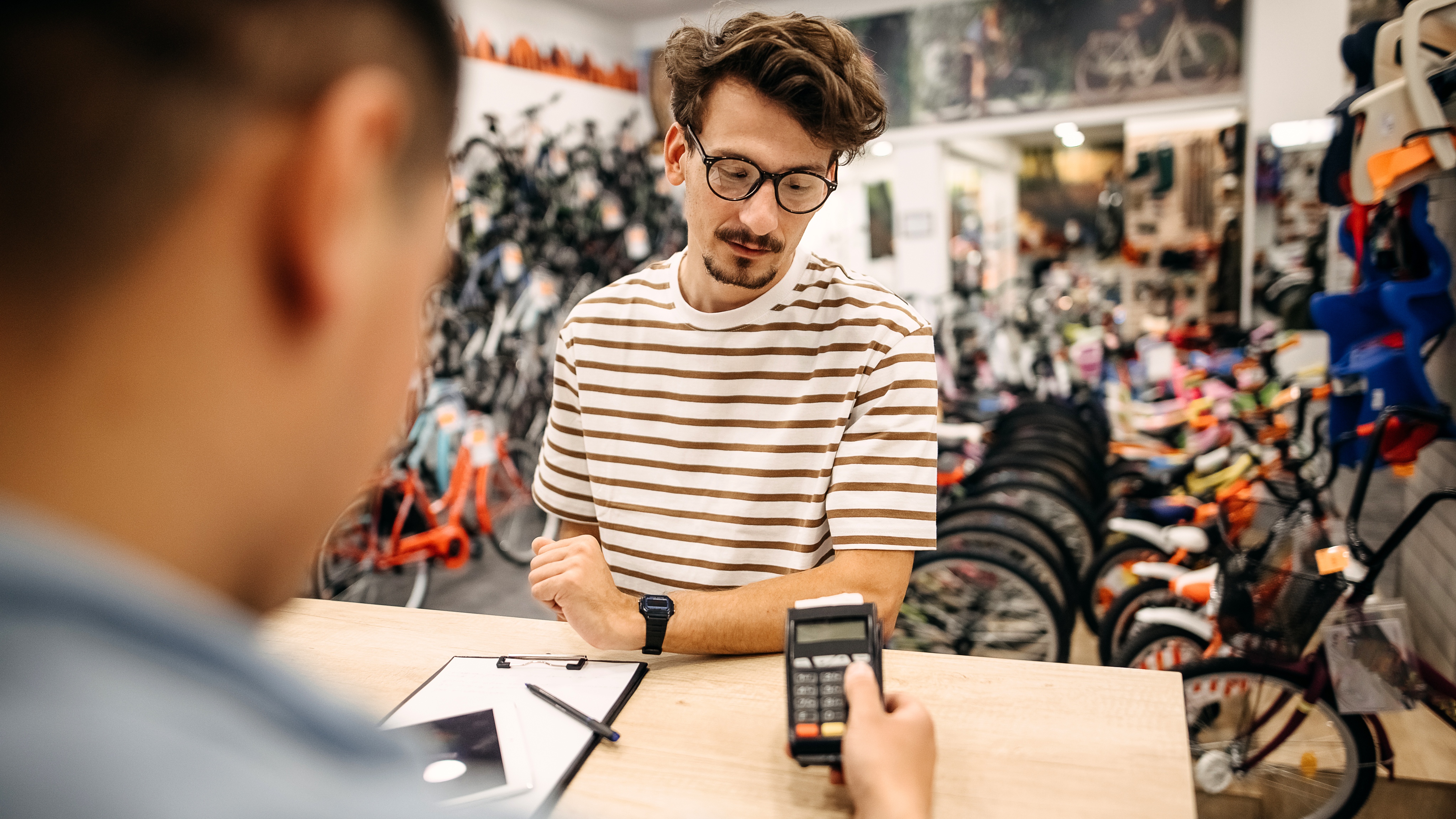
If I had a pound for every time I’ve been asked “What’s the best frame material for a bike?” I’d be able to afford most of a Rocket coffee machine.
The truth of the matter is, this is not a straightforward question. The answer depends very much on what the rider is going to use the bike for, where they’re going to ride it, how are they going to ride it, how long they want to keep it and what their budget is.
Let's start by running through the usual suspects, and listing off the commonly accepted truths about each frame material.
