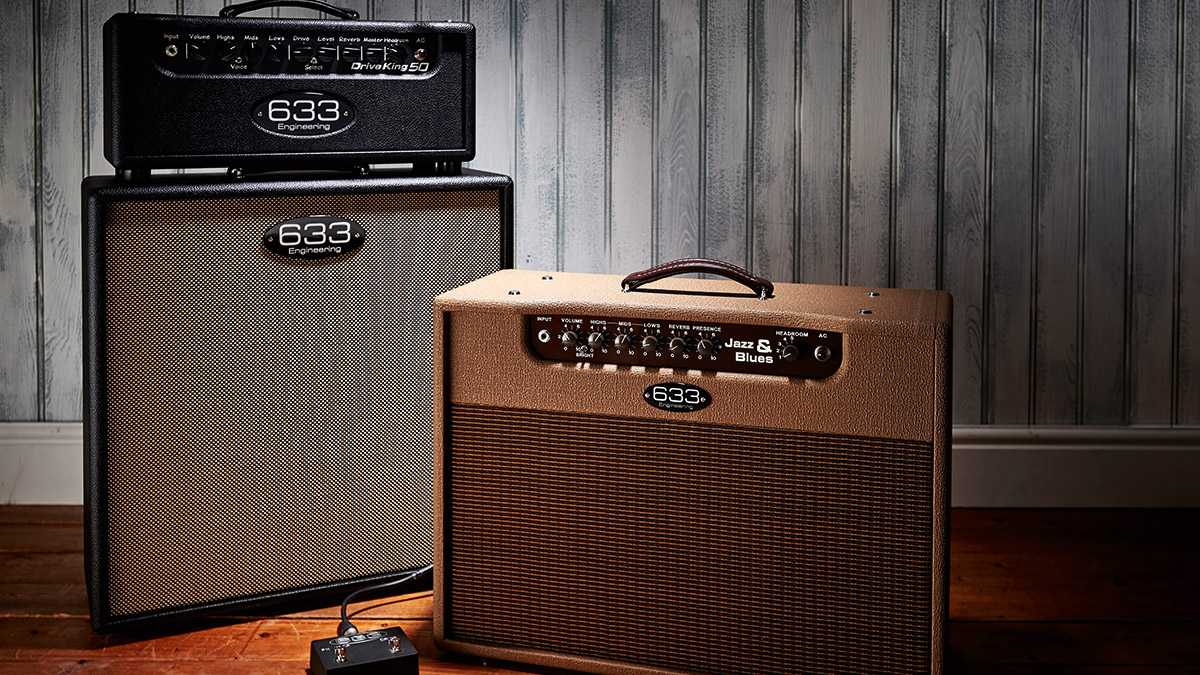
When choosing the different types of wood used in guitar cabinets, a designer will often value stability or consistency most highly; after all, if the material doesn’t change from cab to cab, the results will be more predictable and easier to reliably reproduce. The trouble is, a lot of materials that are consistent don’t always sound as pleasing as we’d hope, at least not to a lot of us guitarists.
MDF is a good example. Medium-density fibreboard is a material that has been favoured by cabinet makers in the past for its consistent behaviour at a low cost, but there are a couple of major downsides – the biggest one being that it generally sounds a bit dead. It can be hard to describe, but it often sounds too controlled, like there is something missing.
So if controlled and stable doesn’t always work, then what about flipping and going for wood? This can work really well. As guitarists, we’re used to looking at wood on our guitars, but – without wanting to be too controversial – its role in shaping the cabinet’s sound is as important, if not more so on some of the instruments we play. But the downside of wood is that every piece is different.
Various parts of a tree will have a different density, let alone trees from different forests, which is the opposite problem to MDF. Using wood can be really hard to achieve consistent results, which to me as a player isn’t that big of a deal, but as a manufacturer is a real headache.
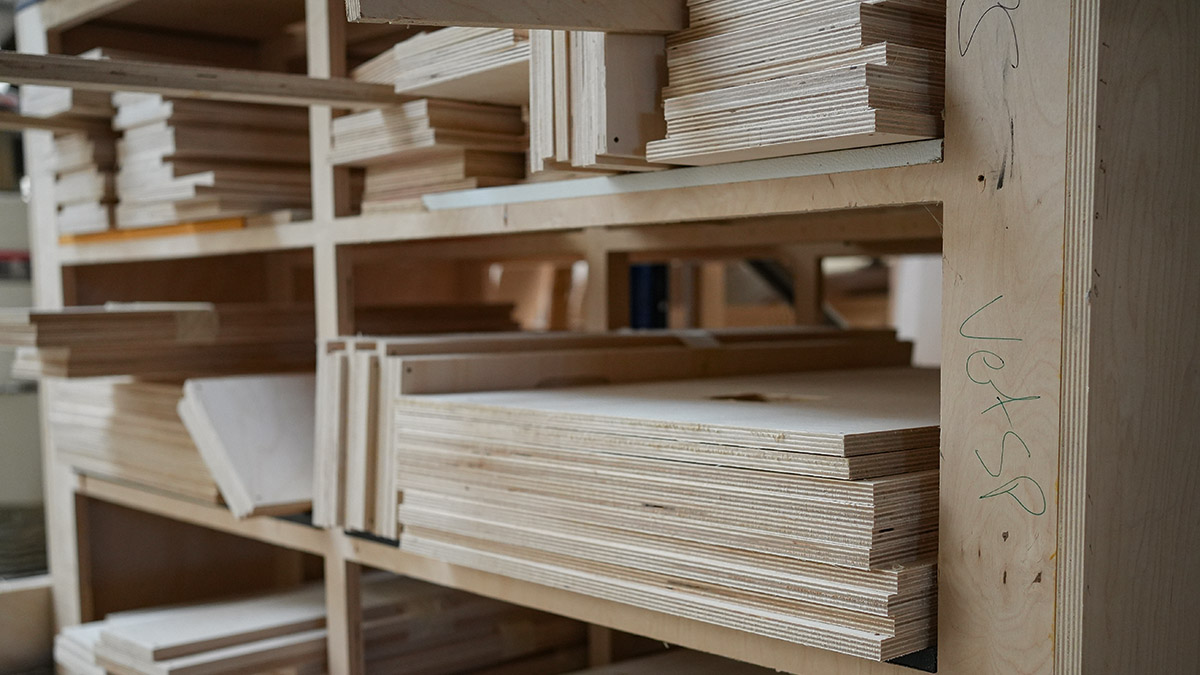
So that’s the extremes – an engineered, consistent material and a natural, inconsistent material – but there has to be something in the middle, a Goldilocks-type material that sounds just right. For me, that middle ground is plywood or, more accurately, birch ply.
