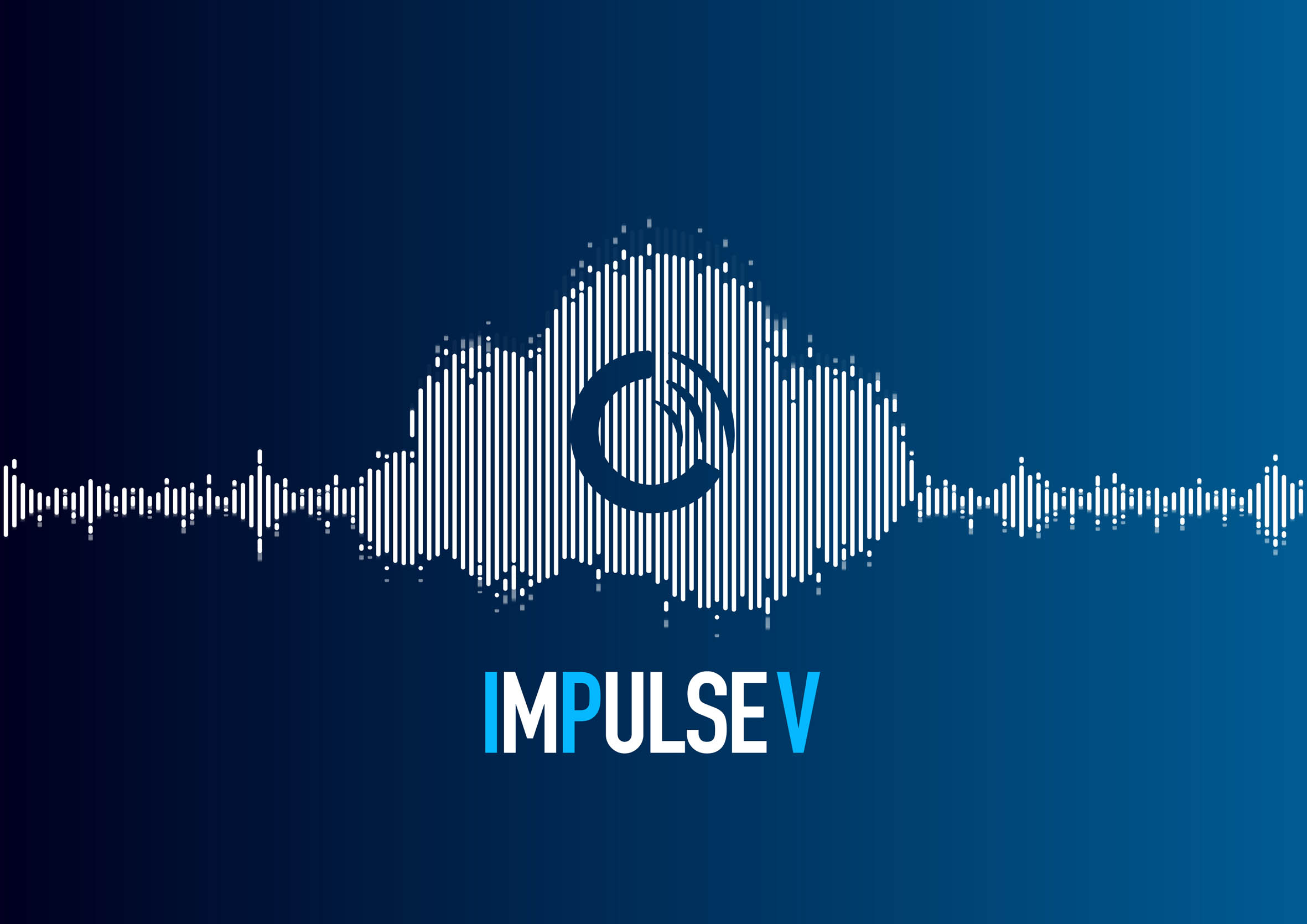
As it celebrates its diamond jubilee this year, Calrec has announced that it will be pushing the boundaries of audio broadcasting at IBC 2024 with a full range of connected technologies enabling broadcasters to scale their processing directly in the cloud.