Steel is real
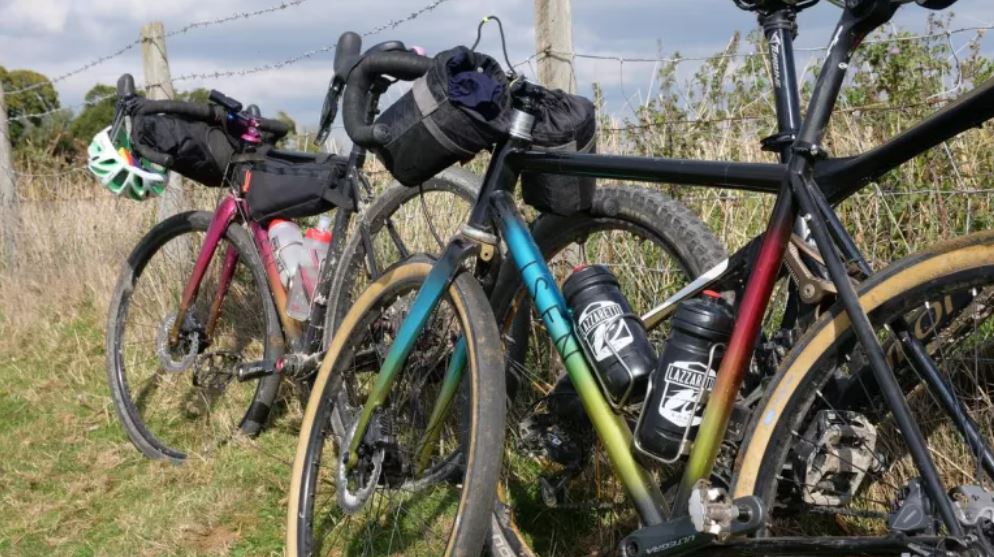
Firstly, we have the venerable steel frame. Bikes were pretty much first made in steel (wood actually, if you’re counting hobby horses but I’m talking about Starley’s Safety bicycle), but the material has evolved in line with how long it has existed in bike frames. I’d be tempted to say that modern steel tubes for bicycle frames are some of the most highly manipulated tubing money can buy; it’s pretty much the norm for even a cheap steel tube to be internally double butted, cold drawn and heat treated. All these processes culminate in making a tube which is both incredibly strong, resilient to fatigue and relatively light.
The huge benefit of steel is that it’s easy to manufacture a bicycle frame from it which is why it is the material of choice for the majority of custom frame builders. It means they can build a great bike, in custom geometries that don’t cost the Earth.
The downside of steel tubing in many people’s eyes, is that due to its density, it weighs more than most of the other materials on this list, which isn’t to say the frames weigh more, but we will come back to that later.
Aluminium has come of age
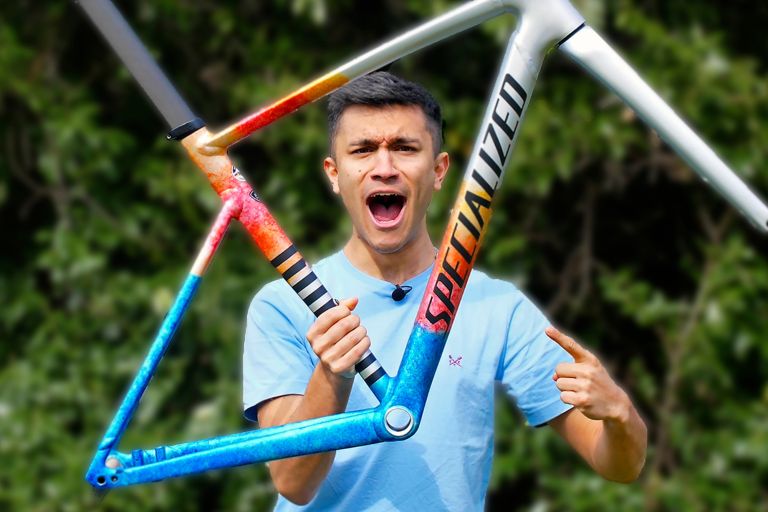
Next on the list, we have aluminium. Aluminium became the material of choice for racing road and mountain bikes in the late 80s and early 90s with companies like Cannondale and Klein leading the way. They soon grew a reputation for huge tube sizes, incredible stiffness and light weight. The common problem with most of these early aluminium frames was that they didn’t fatigue well. I remember racing the Malvern Classic mountain bike race and watching as numerous riders walked over the finish line with their new unicycles as the head tubes had sheared off.