It’s great for strength, consistency (although this can vary more than you’d think), it has a lovely natural EQ to it, and it’s a material that is favoured by most cabinet makers. That said, there are many different variations and each cabinet maker seems to have a personal favourite.
Mesa/Boogie, for example, favours a marine-grade birch ply, a ply that may use birch from the same forests but has its ply stuck together with a water-resistant glue, which makes the cabinet sound a tad darker. It’s probably worth mentioning that fellow Californian manufacturer Fender traditionally used pine on its cabinets, a material that is less predictable but in ample supply on the West Coast.
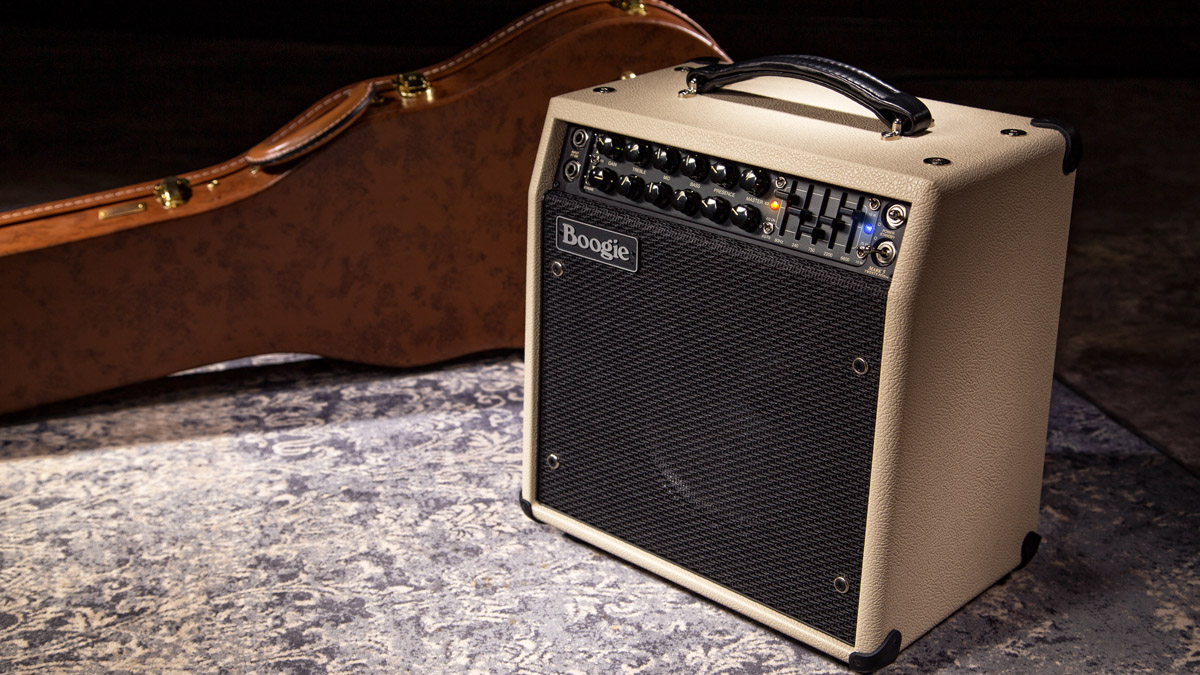
The ability to make plywood from many different woods means that makers can give a different vibe to a cab without too much sacrificing of consistency.
I have been told that Mr Dumble didn’t like the sound of birch ply so opted for something different. The next part of the story seems to vary, but it seems he favoured some kind of okoume ply, a material that has some similar qualities to mahogany, definitely has its own sound and is surprisingly light.
If light weight is something you’re after in your ply, you’ll probably want to go for a type of poplar, usually an Italian poplar. It’s a nice-sounding material and one that is starting to become much more popular due to the scarcity (and rocketing price) of birch
Now, if light weight is something you’re after in your ply, you’ll probably want to go for a type of poplar, usually an Italian poplar. It’s a nice-sounding material and one that is starting to become much more popular due to the scarcity (and rocketing price) of birch ply and the shift towards lighter gear. It’s also an alternative to pine, a wood that was traditionally used to help keep things nice and light.
So I think we’re safe to conclude that material really does make a difference to your cabinet. And here’s a fun activity to try if you have some wood in your proximity. In our workshop we often try to guess the wood being used on a given tool. As each wood resonates differently on the tools, it sounds different – believe it or not.
Obviously, size changes the sound, but there is an audible difference between various types or woods, ply and even differing grades of ply used on machines that cause vibration. They all smell different, too… but you’ll know I’m running out of topics when I write a piece on that!