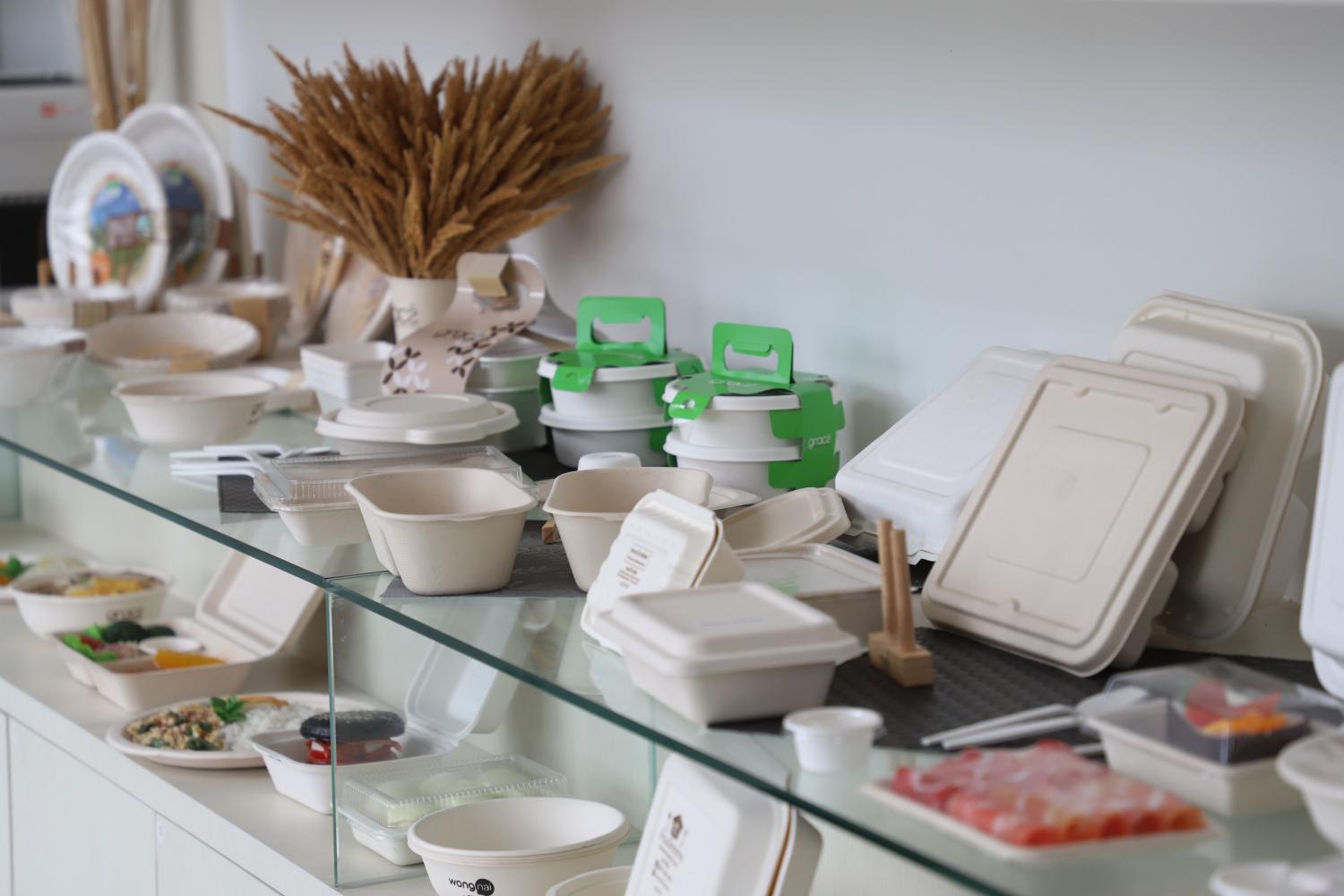
Biodegradable Packaging for Environment (BPE), a Thai manufacturer of food and beverage containers made from agricultural refuse, has resumed a plan to list the company on the stock market as it continues to expand its packaging business.
The company aims to produce more eco-friendly containers under the Gracz brand to replace styrofoam and plastic containers that are popular with street food vendors, but are not good for the environment.
BPE assigned Tisco Financial Group Plc as its financial advisor to develop the listing plan by 2026 in order to raise funds under an initial public offering (IPO) scheme, said Weerachat Kittirattanapaiboon, chief executive of BPE.
The company has yet to decide how many of the shares, currently all held by members of Mr Weerachat's family, will be sold to investors.
With registered capital of 400 million baht, BPE wants to expand its business, increasing production capacity to 10 million pieces per day, up from 2 million pieces at present.
He estimates the company needs to spend 1.2 billion baht for the capacity expansion at its factory in Chai Nat, located 192 kilometres north of Bangkok.
The IPO plan was delayed because of the pandemic, which slowed down growth of packaging materials made from refuse-derived fibre, said Mr Weerachat.
These types of packaging still remain popular among consumers overseas.
BPE expects its revenue to grow by 50% next year, up from almost a billion baht this year, as the trend for eco-friendly containers, especially those made of fibre from agricultural leftovers, is expected to rebound to a pre-pandemic level, he said.
BPE developed new products in addition to plates and bowls during the pandemic, including food boxes, tiffin boxes, hot and cold drink cups and straws, all of which are produced from biodegradable materials.
The company also designed special packaging materials including a fresh durian package that can contain the strong smell during transport, and a plate that can absorb cooking oil from deep-fried food.
BPE uses a variety of raw materials produced from agricultural refuse. As well as the sugar cane fibre it used initially, the company now utilises rice straw, coconut sheath, palm oil, bamboo, pineapple, water hyacinth and, most recently, durian sheath and hemp in its packaging manufacturing.
The company also cultivates organic bananas on a 100-rai plot near its factory in order to export packaging made of banana leaves.
Such materials were once popular among Thais, but were later replaced by styrofoam and plastic containers because of the low cost of this form of packaging and an insufficient supply of banana leaves.
In non-food packaging, BPE has diversified into producing packaging for products such as toys, garments and some single-use medical equipment.
The company is also conducting a trial on face mask manufacturing.
Financially, BPE cut its production costs by reducing its cost for food boxes from 5 baht to 2 baht per unit.
The company also uses electricity from biomass-fired power generators and solar power panels to promote clean energy.