Modern aluminium frames have largely got over these problems with careful tube manipulation through processes such as hydroforming and heat treating. They now seem to form the majority of the lower price points in road bikes and mountain bikes due to the relative light weight, stiffness and ease of manufacture. Just don’t look into the energy required to get aluminium out of Bauxite if you want to feel smug about your new Green hobby.
Titanium is the material for a ‘forever’ bike
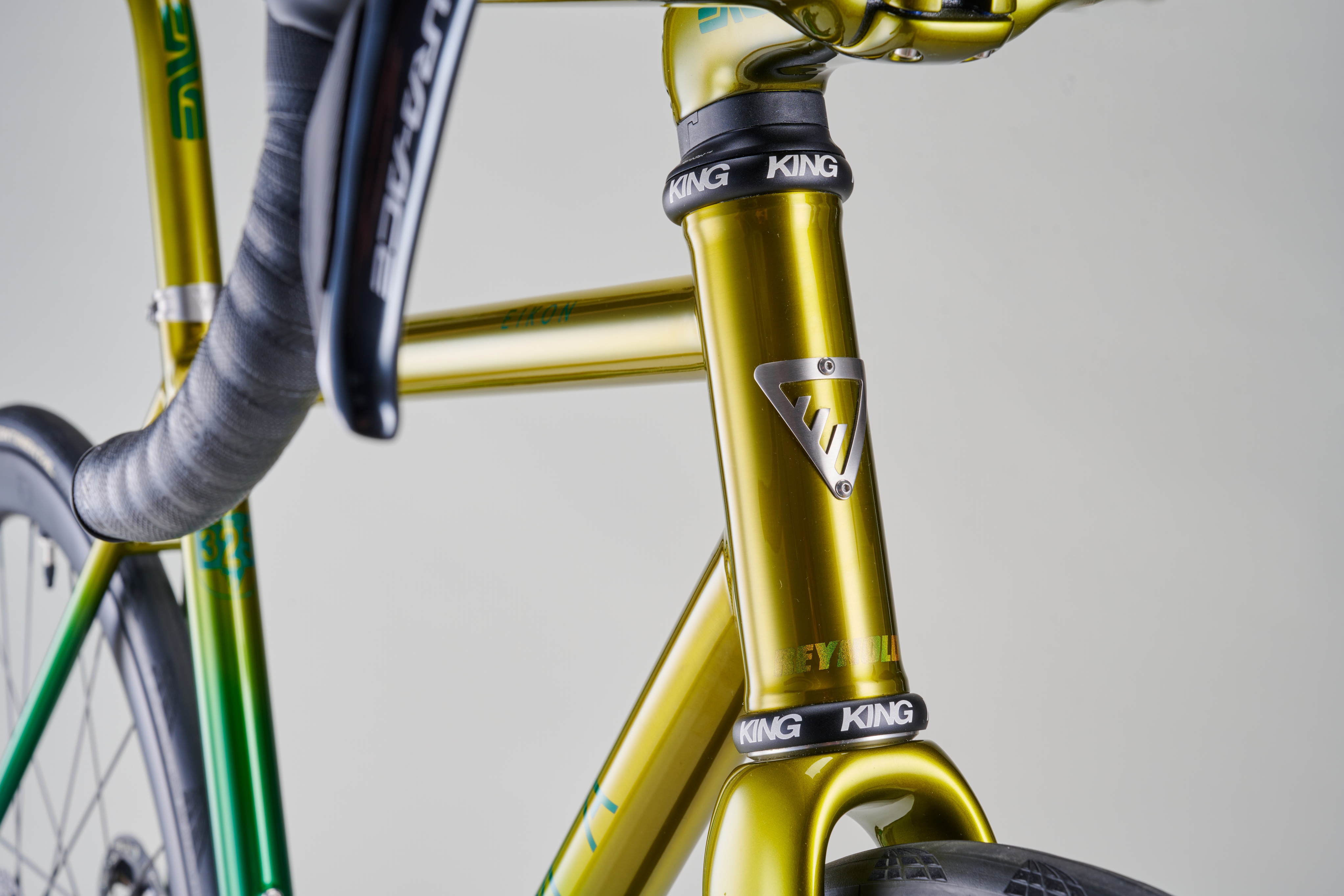
Next in line in the list of metals is titanium. Often admired for its ability to weather any storm due to its chemical inertness, titanium has become a favourite for winter bikes, especially in more temperate climates. It has a reputation for being as lightweight as aluminium but as tough as steel, with an ability to soak up vibration giving a comfortable ride. The problem with titanium is that it’s incredibly hard which makes it difficult or very expensive to manipulate the tubes in any way to alter the ride quality. This means that cheaper titanium bikes tend to be made from what we call plain gauge tubing, meaning the thickness doesn’t change through the whole length of the tube.