Calrec will be exhibiting at IBC 2024 at Stand 8.C47 between Sept. 13-16, at the RAI Amsterdam Convention Center.
Products that it plans to highlight include:
- ImPulseV. Following its development preview at NAB, Calrec’s ImPulseV cloud-based DSP processing core will make its debut at IBC. Delivering the same audio quality and feature set as Calrec’s hardware-based ImPulse processing cores, ImPulseV is hosted entirely in a public cloud environment like AWS, which can be accessed from anywhere in the world.
- Using the same interfaces that Calrec users are already familiar with, it can be controlled either through the Calrec Assist web UI or directly from a Calrec Argo console. It means that while there is no difference to the user, broadcasters can enjoy significant operational cost savings by reducing their reliance on physical hardware and scaling productions more efficiently.
- At IBC, Calrec’s ImPulseV system features 264 DSP paths (split between 128 input channels and 136 output paths) and fully immersive formats up to 7.1.4, with control provided directly from an Argo console surface.
- Argo Q & Argo S. Also on show is the Argo Q & S, the multi-award-winning audio control surface which brings unrivaled flexibility, IP-native supercharged DSP, unwavering remote-control capability, and future-proof technologies built around Calrec’s ImPulse core and Assist UI. It means that whether you are working on physical hardware panels or on a remote GUI, the user interface is both familiar and easy to drive. Meanwhile, its modular panel system encourages broadcasters to adapt surface hardware to meet their requirements, with two mid-level rows of interchangeable panels on the Argo Q model, and one mid-level row on the Argo S model. Calrec’s comprehensive system of user templates enables users to instantly change the hardware user interface to meet changing requirements or user preferences. Argo’s physical control surface uses optically bonded touchscreens to provide unrivalled visual feedback and allows users to build definable functions and apply them as templates. This functionality helps operators move around the surface faster and makes it more intuitive.
- Argo’s console architecture offers unparalleled system resilience with each 12-fader wide section remaining fully independent in terms of processing capabilities, path control access, power supplies and connectivity. This system flexibility also means each self-contained section can be connected using local or wide area networks, ideal for distributed productions. For example, a customer could have a 48-fader main console in London and a 12-fader FX surface in New York, both connected to an ImPulse core, allowing them the flexibility to work in whatever way they wish.
- ImPulse and ImPulse1. ImPulse and ImPulse1 are powerful ST2110 native audio processing and routing engines. ImPulse delivers over 2,380 processing paths for the most demanding NGA productions, while ImPulse1 is a compact 1U unit designed to meet the needs of small to medium single mixer applications, delivering 304 to 672 processing paths. With the addition of the cloud-based ImPulseV at IBC, Calrec’s range of ImPulse engines aims to offer a variety of options for all its customers. All three work with both Argo and the browser-based Calrec Assist web GUI to enable remote and distributed working, as well as headless operation. Dual redundant cores or a single core with smaller DSP licenses can be offered.
- Type R. Calrec’s Type R modular, expandable IP mixing system is also on the stand. It too is designed to encourage customers to take advantage of distributed production and flexible workflows. Its three hardware and soft panels can create a variety of system types. It integrates with station automation systems like Ross Overdrive, Sony ELC and Grass Valley Ignite.
In response to the explosion of remote production and distributed working over the last couple of years, Calrec also reported that it will announce an expansion of its remote production capability.
Calrec noted that this year’s incredibly exciting summer of sports has seen widespread adoption of these trends disrupting the traditional need for the control room and operator to be located at the venue. This changes how the operator, and the equipment are managed, as well as providing greater consistency in the mixing. More information about this new innovative toolset will be revealed at IBC 2024.