Typically, if a tube is going to break, it will always be at one of the joints meaning that you can make the material between the joints thinner. This is called butting, which not only saves weight but also alters the way that tube reacts to road vibration and fatigue.
Because titanium is so hard, it’s incredibly difficult to butt the tubes by normal means, which is typically cold drawing tubes through mandrels or swaging them. A little bit like squeezing Play-Doh through a mould. Some incredibly brave smallscale builders have been known to put plain gauge tubes onto a lathe and skim off the excess material and some bigger companies do it by means of a centerless grinder, but it’s still incredibly wasteful as it’s removing material to waste, hence the typically associated pricetag.
Carbon is King for the masses
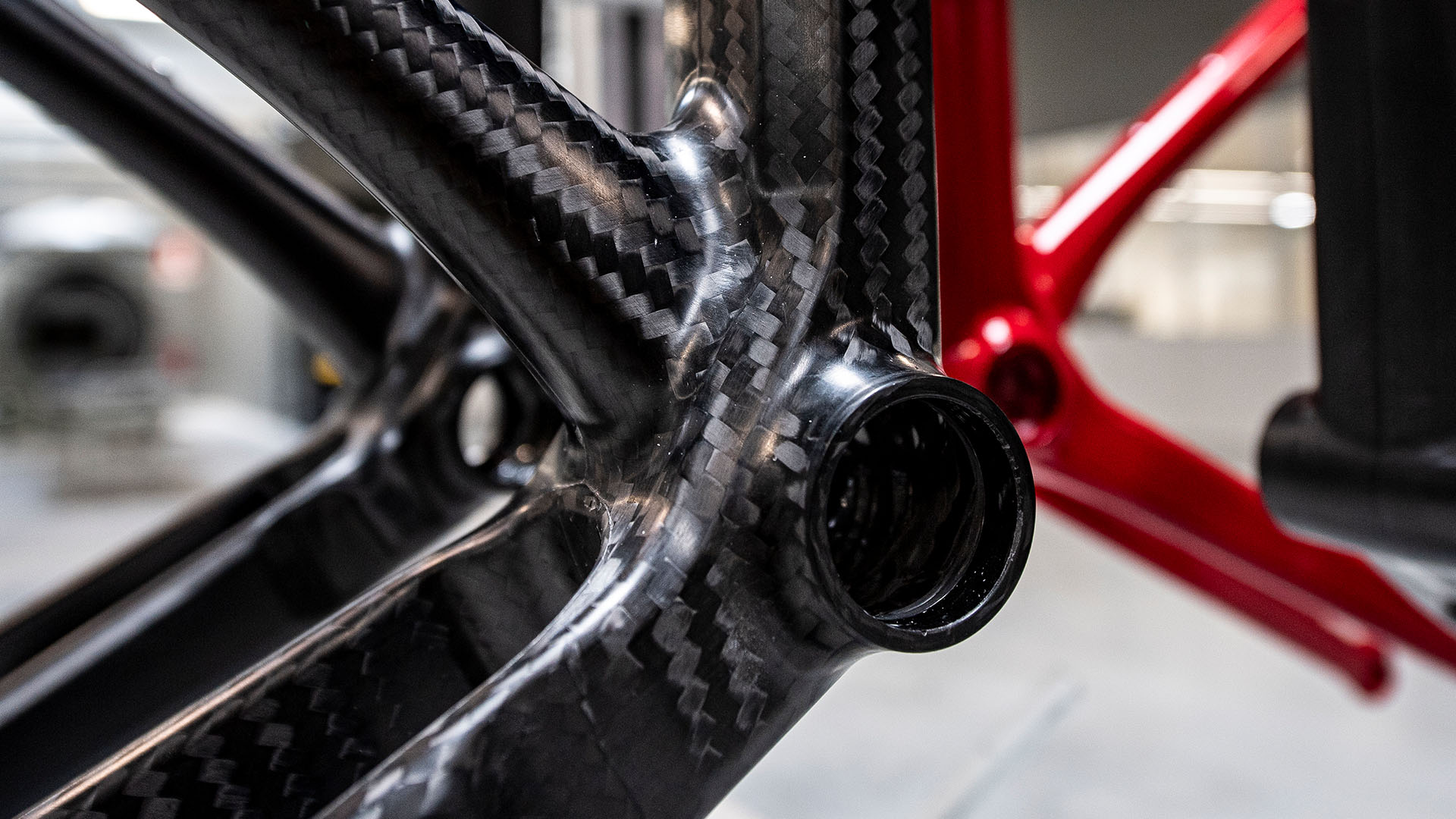
Then finally, we come to carbon fibre. This begins life as a material sheet, made from carbon strands, which is either woven and described as 3K, 6K et cetera or unidirectional, which is essentially matting made of strands of carbon. Much like chopped strand glass fibre with a fancy name.
An epoxy resin is soaked through the carbon material and it is typically placed into a mould to cure and harden into rigid carbon fibre. The high strength properties everyone loves about carbon fibre comes from the relationship between the material and the resin which is typically known as the interface.
There are two ways to make bicycles from carbon fibre. Firstly, you can take or make tubes and then cut them to suit the geometry of the frame you’re making, just like you would with a metal frame. These tubes can then be joined together with a little extra material and resin, just like a lug on a steel frame. This tube-to-tube construction gives you the benefits of carbon fibre with the ability to still make custom geometry, although it is a little more labour intensive.
The other way is to pay £100,000 plus for a mould and then lay sheets of carbon into that to create a part of a frame. Any moulded carbon frame is typically made up of five or more components. In many cases, each frame size will share some of these components with its adjacent frame sizes, which is why if you look at geometry charts of production carbon frames and plot the stack and reach on a chart, it would not be linear but stepped, due to the constraints of the moulds being shared. This method is however a very economical way to produce decent quality frames on a mass production scale. It’s a bit like those moulded popout surf boards everybody learns on before buying a handshaped board. It’s why we typically refer to these in the workshop as ‘plastic popouts’.
Now I’m fully aware that I’m being overly critical. It's because I’m an old git and I hanker for the days when every town had its own frame builder and people rode around on bikes that fitted them perfectly, but you have to admit that the low price for the relative high performance of cheap carbon frames has got a huge amount of people into cycling.
The weird and wonderful
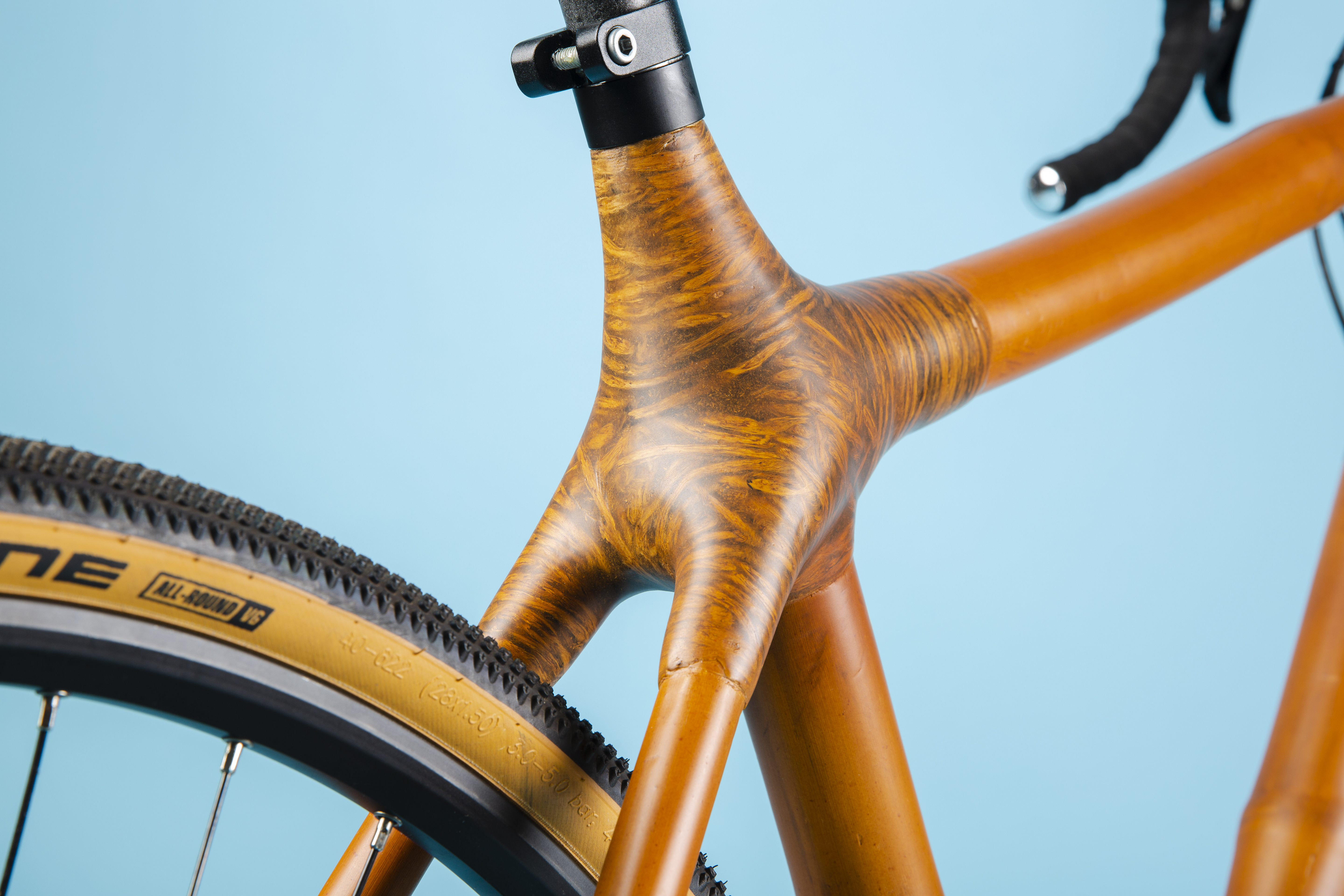
So we’re almost at the end of our list of frame materials. I haven’t really touched on some of the weird and wonderful stuff such as magnesium. Magnesium is very plentiful, with enough to be found in one cubic meter of seawater to make a bicycle frame, or so the ad men would have us believe, but the bikes had a strange tendency of falling to bits under stress.
There was also a trend for metal matrix composites in the 90s, spearheaded by the likes of Specialized with their M2 bikes, but the costs of manufacture became prohibitive and was soon overtaken by the then-new-fangled carbon bikes.
There were a few other weird and wonderful materials, such as bamboo, which can be used to make bicycle frames but I think a lot of the cutting edge right now is in 3D printing and mixing materials for optimum benefits. I recently saw a Bastion and a Festka side-by-side, the Bastion with its 3D printed titanium lugs and carbon tubes sitting next to the Festka with its titanium tubes and carbon fibre lugs. Without physically bench testing these with expensive measurement tools it would be pretty hard to claim one was better than the other.
The bottom line...
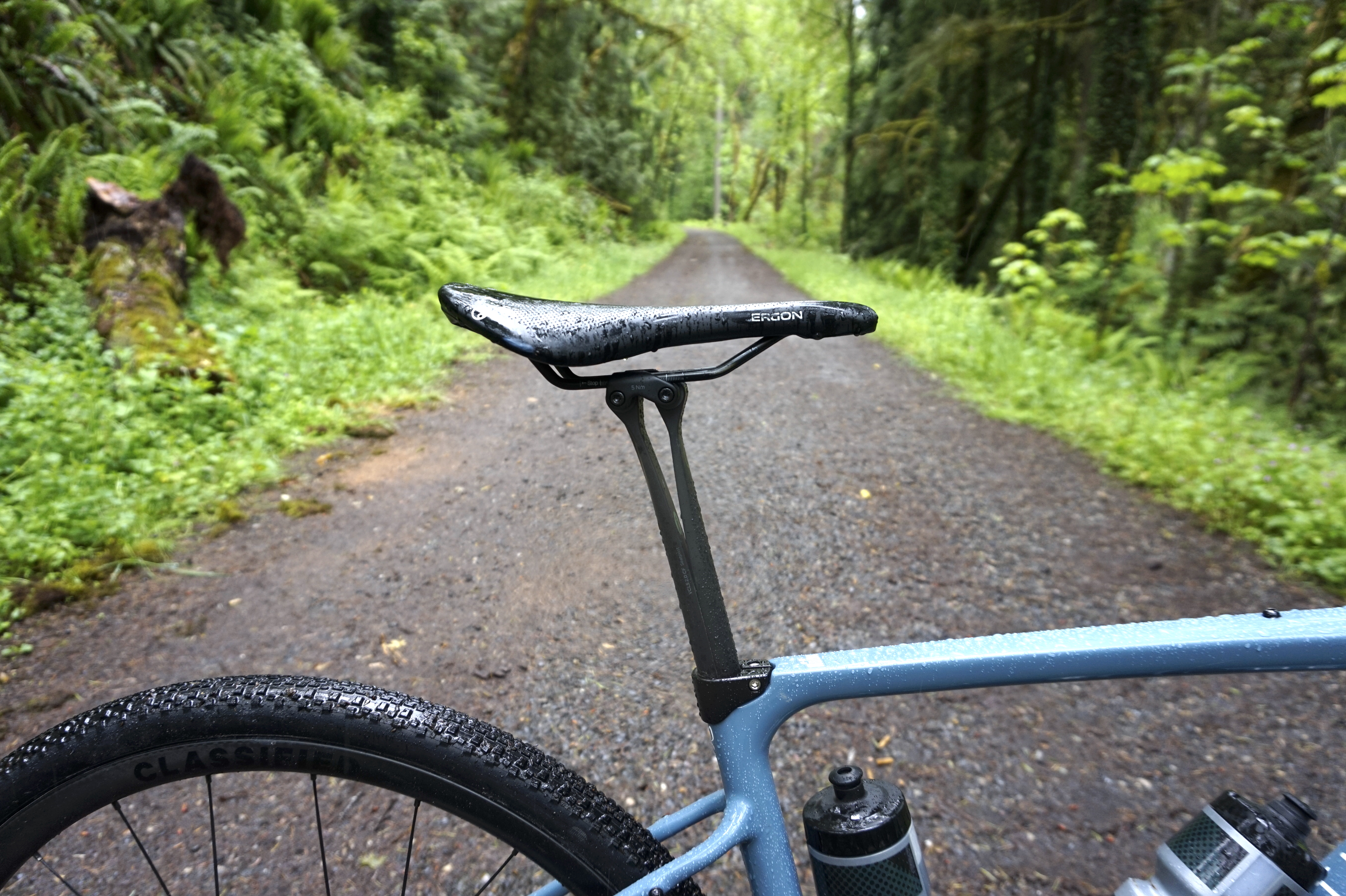
I think that brings me neatly to the main point here. If I were to get well-made examples of each frame material and ride them side-by-side, the biggest differences would be provided not by the frame material but by the length of the seatpost sticking out from the frame and the pressure of the tyres. When you consider the double diamond design of most modern bicycle frames, it’s an incredibly efficient structure. If you analyze the amount of flex in each triangle, it would be barely perceptible.
The seatpost on the other hand is a cantilevered beam sitting at an angle with around 60% of your weight resting on it. So if you have a lot of seatpost sticking out from your frame, it’s going to flex more. Canyon and Ergon know this and produce seat posts that are essentially carbon leaf springs.
Also, with the modern trend towards large tyres and lower pressures, these have far more impact on our sensory perception of how our bike feels due to the increased levels of grip and shock absorbance. If I were being cynical, I might suggest that the reason disc brakes were accepted so readily by mass-market manufacturers, was because they facilitated the use of much bigger tyres, enabling them to simply make the frames light and stiff without having to worry about adding any comfort through clever materials engineering.
So back to the question at hand, what is the best frame material? Titanium and steel, especially the new stainless steels, last the longest. Aluminium will give a great balance of lightweight and low cost while carbon fibre will typically be relatively light and can be relatively inexpensive but won’t last as long due to the interface between the carbon resin eventually breaking down.
Be aware, though this Venn diagram overlaps pretty massively. I own a steel bike which weighs just under 7kg and we see plenty of carbon bikes which weigh a couple of kilos more than this.
So I guess my advice would be this, don’t write off any particular frame material based solely on its reputation. How well the frame fits you is the more important thing as well as how long you want your investment to last.
Now, where did I leave that Aeropress….